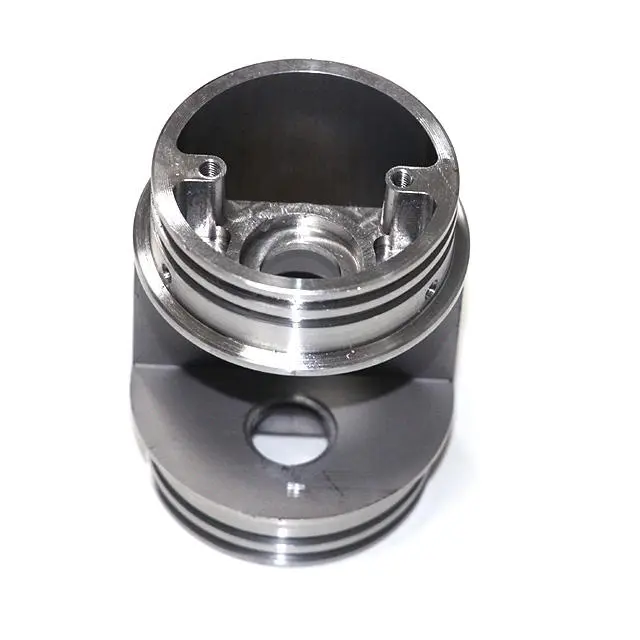
- +8615586668226
- [email protected]
- No. 30, Hongbang Industrial Park, Shenzhen
This article will demystify the factors influencing sheet metal fabrication costs, providing you with essential insights to make informed decisions for your next project. Whether you’re in the aerospace, automotive, medical, or any other industry, understanding these cost drivers can help you optimize your budget and achieve the best value for your investment. This comprehensive guide will explore everything you need to know about sheet metal fabrication pricing, making it worth your time to delve into the details.
What is Sheet Metal Fabrication and Why is it Important?
How Does the Raw Material Impact Sheet Metal Fabrication Costs?
What Role Do Labor Costs Play in Metal Fabrication Pricing?
How Can Customization Affect the Average Cost of Sheet Metal Products?
Can a Sheet Metal Fabricator Help Reduce Costs?
What are Common Sheet Metal Fabrication Processes and Their Costs?
How Do Maintenance Costs Factor into the Overall Price?
What’s the Best Way to Estimate Sheet Metal Fabrication Costs?
Can Using a Sheet Metal Fabrication Cost Calculator Provide Accurate Projections?
How Can You Optimize Your Sheet Metal Fabrication Project for Cost-Effectiveness?
Sheet metal fabrication is a crucial manufacturing process that involves cutting, bending, and assembling sheet metal into desired shapes and structures. From the chassis of your car to the casing of your electronic devices, sheet metal components are ubiquitous, making this process fundamental across various industries. My company, cnc fabrication services, specializes in providing high-quality sheet metal fabrication solutions for a diverse range of applications, including aerospace, automotive, medical devices, electronics, and more.
The importance of sheet metal fabrication lies in its versatility and ability to create durable, precise, and cost-effective parts. It’s a cornerstone of modern manufacturing, enabling the production of both simple and complex designs with high accuracy. Understanding sheet metal fabrication is essential for anyone involved in product development, as it directly impacts the quality, functionality, and cost of the final product. By utilizing our machining services, we can ensure that each part meets the stringent quality standards required in these demanding sectors.
The cost of the raw material is a significant factor in determining metal fabrication costs. Different types of sheet metal, such as steel, aluminum, and copper, vary in price based on their properties, availability, and market demand. For instance, stainless steel is generally more expensive than mild steel due to its superior corrosion resistance and strength. In my experience, choosing the right material is a balance between performance requirements and budget constraints. For example, for aerospace components, high-grade aluminum or titanium might be necessary, while automotive parts can often utilize more cost-effective steel alloys. The material cost can constitute a substantial portion of the overall sheet metal fabrication cost, and fluctuations in the market can significantly impact the final price. It is advisable to partner with experienced sheet metal fabricators who can guide you in material selection.
Furthermore, the thickness and size of the sheet metal also influence the raw material cost. Thicker sheets are typically more expensive, and larger parts require more material, leading to higher costs. When designing your project, it’s important to consider standard sheet metal sizes to minimize waste and optimize material usage. Additionally, purchasing sheet metal in bulk or through established suppliers can often lead to cost savings. As a company deeply embedded in the industry, we leverage our extensive network to procure high-quality materials at competitive prices, passing those savings on to our customers.
Labor costs are another critical component of metal fabrication pricing. The complexity of the project, the skill level of the fabricator, and the geographic location all play a role in determining the hourly cost of labor. Highly intricate designs or projects requiring specialized techniques, such as 5 axis CNC machining, often demand more time and expertise, leading to higher labor costs. Moreover, experienced metal fabricators with a proven track record command higher rates due to their ability to deliver superior quality and efficiency.
