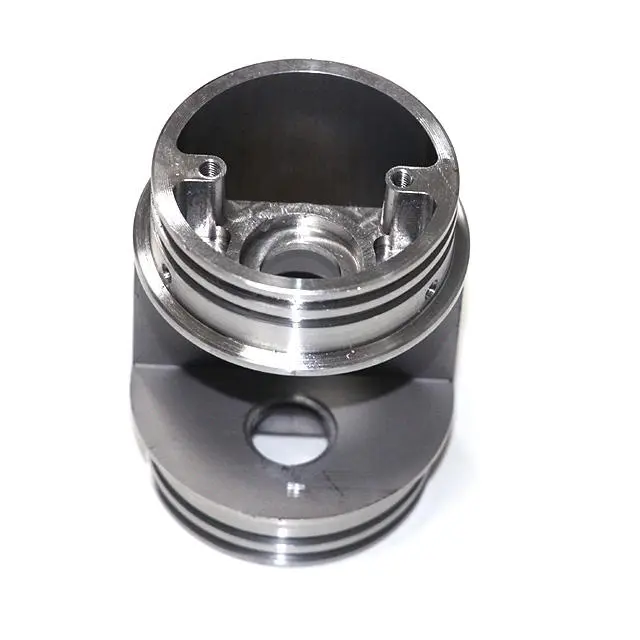
- +8615586668226
- [email protected]
- No. 30, Hongbang Industrial Park, Shenzhen
At their core, gears are toothed wheels designed to transmit motion and power between rotating shafts. The type of gear is determined by the orientation of their teeth and shafts and affects their speed, torque, and the direction of motion. They allow mechanical devices to function efficiently, and the selection of the appropriate gear is critical for the performance and durability of any mechanical system. Without gears, many of the machines we rely on every day would be impossible. The precise engineering and manufacturing of gears is essential to ensure proper functioning of mechanical systems, from simple clocks to complex robotic arms. The ability to modify speed and torque with gears enables optimized performance for specific tasks. For instance, a high-speed motor can be geared down to provide the necessary power at a lower speed for heavy lifting operations. We at CNC understand that each type of gear plays an important role in the engineering world.
Gears are essential in mechanical systems because they:
Spur gears are one of the most common and simplest types of gear. They feature straight teeth that are parallel to the axis of rotation. This simplicity makes them relatively inexpensive to manufacture and easy to use. Spur gears are typically used in applications where shafts are parallel and the need for smooth, quiet operation is not paramount. While the simple design of spur gears makes them reliable, it also means they are more likely to produce noise and vibrations, especially at higher speeds, when compared to a helical gear. A great example of this can be seen in older mechanical clocks where the sound of gears clicking is a common attribute. In simple, low-speed applications like gearboxes for toys, spur gears are ideal.
Spur gears are the simplest and most economical option of the various types of gears, and are widely used in:
Unlike spur gears, helical gears have teeth that are cut at an angle to the axis of rotation. This helical angle offers several advantages over spur gears. Because their teeth engage gradually rather than all at once, they operate more smoothly and quietly. This angled tooth design also allows for the transmission of higher loads than spur gears and the gear is also well suited for high-speed applications. However, helical gears produce an axial thrust load which needs to be accounted for in the system design. Helical gears are often used in automotive transmissions due to their high performance and quiet operation. A type of helical gear, the double helical gear, can mitigate the issues associated with axial thrust, with both a right and left-hand helix, which cancel each other out. The operation of helical gears are commonly used due to their quiet operation.
Helical gears are preferred in:
Bevel gears are designed to transmit motion between two intersecting shafts, typically at a 90-degree angle, but not always. They have teeth that are tapered, resembling a cone, and are essential for applications where the direction of motion needs to change. These are often used in differentials in vehicles. There are two main types: straight bevel gears and spiral bevel gear. Straight bevel gears are similar to spur gears in that their teeth are straight, while spiral bevel gears have curved teeth, similar to helical gear. This spiral design provides smoother, quieter operation. A variation of this is a miter gear, which is a bevel gear with equal numbers of teeth. Miter gear is used to transmit motion between shafts at a 90-degree angle. Bevel gears and hypoid gears are used in automotive differentials to transmit torque to the wheels.
Here are some applications of bevel gears:
A worm gear consists of a screw-like gear (the worm) that meshes with a specialized gear called a worm wheel. Worm gears are used to transmit power between non-intersecting shafts at a 90-degree angle. This type of gear is typically used for very high gear ratio reductions in speed. Worm gears are also non-reversible, which means the gear can not be driven by the wheel which makes them excellent in safety mechanisms like winches and hoists, as the load is secure due to the nature of gear ratio. The most significant advantage of a worm gear is its capacity for high reduction ratios in a compact space. One turn of the worm produces only small rotation in the worm wheel which allows for a large speed reduction. Worm gears offer a reliable and powerful means for transmitting torque at different speeds, making them suited for applications that benefit from a large reduction in speed for high torque operation.
Worm gears are commonly used in:
An internal gear is a gear with teeth on the inside of a cylinder or a ring. These gears have very specific applications and aren’t seen as often as external gear. They are designed to mesh with external gears or spur gears, and because of this they are often used in space-saving applications due to its size. Internal gear is commonly seen in planetary gear systems, which are often used in automatic transmissions and are capable of large gear ratio change in a small space. The most common application for internal gears mesh with external is in transmissions for vehicles.
