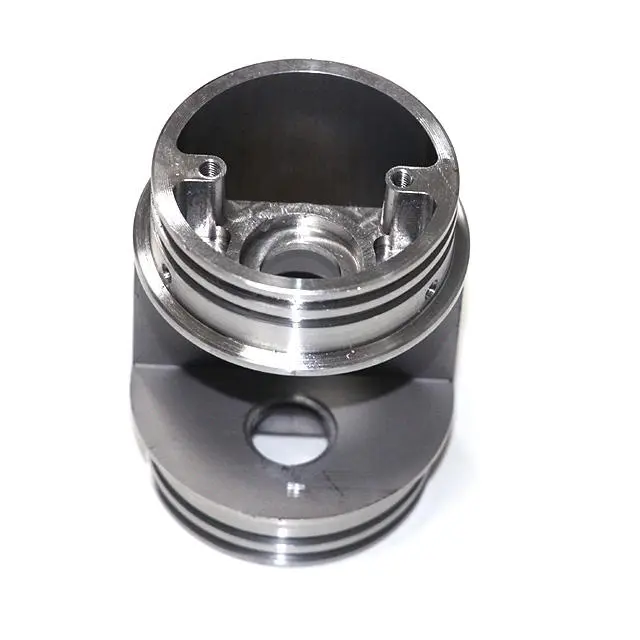
- +8615586668226
- [email protected]
- No. 30, Hongbang Industrial Park, Shenzhen
A CNC mill is a sophisticated machine tool used in manufacturing to create precise parts by removing material from a workpiece. CNC stands for Computer Numerical Control, meaning the machine is controlled by a computer program. Unlike manual milling, where an operator controls the machine by hand, a CNC mill executes pre-programmed instructions, ensuring high accuracy and repeatability. This machine tool is like a smart robot that can craft complex shapes with incredible precision.
At the heart of every CNC machine is the capability to interpret and execute complex instructions, ensuring that each machine operates with the utmost precision and efficiency. The process begins with a digital design, often created using computer-aided design (CAD) software. This design is then translated into a set of instructions called G-code, which guides the machine’s movements. The CNC mill has a rotating cutting tool that moves along multiple axes, removing material from the workpiece to achieve the desired shape. The workpiece is typically clamped onto a table, which can also move in different directions. We’ve honed our skills over years of operating these complex machines, ensuring that every project meets the highest standards of quality and precision.
The CNC milling process is a subtractive manufacturing process that involves removing material from a workpiece using a rotating cutting tool. It’s a bit like sculpting, but instead of chisels, we use high-speed, computer-guided tools. The process that uses computer-aided manufacturing (CAM) software to generate toolpaths. The steps in using CNC milling are as follows:
Design: Create a digital model of the part using CAD software. We start with a design and turn it into a plan for our machines.
Programming: Convert the CAD model into G-code using CAM software. This code tells the machine exactly what to do.
Setup: Mount the workpiece on the machine table and load the appropriate cutting tool into the spindle.
Execution: Run the G-code program, and the CNC machine will automatically cut the part. The machine follows the plan, cutting the material with precision.
Finishing: Once the milling is complete, the part may require additional finishing processes, such as deburring or surface treatment.
The CNC milling process is known for its ability to produce highly accurate and complex parts, making it a popular choice in various industries. CNC milling machines are the workhorses of our production, enabling us to create intricate components for a wide range of applications.
There are different types of CNC milling machines, each designed for specific applications. It’s like having different tools for different jobs, each one specialized for its task. Vertical milling machines are the most common, with a vertical spindle that holds the cutting tool. These machines are versatile and can handle a wide range of tasks. Horizontal milling machines, on the other hand, have a horizontal spindle and are better suited for heavy-duty operations.
Multi-axis milling machines such as 5-axis milling machines, can move the cutting tool along five different axes, allowing for the creation of complex and intricate shapes. Imagine a machine that can twist and turn in five different directions – that’s the power of a 5-axis machine. There are also specialized machines like 4-axis milling machine, angular milling machines, and CNC lathes, each designed for specific milling operations. Choosing the right machine depends on the specific requirements of the project.
