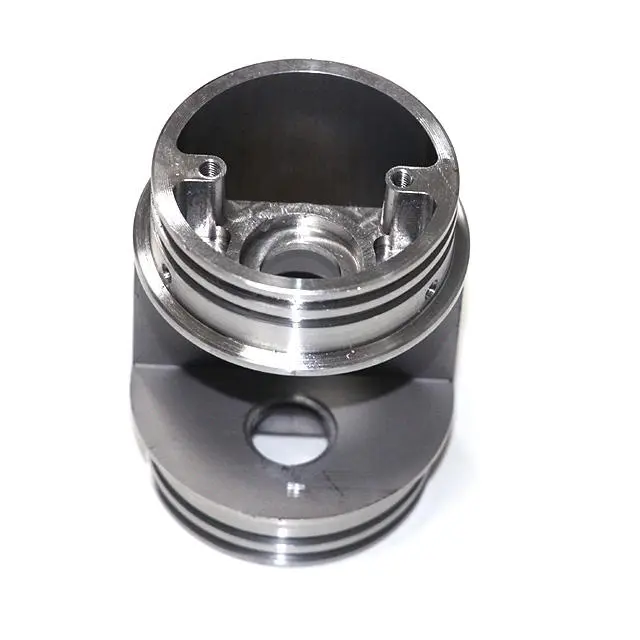
- +8615586668226
- [email protected]
- No. 30, Hongbang Industrial Park, Shenzhen
A CNC machine, at its core, is a power-driven machine used to cut materials with precision. But what sets it apart from a manual machine is its use of computer-based numerical control. Instead of a human operator physically guiding the cutting tool, a CNC machine uses a pre-programmed code—called g-code—to direct its movements. This allows for incredibly accurate and repeatable results, making it a cornerstone of modern manufacturing. CNC is a subtractive manufacturing process. CNC machining is a subtractive process where material is removed from a piece of material. This involves using a variety of tools to carve out the desired shape, with the CNC machine ensuring that the process is carried out with minimal error.
This automation is a huge leap from older, manual machine tools. It allows for the creation of complex and intricate parts that would be incredibly difficult, if not impossible, to produce by hand. CNC is a marvel of modern engineering and is the backbone of modern manufacturing technologies.
There’s not just one type of CNC machine; the industry utilizes various machines, each designed for specific machining operations. Some of the most common types of CNC machine include:
Each of these machines are used for a wide variety of applications, from simple parts to complicated ones. The variety of manufacturing needs is met by the range of CNC machine tools.
The CNC machining process might seem complex, but it can be broken down into a few key steps. First, a part is designed using computer-aided design (CAD) software. This design is then translated into g-code, a programming language that CNC machines understand. The g-code dictates every movement of the cutting tool, including speed, direction, and depth of cut. The machine operator then loads the workpiece into the machine and starts the program. The CNC machine then automatically executes the program, removing material and producing the final part.
The whole machining process relies on precision and the ability to repeat the same operations time and again. A crucial factor in the machining process is feed rate, the speed at which the cutting tool moves across the workpiece. In essence, the CNC machining process is about precision, efficiency, and consistency, all of which are crucial for high-quality production.
Operating a CNC machine requires a unique blend of technical skills and practical knowledge. A machinist needs to understand the basics of machining processes, including how different cutting tool affect different materials. They need to be able to interpret technical drawings and understand the principles of computer-aided manufacturing (CAM). This includes knowledge of g-code and m-code. They need to know how to set up the machine, load workpieces, and monitor the machining operation.
But it’s not all about technical skill; a good machinist must also be a problem-solver, able to troubleshoot issues and make adjustments as necessary. They must also understand safety procedures to avoid damage to the machine and prevent accidents. A CNC machinist is a highly skilled tradesperson that is vital in the modern machining industry.
The story of numerical control goes back to the late 1940s and early 1950s, when engineers began experimenting with using punched cards to control machine tool movements. These early numerical control systems were a giant leap forward, allowing machines to perform complex operations with better accuracy and repeatability than manual machine tools. By the 1960s, computers started to be integrated into these systems, leading to the creation of computer numerical control (CNC) machines.
The development of CNC technology completely transformed manufacturing techniques. Early machines were bulky and expensive. With the advancement of computer software and computer-aided machining, these machines have become more affordable and accessible, and they are used in all kinds of industries now. The brief history of cnc is a history of innovation that has completely changed the way things are manufactured. This includes cnc technology as a foundation of modern manufacturing.
CNC machines are incredibly versatile and can perform a wide range of machining operations. Some of the most common include:
These machining operations are essential to various manufacturing processes and enable the creation of countless products and parts. A CNC machine can do a variety of tasks with different tools used.
CNC machines are a crucial part of the manufacturing process for many industries. In a manufacturing program, it provides a precise way to make parts and products. From aerospace to medical devices, CNC machining is used to create components that require high precision, repeatability, and accuracy. It plays a central role in the subtractive manufacturing process. Unlike additive manufacturing, which builds parts by adding material layer by layer, machining is a subtractive manufacturing approach that cuts away material from a solid block.
