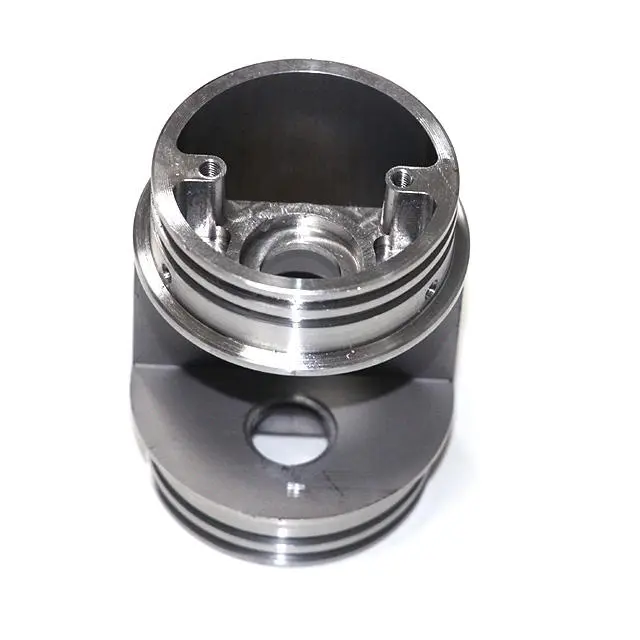
- +8615586668226
- [email protected]
- No. 30, Hongbang Industrial Park, Shenzhen
Plasma cutting is a thermal cutting process that uses a high-temperature plasma arc to melt and remove material from a workpiece. But how does it actually work? A plasma cutter works by sending an electric arc through a gas, such as compressed air, oxygen, nitrogen, or argon, and this is used for plasma. The gas is forced through a small nozzle, and the electric arc ionizes the gas, turning it into plasma. Plasma is often called the fourth state of matter, alongside solid, liquid, and gas. When plasma is pushed towards the cutting head, it reaches incredibly high temperatures, often exceeding 20,000°C.
The plasma torch then directs this high-temperature plasma jet towards the workpiece. Since plasma is electrically conductive, as the plasma arc contacts the metal, the intense heat melts the metal, and the high-velocity gas blows the molten metal away, creating a clean cut. This process is incredibly effective for cutting conductive materials like steel, stainless steel, aluminum, brass, and copper. The precision of the cut is controlled by the movement of the torch across the cutting table, often guided by a computer numerical control (CNC) system.
As a leading provider of CNC precision manufacturing services, we recognize that plasma cutting offers several advantages for a variety of fabrication projects. One of the primary benefits of plasma cutting is its speed. Plasma cutting is one of the fastest methods available, especially when it comes to cutting thick materials. It significantly outperforms traditional methods like flame cutting or sawing, leading to increased productivity and faster turnaround times. This high-speed cutting capability is particularly valuable for industries like automotive and industrial equipment, where time is of the essence.
Another significant advantage is the versatility of plasma cutters. They can cut a wide range of conductive metals, including sheet metal, with thicknesses ranging from thin gauge to several inches. This makes plasma cutting suitable for cutting various applications, from intricate designs to heavy-duty structural components. Moreover, plasma cutting needs no preheating, saving valuable time compared to other cutting methods. In contrast to flame cutting, the initial setup is faster, further contributing to efficiency. The process delivers precise cuts.
While plasma cutting has many benefits, it also has some disadvantages. One potential drawback is the heat-affected zone (HAZ). The intense heat generated during the cutting process can alter the material properties near the cut edge. This can be a concern for certain applications where material integrity is critical. However, advancements in plasma cutting technology are continuously minimizing the HAZ.
Another disadvantage of plasma cutting is the quality of the cut edge. While generally good, it may not be as smooth or precise as that achieved with laser cutting. There is often a slight bevel on the cut edge, and dross (solidified molten metal) can sometimes adhere to the bottom of the cut. These imperfections may require secondary finishing operations, such as grinding or machining, adding time and cost to the fabrication project. In addition, there are limitations when it comes to the range of materials that can be cut. It is best suited for electrically conductive materials. Non-conductive materials like plastic or wood are better processed using alternative cutting methods.
Choosing between CNC plasma cutting and laser cutting depends on several factors, including the type of material, thickness, required precision, and budget. Laser cutting services are known for their exceptional precision and ability to create intricate designs with very narrow kerfs (the width of the cut). This makes them ideal for applications that demand high accuracy and smooth edges, such as those found in the electronics and medical devices industries. However, laser cutting machines are typically more expensive than CNC plasma machines, both in terms of initial investment and operating costs.
