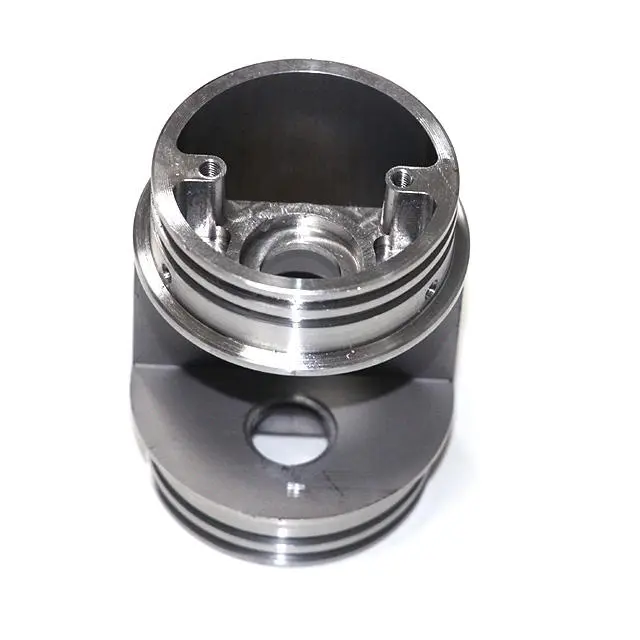
- +8615586668226
- [email protected]
- No. 30, Hongbang Industrial Park, Shenzhen
When it comes to CNC machining, several key factors significantly impact the cost of your project. As a representative of CNC fabrication services, I’ve seen how these elements can affect the final price. Understanding these can help you make informed decisions to optimize your budget.
Material Selection: The type of metal or other material you choose is a significant cost factor. Some materials are inherently more expensive to machine than others due to their hardness or abrasiveness. For example, titanium is generally more costly to process than aluminum. At our facility, we always advise clients on the most cost-effective materials that meet their project requirements. We have to remember, material cost, especially when it comes to metal parts, affects overall cost.
Machine Time: This is perhaps the most crucial element. Machine time directly correlates with the complexity of the CNC machined part and the number of operations required. Longer machine time means higher costs. For instance, parts with deep pockets or intricate designs will naturally take longer to produce. Time is money, and it also applies to cnc machining time.
Choosing the right material is crucial in managing CNC machining cost. Different materials have varying properties that affect their machinability. As someone deeply involved in CNC fabrication services, I always emphasize this point to our clients.
Hardness and Abrasiveness: Harder materials like stainless steel or titanium require more robust CNC tools and slower cutting speeds, leading to increased machine time and higher costs. For instance, when working with hardened steel, the wear and tear on tools are significantly higher compared to softer materials like aluminum. In the case of hard materials, using an end mill is difficult to machine.
Material Cost: The raw material cost itself plays a vital role. Exotic alloys or specialized plastics are generally more expensive than common metals like aluminum or brass. Our team often presents clients with a cost-benefit analysis to determine if the advantages of a pricier material justify the added expense. The price of the machine that is used to cut materials also needs to be accounted for.
Machine time is a fundamental aspect of CNC machining cost reduction. The longer a CNC machine is running to produce a part, the higher the operational costs. As a professional in the field, I always highlight this during project consultations.
Complexity of Operations: Each cut, drill, or milling operation adds to the total machine time. For example, a simple bracket might take minutes, while a complex component with multiple features could take hours. Our engineers work diligently to optimize tool paths and minimize unnecessary movements.
Tool Changes: Frequent tool changes can add to the machine time. If a part requires multiple tools, each changeover adds non-productive time. We strive to design processes that minimize these changes, often using multi-axis CNC system for efficiency. Using the proper milling machine for the job can help reduce the cost.
Tight tolerance and specific surface finish requirements can significantly increase costs in CNC machining. Achieving precision comes at a price, and as a CNC fabrication expert, I often guide clients through these considerations.
