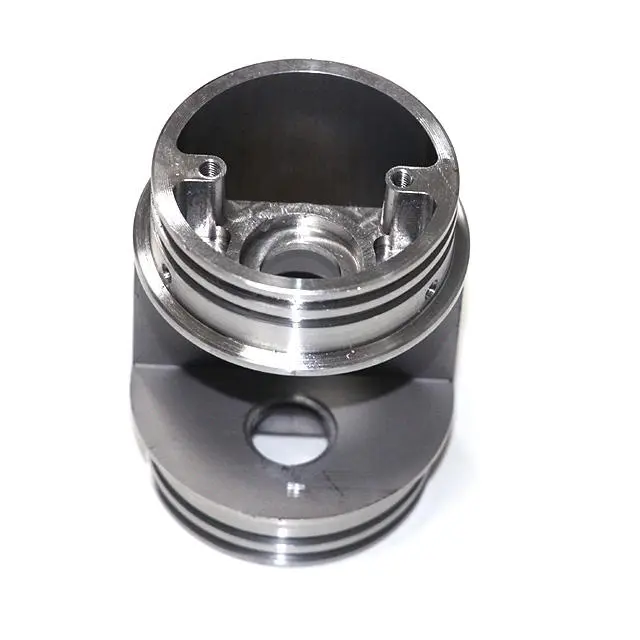
- +8615586668226
- [email protected]
- No. 30, Hongbang Industrial Park, Shenzhen
Precision in CNC machining is not just a desirable attribute; it’s the bedrock upon which industries like aerospace, medical devices, and electronics rely. The ability of a CNC machine to produce parts with exact dimensions, often within a few micrometers, determines the functionality, safety, and reliability of the final product. As a company specializing in CNC fabrication services, we’ve witnessed firsthand how precision directly impacts our clients’ success. For example, in the aerospace industry, the slightest deviation from specified dimensions can compromise the integrity of an aircraft component.
Moreover, precision machining allows for the creation of intricate designs and complex geometries that would be impossible with less accurate methods. This capability opens up new possibilities in product development, enabling innovation and enhancing performance across various applications. Our experience has shown that customers who prioritize precision in their CNC projects often see significant improvements in product quality and efficiency. We are a CNC fabrication services company dedicated to offering the best manufacturing solutions.
The 0.0001mm increment, also known as the least input increment, represents the smallest movement a CNC machine can execute along an axis. This tiny increment is crucial for achieving high precision in machining operations. When a machine can move and cut at such fine intervals, it can produce parts with incredibly smooth surfaces and precise features. For instance, when creating molds for injection molding, achieving a 0.0001mm increment ensures that the final product will have the desired shape and surface finish, free of imperfections.
In practical terms, a smaller increment system allows for finer control over the cutting tool’s path, reducing the risk of errors and improving the overall quality of the machined part. Our CNC machinists regularly work with these minute increments, leveraging our machines’ capabilities to meet the stringent requirements of industries like medical devices and electronics, where precision is paramount. This degree of accuracy is particularly beneficial in milling and turning applications, where complex shapes and tight tolerances are common.
Tolerance in CNC machining refers to the allowable deviation from the specified dimensions of a part. It defines the range within which a feature’s actual size can vary and still be considered acceptable. Tolerances are essential because achieving absolute perfection in manufacturing is practically impossible. Instead, engineers define an acceptable range of variation that ensures the part will function as intended without unnecessary cost or effort.
Small tolerances, such as those enabled by the 0.0001mm increment, are critical in applications where precise fit and alignment are crucial. For example, in the assembly of medical devices, even a slight misalignment can affect the device’s performance and safety. As a provider of CNC fabrication services, we work closely with our clients to understand their tolerance requirements and ensure our machines are calibrated to deliver the required precision. The tolerance band defines the upper and lower limits of acceptable variation, and our goal is always to work within its tolerance band, aiming for the mean value to achieve optimal results.
