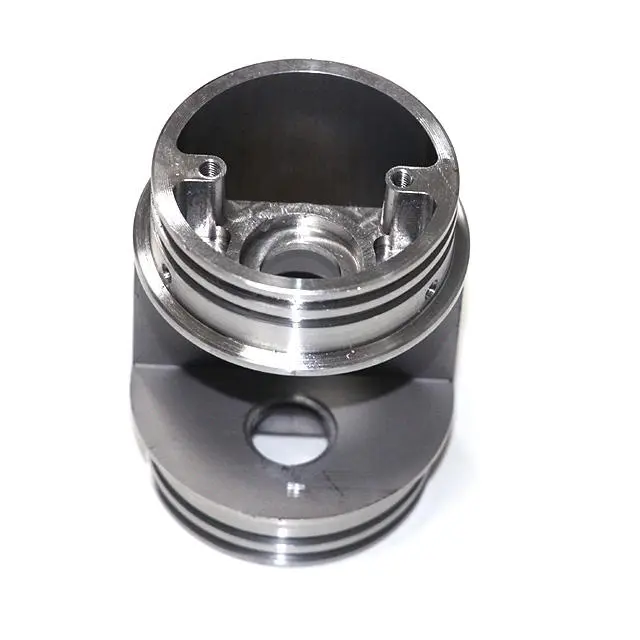
- +8615586668226
- [email protected]
- No. 30, Hongbang Industrial Park, Shenzhen
A milling operation is a machining process that uses rotary cutters to remove material from a workpiece, advancing (or feeding) in a direction at an angle with the axis of the tool. It covers a wide variety of different operations and machines, on scales from small individual parts to large, heavy-duty gang milling operations. As a cnc fabrication service provider, I’ve witnessed firsthand how crucial milling is in shaping the precision components used in industries like aerospace and automotive. The precision and versatility of milling make it indispensable in creating complex shapes and designs with high accuracy.
The importance of milling operations cannot be overstated, especially in sectors like medical devices and electronics, where precision is paramount. Milling allows for the creation of intricate parts with tight tolerances, ensuring the final product functions flawlessly. The ability to work with a variety of materials, from metals to plastics, further underscores the versatility of milling. In my experience, understanding the nuances of different milling techniques and selecting the right machine and tools can significantly impact the quality and efficiency of production.
There are numerous types of milling, each designed for specific applications and outcomes. Peripheral milling, for example, involves using the periphery of the milling cutter to make cuts. This technique is ideal for creating slots or grooves. On the other hand, face milling utilizes both the periphery and the face of the cutter, making it suitable for finishing flat surfaces. Understanding these distinctions is vital for optimizing the milling process and achieving desired results.
Beyond these, there are specialized types of milling such as form milling, which uses a form milling cutter to produce specific contours, and thread milling, which is used to create threads. Each type of milling requires specific tools and techniques. For instance, thread milling is particularly beneficial for creating internal and external threads with precision, a common requirement in industrial equipment manufacturing. As a professional in the field, I emphasize the importance of selecting the right milling technique to ensure both quality and efficiency. Learn more about our machining services to understand how we optimize these processes for our clients.
Mill machines are the workhorses of modern manufacturing, capable of performing a wide range of milling operations. These machines can be broadly categorized into vertical mills and horizontal mills, each offering unique advantages. Vertical mills are particularly versatile, suitable for a variety of tasks from drilling to complex contouring. Horizontal milling machines, on the other hand, excel in heavy-duty cutting and are often used for making slots and grooves.
In modern manufacturing, mill machines are often integrated into a larger production line, working in concert with other machines and systems. This integration allows for a seamless flow of materials and information, optimizing the manufacturing process. Our facility utilizes state-of-the-art mill machines equipped with advanced control systems, enabling us to meet the stringent demands of industries such as robotics and consumer products. The precision and reliability of these machines are crucial in ensuring the quality and consistency of the parts we produce.
A face mill is a milling cutter designed to cut primarily with the end face of the cutter. It’s used for creating flat surfaces on the workpiece and is particularly effective for face milling operations. Face mills are known for their ability to produce smooth finishes and are commonly used in industries requiring high precision, such as aerospace and medical devices. The design of a face mill, with multiple cutting edges, allows for efficient material removal and superior surface finish.
In my experience, face mills are indispensable when it comes to achieving a high-quality finish on large surfaces. They are particularly useful in preparing materials for further processing or assembly. For example, in the automotive industry, face mills are used to ensure that engine components have perfectly flat surfaces, which is crucial for optimal performance. Our use of advanced face mills in our cnc fabrication service ensures that we deliver components that meet the exacting standards of our clients.
CNC milling machines represent a significant advancement in milling technology. These machines use computer numerical control (CNC) to automate the milling process, allowing for precise and repeatable operations. CNC milling machines can perform a wide range of tasks, from simple drilling to complex 3D contouring, making them incredibly versatile. The automation capabilities of CNC machines reduce the need for manual intervention, leading to increased efficiency and reduced error rates.
The introduction of CNC milling machines has had a profound impact on various industries. For instance, in the aerospace sector, CNC milling is used to create intricate components with extremely tight tolerances. The ability of CNC machines to work with a wide range of materials, including metals, plastics, and composites, makes them invaluable in modern manufacturing. At our facility, we leverage the capabilities of CNC milling machines to produce high-quality parts for a variety of applications, ensuring precision and consistency in every project.
The choice between a vertical mill and a horizontal mill depends on the specific requirements of the milling operation. Vertical mills have a vertically oriented spindle, making them ideal for tasks that involve drilling, plunging, and working on the top surface of a workpiece. They are particularly well-suited for creating complex shapes and contours. Horizontal milling machines, with their horizontally oriented spindle, are better suited for heavy-duty cutting and operations that require the removal of large amounts of material, for example, our 5 axis CNC machining.