CNC also enables a manufacturing process that can be easily modified and adapted to changing needs. By simply changing the g-code program, the same machine can create different parts. This flexibility makes CNC machining ideal for both mass production and rapid prototyping. The development of new manufacturing methods hinges on CNC machinery.
Numerical control (NC) refers to the method of using numbers, symbols, and other coded instructions to operate a machine tool. This contrasts with older machines that were operated manually by a machine operator. In a numerical control system, the machine follows a set of instructions, usually in the form of g-code. These instructions dictate the path, speed, and depth of the cutting tool.
Numerical control forms the backbone of automation in manufacturing. The use of g-code and m-code enables machines to operate independently and consistently, ensuring that each part is made to the same specifications. Numerical control is a big step in improving manufacturing consistency and quality.
The machine tool is the core of the whole CNC machining system. It’s the machinery that actually does the work of removing material from the workpiece. The machine tool includes many components, such as the spindle, the cutting tool, the axes of motion, and the workholding mechanisms. The quality and capabilities of the machine tool directly impact the accuracy, speed, and precision of the final product. It is important to chose a machine tool that suits the manufacturing directives.
A good machine tool should be robust, reliable, and able to hold tight tolerances. It should also be able to handle the different kinds of cutting tool required for different machining operations. Without a capable machine tool, the benefits of computer numerical control cannot be fully realized.
Automation is one of the biggest advantages of using CNC machines. Because a CNC machine uses a pre-written manufacturing program, once the program is started, the machine can operate on its own. This drastically reduces the need for manual intervention. The machine can perform repeated tasks, and it frees up the time of CNC machinists to work on more complex tasks. Automation can drastically improve productivity and lower manufacturing costs.
The automation capabilities of CNC machines are not just limited to the machining operation itself. Many machines can also be integrated into larger automated production lines, where parts are automatically loaded, machined, and unloaded. This makes CNC machinery a key player in the modern manufacturing of a wide variety of products. CNC is the heart of modern manufacturing.
Computer numerical control, or CNC, is the heart of new CNC technology. It’s the way the machine understands how to move and cut materials. The computer numerical control system uses g-code and m-code to tell the machine where to move and how fast. This controlled machine movement leads to a high level of precision and repeatability.
Computer-aided manufacturing (CAM) software plays a crucial role in the CNC machining process. CAM software is used to convert the 3D model of the part from computer-aided design (CAD) into a manufacturing program for a CNC machine. It also enables the user to optimize the machining operations, choose the appropriate cutting tools, and simulate the machining process. CAM allows machines allow more complex parts to be made than ever before.
A career as a CNC machinist is a challenging, rewarding, and stable career path. As manufacturing evolves, the demand for skilled CNC machinists grows. A machinist can work in many different industries, such as aerospace, automotive, and medical devices, offering a diverse range of opportunities. There is always a need for CNC machinists.
The job of a CNC operator or CNC machinist allows you to work with complex machinery and create physical products. CNC is an important field for the future of the manufacturing industry. If you have a knack for problem-solving and enjoy working with your hands, then a career as a CNC machinist might be the right fit for you.
What does CNC mean?
CNC means Computer Numerical Control. It refers to a system in which a computer is used to control the movements of a machine tool.
Is CNC a subtractive or additive process?
CNC machining is a subtractive manufacturing process where material is removed from a workpiece.
What is g-code and m-code?
Called g-code, it is a programming language that CNC machines use to understand how to move and cut, while m-code is used for machine functions like coolant on/off or spindle start/stop.
What are common materials used in CNC machining?
CNC machines can be used to cut materials like aluminum, steel, plastic, and wood.
Can I make my own parts with CNC machinery?
Yes, with the right tools and skills you can use CNC machines for part manufacturing. Many hobbyists now use CNC routers and smaller machines.
How to learn understanding of CNC?
There are many community colleges and vocational schools that offer courses in CNC machining. There are also a lot of online resources for learning what CNC is.
If you are in need of expert CNC services for machining, fabrication, or rapid prototyping, contact us today to learn how our advanced CNC machines can bring your vision to life. Check out our machining services for more information on the breadth of our offerings. Our CNC expertise can deliver results for many applications, from aerospace and automotive to electronics. Let us know how we can help with your next project! If you want to know about the materials we use, we have you covered. Explore our fabrication services to see how we can meet your needs!
Get the latest trends and facts about CNC fabrication from our blog.
Shenzhen Runkey Precision Technology Co. Ltd, a subsidiary of the Tensun Group, is your trusted one-stop solution for custom manufacturing from prototyping to production.Transforming your idea into reality with digital manufacturing resources,streamlined processes, expert guidance,accelerated timelines, and uncompromising quality.
©2024. CNC Fabrication All Rights Reserved.