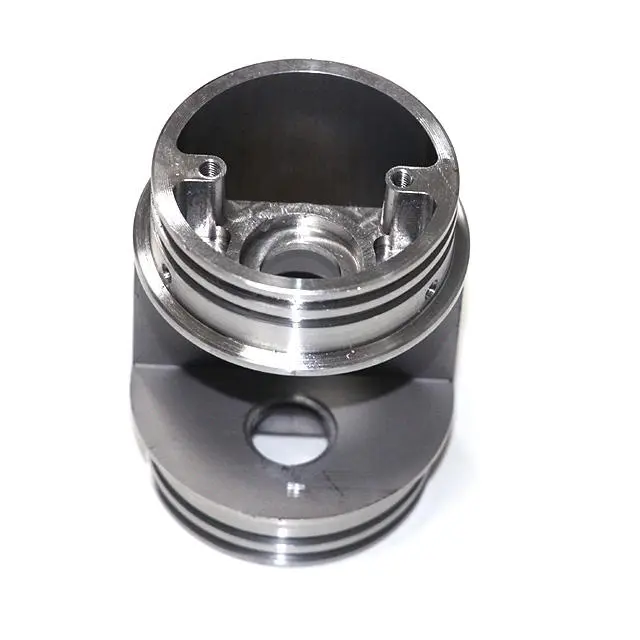
- +8615586668226
- [email protected]
- No. 30, Hongbang Industrial Park, Shenzhen
CNC stands for Computer Numerical Control. A CNC machine is an automated manufacturing tool that uses pre-programmed computer software to dictate the movement of factory tools and machinery. As an experienced CNC fabrication services provider, I’ve witnessed firsthand how these machines have transformed the manufacturing landscape. They operate with unparalleled precision, capable of producing intricate machined parts that would be impossible to create using manual methods. They are used in many industries for making precision parts from materials like metal, plastic, and wood.
The introduction of CNC machines marked a significant leap from traditional manual machining. Before CNC, operations were controlled by hand, which was time-consuming and prone to human error. CNC machines automate these processes, ensuring that each part is produced with consistent quality and accuracy. One of the main factors that set CNC machines apart is their ability to perform complex operations with high precision. These machines operate on multiple axes, allowing for intricate cuts and shapes. For instance, a 5-axis CNC machine can move in five different directions, enabling the creation of extremely complex parts, which is crucial in industries like aerospace and medical device manufacturing.
CNC milling is a pivotal machining process that involves using rotating cutters to remove material from a workpiece. This method is particularly advantageous for rapid prototyping. As someone deeply involved in product development, I can attest to the speed and efficiency that CNC milling brings to the prototyping stage. Unlike 3D printing, which builds parts layer by layer, CNC milling starts with a solid block of material and carves out the desired shape. This subtractive approach is not only faster but also allows for a wider range of materials to be used. It can be used for mass production.
CNC milling machines are known for their versatility. They can create a wide array of shapes and features, from simple slots to complex contours. This makes them ideal for producing prototypes that accurately represent the final product. In my experience, the ability to quickly iterate on designs is crucial in product development. CNC milling allows for rapid adjustments and modifications, saving valuable time and resources. Moreover, the surface finish achieved with CNC milling is often superior to other methods, resulting in a prototype that closely resembles the intended end product.
The operation of a CNC machine is a fascinating blend of mechanical precision and computer programming. At its core, a CNC machine relies on a set of instructions, known as G-code, which directs the movement of the cutting tool. This code is generated using CAD and CAM software. As a machinist, I find the precision of these machines to be remarkable. They can achieve tolerances as tight as 0.005 inches, ensuring that each part is produced to exact specifications.
The cutting tool is a crucial component of any CNC machine. Different tools are used for various operations. For example, an end mill is used for creating flat surfaces, while a standard drill is used for making hole sizes. The choice of tool depends on the material being cut and the desired surface finish. Proper tool selection is vital for achieving optimal results and extending the lifespan of the machine. When used for cutting, the choice of tool is essential. For example, carbide tools are often used for cutting hard materials like stainless steel due to their durability and heat resistance.
There are various types of CNC machines, each designed for specific applications. The most common types include mills, lathes, and routers. Mills are versatile machines that can perform a wide range of operations, such as drilling, cutting, and shaping. Lathes, on the other hand, are primarily used for creating cylindrical parts by rotating the workpiece against a stationary cutting tool. The different CNC machines play critical roles in various manufacturing processes. For instance, CNC milling machines are excellent for producing flat surfaces and complex shapes, while CNC lathes excel in creating cylindrical components. The choice of machine depends on the specific requirements of the project.
