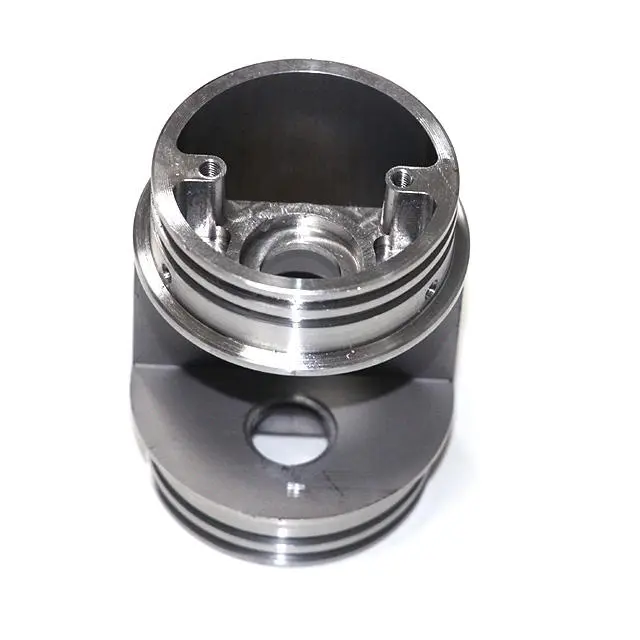
- +8615586668226
- [email protected]
- No. 30, Hongbang Industrial Park, Shenzhen
The Society of the Plastics Industry (SPI) has established a set of standards for surface finishes on injection molds. These standards help ensure consistency and quality across the plastic industry. As someone who’s been in the CNC fabrication service for years, I can tell you that adhering to these SPI surface finish standards is not just about meeting requirements. It’s about delivering excellence. Each standard, from SPI-A1 to SPI-D3, dictates a specific surface roughness and texture, achieved through various polishing techniques. For instance, an SPI-A1 finish requires a diamond buff polish, resulting in a mirror-like shine, often desired in consumer products and medical devices for their aesthetic appeal and ease of cleaning.
Understanding these standards is crucial. Imagine ordering a batch of injection molded parts only to find the surface finish doesn’t meet your expectations. It can lead to delays, increased costs, and even product failure. That’s why at my facility, we meticulously follow these guidelines. For instance, when we produce parts for the aerospace industry, a high-gloss finish isn’t just about looks, it impacts aerodynamics. While for automotive components, a textured finish might be required for grip or to reduce glare.
The mold surface is the blueprint for your part’s finish. Any imperfection, scratch, or texture on the mold will directly transfer to the molded part. From my experience, this is where many projects hit a snag if not carefully managed. I always emphasize to my clients that the quality of the mold finish is as important as the material selection. A well-prepared mold ensures that the surface finish of the final product is exactly as intended.
Consider this: a mold designed for a glossy finish needs a highly polished surface, typically achieved through diamond buffing. If the mold surface isn’t perfectly smooth, the molded parts will show imperfections. Similarly, for a matte finish, the mold might be treated with abrasive blasting to create a uniform, non-reflective surface. It’s a direct correlation – the smoother the mold surface, the glossier the part. And the rougher the mold surface, the more matte or textured the molded part will be. We’ve successfully applied this in projects for robotics and industrial equipment, where the surface finish can significantly impact the product’s functionality and durability.
Yes, there are twelve SPI mold finishes, categorized into four grades: A, B, C, and D. Each grade offers a different level of surface finish, ranging from mirror-like to dull. Here’s a quick breakdown based on my hands-on experience:
Grade | Description | Typical Applications |
A | Highly polished, mirror-like finish | Lenses, optical parts, high-end consumer goods |
B | Semi-glossy, smooth finish | Housings, covers, general-purpose parts |
C | Matte finish, some texture | Functional parts, internal components |
D | Rough, textured finish, often with visible machining marks | Parts requiring grip, non-slip surfaces |
From producing plastic injection molded parts for electronics with a smooth SPI-B finish to creating rugged components for heavy equipment with an SPI-D textured finish, I’ve seen firsthand how choosing the right grade impacts the end product. For example, grade A finishes, which include SPI-A1, SPI-A2, and SPI-A3, are achieved using diamond buffing, resulting in that highly sought-after mirror shine. These are perfect for parts where appearance is paramount. On the other hand, grade D finishes like SPI-D2, obtained through dry blasting with glass beads, provide a non-directional, textured matte finish that’s great for parts needing extra grip.
While SPI is a widely recognized standard in North America, VDI 3400 is another important standard, particularly in Europe. VDI, set by the Association of German Engineers (Verein Deutscher Ingenieure), also defines surface texture but uses a different scale. In my work, I often encounter clients who are familiar with one but not the other, leading to potential misunderstandings. It’s crucial for anyone in this industry to grasp both standards.
