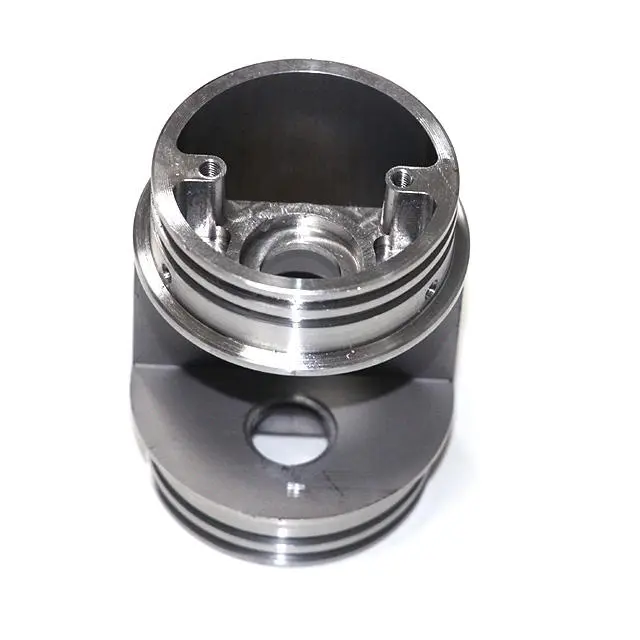
- +8615586668226
- [email protected]
- No. 30, Hongbang Industrial Park, Shenzhen
CNC machines are the backbone of modern manufacturing. Here’s how they power industries:
Machine Type | Key Features | Common Uses |
---|---|---|
5-Axis CNC Machining | Rotates on X, Y, Z, A, and B axes | Aerospace turbines, medical implants |
CNC Lathe | Rotates workpiece against stationary tools | Automotive shafts, hydraulic components |
CNC Router | High-speed cutting for soft materials | Signage, custom furniture, prototypes |
Did you know? 5-axis CNC machines reduce setup time by 70% for complex geometries compared to 3-axis systems.
Key Machines to Know:
Every CNC machine relies on precision components to function:
Example: A CNC milling machine’s critical parts.
Pro Tip: Regular maintenance of components like ways (linear guides) ensures long-term accuracy. For heavy equipment projects, prioritize machines with rigid beds and knees.
Choosing the right tool impacts quality and speed:
Top Tools for Common Tasks:
Case Study: A robotics company reduced cycle time by 25% by switching to ceramic cutters for aluminum parts. Explore our CNC milling services for optimized tooling solutions.
From roughing to finishing:
Stat Alert: Proper surface grinding can improve part lifespan by 3x.
Material choice drives performance:
Material | Pros | Ideal For |
---|---|---|
Aluminum | Lightweight, corrosion-resistant | Aerospace frames |
Titanium | High strength-to-weight ratio | Medical implants, defense |
PEEK | Heat-resistant, biocompatible | Semiconductor components |
Fun Fact: Aluminum extrusion speeds up prototyping by 50% vs. traditional machining.
Ensure every micron counts:
Expert Insight: Pair precision machining with statistical process control for Six Sigma quality.
From CAD to G-code:
Did You Know? Our CNC solutions include CAM programming support to eliminate errors.
A shaky workpiece ruins precision. Top fixtures include:
Pro Advice: For sheet metal fabrication, use nested fixtures to maximize material use.
Protect and beautify your parts:
Case Study: A consumer products brand boosted sales by 15% with polished, cosmetic finishes.
Trust matters. We comply with:
Why It Matters: Certifications like RoHS ensure your parts meet global environmental regulations.
How do I choose between CNC milling and turning?
What materials can be CNC machined?
Metals (aluminum, steel), plastics (PEEK, ABS), and composites.
Why is surface finish important?
Affects friction, corrosion resistance, and aesthetics. Learn about surface finishing options.
How do certifications impact my project?
They guarantee quality, safety, and regulatory compliance—critical for medical and defense sectors.
Ready to Elevate Your Manufacturing? Contact Us for a free consultation—whether you need rapid prototyping or high-volume production.
Get the latest trends and facts about CNC fabrication from our blog.
Shenzhen Runkey Precision Technology Co. Ltd, a subsidiary of the Tensun Group, is your trusted one-stop solution for custom manufacturing from prototyping to production.Transforming your idea into reality with digital manufacturing resources,streamlined processes, expert guidance,accelerated timelines, and uncompromising quality.
©2024. CNC Fabrication All Rights Reserved.