The debate between the metric and imperial measurement systems in CNC machining is a long-standing one. While both systems have their merits, the metric system, particularly when dealing with increments as small as 0.0001mm, offers certain advantages. The metric system’s decimal nature makes it inherently more compatible with digital CNC controls, simplifying calculations and reducing the risk of errors.
Many CNC machines are designed to operate in metric mode by default, with the 0.0001mm increment representing a standard level of precision achievable by modern machines. The equivalent in the imperial system, 0.00001 inch, is less commonly used and can be more challenging to work with due to the need for more decimal places. Our experience suggests that working in the metric measurement system provides a better resolution than the imperial system, especially when dealing with very small tolerances. 0.001 mm is less than half of 0.0001 inch, making it a finer unit for precision work.
Offset adjustments are a critical aspect of CNC machining, especially when striving for high precision. An offset is a correction applied to the programmed toolpath to compensate for variations in tool size, workpiece position, or machine calibration. In the context of a 0.0001mm increment, even the slightest discrepancy can impact the final dimensions of a part, making offset adjustments essential.
For example, if a cutting tool is slightly smaller than specified in the program, the CNC machinist can apply an offset to ensure the machine cuts to the correct depth and size. Similarly, if the workpiece is not perfectly aligned, an offset can be used to adjust the cutting path accordingly. Our CNC machinists are highly skilled in making these offset adjustments, using precise measuring tools and their expertise to achieve the desired precision. Offset adjustment is particularly important in applications like precision machining, where even minute deviations can be critical.
Maintaining small tolerances, such as those achievable with a 0.0001mm increment, presents several challenges in CNC machining. One of the primary challenges is thermal expansion. As a machine operates and heats up, both the cutting tool and the workpiece can expand, potentially affecting the dimensions of the finished part. To mitigate this, modern machine shops often use temperature-controlled environments and advanced cooling systems.
Another challenge is tool wear. Even the most durable cutting tools will wear down over time, which can affect their size and shape, leading to deviations from the desired dimensions. Regular tool inspection, replacement, and the use of offset adjustments are crucial for maintaining precision. Additionally, factors like machine vibration, spindle runout, and even the type of material being machined can impact the ability to hold small tolerances. Our CNC fabrication services address these challenges through rigorous quality control processes, regular maintenance, and the use of advanced manufacturing technologies.
Not all CNC machines are capable of achieving a 0.0001mm increment. The ability to reach such fine levels of precision depends on various factors, including the machine’s design, construction, and the quality of its components. High-end machines, often used in industries like aerospace and medical device manufacturing, are typically designed with superior components and advanced control systems that enable them to achieve and maintain incredibly small increments.
For example, machines from manufacturers like GF Machining Solutions are renowned for their precision and ability to work with extremely tight tolerances. However, it’s important to note that even with the most advanced machine, achieving a 0.0001mm increment consistently requires careful calibration, precise programming, and skilled operation. Our modern machine shop invests in top-of-the-line equipment and employs experienced CNC machinists to ensure we can meet our clients’ most demanding precision requirements.
The choice between the metric and imperial measurement system can significantly impact precision in CNC machining. As mentioned earlier, the metric system, with its decimal-based units, often offers advantages when working with very small increments like 0.0001mm. This is because metric units can be easily divided and multiplied by powers of 10, simplifying calculations and reducing the risk of errors in programming and offset adjustments.
In contrast, the imperial system, with its fractions and less intuitive divisions, can be more challenging to work with when high precision is required. For example, half of 0.0001 inch is 0.00005 inch, which requires more decimal places and can be more prone to rounding errors. While modern CNC controls can handle both systems, our experience suggests that the metric system often provides a better resolution and is generally preferred for high-precision applications.
Modern CNC machining benefits from a range of advanced technologies that enhance precision and enable the achievement of incredibly small increments like 0.0001mm. One such technology is linear motors. Unlike traditional ball screws, linear motors provide faster, more accurate, and smoother motion, significantly improving a machine’s positioning accuracy. They are very useful in 5 axis cnc machining.
Another important technology is high-resolution encoders. These devices provide precise feedback on the position of the machine’s axes, allowing the control system to make minute adjustments in real-time. When combined with advanced control algorithms, high-resolution encoders enable CNC machines to achieve and maintain extremely tight tolerances.