Tolerance Impact: Tight tolerance demand more precise machining, often requiring slower speeds and finer cuts, thus increasing machine time. For instance, achieving a tolerance of ±0.001 inches takes considerably longer than ±0.01 inches. We always discuss the necessity of extremely tight tolerances, as they can significantly increase the cost. In some cases, a slightly looser tolerance can achieve the same functional outcome at a lower cost. Tight tolerance comes at a cost!
Surface Finish: High-quality surface finishes, such as those required for aesthetic or functional reasons, often necessitate additional processes like polishing or grinding. These extra steps add to the overall machining time and, consequently, the cost. For example, achieving a mirror-like finish on a sheet metal fabrication component may involve multiple passes with increasingly fine abrasives, extending the machining process.
The complexity of a part’s geometry is a significant factor in determining CNC machining costs. Intricate designs often require more sophisticated machining strategies, which can escalate expenses.
Undercuts and Internal Features: Parts with undercuts or internal features that are not easily accessible often require specialized tooling or multiple setups. For example, a part with deep internal pockets might need a longer, more slender end mill, which can be more prone to deflection and breakage, slowing down the process.
Thin Walls: Machining thin walls presents unique challenges. Thin walls can be prone to vibration and deformation during machining, requiring slower feed rates and potentially additional support structures. This not only increases machine time but can also raise the risk of part rejection due to dimensional inaccuracies. Cnc tools that are used need to be suitable for thin walls.
Setup and tooling are often overlooked but critical components of the cost of CNC machining. Efficient setup and appropriate tooling can significantly impact the final cost of CNC parts.
Setup Time: Each time a CNC machine is set up for a new part or operation, it adds non-productive time to the process. Reducing the number of setups can significantly reduce costs. For instance, designing a part that can be machined in a single setup instead of multiple ones can lead to substantial time and cost savings.
Tooling Costs: The type of tools required for a specific job can affect the cost per unit. Standard tools are generally less expensive than custom or specialized tools. At our facility, we maintain a wide range of standard tools and advise clients on designs that utilize them to minimize expenses.
Design for Manufacturability (DFM) is a crucial aspect of cost-effective CNC machining. By considering manufacturing limitations and capabilities during the design phase, we can often reduce costs and production time. DFM principles can reduce cnc machining expenses significantly.
Standardization: Using standard hole sizes, thread types, and feature dimensions can reduce the cost by minimizing the need for special tools. For example, designing a part with common metric thread sizes instead of unique ones allows for the use of readily available, less expensive tooling.
Simplification: Simplifying part geometry can lead to significant cost savings. Removing unnecessary features or modifying complex shapes can reduce machine time and complexity. Our engineers often collaborate with clients to identify areas where simplification can be applied without compromising functionality.
CNC milling and CNC turning are two primary methods in CNC machining, each with its own cost implications. Understanding these differences can help in choosing the most economical process for specific CNC parts.
CNC Milling: This process is ideal for creating complex shapes and features on flat or block-like parts. However, CNC milling machines can be more expensive to operate for simpler, cylindrical parts compared to turning. For instance, creating a square housing with multiple holes and pockets is efficiently done with milling.
CNC Turning: CNC turning is best suited for cylindrical parts or components with rotational symmetry. Turning operations are generally faster and more cost-effective for these types of parts. For example, producing a shaft or a round spacer is typically cheaper and quicker on a lathe. We have both cnc milling machines and lathes available to clients.
The number of setups required to machine a part is a critical factor influencing the price of CNC machining. Each setup adds time and cost to the process, impacting the final cost of CNC machined parts.
Multiple Setups: Each time a part needs to be repositioned or refixtured, it introduces additional setup time. This non-cutting time can significantly increase the overall cost, especially for complex parts. For example, a part that requires machining on all six sides in separate setups will be considerably more expensive than one that can be completed in a single setup.
Reducing Setups: One of our primary strategies is to minimize the number of setups. By employing advanced techniques like 5-axis machining or designing parts that can be held in a single fixture, we can dramatically reduce the cost per part. We strive to reduce the number of machine setups for our clients.
Beyond the fundamental principles, there are several innovative approaches we employ at our CNC fabrication services to further reduce CNC machining cost.
