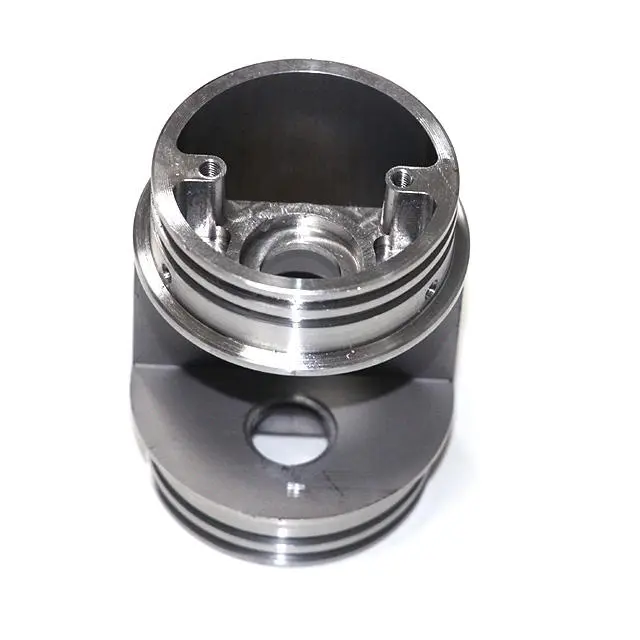
- +8615586668226
- [email protected]
- No. 30, Hongbang Industrial Park, Shenzhen
A threaded hole is a hole that contains internal threads. This allows for the insertion of threaded fasteners, enabling secure assembly.
Understanding threaded holes is vital for producing strong and reliable products.
A tapped hole is a specific type of threaded hole that involves cutting threads into the material.
Tapping creates a precise hole with internal threads, making it an integral aspect of assembly.
Recognizing different types of threaded holes helps to select the right one for specific needs.
Creating a tapped hole involves several precise steps to ensure quality and fit:
Drilling a Pilot Hole
Tapping the Hole
Finishing
Knowing how to create a tapped hole ensures that each component meets desired specifications.
While often used interchangeably, there are subtle differences:
Feature | Threaded Hole | Tapped Hole |
---|---|---|
Definition | Includes any hole with threads | Specifically refers to a hole with cut threads |
Creation | Can use inserts or tapping | Always created by using a tap |
Application | General term encompassing all thread types | More precise, often requiring specific tooling |
Understanding tapped holes vs threaded holes assists in clarifying manufacturing instructions.
Threaded holes are present in various applications, each with unique requirements:
Aerospace
Automotive
Medical Devices
Proficiency in creating threaded holes is essential for success in these fields.
The blind hole is a versatile feature in manufacturing:
Advantages
Challenges
Blind holes are a staple in industrial equipment and construction applications.
Selecting the right type of threaded hole involves assessing several project-specific factors:
Consulting with professionals, like our team at CNC Solutions, ensures optimal designs.
Mastering the art of threaded holes creation requires attention to detail:
Use Appropriate Tools
Ensure Precision
Optimize Machining Conditions
Following these tips ensures the success of threaded holes in your projects.
What is the importance of a tapped hole?
A tapped hole provides the precision required for secure threaded connections in various applications.
How does a blind hole differ from a through hole?
A blind hole does not penetrate the material completely, while a through hole goes all the way through.
Why are internal threads important?
Internal threads enable the use of threaded fasteners, crucial for assembling parts.
How do you prevent breaking a tap when creating a tapped hole?
Use steady pressure and lubrication, and avoid excessive force during the operation.
What materials can be used for threaded holes?
Almost any machinable material can have threaded holes, including metals and plastics.
At our CNC fabrication manufacturing plant, we specialize in precision thread creation tailored to your industry needs, from Automotive to Medical Devices and more.
Explore our services:
Contact us today to advance your manufacturing with expert threaded hole solutions.
Get the latest trends and facts about CNC fabrication from our blog.
Shenzhen Runkey Precision Technology Co. Ltd, a subsidiary of the Tensun Group, is your trusted one-stop solution for custom manufacturing from prototyping to production.Transforming your idea into reality with digital manufacturing resources,streamlined processes, expert guidance,accelerated timelines, and uncompromising quality.
©2024. CNC Fabrication All Rights Reserved.