Additionally, technologies like 3D printing and additive manufacturing are increasingly being integrated with CNC machining to create hybrid manufacturing processes. These processes combine the precision of CNC machining with the design freedom of additive manufacturing, opening up new possibilities for creating complex, high-precision parts.
As a leading provider of CNC fabrication services, we understand the critical importance of precision in modern manufacturing. Our state-of-the-art facility houses a wide range of advanced CNC machines, including turning centers, machining centers, and specialized equipment for milling and turning applications. We invest in top-of-the-line equipment from reputable manufacturers and continually update our capabilities to stay at the forefront of manufacturing technologies.
Our team of experienced CNC machinists is skilled in working with a variety of materials and can handle projects ranging from simple prototypes to complex, high-volume production runs. We pride ourselves on our ability to achieve incredibly tight tolerances, including those enabled by the 0.0001mm increment. Our rigorous quality control processes, combined with our expertise in offset adjustments and precision measurement, ensure that every part we produce meets the highest standards of quality and accuracy.
But what truly sets us apart is our commitment to customer satisfaction. We work closely with each client to understand their unique needs and provide tailored manufacturing solutions that meet their specific requirements. Whether you need rapid prototyping for a new product or high-volume production of precision components, we have the expertise and capabilities to deliver exceptional results.
What is a CNC machine and how does it work?
A CNC machine is a computer-controlled cutting machine that uses pre-programmed instructions to precisely cut and shape materials. It works by interpreting digital designs (CAD) and translating them into precise movements of cutting tools.
What does ‘tolerance’ mean in CNC machining?
Tolerance in CNC machining refers to the permissible variation from a specified dimension. It defines the acceptable range within which a feature’s actual size can vary.
Why is the metric system often preferred in high-precision CNC machining?
The metric system is often preferred due to its decimal nature, which simplifies calculations and reduces the risk of errors when working with small increments like 0.0001mm.
What is an offset adjustment in CNC machining?
An offset adjustment is a correction applied to the programmed toolpath to compensate for variations in tool size, workpiece position, or machine calibration, ensuring precise machining.
Can CNC machining be combined with other manufacturing processes?
Yes, CNC machining can be integrated with other processes like 3D printing and additive manufacturing to create hybrid manufacturing solutions that offer enhanced design flexibility and precision.
How do I choose the right CNC fabrication service for my project?
Consider factors like the provider’s experience, equipment capabilities, quality control processes, and ability to meet your specific precision and tolerance requirements.
Precision in CNC machining, particularly at the 0.0001mm increment, is crucial for industries requiring high accuracy and reliability.
The metric measurement system often offers advantages in high-precision CNC applications due to its decimal nature.
Offset adjustments are essential for compensating for variations and ensuring precise machining to specified dimensions.
Maintaining small tolerances presents challenges such as thermal expansion and tool wear, requiring advanced technologies and rigorous quality control.
Not all CNC machines can achieve a 0.0001mm increment; it depends on the machine’s design, construction, and components.
Advanced technologies like linear motors and high-resolution encoders enhance precision in modern CNC machining.
Choosing the right CNC fabrication service involves considering their experience, equipment, quality control, and ability to meet specific precision needs.
Our CNC fabrication services offer state-of-the-art equipment, experienced CNC machinists, and a commitment to customer satisfaction, making us an ideal partner for high-precision projects.
By understanding the intricacies of CNC machining and the importance of precision, businesses can make informed decisions and achieve superior results in their manufacturing endeavors.
If you have any questions please reach out to us via our contact form
Get the latest trends and facts about CNC fabrication from our blog.
Shenzhen Runkey Precision Technology Co. Ltd, a subsidiary of the Tensun Group, is your trusted one-stop solution for custom manufacturing from prototyping to production.Transforming your idea into reality with digital manufacturing resources,streamlined processes, expert guidance,accelerated timelines, and uncompromising quality.
©2024. CNC Fabrication All Rights Reserved.