At cnc fabrication services, we pride ourselves on our team of highly skilled professionals. Our fabricators are proficient in various techniques, including laser cutting, welding, and metal bending using a press brake. They undergo continuous training to stay abreast of the latest industry advancements, ensuring that we deliver top-notch results. While our labor costs may reflect the expertise we offer, we strive to balance quality with affordability. We achieve this through efficient project management, optimized workflows, and a commitment to continuous improvement. As a result, we can offer competitive fabrication pricing without compromising on the quality and precision that our clients expect, making us a preferred partner for projects across diverse industries like aerospace and automotive.
Customization significantly impacts the average cost of sheet metal products. Standard, off-the-shelf components are typically more affordable than custom metal parts due to economies of scale. When you require custom designs or specialized features, the fabrication process becomes more complex, involving additional design work, tool setup, and potentially specialized manufacturing techniques. For instance, creating unique shapes or incorporating intricate patterns may necessitate the use of advanced techniques like laser cutting or wire EDM, increasing the manufacturing cost.
However, customization can also lead to long-term cost savings and improved functionality. Tailoring parts to your specific needs can enhance performance, reduce assembly time, and minimize the need for modifications down the line. At cnc fabrication services, we specialize in creating custom solutions that meet the unique requirements of our clients. We work closely with you to understand your needs and develop designs that optimize both form and function. Our expertise in CNC machining and rapid prototyping allows us to create prototypes and refine designs efficiently, reducing overall production cost in the long run.
Absolutely! A skilled metal fabricator can be instrumental in helping you reduce costs throughout the fabrication process. They can offer valuable insights into design optimization, material selection, and manufacturing techniques that can significantly impact the overall cost of your project. For example, they might suggest alternative materials that offer similar performance at a lower cost or recommend design modifications that simplify the fabrication process and minimize material waste. With years of experience, our team can quickly identify areas where costs can be optimized without compromising quality.
Moreover, experienced sheet metal fabricators often have established relationships with material suppliers, allowing them to source raw materials at competitive prices. They can also leverage their expertise to minimize lead times and streamline production, reducing labor and overhead costs. At cnc fabrication services, we view ourselves as partners in our clients’ success. We work collaboratively with you from the initial stages of product development to identify cost-saving opportunities and optimize your project for maximum efficiency.
Several processes are involved in sheet metal fabrication, each with its own cost implications.
Cutting: This is the initial step where the sheet metal is cut into the desired shape. Common cutting methods include shearing, laser cutting, and punching. Laser cutting is particularly precise and efficient, especially for intricate designs, but it can be more expensive than traditional methods. At cnc fabrication services, we offer both laser cutting and CNC turning services to cater to a wide range of cutting needs.
Bending: This process involves shaping the sheet metal using tools like a press brake. The complexity of the bends and the thickness of the material influence the cost. Simple bends are relatively inexpensive, while complex or multiple bends require more time and specialized tooling. For instance, our metal bending services are tailored to handle diverse project requirements, from simple to highly intricate designs.
Welding: This is used to join multiple sheet metal parts together. The type of weld required, the material, and the size of the project all impact the cost. For example, TIG welding offers high precision but is typically more expensive than MIG welding. Our skilled welders are proficient in various welding techniques, ensuring strong and durable joints.
Finishing: This includes processes like deburring, grinding, powder coating, anodizing, and painting. Finishing adds to the aesthetic appeal and durability of the product but also increases the overall cost.
Understanding these processes and their associated costs is crucial for budgeting your project. At cnc fabrication services, we offer a comprehensive range of sheet metal fabrication services, including cutting, bending, welding, and finishing. Our team can guide you through each step of the process, helping you make informed decisions that align with your budget and quality expectations.
Maintenance costs are often overlooked but play a significant role in the overall cost of sheet metal products. Choosing durable materials and high-quality fabrication techniques can minimize the need for future repairs and replacements, reducing long-term expenses. For example, using corrosion-resistant materials like stainless steel or applying protective finishes like powder coating can extend the lifespan of your product and reduce maintenance costs. When considering metal fabrication costs, it’s important to look beyond the initial investment and consider the potential expenses associated with upkeep and repairs.
At cnc fabrication services, we prioritize quality and durability in our fabrication process. We use high-grade materials and employ rigorous quality control measures to ensure that our products withstand the test of time. While this may result in a slightly higher upfront cost, it can lead to significant savings in the long run by minimizing the need for maintenance and extending the product’s lifespan. We also offer surface finishing services, such as anodizing and galvanizing, to enhance the durability and longevity of your parts, making them suitable for demanding environments in industries like aerospace and energy.
Estimating sheet metal fabrication costs accurately requires careful consideration of various factors, including material costs, labor costs, design complexity, and production volume. One effective approach is to break down the project into individual components and estimate the cost of each based on the specific fabrication process required. For example, you can calculate the material cost by determining the amount of sheet metal needed and multiplying it by the cost per unit. Labor costs can be estimated by considering the time required for each operation and multiplying it by the hourly rate of the fabricator.