Vertical mills are often preferred for their versatility and ease of use, especially in smaller-scale operations or when working with intricate parts. They are commonly used in tool and die making, as well as in the production of custom parts. Horizontal mills, on the other hand, are the machines of choice for large-scale production and heavy-duty applications. Their robust construction and ability to handle large workpieces make them ideal for industries such as heavy equipment and construction.
CNC milling offers numerous advantages over traditional manual milling methods. One of the most significant benefits is the precision and repeatability that CNC machines provide. These machines can perform complex operations with a high degree of accuracy, ensuring that each part produced meets the specified tolerances. This level of precision is crucial in industries such as aerospace and medical devices, where even the slightest deviation can have significant consequences.
Another key advantage of CNC milling is its efficiency. CNC machines can operate continuously with minimal downtime, significantly increasing production rates. The automation capabilities of CNC machines also reduce labor costs and minimize the risk of human error. Additionally, CNC milling allows for greater flexibility in design and manufacturing. With CNC machines, it’s possible to quickly and easily modify designs and produce custom parts, making it an ideal solution for prototyping and small-batch production.
Peripheral milling is a milling technique that utilizes the periphery of the milling cutter to make cuts. This method is particularly effective for creating slots, grooves, and other features along the edge of a workpiece. Vertical milling machines are often used for peripheral milling due to their ability to position the cutter accurately and maintain a consistent depth of cut.
Vertical milling machines offer several advantages for peripheral milling. Their vertically oriented spindle allows for precise control over the milling cutter, enabling the creation of intricate features with high accuracy. Additionally, vertical milling machines are typically equipped with advanced control systems that allow for complex tool paths and automated operations. This makes them ideal for industries that require precision and repeatability, such as electronics and telecommunications.
There are many different types of milling operations, each designed for specific applications and outcomes. Some common types of milling include face milling, peripheral milling, slot milling, and chamfer milling. Face milling, as previously discussed, is used for creating flat surfaces, while peripheral milling is ideal for cutting slots and grooves.
Slot milling involves using an end mill or slotting cutter to create narrow slots or channels in the workpiece. This technique is commonly used in the manufacturing of keyways and other features that require precise alignment. Chamfer milling is used to create beveled edges or chamfers, which can improve the appearance and functionality of a part. Understanding the various types of milling operations is essential for selecting the right tools and techniques for a given task.
CNC milling is a versatile and powerful manufacturing process that is well-suited for a wide range of industries. Its precision, efficiency, and flexibility make it an ideal choice for sectors such as aerospace, automotive, medical devices, and electronics. In the aerospace industry, CNC milling is used to create complex components with extremely tight tolerances, ensuring the safety and reliability of aircraft.
In the automotive sector, CNC milling is used to produce engine components, transmission parts, and other critical components that require high precision and durability. The ability of CNC machines to work with a variety of materials, including metals and plastics, makes them invaluable in this industry. Similarly, in the medical devices field, CNC milling is used to create intricate and precise parts for medical instruments and implants, where accuracy and reliability are paramount.
What is a milling operation?
A milling operation is a machining process that uses rotary cutters to remove material from a workpiece. It’s a versatile process used across various industries to create complex shapes and designs.
What are the main types of milling?
The main types of milling include face milling, peripheral milling, slot milling, and thread milling. Each type is designed for specific applications and uses different tools and techniques.
How do CNC milling machines differ from manual milling machines?
CNC milling machines use computer numerical control to automate the milling process, offering greater precision, repeatability, and efficiency compared to manual milling machines.
What is a face mill used for?
A face mill is used for creating flat surfaces on a workpiece. It’s particularly effective for achieving smooth finishes and is commonly used in industries requiring high precision.
Why is CNC milling ideal for industries like aerospace and medical devices?
CNC milling offers the precision, repeatability, and flexibility needed to produce complex components with tight tolerances, making it ideal for industries like aerospace and medical devices where accuracy is critical.
What are the advantages of using a vertical mill versus a horizontal mill?
Vertical mills are versatile and well-suited for tasks involving drilling and contouring on the top surface of a workpiece. Horizontal mills are better for heavy-duty cutting and operations requiring the removal of large amounts of material.
Milling operations are essential in modern manufacturing, providing precision and versatility.
Face mills are crucial for achieving high-quality finishes on flat surfaces.
CNC milling machines revolutionize the milling process with automation, precision, and efficiency.
Understanding the differences between vertical mills and horizontal mills helps in selecting the right machine for specific tasks.
CNC milling offers numerous advantages, including precision, repeatability, efficiency, and flexibility.
Different types of milling operations, such as face milling, peripheral milling, slot milling, and chamfer milling, cater to various manufacturing needs.
CNC milling is ideal for diverse industries, including aerospace, automotive, medical devices, and electronics, due to its precision and versatility.
As a provider of cnc fabrication services, we are committed to delivering high-quality parts that meet the exacting standards of our clients. Whether you’re in the aerospace, automotive, or medical devices industry, our expertise in CNC solutions and advanced milling techniques ensure that we can meet your specific needs. Contact us today to learn more about how our fabrication services can support your manufacturing goals. Our team is ready to assist you with projects ranging from rapid prototyping to full-scale production, ensuring precision and quality at every step.
Get the latest trends and facts about CNC fabrication from our blog.
Shenzhen Runkey Precision Technology Co. Ltd, a subsidiary of the Tensun Group, is your trusted one-stop solution for custom manufacturing from prototyping to production.Transforming your idea into reality with digital manufacturing resources,streamlined processes, expert guidance,accelerated timelines, and uncompromising quality.
©2024. CNC Fabrication All Rights Reserved.