CNC plasma cutting, on the other hand, excels at cutting thicker materials and offers faster cutting speeds, especially for thicker metals. It’s a more cost-effective solution for many fabrication projects, particularly those involving thicker materials like steel and aluminum. While plasma cutters may not achieve the same level of precision as lasers, they still provide excellent cut quality suitable for a wide range of applications. A CNC plasma cutting machine can be the better choice when you need speed and versatility without sacrificing too much precision.
Plasma cutters are highly versatile when it comes to the types of materials they can cut. They are primarily used for cutting metals that are electrically conductive. This includes common materials like mild steel, stainless steel, and aluminum, which are widely used across various industries. Plasma cutting is also effective for cutting other conductive metals, such as copper, brass, and titanium.
The thickness of the material that a plasma cutter can handle depends on the power of the machine. Entry-level plasma cutters can typically cut materials up to 1/2 inch thick, while industrial-grade machines can handle thicknesses of several inches. For instance, in our CNC precision manufacturing plant, we often use plasma cutting for thick stainless steel plates used in the aerospace and heavy equipment industries. Sheet metal fabrication also uses plasma cutting.
The primary difference between a CNC plasma cutter and a manual (or handheld) plasma cutter lies in the control and automation of the cutting process. Handheld plasma cutters are portable and operated manually by a technician who guides the plasma torch along the desired cut path. This method requires a steady hand and a good eye to achieve accurate cuts. While suitable for small projects or on-site repairs, manual plasma cutting lacks the precision and repeatability of CNC plasma cutting. A plasma cutter may have this feature.
A CNC plasma cutter, on the other hand, is a computer-controlled machine that automates the entire cutting process. The technician programs the desired design into the CNC software, and the machine takes over, precisely moving the plasma torch along the programmed path. This automation ensures consistent, accurate cuts every time, making CNC plasma cutting ideal for complex shapes and high-volume production.
Plasma cutting involves high temperatures, bright light, and potentially hazardous fumes, so safety is paramount. Here are some essential safety precautions to follow:
Eye Protection: Always wear appropriate eye protection, such as a welding helmet with a shade suitable for plasma cutting. The intense light emitted during the process can cause serious eye damage.
Protective Clothing: Wear flame-resistant clothing, gloves, and leather boots to protect your skin from sparks and molten metal.
Ventilation: Ensure adequate ventilation in the work area to remove fumes and gases produced during cutting. Use a fume extraction system if necessary.
Fire Safety: Keep a fire extinguisher nearby and be aware of potential fire hazards. Remove any flammable materials from the cutting area.
Electrical Safety: Regularly inspect the plasma cutter and its cables for damage. Make sure the machine is properly grounded to prevent electrical shock.
CNC plasma cutting is highly suitable for high-volume production due to its speed, automation, and repeatability. The ability of a CNC plasma machine to quickly cut through thick materials makes it a popular choice for industries that require large quantities of parts, such as automotive, construction, and industrial equipment. The automation provided by CNC control ensures consistent quality and reduces labor costs, further enhancing productivity.
For high-volume production, a CNC plasma cutting machine can be integrated into a larger manufacturing cell, with automated material handling and part removal systems. This streamlines the entire process, from loading raw materials to unloading finished parts, maximizing efficiency and throughput.
Selecting the right plasma cutting machine for your needs depends on several factors. Consider the following:
Material Type and Thickness: What types of metals will you be cutting, and what is the maximum thickness? Choose a machine with sufficient power to handle your typical materials.
Cutting Speed: How fast do you need to cut? If speed is a priority, look for a machine with high cutting speeds.
Duty Cycle: The duty cycle indicates how long the machine can operate continuously without overheating. For heavy-duty use, choose a machine with a high duty cycle.
Cut Quality: Consider the required edge quality. If you need very smooth edges, you may want to consider a high-definition plasma system or even explore laser cutting.
Table Size: The size of the cutting table should be large enough to accommodate your largest workpieces.
Budget: Plasma cutting machines range in price from a few thousand dollars to tens of thousands. Determine your budget and choose a machine that offers the best value for your needs.