Another valuable tool is to consult with experienced sheet metal fabricators. They can provide insights into potential cost drivers, suggest design optimizations, and offer accurate quotes based on your project specifications. At cnc fabrication services, we offer free consultations and detailed quotes to help you understand the cost implications of your project. We can also provide cost analysis to improve your pricing strategy. Our team can analyze your design, recommend cost-effective materials and techniques, and provide a comprehensive breakdown of the metal fabrication cost.
While a sheet metal fabrication cost calculator can be a helpful starting point, it’s important to understand its limitations. These calculators typically provide rough estimates based on general parameters and may not account for the specific nuances of your project. Factors such as design complexity, material availability, and the expertise of the fabricator can significantly impact the final cost, and these are often not fully captured by online calculators. They are primarily designed to offer a ballpark figure and may not reflect the actual cost data or fabrication pricing of a specialized service provider.
That said, a sheet metal fabrication cost calculator can be useful for obtaining a preliminary understanding of potential costs and comparing different materials or processes. However, it’s always best to consult with a professional metal fabricator for accurate and detailed cost projections. At cnc fabrication services, we offer personalized quotes based on your specific project requirements. We take into account all relevant factors, including design complexity, material selection, production volume, and lead times, to provide you with a precise estimate.
Optimizing your sheet metal fabrication project for cost-effectiveness involves careful planning, design considerations, and collaboration with your fabricator. Here are some tips to help you reduce costs without compromising quality:
Design for Manufacturability: Simplify your design to minimize the number of operations required during fabrication. Avoid overly complex shapes or features that necessitate specialized tooling or techniques.
Optimize Material Usage: Choose standard sheet metal sizes to minimize waste and reduce material costs. Consider using pre-plated sheet metal to eliminate the need for post-fabrication finishing.
Consolidate Parts: Combine multiple parts into a single component to reduce assembly time and labor costs.
Choose the Right Material: Select a material that meets your performance requirements without being unnecessarily expensive. For example, consider using uncoated cold rolled steel for components that don’t require high corrosion resistance.
Plan for Volume: Higher production volumes often lead to lower per-unit costs due to economies of scale.
Collaborate with Your Fabricator: Work closely with your fabricator from the early stages of product development to identify cost-saving opportunities.
At cnc fabrication services, we specialize in helping our clients optimize their projects for cost-effectiveness. We offer design assistance, material recommendations, and process optimization to ensure that you get the best value for your investment. Our expertise in CNC solutions, including on-demand manufacturing and assembly, allows us to streamline production and reduce overall costs.
1. What is the average cost of sheet metal fabrication?
The average cost of sheet metal fabrication varies widely depending on factors such as material, design complexity, and production volume. It’s best to obtain a personalized quote from a fabricator for an accurate estimate.
2. How can I reduce the cost of my sheet metal project?
You can reduce costs by optimizing your design, choosing cost-effective materials, consolidating parts, planning for volume, and collaborating with your fabricator.
3. What is the most expensive part of sheet metal fabrication?
The most expensive part can vary, but often it’s either the raw material cost or the labor cost associated with complex designs and specialized techniques.
4. How does the type of metal affect the fabrication cost?
The type of metal significantly impacts the cost. For instance, stainless steel is generally more expensive than mild steel due to its superior properties.
5. Does the size of sheet metal parts affect the cost?
Yes, the size of sheet metal parts directly affects the cost, as larger parts require more material and may be more challenging to fabricate.
6. What is the typical lead time for a sheet metal fabrication project?
Lead times vary depending on the project’s complexity, the fabricator‘s workload, and material availability. It’s best to discuss lead times with your fabricator during the planning stages. We offer various CNC solutions like rapid prototyping to reduce lead times whenever possible.
Here are the most important things to remember about sheet metal fabrication costs:
Raw material costs are a significant factor, influenced by the type, thickness, and size of the sheet metal.
Labor costs depend on the complexity of the project, the skill level of the fabricator, and the geographic location.
Customization can increase costs but also lead to long-term benefits.
A skilled fabricator can help reduce costs through design optimization, material selection, and process efficiency.
Understanding the various fabrication processes and their associated costs is crucial for budgeting.
Maintenance costs should be considered in the overall cost of ownership.
Accurate cost estimation requires careful consideration of all relevant factors.
While sheet metal fabrication cost calculators can provide rough estimates, it’s best to consult with a professional for precise projections.
Optimizing your project for cost-effectiveness involves design considerations, material selection, and collaboration with your fabricator.
By understanding these key takeaways, you can make informed decisions, optimize your sheet metal fabrication projects, and achieve the best value for your investment. At cnc fabrication services, we are committed to providing high-quality, cost-effective sheet metal fabrication solutions tailored to your specific needs. Contact us today to get started on your next project and experience the difference that expertise and dedication can make.
Internal Links:
Get the latest trends and facts about CNC fabrication from our blog.
Shenzhen Runkey Precision Technology Co. Ltd, a subsidiary of the Tensun Group, is your trusted one-stop solution for custom manufacturing from prototyping to production.Transforming your idea into reality with digital manufacturing resources,streamlined processes, expert guidance,accelerated timelines, and uncompromising quality.
©2024. CNC Fabrication All Rights Reserved.