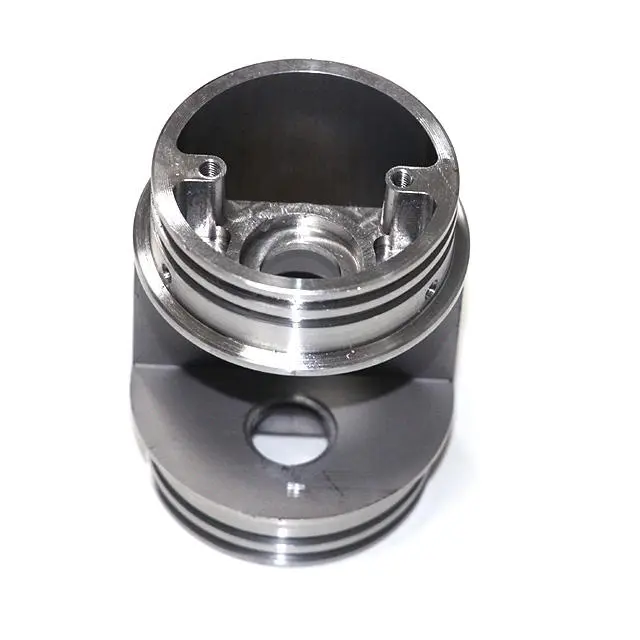
- +8615586668226
- [email protected]
- No. 30, Hongbang Industrial Park, Shenzhen
What is Machining?
Machining is a subtractive manufacturing process where material is removed from a workpiece using cutting tools to create a desired shape. This process utilizes machine tools like lathes, milling machines, and drills to achieve precise dimensions and surface finishes. The removed material, often in the form of chips, is a byproduct of the machining operation. Machining plays a vital role across diverse industries, including Aerospace, Automotive, and Medical Devices.
Why is Understanding Machining Important?
A strong grasp of machining processes is crucial for effective product design, material selection, and manufacturing process optimization. Choosing the right machining technique can significantly impact production costs, lead times, and final product quality. From CNC Machining to traditional methods, each type of machining offers unique capabilities and advantages.
What are the Different Types of Machining?
Machining processes can be broadly categorized into conventional and non-conventional methods. Conventional machining relies on direct contact between a cutting tool and the workpiece, whereas non-conventional machining employs energy sources like lasers, electrical discharges, or chemicals for material removal.
1. What is CNC Machining?
CNC (Computer Numerical Control) machining is a highly automated process that uses pre-programmed computer code to control the movement of machine tools. CNC machining allows for high precision, repeatability, and complex geometries. CNC Solutions offer a wide range of capabilities, from milling and turning to multi-axis machining.
2. What is Milling?
Milling is a machining process that uses a rotating cutting tool with multiple cutting edges to remove material from a workpiece. It is often used to create flat surfaces, slots, and complex shapes. Milling machines come in various types, including horizontal and vertical milling machines. From roughing operations to finishing, milling plays a crucial role in achieving precise dimensions and smooth surface finishes.
3. What is Turning?
Turning is a machining operation performed on a lathe, where the workpiece rotates while a single-point cutting tool removes material. This process is commonly used to create cylindrical shapes, such as shafts, pins, and screws. CNC Turning offers high precision and efficiency for turning operations.
4. How Does Drilling Work?
Drilling is a machining process that creates holes in a workpiece using a rotating cutting tool called a drill bit. Drilling operations are crucial for creating holes for fasteners, passages for fluids, and other features. The diameter and depth of the hole can be precisely controlled using different drill bits and machining parameters.
5. What are the Benefits of Grinding?
Grinding is a finishing operation that uses an abrasive wheel to remove small amounts of material from a workpiece. Grinding achieves high precision and surface finish, often used for final dimensional adjustments and surface smoothing. It’s a vital process in achieving tight tolerances and polished surfaces.
6. Exploring Non-Conventional Machining
Non-conventional machining methods offer unique advantages for materials that are difficult to machine using traditional methods. These techniques include Electrical Discharge Machining (EDM), Chemical Machining, Laser Beam Machining (LBM), Abrasive Jet Machining (AJM), Water Jet Machining (WJM), Ultrasonic Machining (USM), Plasma Arc Machining (PAM), Electrochemical Machining (ECM), and Ion Beam Machining (IBM). Each of these techniques offers unique capabilities, from intricate shapes with EDM to precise material removal with laser beam machining.
7. Chemical Machining: A Detailed Look
Chemical machining uses chemical etchants to selectively remove material from a workpiece. This process is often used to create complex shapes in thin materials, such as sheet metal. It’s a valuable technique for creating intricate parts and patterns.
8. Understanding the Role of Cutting Tools
Cutting tools play a vital role in machining processes. Selecting the right cutting tool material, geometry, and coating is crucial for achieving optimal machining performance, surface finish, and tool life. From carbide inserts to high-speed steel tools, understanding cutting tool characteristics is essential for any machinist.
9. Machining in Metal Fabrication
Metal fabrication encompasses a range of processes, including cutting, bending, and assembling metal parts. Machining plays a key role in creating precise components for metal fabrication projects. Choosing the right machining process can significantly impact the efficiency and quality of the final fabricated product.
10. Conventional vs. Non-Conventional Machining: Which is Right for You?
Choosing between conventional and non-conventional machining depends on several factors, including the material being machined, the desired tolerances, the complexity of the part, and production volume. Understanding the advantages and limitations of each approach is crucial for making informed decisions.
What is the difference between milling and turning? Milling uses a rotating cutting tool with multiple cutting edges, while turning involves rotating the workpiece against a single-point cutting tool.
What are the advantages of CNC machining? CNC machining offers high precision, repeatability, and the ability to create complex geometries.
What materials can be machined? A wide range of materials can be machined, including metals, plastics, and composites.
What are the key factors to consider when selecting a machining process? Factors to consider include material properties, desired tolerances, part complexity, and production volume.
What are some common machining challenges? Common challenges include tool wear, vibration, and achieving tight tolerances.
How can I improve the efficiency of my machining process? Optimizing cutting parameters, selecting the right cutting tools, and implementing automation can improve machining efficiency.
Machining is a subtractive manufacturing process that removes material to create desired shapes.
Different types of machining processes exist, each with its own advantages and applications.
CNC machining offers high precision and automation.
Selecting the right cutting tools is crucial for optimal machining performance.
Understanding the different types of machining can help optimize design and manufacturing processes.
This detailed guide to machining provides a foundation for understanding this essential manufacturing process. Whether you are a seasoned engineer or just starting to explore the world of manufacturing, we hope this article has provided valuable insights. Contact us today to learn how our Machining Services can help bring your next project to life.
Get the latest trends and facts about CNC fabrication from our blog.
Shenzhen Runkey Precision Technology Co. Ltd, a subsidiary of the Tensun Group, is your trusted one-stop solution for custom manufacturing from prototyping to production.Transforming your idea into reality with digital manufacturing resources,streamlined processes, expert guidance,accelerated timelines, and uncompromising quality.
©2024. CNC Fabrication All Rights Reserved.