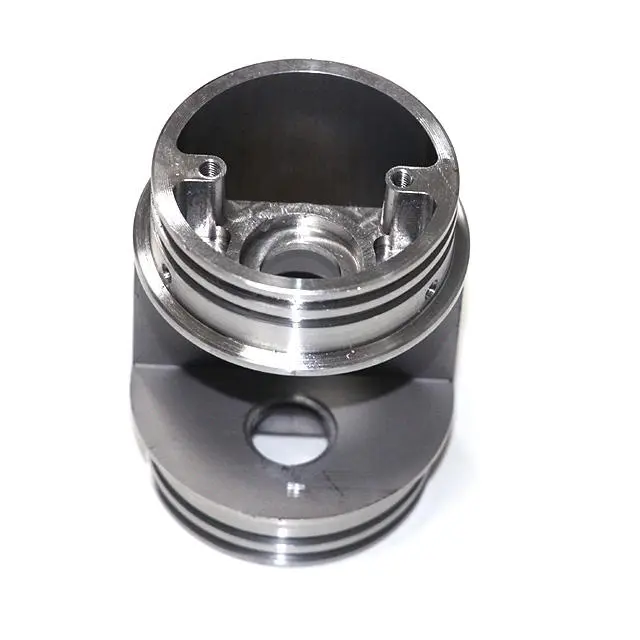
- +8615586668226
- [email protected]
- No. 30, Hongbang Industrial Park, Shenzhen
Electrical Discharge Machining, or EDM, is a non-traditional machining process that uses electrical sparks to shape a workpiece. It’s particularly effective for materials that are difficult to machine using conventional methods. EDM is a metalworking technology gaining popularity due to its ability to create complex shapes and work with extremely hard materials.
EDM is especially valuable in industries like aerospace, automotive, and medical devices. It is known for its precision and ability to work with delicate or intricate parts. As a leading CNC fabrication services provider, we leverage EDM to deliver top-quality components tailored to our client’s specific requirements. EDM is particularly useful when traditional methods fall short, as EDM does not need mechanical force for cutting.
Wire EDM and sinker EDM are two distinct types of EDM, each with unique capabilities. Wire EDM uses a thin, electrically charged wire electrode to cut through the workpiece, like a high-tech saw. Sinker EDM, also known as ram EDM, uses a custom-shaped electrode to erode the material, creating a cavity that mirrors the electrode’s shape. The main difference between EDM variations lies in their application: wire EDM for intricate cuts and sinker EDM for creating complex cavities.
The choice between wire EDM and sinker EDM depends on the project’s needs. Wire EDM is ideal for creating narrow slots and detailed contours. In contrast, sinker EDM excels in molding intricate 3D shapes, often used in mold making and die casting. Our expertise in both wire EDM and sinker EDM ensures that we can meet diverse manufacturing challenges, offering precision and quality in every project.
The two main types of EDM are wire EDM and sinker EDM. Wire EDM, using a thin wire as an electrode, is perfect for making precise cuts and is widely used in creating punches, dies, and other detailed components. Sinker EDM uses a pre-shaped electrode to form a specific cavity in the workpiece, commonly used in the production of molds and complex shapes.
These two types of EDM cater to various manufacturing needs. Wire EDM is frequently employed in the aerospace and medical industries for its precision in cutting complex shapes. Sinker EDM finds its niche in creating intricate molds for the automotive and consumer product industries. As experts in CNC fabrication services, we understand the nuances of each process, ensuring optimal results for our clients.
Wire-cut EDM stands out for its exceptional precision. This method involves using a thin heated wire, typically made of brass or coated steel, which acts as an electrode. The wire is guided along a programmed path, creating sparks between the wire and the workpiece that erode the material. This process allows for extremely precise cuts, making it ideal for intricate and complex parts.
Wire EDM is particularly advantageous when working with hard or exotic materials that are difficult to machine using traditional methods. It’s widely used in industries requiring high precision, such as aerospace, medical devices, and tool and die making. In these sectors, wire EDM ensures accuracy, reduces material waste, and enables the production of parts with tight tolerances.