The number of axes a CNC machine has also significantly impacts its capabilities. A 3-axis machine can move in three directions: X, Y, and Z. This is sufficient for many basic machining operations. However, for more complex parts, a 5-axis machine may be necessary. These machines can rotate the workpiece, allowing for cuts from multiple angles. 5-axis machining is particularly useful in industries like aerospace and automotive, where intricate and high-precision components are required.
Machining deep pockets presents unique challenges in CNC machining. A deep pocket is a cavity that extends far into the workpiece, creating a narrow and deep space. One of the primary issues is tool access. As the pocket gets deeper, it becomes more difficult for the cutting tool to reach the bottom without hitting the sides. This can lead to tool breakage or a poor surface finish.
To overcome these challenges, specialized tools and techniques are often employed. Long-reach end mills can be used to access deeper areas, but they must be used with care to prevent deflection and vibration. In some cases, it may be necessary to machine the pocket in multiple steps, gradually increasing the depth with each pass. Additionally, using a machine with a high-speed spindle can help improve chip evacuation and reduce the risk of tool damage.
Precision and tolerance are critical aspects of CNC machining. Tolerance refers to the allowable deviation from a specified dimension. In CNC machining, achieving tight tolerances is essential for ensuring that parts fit together correctly and function as intended. As someone who has worked on numerous high-precision projects, I understand the importance of maintaining strict quality control.
CNC machines are capable of achieving incredibly high precision, but this requires careful calibration and maintenance. Factors such as tool wear, machine vibration, and thermal expansion can affect the accuracy of the machining process. Regular machine maintenance and using high-quality cutting tools are crucial for maintaining precision. Additionally, the control system of the CNC machine plays a significant role in ensuring accuracy. Modern CNC machines use advanced servo motors and ball screws to achieve precise movements. For example, incorporating 5 axis CNC machining capabilities can significantly enhance the complexity and precision of the parts produced, catering to the demands of industries like aerospace and medical devices.
Understanding the factors that affect the cost of CNC machined parts is essential for both manufacturers and customers. One of the primary factors is the cost of the machine itself. High-end CNC machines, such as 5-axis CNC milling machines, come with a significant price tag. However, they offer capabilities that can justify the investment for certain applications. The price of the machine is an essential consideration when calculating the overall production costs.
Another important factor is machining time. The longer it takes to machine a part, the higher the cost. Longer machining times are often necessary for complex parts that require multiple operations and intricate cuts. The cost of the cutting tool also plays a role. High-quality tools can be expensive, but they often provide better performance and longer lifespan, which can reduce costs in the long run. In our operations, we meticulously conduct a cost analysis to determine the most cost-effective approach, considering factors like machining time, material costs, and tool expenses. By optimizing these elements, we strive to deliver high precision parts at competitive prices. For example, utilizing CNC turning for cylindrical parts can significantly reduce machining time compared to other methods.
CNC machining has applications across a wide range of industries. In the aerospace sector, CNC machines are used to produce high-precision components for aircraft and spacecraft. The ability to create complex shapes with tight tolerances is crucial in this industry. For instance, 5-axis machining is often used to produce turbine blades and other intricate parts. These components require not only precision but also the ability to withstand extreme conditions, showcasing the critical role of CNC machining in ensuring both performance and safety in aerospace applications.
In the automotive industry, CNC machining is used to manufacture everything from engine parts to custom car accessories. The speed and efficiency of CNC machines make them ideal for producing large volumes of parts with consistent quality. Our work in the automotive sector has shown that CNC machining can significantly reduce lead times and improve the overall quality of components like engine blocks and transmission cases, contributing to higher performance and reliability in vehicles.
The medical device industry also relies heavily on CNC machining. CNC machines are used to create implants, surgical instruments, and other medical devices that require high precision and biocompatible materials. The ability to work with a variety of materials, including titanium and stainless steel, makes CNC machining an excellent choice for this sector.
The field of CNC machining is constantly evolving. One of the most significant trends is the integration of automation and robotics. Automated CNC machines can operate with minimal human intervention, increasing efficiency and reducing labor costs. As someone who is always looking to the future, I believe that automation will play an increasingly important role in CNC machining. Another trend is the rise of 3D printing and other additive manufacturing techniques. While 3D printing has its limitations, it can be used in conjunction with CNC machining to create hybrid manufacturing processes. For instance, a 3D printer can be used to create a near-net shape part, which is then finished using a CNC machine. The future of CNC machining looks promising. Advances in machine technology, software, and materials will continue to drive innovation in the field. The trend toward smaller, more affordable CNC machines is making this technology accessible to a wider range of businesses. Additionally, the use of artificial intelligence and machine learning in CNC machining is expected to enhance process optimization and predictive maintenance.