Plasma cutting technology continues to evolve, with ongoing advancements aimed at improving cut quality, speed, and efficiency. High-definition plasma systems are becoming increasingly popular, offering near-laser quality cuts with reduced bevel and dross. These systems use advanced gas flow and torch designs to achieve a more focused plasma arc, resulting in cleaner, more precise cuts.
Another trend is the integration of advanced software and automation features. Modern CNC plasma machines are equipped with user-friendly software that simplifies programming and allows for complex cutting patterns. Some systems even incorporate automatic torch height control and collision avoidance features, further enhancing productivity and reducing the risk of errors.
Here’s a table summarizing some key advancements in plasma cutting technology:
Feature | Traditional Plasma Cutting | High-Definition Plasma Cutting | Future Trends |
Cut Quality | Good, some bevel and dross | Excellent, near-laser quality | Near-perfect edges, minimal HAZ |
Cutting Speed | Fast | Fast | Even faster cutting speeds |
Material Thickness | Up to several inches | Up to several inches | Increased thickness capacity |
Precision | Moderate | High | Ultra-high precision |
Automation | Basic CNC control | Advanced CNC control, automatic features | AI-powered optimization, predictive maintenance |
Operating Costs | Relatively low | Moderate | Further reduced operating costs |
Environmental Impact | Moderate fume generation | Reduced fume generation | Minimal environmental impact |
What is the main advantage of using a CNC plasma cutter over a manual one?
The main advantage is automation and precision. A CNC plasma cutter uses computer control to guide the cutting torch, ensuring consistent and accurate cuts every time, which is crucial for complex shapes and high-volume production.
Can a plasma cutter cut through any type of metal?
Plasma cutters are most effective on electrically conductive materials. While they can cut through a wide range of metals like steel, aluminum, copper, and brass, they are not suitable for non-conductive materials like plastic or wood.
How thick of metal can a plasma cutter typically cut?
The cutting thickness depends on the power of the plasma cutter. Entry-level models can cut up to 1/2 inch, while industrial-grade machines can handle thicknesses of several inches.
Is plasma cutting more cost-effective than laser cutting?
Generally, yes. While laser cutting offers higher precision, plasma cutting is more cost-effective, especially for thicker materials. The initial investment and operating costs for plasma cutters are typically lower than for laser cutters.
What are the safety glasses requirements for plasma cutting?
Safety glasses used for plasma cutting must be specifically designed to protect against the intense light and radiation emitted during the process. They should have a shade number appropriate for plasma cutting, typically between shade 5 and shade 8, depending on the amperage of the plasma cutter.
How does the heat-affected zone in plasma cutting compare to other cutting methods?
The heat-affected zone (HAZ) in plasma cutting is generally larger than in laser cutting but smaller than in oxy-fuel cutting. High-definition plasma cutting systems have significantly reduced the HAZ compared to traditional plasma cutting.
Plasma cutting is a versatile and efficient method for cutting a wide range of conductive materials.
CNC plasma cutting offers automation, precision, and repeatability, making it ideal for high-volume production.
While plasma cutting has some disadvantages, such as the heat-affected zone and potential edge imperfections, advancements in technology are continuously addressing these issues.
Choosing between plasma cutting and laser cutting depends on the specific application requirements, including material type, thickness, desired precision, and budget.
Safety is paramount when using a plasma cutter, and proper precautions must always be taken.
As a leading provider of CNC machining and fabrication services, we at CNC precision manufacturing have extensive experience utilizing plasma cutting to deliver high-quality parts for various industries. We invite you to contact us to discuss your specific needs and discover how our expertise can benefit your next fabrication project.
The future of plasma cutting is bright, with ongoing advancements promising even better cut quality, speed, and efficiency.
If you’re ready to take advantage of the power and precision of CNC plasma cutting for your next fabrication project, don’t hesitate to reach out to us. We are committed to providing exceptional service and delivering parts that meet the highest standards of quality and precision. We are always eager to discuss your project and demonstrate how our CNC Solutions and expertise can benefit you. Let’s work together to bring your ideas to life!
Get the latest trends and facts about CNC fabrication from our blog.
Shenzhen Runkey Precision Technology Co. Ltd, a subsidiary of the Tensun Group, is your trusted one-stop solution for custom manufacturing from prototyping to production.Transforming your idea into reality with digital manufacturing resources,streamlined processes, expert guidance,accelerated timelines, and uncompromising quality.
©2024. CNC Fabrication All Rights Reserved.