Here’s a simplified comparison:
SPI: Primarily based on visual appearance and uses grades A, B, C, and D.
VDI 3400: More focused on the technical roughness average (Ra) value measured in micrometers (µm).
For instance, a VDI 3400 grade of 18 corresponds roughly to an Ra of 0.80 µm, which might align with an SPI-B2 finish. However, it’s not always a direct translation. A VDI 3400 texture or surface finish standard provides a more technical specification, while SPI mold finishes we offer often lean towards the visual aspect. As a rule of thumb, if your project involves international partners or is based in Europe, familiarizing yourself with VDI injection molding standards is essential. I always advise my clients, “When in doubt, specify both SPI and VDI values to avoid any confusion.”
SPI glossy finishes are all about achieving that high shine, mirror-like surface. These are the SPI-A grades, specifically A1, A2, and A3. From my years in the business, I can tell you that these finishes are not just about aesthetics, they are about precision. Achieving a perfect SPI-A1, the highest gloss level, requires meticulous polishing with diamond compounds. It’s a painstaking process, but the results are stunning.
These SPI glossy finishes are ideal for products where visual appeal is paramount. Think of the sleek, shiny surfaces of high-end electronic casings or the flawless clarity of optical lenses. We’ve used SPI-A finishes in numerous projects, including creating medical devices where a smooth, easily sanitized surface is crucial. The key to success with these finishes is starting with a high-quality mold and using the right polishing techniques. It’s a delicate balance of applying the right pressure and using the correct grade of diamond compound to achieve that perfect shine without damaging the mold surface.
SPI semi-glossy finishes, namely SPI-B1, B2, and B3, offer a balance between shine and practicality. These finishes provide a smooth surface but without the mirror-like reflection of the A-grade finishes. I often recommend SPI semi-glossy finishes for parts that need to look good but also be resistant to fingerprints and minor scratches. These are your everyday workhorses of the plastic industry.
Consider the housing of a handheld electronic device. It needs to be visually appealing but also durable enough to withstand daily handling. An SPI-B2 finish, achieved through fine grit sandpaper polishing, strikes that perfect balance. It’s smooth to the touch, hides minor imperfections, and doesn’t show fingerprints as readily as a high-gloss finish. We’ve successfully used these finishes in projects ranging from automotive interior components to parts for consumer products where durability and aesthetics go hand in hand.
SPI matte finishes, encompassing SPI-C1, C2, and C3, are all about creating a non-reflective, uniform surface. These finishes are achieved using stone polishing, resulting in a slightly textured surface that diffuses light. I find that SPI matte finishes are often misunderstood. They’re not just about reducing glare; they can also add a tactile quality to the molded part.
These finishes are particularly useful for internal components where light reflection could be an issue, such as inside machinery or industrial equipment. They’re also great for parts that require painting or labeling, as the slightly rough surface texture provides better adhesion. I recall a project where we used an SPI-C2 finish for parts in a piece of new energy equipment. The matte finish not only reduced glare but also provided a better surface for the application of warning labels. It was a perfect example of how choosing the right surface finish can enhance both form and function.
Textured surface finishes in injection molding, represented by the SPI-D grades, go beyond just matte. They introduce a deliberate texture to the surface of the molded part. This can range from a light stipple to a more pronounced pattern. From my experience, textured surface finishes serve both aesthetic and functional purposes. They can hide minor imperfections, provide grip, and even mimic the look of other materials like leather or wood.
Achieving these textures requires special treatment of the mold surface, often through chemical etching or dry blasting. For example, an SPI-D2 finish, created by dry blasting with glass beads, results in a uniform, non-directional texture. This is often used in parts for the aerospace industry where a non-slip surface is crucial. I’ve also seen a growing trend in using textured finishes in consumer products to create unique tactile experiences. It’s a fascinating area where design and functionality converge, and the possibilities are virtually endless.
Choosing the right surface finish is a critical decision that impacts both the aesthetics and functionality of your injection molded parts. It’s not a one-size-fits-all scenario. I always advise my clients to consider the following factors:
End-Use Application: How will the part be used? Will it be visible to the end-user? Does it need to withstand wear and tear?
Material Choice: Different injection molding materials react differently to various finishes. A plastic that works well with a glossy finish might not be suitable for a textured one.
Aesthetic Requirements: What is the desired look and feel of the part? Is a high-gloss finish necessary, or would a matte or textured finish be more appropriate?
Functional Needs: Does the part require specific properties like grip, light diffusion, or ease of cleaning?
Cost: Generally, the higher the gloss level, the more expensive the mold preparation and injection molding process.