A wide range of materials can be used in CNC milling, including metals, plastics, and composites. CNC milling can work with a variety of materials, from soft plastics to hard metals. Each material has its own unique properties that must be considered during the milling operation. Some of the most common materials include:
Aluminum: Lightweight and easy to machine, aluminum is a popular choice for many applications. It’s like the go-to metal for many projects because it’s easy to work with and versatile. Aluminum is often the preferred material for our aerospace and automotive clients due to its excellent strength-to-weight ratio.
Steel: Strong and durable, steel is often used for heavy-duty components. Steel is tough and reliable, ideal for parts that need to withstand a lot of stress.
Stainless Steel: Known for its corrosion resistance, stainless steel is ideal for parts that will be exposed to harsh environments. It’s perfect for parts that need to resist rust and corrosion.
Brass: Easy to machine and with excellent electrical conductivity, brass is often used for electrical connectors and other components. Brass is great for electrical parts because it conducts electricity well.
Plastics: Various types of plastics, such as ABS, polycarbonate, and nylon, can be milled. Each type of plastic has its own unique properties.
Composites: Materials like carbon fiber and fiberglass can be milled, offering high strength and low weight.
CNC milling operations can be categorized into several types, each designed to achieve a specific result. Think of it like having different moves in a dance, each one creating a unique effect. Face milling involves using a face milling cutter to create a flat surface on the workpiece. It’s like smoothing out a rough surface to make it perfectly flat. Plain milling, also known as slab milling, involves using a plain milling cutter to remove material from a flat surface.
Angular milling is used to create angled surfaces or features, while form milling involves using a specially shaped cutter to create complex contours. Our advanced machines can handle even the most intricate designs, delivering results that exceed our clients’ expectations. Other common milling operations include drilling, boring, reaming, and tapping. Each operation requires a specific type of cutting tool and technique.
The cost of CNC milling can vary widely depending on several factors, including the complexity of the part, the material being used, the type of machine required, and the volume of the production run. It’s like pricing a custom-made suit – the more intricate the design, the higher the cost. For simple parts made from easy-to-machine materials, the cost can be relatively low. However, for complex parts made from difficult-to-machine materials, the cost can be significantly higher.
Other factors that can affect the cost include the setup time, the programming time, and the finishing processes required. To reduce the cost of CNC milling, it’s important to optimize the design for manufacturability, choose the right material, and select the most efficient milling process. Our team works closely with clients to find the most cost-effective solutions without compromising on quality.
CNC milling offers numerous advantages over traditional manual milling. It’s like comparing a handcrafted letter to an email – both have their merits, but the email is faster and more consistent. One of the primary benefits of CNC milling is its high accuracy and precision. CNC machines can create parts with tolerances as tight as +/- 0.001 inches, ensuring that each part is identical to the next. This level of accuracy is difficult, if not impossible, to achieve with manual milling.
Another advantage is the speed and efficiency of the process. CNC machines can operate 24/7, significantly reducing lead times. Additionally, CNC milling is highly repeatable, meaning that once a program is created, it can be run over and over again to produce identical parts. This is particularly beneficial for high-volume production runs. With our state-of-the-art equipment and experienced team, we can handle projects of any size and complexity with ease.
CNC milling applications are diverse and span across numerous industries. It’s like a Swiss Army knife, useful in so many different situations. In the aerospace industry, CNC milling is used to create precision components for aircraft and spacecraft. The automotive industry relies on CNC milling to produce engine parts, body panels, and other components. Our expertise in CNC milling allows us to serve a wide range of industries, from aerospace to consumer products.
The medical industry uses CNC milling to manufacture surgical instruments, implants, and other medical devices. CNC milling is also used in the electronics industry to produce circuit boards, enclosures, and other components. Other industries that heavily relies on CNC milling include defense, energy, and consumer products. Our expertise in CNC milling allows us to serve a wide range of industries, from aerospace to consumer products. The versatility of CNC milling makes it an indispensable process in modern manufacturing.
While both CNC milling and CNC turning are subtractive manufacturing process that uses computer-controlled machines to remove material from a workpiece, there are some key differences between the two processes. It’s like comparing a saw to a lathe – both cut, but they do it differently. CNC milling involves using a rotating cutting tool to remove material from a stationary workpiece. CNC turning, on the other hand, involves rotating the workpiece against a stationary cutting tool.
