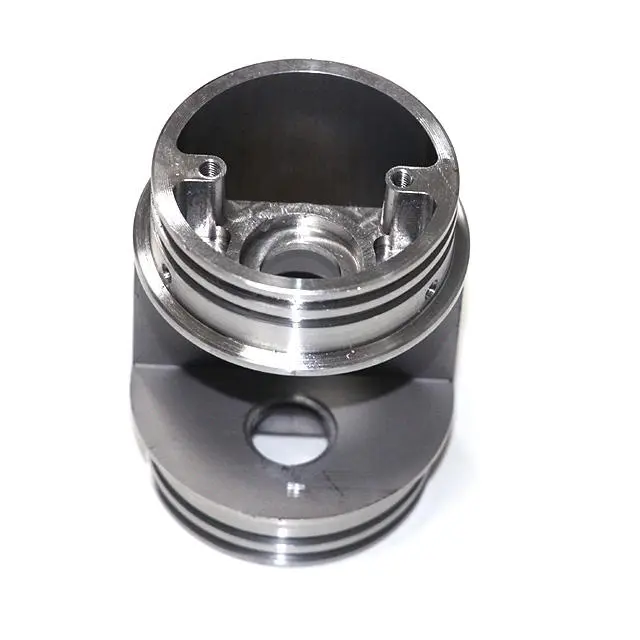
- +8615586668226
- [email protected]
- No. 30, Hongbang Industrial Park, Shenzhen
In today’s competitive landscape, businesses across various sectors face the constant pressure to innovate, improve quality, and reduce time-to-market. Whether you’re developing a new aerospace component, a life-saving medical device, or a cutting-edge consumer electronic, precision and reliability are non-negotiable. You need a manufacturing partner who understands your specific needs and can deliver consistent, high-quality results. Are your current parts up to par?
We are a leading CNC manufacturing service and product manufacturing factory, specializing in delivering precision-engineered components and assemblies. We combine state-of-the-art technology with decades of experience to provide a comprehensive range of services, from Rapid Prototyping to On Demand Manufacturing. Our commitment to quality, efficiency, and customer satisfaction sets us apart.
We have extensive experience serving a broad spectrum of industries, each with its unique requirements and challenges. Here’s a glimpse of how we tailor our services:
Our facility is equipped with advanced CNC machinery, enabling us to offer a wide range of services:
One critical aspect of CNC machining that significantly impacts quality and efficiency is the depth of cut. This parameter, often overlooked, is the thickness of material removed in a single pass of the cutting tool. It’s a fundamental factor affecting:
The optimal depth of cut depends on several factors, including:
Formula:
The basic formula for depth of cut in turning is:
ap = (dw - dm) / 2
Where:
ap
= Depth of cutdw
= Diameter of the workpiecedm
= Diameter of the machined areaExample Table:
Machining Process | Typical Depth of Cut Range (mm) | Factors Influencing Depth |
---|---|---|
Turning | 0.5 – 3.0 | Material, Tool, Machine |
Milling (General) | 0.5 – 10.0 | Operation, Material, Tool |
Milling (Finishing) | 0.1 – 0.5 | Surface Finish Requirement |
Drilling | Varies by Drill Size | Hole Depth, Material |
Grinding | 0.01 – 0.1 | Precision, Finish |
Fine-tuning the depth of cut is crucial for:
We have experience machining a wide range of materials, each with its unique properties: (Materials)
We understand the specific challenges of machining each material and adjust our processes accordingly.
Quality is at the heart of everything we do. We employ rigorous quality control measures throughout the entire manufacturing process, from initial design review to final inspection. Our quality assurance processes include:
A leading aerospace company required a complex, high-precision component for a new aircraft engine. The component was made from titanium and required extremely tight tolerances. Using our 5 Axis CNC Machining capabilities and expertise in machining difficult materials, we were able to successfully manufacture the component to the exact specifications, meeting the stringent requirements of the aerospace industry. The client was extremely satisfied with the quality, precision, and on-time delivery.
(A)ction:
Are you looking for a reliable, experienced CNC manufacturing partner? Contact us today to discuss your project requirements and receive a free quote. Let us help you bring your designs to life with precision, quality, and efficiency. We’re here to provide a quick and straightforward answer!
What is the typical lead time for a CNC machining project?
Lead times vary depending on the complexity of the project, material availability, and order quantity. We strive to provide the fastest possible turnaround times without compromising quality. Contact us for a specific estimate.
What file formats do you accept?
We accept a wide range of CAD file formats, including STEP, IGES, DXF, DWG, and SolidWorks files.
Do you offer design assistance?
Yes, our experienced engineers can provide design for manufacturability (DFM) feedback and assist with optimizing your designs for CNC machining.
What are your quality control procedures?
As mentioned earlier, we have rigorous quality control procedures in place, including in-process inspection, FAI, final inspection, and CMM inspection.
How do I maintain the tools once you have manufactured them?
It is advisable to carry out maintenance from time to time, checking the status of each part.
What tolerances can you achieve?
It will depend on the material, but we have high-precision tools to offer the best possible result.
Contact us today to experience the difference!
Get the latest trends and facts about CNC fabrication from our blog.
Shenzhen Runkey Precision Technology Co. Ltd, a subsidiary of the Tensun Group, is your trusted one-stop solution for custom manufacturing from prototyping to production.Transforming your idea into reality with digital manufacturing resources,streamlined processes, expert guidance,accelerated timelines, and uncompromising quality.
©2024. CNC Fabrication All Rights Reserved.