Choosing the right CNC machine can be a daunting task. There are many factors to consider, including the type of machine, the number of axes, the size of the work envelope, and the cost. As an expert in the field, I recommend starting by identifying your specific needs and requirements. What type of parts will you be machining? What materials will you be working with? What level of precision do you need?
Once you have a clear understanding of your needs, you can begin to research different CNC machines. It’s important to consider not only the initial cost of the machine but also the ongoing maintenance and operating costs. Look for machines that are reliable and well-supported by the manufacturer. Reading reviews and seeking recommendations from other users can also be helpful. Consider the advantages and disadvantages of various machines based on your specific needs. For instance, while a 3-axis CNC milling machine might suffice for simpler tasks, projects requiring intricate details might necessitate a 5-axis model. Understanding these nuances can lead to more informed decisions.
What is CNC machining and how does it differ from manual machining?
CNC machining is a manufacturing process that uses computer numerical control (CNC) to automate the operation of machinery. Unlike manual machining, which relies on human operators to control the tools, CNC machining uses pre-programmed software to dictate the movement of the cutting tools. This results in greater precision, higher efficiency, and the ability to produce complex parts with consistent quality.
What are the advantages of using CNC machining for prototyping?
CNC machining offers several advantages for prototyping, including speed, precision, and material versatility. CNC milling, in particular, is well-suited for creating prototypes quickly and accurately. Unlike additive methods like 3D printing, CNC milling can work with a wide range of materials and produce parts with excellent surface finish.
How does the number of axes affect the capabilities of a CNC machine?
The number of axes determines the complexity of the parts that a CNC machine can produce. A 3-axis machine can move in three directions (X, Y, and Z), which is sufficient for many basic machining operations. However, a 5-axis machine can also rotate the workpiece, allowing for cuts from multiple angles. This makes 5-axis machining ideal for creating complex and intricate parts.
What factors should I consider when choosing a CNC machine?
When choosing a CNC machine, it’s important to consider your specific needs, including the type of parts you will be machining, the materials you will be working with, and the level of precision required. Other factors to consider include the cost of the machine, ongoing maintenance and operating costs, and the level of support provided by the manufacturer.
What is a G-code and how is it used in CNC machining?
G-code is a programming language used to control CNC machines. It consists of a set of instructions that tell the machine how to move the cutting tool, where to cut, and how fast to operate. G-code is typically generated using CAD/CAM software and is essential for ensuring that the CNC machine produces parts according to the desired specifications.
What industries benefit from CNC machining?
CNC machining benefits a wide range of industries, including aerospace, automotive, medical devices, electronics, and consumer products. These industries rely on CNC machining for its precision, efficiency, and ability to produce complex parts from various materials. The versatility of CNC machining makes it a valuable asset in many manufacturing applications.
CNC machining is a versatile and precise manufacturing process used across various industries.
CNC machines automate the operation of machinery, resulting in greater efficiency and accuracy compared to manual methods.
CNC milling is particularly advantageous for rapid prototyping due to its speed, precision, and material versatility.
The number of axes on a CNC machine determines its capabilities, with 5-axis machines offering the ability to create complex and intricate parts.
Factors such as machining time, tool costs, and the cost of the machine itself affect the overall cost of CNC machined parts.
CNC machining has applications in industries such as aerospace, automotive, medical devices, electronics, and consumer products.
Advancements in automation, robotics, and additive manufacturing are shaping the future of CNC machining.
Choosing the right CNC machine requires careful consideration of your specific needs, budget, and the level of support provided by the manufacturer.
For further assistance with your CNC machining needs, please don’t hesitate to contact us.
Explore our comprehensive fabrication services to discover how we can support your projects with precision and expertise.
Discover the precision of our CNC turning services, tailored to meet your specific requirements.
Learn about the intricacies of 5-axis CNC machining and how it can elevate the complexity and quality of your parts.
Dive into the world of CNC solutions to see the range of possibilities we offer for your manufacturing needs.
By integrating our expertise with cutting-edge technology, we are dedicated to delivering exceptional results that meet the highest standards of quality and precision. Whether you are in the aerospace, automotive, medical, or any other industry, our CNC machining services are designed to provide innovative solutions tailored to your unique requirements.
Get the latest trends and facts about CNC fabrication from our blog.
Shenzhen Runkey Precision Technology Co. Ltd, a subsidiary of the Tensun Group, is your trusted one-stop solution for custom manufacturing from prototyping to production.Transforming your idea into reality with digital manufacturing resources,streamlined processes, expert guidance,accelerated timelines, and uncompromising quality.
©2024. CNC Fabrication All Rights Reserved.