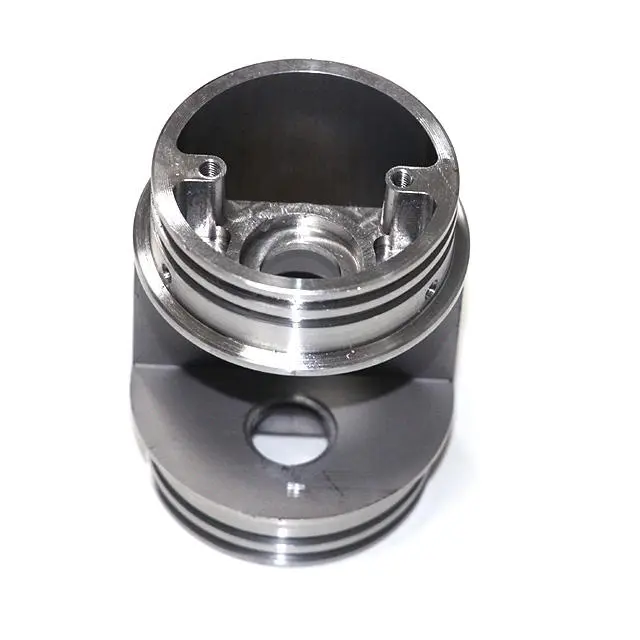
- +8615586668226
- [email protected]
- No. 30, Hongbang Industrial Park, Shenzhen
While both machines automate precision machining tasks, they are designed for different purposes, making them ideal for specific applications. Understanding the differences between these machines is important for selecting the right tool for your manufacturing needs.
Feature/Capability | CNC Mill | CNC Router |
CNC control | ✔ | ✔ |
Moving tool & stationary part | ✔ | ✔ |
Versatility | ✔ | ✔ |
Subtractive machining | ✔ | ✔ |
Handles soft materials | X | ✔ |
Handles hard materials | ✔ | X |
Larger worktables | X | ✔ |
More rigid tooling | ✔ | X |
Larger cut width/depth | X | ✔ |
Tighter tolerances | ✔ | X |
Multi-axis capability | ✔ | X |
Faster cutting | X | ✔ |
CNC routers use X-, Y-, and Z-axis movements to guide the cutting tool across the workpiece, cutting or engraving materials like wood, plastic, and composites. They typically come in various sizes and are often used for larger workpieces. CNC mills, by contrast, are more rigid and precise, using rotary cutting tools to machine harder materials. Mills can have up to 12 axes, enabling more advanced machining options.
CNC routers often use user-friendly software with simplified programming, making them suitable for industries like woodworking or sign-making. CNC mills require more advanced software to handle complex geometries and intricate toolpaths.
CNC routers are popular in industries such as woodworking, cabinetry, and sign-making. They excel at intricate 2D and 3D designs but are generally used for less precise, less complex work. CNC mills, on the other hand, are commonly used in aerospace, automotive, and medical industries, where high precision and complex parts are required. CNC mills offer tight tolerances and are suitable for harder materials like metals.
CNC routers handle softer materials like wood, plastic, and aluminum. They lack the rigidity to cut harder materials effectively. CNC mills, however, can easily machine through hard metals like stainless steel, titanium, and composites, thanks to their more robust structure and tooling.
CNC routers are generally built for lower cutting speeds and lighter cutting forces, suited to softer materials. CNC mills, in contrast, are designed for higher cutting speeds and stronger forces, making them ideal for tougher materials. CNC mills feature more robust spindles and higher horsepower, allowing for precision machining of harder materials.
CNC routers use router bits, available in various profiles for cutting, shaping, and engraving softer materials. CNC mills, however, use specialized tools like end mills and drills to cut metals, offering more diverse options for precise machining tasks.
CNC mills are generally more expensive due to their robust construction and advanced tooling. They range from several thousand to hundreds of thousands of dollars, depending on size and capabilities. CNC routers, particularly hobbyist or entry-level models, are more affordable, making them accessible to small businesses working primarily with non-metallic materials. Outsourcing CNC milling services tends to be more costly than CNC routing, given the higher precision required for metal machining.
In summary, CNC routers and CNC mills are both highly capable machines but serve different purposes. CNC routers are excellent for handling softer materials and larger workpieces, while CNC mills are better suited for complex, precise machining on harder materials. By understanding the key differences in material capabilities, speed, power, and costs, you can make informed decisions about which machine is right for your specific manufacturing needs. Whether investing in equipment or outsourcing services, choosing the correct CNC technology is essential for optimizing your production process.
Get the latest trends and facts about CNC fabrication from our blog.
Shenzhen Runkey Precision Technology Co. Ltd, a subsidiary of the Tensun Group, is your trusted one-stop solution for custom manufacturing from prototyping to production.Transforming your idea into reality with digital manufacturing resources,streamlined processes, expert guidance,accelerated timelines, and uncompromising quality.
©2024. CNC Fabrication All Rights Reserved.