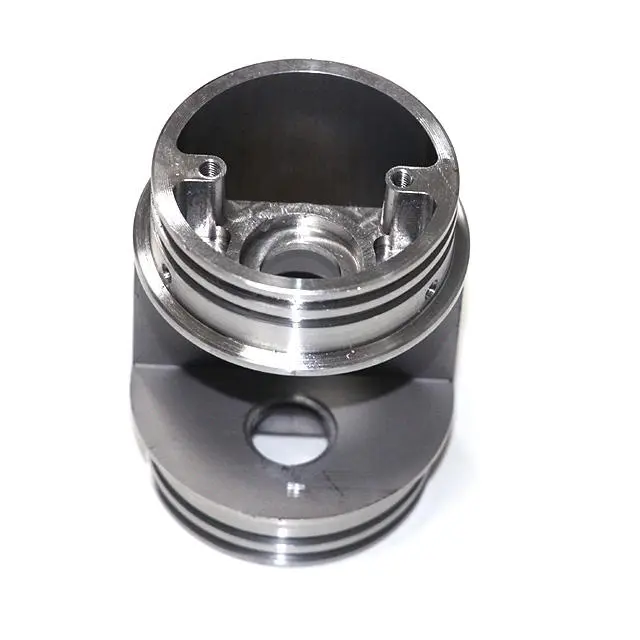
- +8615586668226
- [email protected]
- No. 30, Hongbang Industrial Park, Shenzhen
Brackets are unsung heroes in engineering, acting as robust connectors between components. From supporting aerospace instrumentation to securing medical device panels, these versatile parts ensure structural integrity across industries.
“Precision brackets are the backbone of reliable machinery,” notes John Carter, Lead Engineer at AeroTech Solutions.
Our CNC manufacturing services cater to diverse sectors:
Modern bracket production combines traditional craftsmanship with digital precision:
Process | Key Benefit | Ideal For |
---|---|---|
Laser Cutting | ±0.1mm accuracy | Complex profiles |
CNC Press Brakes | Consistent 90°-120° bends | High-volume production |
TIG Welding | Clean, durable joints | Medical-grade components |
Powder Coating | Enhanced corrosion resistance | Outdoor applications |
Did you know? 78% of manufacturers report improved part consistency after implementing CNC brake systems (Manufacturing Trends Report 2023).
Selecting the right material ensures optimal performance:
Stainless Steel 304
Aluminum 6061-T6
Cold-Rolled Steel
Explore our material selection guide for detailed comparisons.
Avoid costly redesigns with these pro tips:
Case Study: Reduced automotive bracket weight by 22% through strategic aluminum perforation patterns. Read full case study
Request instant quote for your custom bracket project.
What thickness is ideal for load-bearing brackets?
For most industrial applications, 3-5mm steel or 4-6mm aluminum provides optimal strength-to-weight ratio.
How do I prevent galvanic corrosion in multi-material assemblies?
Use dielectric spacers or specify compatible metals like stainless steel with aluminum.
Can you create custom surface finishes?
Yes! We offer everything from brushed metal textures to MIL-SPEC anodizing.
What’s your typical turnaround time?
Prototypes in 3-5 days, production runs in 2-3 weeks depending on complexity.
Contact our engineering team today for a free design consultation.
Ready to elevate your bracket manufacturing? Schedule a consultation with our CNC specialists today!
Get the latest trends and facts about CNC fabrication from our blog.
Shenzhen Runkey Precision Technology Co. Ltd, a subsidiary of the Tensun Group, is your trusted one-stop solution for custom manufacturing from prototyping to production.Transforming your idea into reality with digital manufacturing resources,streamlined processes, expert guidance,accelerated timelines, and uncompromising quality.
©2024. CNC Fabrication All Rights Reserved.