Internal gears are preferred in:
A gear train is a combination of two or more gears that work together to transmit power and motion. By using various sizes of gears, it’s possible to achieve a wide range of speeds and torques. The gear ratio of a gear train is determined by the number of teeth on the driven gear divided by the number of teeth on the driving gear. This makes it possible to create a system with high torque at a lower speed or high speed and lower torque, based on the gear design. By changing the gear set in the gear train, an engineer can fine-tune how the mechanical force is transferred from one point to another, ensuring efficient and precise mechanical control.
Here are key uses of gear train:
A rack and pinion gear system converts rotational motion into linear motion, or vice versa. The gear rack is a straight bar with teeth, and the pinion is a standard circular gear that meshes with the gear rack. This system is used in car steering systems to convert the rotation of the steering wheel to the back and forth motion of the car’s wheels. The rack and pinion gear system provides a simple and effective mechanism for converting between rotary and linear movement, and is used in a vast variety of industries, making it an extremely versatile mechanical design.
Rack and pinion gear systems are useful in:
The reason there are so many different types of gear is because each type of gear has its own unique set of characteristics that make it suitable for specific applications. The needs of different applications range from the speed and direction of motion to how much torque is needed. For example, a simple clock might utilize spur gears, whereas a car’s transmission uses helical gear, and a winch may use a worm gear. To optimize the performance, longevity, and safety of mechanical systems, the correct gear type must be selected. That’s why at CNC Fabrication Manufacturing plants for products we know how important it is to work with our clients to ensure we meet their needs.
Some reasons for the variety of gear types include:
Plastic gears are used in a number of applications due to being lightweight, low cost, and requiring no lubrication. They are ideal for applications that do not require high levels of torque, and can be molded into shapes that are not easily achievable using metal. The use of plastic gears has become more prominent in recent years in applications ranging from toys to electronics, and they are often used in consumer electronics. They offer a cost-effective alternative to metal gears and are commonly found in gear trains.
Plastic gears find their place in:
Gears are used across almost all industries, from tiny watch gears to large industrial machinery gears. In the automotive industry, gears are used in transmissions, differentials, and steering systems. The aerospace sector relies on highly precise gears in aircraft engines and control mechanisms. In manufacturing, gears are used in machine tools, conveyor systems, and robotics. The medical field uses gears in surgical tools and medical equipment. Gears are commonly used in power generation, construction equipment and in robotics, where complex gear systems enable precise and coordinated movements. The applications for gears are diverse, but the goals are always the same: efficiency and reliability. Gears play a crucial role in virtually every industrial sector. The vast array of machinery in use depends on gears work to transmit power.
Here are some industries that depend on gears:
Gears work by meshing together and transferring rotational motion from one gear to another. When two gears mesh, the teeth of one gear push against the teeth of another gear, causing it to rotate. The gear ratio, determined by the number of teeth on each gear, dictates the change in speed and torque between the two gears. Gears transmit power efficiently, and are commonly seen in gear drive systems.
The precise tooth design of each gear helps to achieve smooth and efficient transfer of motion. A key element to how gears work is the interlocked teeth, which ensures the power is efficiently transferred, and allows for the control of speed and torque. The use of multiple gears creates what is called a gear train, which allows more complex power transmission systems.
How does gear size affect gear ratio?
The size of a gear directly impacts its gear ratio. Larger gears have more teeth, and when paired with smaller gears, provide a high gear reduction and increase torque output.
What is the difference between a spur gear and a helical gear?
Spur gears have straight teeth parallel to the axis, while helical gears have angled teeth, making them smoother and quieter.
What makes a worm gear non-reversible?
The unique design of a worm gear, where the worm drives the wheel, prevents the wheel from turning the worm, making it non-reversible.
What is the role of gears in a car’s transmission?
Gears in a car’s transmission are used to adjust the speed and torque delivered from the engine to the wheels, allowing the car to perform optimally in different conditions.
Can gears be manufactured using different materials?
Yes, gears can be manufactured using various materials including metals like steel, brass, and aluminum, as well as plastics, depending on application requirements.
Why are some gears made from plastic?
Plastic gears are lightweight, cost-effective, and can be used in applications where high torque isn’t required, and often require no lubrication.
In conclusion, the world of gears is diverse and complex, with each type of gear having its own set of properties and applications. From simple spur gears to complex worm gears and planetary gear systems, these mechanical components play a crucial role in power transmission across industries. Understanding how gears work and their unique attributes helps engineers and designers to choose the right gear type for each specific application. As a gear manufacturer we have a deep understanding of how each type of gear works, ensuring that we can deliver high-quality products for a range of industrial uses.
Key points to remember about gears:
If you’re in need of high-quality, precision-engineered gears, we invite you to contact us at CNC Fabrication Manufacturing plants for products. We’re ready to help you find the perfect gear solutions for your next project. Be sure to visit our page on CNC Machining, as well as Surface Finishing, Precision Machining, and Rapid Prototyping to see what we can do for you. Consider also our Fabrication Services to understand all of our capabilities. If you are in the Aerospace field we are happy to help you with all your manufacturing needs.
Get the latest trends and facts about CNC fabrication from our blog.
Shenzhen Runkey Precision Technology Co. Ltd, a subsidiary of the Tensun Group, is your trusted one-stop solution for custom manufacturing from prototyping to production.Transforming your idea into reality with digital manufacturing resources,streamlined processes, expert guidance,accelerated timelines, and uncompromising quality.
©2024. CNC Fabrication All Rights Reserved.