For instance, if you’re producing parts for medical devices, a smooth, easily cleanable surface like SPI-A might be necessary. For automotive interiors, an SPI-B semi-glossy finish could offer the right balance of aesthetics and durability. And for parts requiring a non-slip grip, such as tools or handles, an SPI-D textured finish would be ideal. Always remember, the right surface finish can elevate a good product to a great one.
Material selection plays a crucial role in how the final surface finish turns out. Not all plastics are created equal when it comes to accepting different finishes. From my experience, this is a factor that’s often overlooked, leading to unexpected results.
Here’s a simple table illustrating how common injection molding materials interact with different SPI finishes:
Material | Glossy (SPI-A) | Semi-Glossy (SPI-B) | Matte (SPI-C) | Textured (SPI-D) |
ABS | Good | Excellent | Good | Excellent |
Polycarbonate (PC) | Excellent | Good | Fair | Good |
Polypropylene (PP) | Fair | Good | Excellent | Good |
Nylon (PA) | Good | Fair | Good | Excellent |
For example, Polycarbonate (PC) takes on a glossy finish beautifully, making it ideal for optical parts. ABS, on the other hand, works well with a wider range of finishes, from semi-glossy to textured, making it a versatile choice for various applications. I always emphasize to my clients that understanding the interplay between material properties and surface finish options is crucial. It’s not just about choosing a plastic that’s strong or flexible; it’s about selecting one that can achieve the desired finish while meeting the functional requirements of the part.
What is the most common SPI finish used in the plastic industry?
The most common SPI finishes are SPI-B1, B2, and B3. These semi-glossy finishes offer a good balance of visual appeal and practicality, making them suitable for a wide range of applications.
Can any mold be used to achieve any SPI finish?
No, the mold must be specifically prepared to achieve the desired SPI finish. For instance, a mold designed for an SPI-A1 finish will have a highly polished surface, while a mold for an SPI-D2 finish will have a textured surface created through dry blasting.
How does VDI 3400 relate to SPI finishes?
VDI 3400 is a different standard that also defines surface texture, primarily used in Europe. While there’s no direct conversion, you can find approximate equivalents. For example, a VDI 3400 grade of 18 might be roughly similar to an SPI-B2 finish.
Is a higher gloss SPI finish always better?
Not necessarily. While SPI glossy finishes like A1 are visually appealing, they might not be suitable for all applications. They can be more expensive, show fingerprints more readily, and might not provide the necessary grip or texture for certain parts.
What’s the best SPI surface finish for parts that need to be painted?
For parts that require painting, an SPI-C finish is often preferred. The slightly rougher surface texture provides better adhesion for the paint.
How can I ensure consistency in surface finish across large production runs?
Maintaining consistency requires careful control of the injection molding process, including consistent mold temperature, injection pressure, and cooling time. Regular mold maintenance is also crucial to prevent wear and tear that can affect the surface finish.
Understanding SPI surface finish standards is crucial for achieving the desired aesthetics and functionality in injection molded parts.
The mold surface directly impacts the finish of the molded part.
There are twelve SPI mold finishes, categorized into four grades (A, B, C, and D), each offering a different level of gloss and texture.
SPI glossy finishes (A grades) provide a mirror-like shine, while SPI semi-glossy finishes (B grades) offer a balance of shine and practicality.
SPI matte finishes (C grades) create a non-reflective surface, and SPI textured finishes (D grades) introduce a deliberate texture.
Choosing the right surface finish depends on factors like end-use application, material choice, aesthetic requirements, functional needs, and cost.
Material selection plays a vital role in how the final surface finish turns out.
While SPI is widely used, VDI 3400 is another important standard, especially in Europe.
Ready to bring your project to life with the perfect finish? Contact us today to discuss your injection molding needs. Our team of experts at our CNC fabrication service is here to guide you through every step, ensuring your parts meet the highest standards of quality and precision. From concept to creation, we’re your partners in manufacturing excellence. If you are interested in producing a large batch of high-precision parts, the best way is to rely on professional CNC machining services.
If you’re diving into the world of product development, especially in areas like aerospace or medical devices, understanding the nuances of prototyping is essential. Explore our comprehensive guide on rapid prototyping to gain insights into how this process can accelerate your project’s success.
For those looking to produce parts that require intricate details and a superior finish, sheet metal fabrication is a versatile option. For those needing high-volume production with consistent quality, on-demand manufacturing offers a scalable solution.
Get the latest trends and facts about CNC fabrication from our blog.
Shenzhen Runkey Precision Technology Co. Ltd, a subsidiary of the Tensun Group, is your trusted one-stop solution for custom manufacturing from prototyping to production.Transforming your idea into reality with digital manufacturing resources,streamlined processes, expert guidance,accelerated timelines, and uncompromising quality.
©2024. CNC Fabrication All Rights Reserved.