The wire EDM process is a fascinating display of precision engineering. At its core, a thin wire – typically brass or coated copper – acts as an electrode. This wire is continuously fed from a spool and guided along a predetermined path by a computer-controlled system. As the wire nears the workpiece, controlled electrical discharges, or sparks, are generated. These sparks erode the material, creating a cut that mirrors the wire’s path. A dielectric fluid, usually deionized water, is used to control the sparking and flush away the eroded particles.
This process is notable for its accuracy and ability to cut intricate shapes. Since the wire is continuously fed, it remains unaffected by wear, ensuring consistent cut quality. Moreover, the wire EDM process can be used on a variety of conductive materials, regardless of their hardness. This makes it a versatile choice for numerous applications, from creating aerospace components to crafting precision medical instruments.
Sinker EDM, also referred to as conventional EDM or ram EDM, is a process where an electrode, shaped to the desired form, is submerged in a dielectric fluid along with the workpiece. Electrical discharges occur between the electrode and the workpiece, eroding the material to create a cavity that matches the electrode’s shape. This technique is particularly effective for creating complex 3D shapes and is commonly used in mold making and die production.
Sinker EDM is chosen for its ability to produce intricate internal shapes and cavities that are difficult or impossible to achieve with other methods. It’s especially useful when working with hardened materials or creating sharp internal corners. This method is widely applied in the automotive, aerospace, and consumer electronics industries, where precision molds and complex components are essential.
Feature | Wire EDM | Sinker EDM |
Electrode Type | Thin wire | Custom-shaped electrode |
Cutting Mechanism | Wire erosion | Electrode sinking |
Precision | High, for fine details | High, for complex 3D shapes |
Applications | Intricate cuts, narrow slots | Mold making, complex cavities |
Material Removal | Through wire cutting | Through electrode shape |
Shape Creation | 2D profiles, contours | 3D cavities, internal shapes |
Dielectric Fluid | Typically deionized water | Usually oil-based |
Process Speed | Generally faster | Can be slower, depends on complexity |
Material Hardness | Suitable for very hard materials | Ideal for hardened materials |
Surface Finish | Smooth, often requires less finishing | May require additional finishing |
Cost | Can be more cost-effective for some | Might be higher due to electrode prep |
Common Industries | Aerospace, Medical, Tool & Die | Automotive, Consumer Electronics, Mold |
EDM is renowned for its versatility in machining a wide range of materials. This includes not only standard metals like steel, aluminum, and copper but also exotic alloys and hardened materials. Wire EDM is particularly effective with materials like titanium, Inconel, and carbide, which are notoriously difficult to machine using conventional methods.
The ability of EDM to work with such a diverse array of materials makes it an invaluable tool in various industries. From aerospace, where lightweight yet strong materials are crucial, to the medical field, where biocompatible and precise components are needed, EDM provides a reliable solution. Our expertise in EDM allows us to handle these materials with precision, ensuring high-quality results for our clients.
Wire EDM offers several advantages in modern manufacturing. Its ability to make precise cuts with minimal material waste is a significant benefit. This precision is crucial in industries where accuracy is non-negotiable, such as in the production of aerospace components or medical devices. Additionally, wire EDM can create intricate shapes and work with a wide range of conductive materials, regardless of their hardness.
Another advantage of wire EDM is its efficiency in small-batch production. It’s a cost-effective solution for prototypes or limited-run parts, as it doesn’t require expensive tooling. At our CNC fabrication services, we utilize wire EDM to provide our clients with high-quality, precise components, tailored to their specific needs.
Here are some advantages of using wire EDM in modern manufacturing:
Precision Cutting: Wire EDM is renowned for its ability to make extremely precise cuts. This precision is vital in industries where even the slightest error can be costly.
Complex Shapes: It can create intricate and complex shapes that are often impossible with conventional machining methods.
Material Versatility: Wire EDM can cut through a wide range of conductive materials, including hardened metals and exotic alloys.
Reduced Material Waste: The thin wire used in wire EDM minimizes material removal, leading to less waste and more efficient use of resources.