Process Optimization: Continuously refining our machining processes allows us to identify and eliminate inefficiencies. For example, we’ve implemented advanced CAM software that optimizes tool paths, reducing air cutting time and maximizing material removal rates. Modern CNC machines help reduce time!
Near Net Shape Manufacturing: Whenever possible, we start with materials that are close to the final part’s shape, such as castings or forgings. This reduces the amount of material that needs to be removed, significantly decreasing machine time. For example, using a near-net-shape casting for a complex bracket can cut machining time by 50% or more compared to starting from a solid block.
What is the single most effective way to reduce CNC machining costs?
Optimizing part design for manufacturability is often the most effective strategy. Simplifying geometry, using standard features, and minimizing the number of setups can lead to substantial cost reductions.
How can I determine the most cost-effective material for my CNC machining project?
Consider the material’s machinability, availability, and cost. Softer, more common materials like aluminum are generally cheaper to machine than harder, exotic alloys. Consulting with a CNC machining expert can help you make an informed decision based on your specific requirements. You should always consider the material cost!
Does the quantity of parts ordered affect the CNC machining cost per unit?
Yes, larger quantities typically result in lower cost per unit. This is due to the amortization of setup costs over more parts and potential efficiencies gained from longer production runs.
How can I learn more about designing parts for cost-effective CNC machining?
Engaging with experienced CNC machining services like ours can provide valuable insights. We offer design consultations and can guide you through the process of optimizing your designs for manufacturability and cost efficiency. Consider our CNC solutions to learn more. We can help reduce the costs!
Are there any software tools that can help estimate CNC machining costs?
Yes, several CAD/CAM software packages offer cost estimation features. These tools can provide rough estimates based on material, part geometry, and basic machining parameters. However, for accurate quotes, it’s always best to consult with a professional CNC machining provider. Software can calculate the cost of cnc parts easily.
Can using 5-axis machining reduce costs compared to traditional 3-axis machining?
While 5-axis machines have a higher initial investment, they can reduce overall costs for complex parts by enabling the completion of multiple operations in a single setup. This reduces handling, setup time, and the potential for errors. Check out our page about 5-axis CNC machining to see if it’s a good choice for you.
Material choice significantly impacts cost: Opt for materials that balance performance requirements with machinability.
Machine time is a major cost driver: Design parts that can be produced quickly and efficiently.
Tolerances and surface finish requirements affect expenses: Specify only what’s necessary for functionality and aesthetics.
Complex geometry increases costs: Simplify designs where possible to reduce machining complexity.
Setup and tooling choices matter: Minimize setups and use standard tooling whenever feasible.
Design for Manufacturability (DFM) principles are crucial: Incorporate DFM from the outset to optimize for cost-effective production.
Milling and turning have different cost profiles: Choose the process best suited to your part’s geometry.
Innovative strategies can further reduce expenses: Explore process optimization and near-net-shape manufacturing.
Quantity affects per-unit cost: Larger orders generally lead to lower costs per part.
Consulting with experts is invaluable: Engage with experienced CNC machining services for design and cost optimization.
By implementing these strategies, you can make informed decisions that lead to more affordable, high-quality CNC machined parts. Remember, every project is unique, and finding the right balance between design, material, and process is key to achieving your goals within budget. As a dedicated partner in CNC fabrication services, we’re committed to helping you navigate these complexities and achieve success in your manufacturing endeavors. If you are curious about other machining services we offer, feel free to check out our website. If you need help with metal bending, we can help you. We are ready to help you with your CNC machining projects. We can also assist you with assembly if needed. We can help you reduce costs without sacrificing quality.
Get the latest trends and facts about CNC fabrication from our blog.
Shenzhen Runkey Precision Technology Co. Ltd, a subsidiary of the Tensun Group, is your trusted one-stop solution for custom manufacturing from prototyping to production.Transforming your idea into reality with digital manufacturing resources,streamlined processes, expert guidance,accelerated timelines, and uncompromising quality.
©2024. CNC Fabrication All Rights Reserved.