CNC milling is typically used to create complex parts with flat or contoured surfaces, while CNC turning is better suited for creating cylindrical or conical parts. Think of turning as making a baseball bat, while milling is like carving a statue. Both processes have their own unique advantages and are often used in conjunction with each other to create complex parts.
When choosing CNC machining services or manufacturing services, it’s essential to consider several factors to ensure you get the parts you need with the quality and precision required. It’s like choosing a partner for a critical project – you need someone reliable and skilled. First, look for a company with a proven track record of delivering high-quality parts on time. Experience and expertise in CNC milling and machining are crucial.
Second, consider the company’s capabilities and equipment. Do they have the right machines and tools to handle your specific project? Can they work with the materials you require? Third, evaluate their quality control processes. Do they have rigorous inspection procedures in place to ensure that every part meets your specifications? Finally, consider their customer service and communication. Are they responsive to your needs and willing to work with you to achieve your goals? As a leading provider of CNC fabrication services, we pride ourselves on our commitment to quality, precision, and customer satisfaction.
What is the difference between 3-axis and 5-axis CNC milling?
3-axis CNC milling machines can move the cutting tool along three axes (X, Y, and Z), while 5-axis milling machines can move the tool along five axes (X, Y, Z, A, and B). This allows 5-axis machines to create more complex and intricate shapes.
How accurate is CNC milling?
CNC milling is highly accurate, with tolerances as tight as +/- 0.001 inches. This level of precision ensures that each part is identical to the next.
What is the typical lead time for CNC milling projects?
The lead time for CNC milling projects can vary depending on the complexity of the part, the material being used, and the volume of the production run. However, CNC machines can operate 24/7, significantly reducing lead times compared to manual milling.
Can CNC milling be used for prototyping?
Yes, CNC milling is an excellent choice for prototyping. It allows for the rapid creation of highly accurate prototypes, enabling designers to test and refine their designs quickly. Check out our Rapid Prototyping page for more info.
What are the advantages of using aluminum for CNC machining?
Aluminum for CNC machining is favored due to its lightweight nature, excellent machinability, and good strength-to-weight ratio. It is easier and faster to machine than many other metals, which can lead to reduced machining time and costs.
What are some alternatives to aluminum for CNC machining?
Alternatives to aluminum for CNC machining include steel, stainless steel, titanium, brass, copper, and various engineering plastics like ABS, polycarbonate, and PEEK. The choice depends on the specific requirements of the part, such as strength, weight, corrosion resistance, and cost.
CNC milling is a versatile and essential manufacturing process used across numerous industries.
CNC machines offer high accuracy, precision, and repeatability, making them ideal for creating complex parts.
There are many different types of CNC milling machines, each designed for specific applications.
A wide range of materials can be used in CNC milling, including metals, plastics, and composites.
CNC milling operations include face milling, plain milling, angular milling, and form milling.
The cost of CNC milling depends on factors such as part complexity, material, machine type, and production volume.
CNC milling offers numerous advantages, including high accuracy, speed, efficiency, and repeatability.
CNC milling is used in industries such as aerospace, automotive, medical, electronics, and more.
Choosing the right CNC machining services provider is crucial for ensuring quality, precision, and on-time delivery.
Consider factors such as experience, capabilities, quality control, and customer service when selecting a CNC machining partner.
To take the next step in bringing your project to life with unparalleled precision, explore our Machining Services. Here, you’ll find a team dedicated to excellence, ready to transform your concepts into reality. For an in-depth look at how we tailor our expertise to meet the unique demands of various sectors, visit our Aerospace and Automotive industry pages. Here, we detail our specialized approach, showcasing our commitment to innovation and quality in each field. Additionally, our CNC Solutions page offers a comprehensive overview of the cutting-edge technologies and methodologies we employ, ensuring that we remain at the forefront of the industry. Lastly, for those looking to delve deeper into the specific technologies and materials we utilize, our Materials page provides extensive information on the wide range of options available, each selected for its unique properties and suitability for various applications.
Get the latest trends and facts about CNC fabrication from our blog.
Shenzhen Runkey Precision Technology Co. Ltd, a subsidiary of the Tensun Group, is your trusted one-stop solution for custom manufacturing from prototyping to production.Transforming your idea into reality with digital manufacturing resources,streamlined processes, expert guidance,accelerated timelines, and uncompromising quality.
©2024. CNC Fabrication All Rights Reserved.