No Tool Wear: Since the wire is constantly renewed, there is no tool wear, ensuring consistent quality throughout the machining process.
Cost-Effective for Small Batches: Wire EDM is particularly cost-effective for prototyping and small production runs, as it eliminates the need for expensive tooling.
Smooth Surface Finish: The cuts made by wire EDM are clean and smooth, often requiring minimal post-processing.
Stress-Free Machining: Wire EDM induces minimal stress on the workpiece, making it ideal for delicate or thin parts.
The integration of CNC (Computer Numerical Control) technology with wire EDM has revolutionized the machining process. CNC allows for precise control over the wire‘s movement, enabling the creation of complex and intricate designs with high accuracy. This automation ensures consistency and repeatability, crucial for producing high-quality parts in industries like aerospace and medical devices.
CNC wire EDM machines can operate 24/7, significantly increasing productivity. They can be programmed to perform complex cuts and shapes, making them a vital tool in modern manufacturing. Our use of advanced CNC wire EDM technology reflects our commitment to delivering precision and efficiency in every project.
Selecting the appropriate EDM services is crucial for the success of your project. It’s important to consider the specific requirements of your part, such as the material, complexity of the design, and required precision. Wire EDM is ideal for intricate cuts and working with a variety of materials, while sinker EDM is better suited for creating complex cavities.
As a leading provider of CNC fabrication services, we offer expertise in both wire EDM and sinker EDM. Our team can guide you in choosing the most suitable EDM process for your project, ensuring optimal results. We pride ourselves on our ability to understand and meet the unique needs of each client, delivering precision-engineered components across various industries. Here at CNC fabrication services, we are experts in Sheet Metal Fabrication, Laser Cutting, and Die Casting.
What is the main difference between wire EDM and sinker EDM?
The main difference lies in their application and method. Wire EDM uses a thin wire electrode for precise cutting, ideal for intricate details. Sinker EDM uses a shaped electrode to create cavities, perfect for complex 3D shapes.
Can wire EDM be used for any type of metal?
Wire EDM can be used for any conductive metal, including those resistant to conventional machining processes. This includes hardened metals and exotic alloys, making it highly versatile.
What are the benefits of using CNC technology in wire EDM?
CNC technology enhances wire EDM by providing precise control over the wire’s movement, enabling complex designs with high accuracy. It also ensures consistency, repeatability, and increased productivity.
How does the dielectric fluid work in the EDM process?
In the EDM process, the dielectric fluid acts as an insulator, controls the sparking between the electrode and workpiece, and flushes away eroded particles. It’s crucial for maintaining precision and preventing overheating.
What industries commonly use wire EDM services?
Wire EDM services are commonly used in industries requiring high precision and the ability to work with difficult materials. This includes aerospace, automotive, medical devices, tool and die making, and electronics manufacturing.
Is EDM suitable for mass production?
While EDM is excellent for precision and complex parts, it’s typically more suited for small to medium production runs due to its detailed nature. However, advancements in CNC and automation are making it more viable for larger-scale operations.
EDM, encompassing both wire EDM and sinker EDM, is a versatile and precise machining method.
Wire EDM is ideal for intricate cuts and working with a wide range of conductive materials.
Sinker EDM excels in creating complex 3D shapes and cavities, especially in mold making.
The integration of CNC technology has significantly enhanced the capabilities of wire EDM.
Choosing the right EDM process depends on the specific requirements of your project, including material, design complexity, and precision needs.
As a leading provider of CNC fabrication services, we are committed to delivering high-quality, precision-engineered components using the most suitable EDM techniques for each project.
Get the latest trends and facts about CNC fabrication from our blog.
Shenzhen Runkey Precision Technology Co. Ltd, a subsidiary of the Tensun Group, is your trusted one-stop solution for custom manufacturing from prototyping to production.Transforming your idea into reality with digital manufacturing resources,streamlined processes, expert guidance,accelerated timelines, and uncompromising quality.
©2024. CNC Fabrication All Rights Reserved.