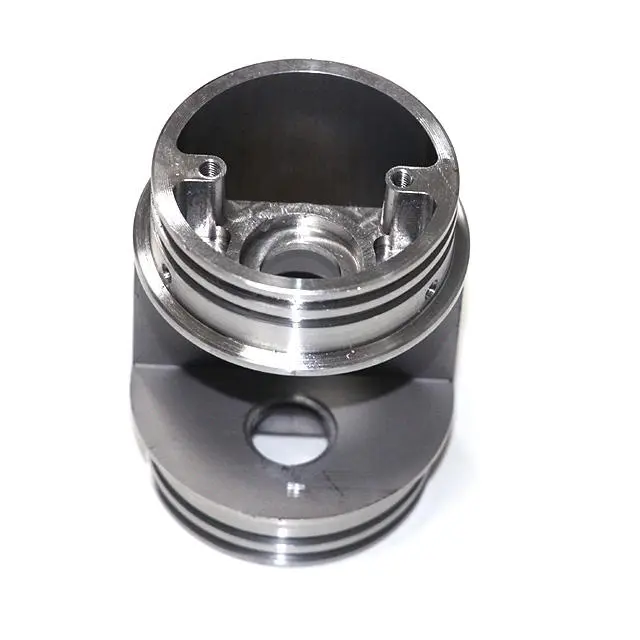
- +8615586668226
- [email protected]
- No. 30, Hongbang Industrial Park, Shenzhen
Stainless steel is a tough material due to its unique alloy composition, specifically its chromium content, which forms a passive layer that resists corrosion. However, this same property makes it incredibly hard and abrasive. When you drill stainless steel, you’re not just cutting metal; you’re battling against this tough, protective layer.
Here’s why drilling stainless steel poses a challenge:
Choosing the right drill bit is crucial when working with stainless steel. Not all drill bits are created equal, and using the wrong type can lead to frustration, damaged materials, and wasted time. As a CNC fabrication service provider, we frequently work with clients in demanding industries like aerospace, automotive, and medical devices, where precision is non-negotiable. Based on my experience, the best drill bits for stainless steel are those made from high-quality materials like cobalt or carbide.
Here’s a breakdown:
The construction of a drill bit significantly impacts its ability to drill through stainless steel effectively. It’s not just about the material; the design and manufacturing process also play a crucial role. At my CNC fabrication plant, we emphasize the use of high-quality tools because we understand how they contribute to the overall quality of our work, particularly in demanding sectors like medical devices and industrial equipment.
Key aspects of drill bit construction to consider include:
Drill bit materials and finishes are critical factors that determine the performance and lifespan of a drill bit, especially when working with stainless steel. As a company specializing in CNC fabrication services, we’ve seen firsthand how the right material and finish can make a significant difference in the efficiency and quality of our work, particularly for clients in industries such as consumer products and energy and renewable energy.
A twist drill bit is the most common type of drill bit used for general-purpose drilling. It gets its name from the helical flutes that “twist” around the body of the bit. Twist drill bits are versatile and can be used to drill a variety of materials, including wood, plastic, and metal, including stainless. We use twist drill bits extensively in our CNC fabrication processes, catering to a wide range of industries, from electronics to telecommunications.
Here’s how a twist drill bit works:
A step drill bit, also known as a unibit, is a cone-shaped bit with a series of steps that increase in diameter. Each step acts as a separate drill size, allowing you to drill multiple hole sizes with a single bit. Step drill bits are particularly useful when working with sheet metal, including stainless steel sheet metal, as they can create clean, burr-free holes. For example, a client in the automotive industry might use a step drill to create mounting holes of various sizes in a stainless steel panel.
Here are some advantages of using a step drill:
A masonry drill bit is designed for drilling into concrete, brick, stone, and other masonry materials. It typically has a carbide tip brazed onto a steel body. While carbide is a very hard material, it’s important to understand that masonry drill bits are not suitable for drilling stainless steel. Using a masonry drill bit on stainless steel is strongly discouraged. We once had a client in the construction industry who mistakenly attempted this, resulting in a damaged workpiece and a broken bit.
Here’s why:
Selecting the right drill bit for your project is crucial for achieving optimal results, especially when working with challenging materials like stainless steel. As a provider of CNC fabrication services, we often advise our clients on tool selection to ensure the success of their projects, particularly in industries like aerospace and defense where precision is paramount.
Here’s a step-by-step buying guide to help you choose the right drill bit:
Installer bits, also known as bellhanger bits or electrician’s bits, are a specialized type of drill bit designed for drilling holes for wires and cables. They are typically longer than standard twist drill bits, ranging from 6 to 18 inches or more. Installer bits often have a small hole near the tip or in the flute, which is used to pull wires back through the hole after drilling. In our CNC fabrication work, we often encounter clients in the telecommunications and electronics industries who require these specialized bits for routing cables within enclosures or through walls.
Here are some key features of installer bits:
Proper maintenance of your drill and drill bits is essential for ensuring their longevity and optimal performance. As a company that relies heavily on precision machining, we understand the importance of tool maintenance. We implement strict maintenance protocols in our CNC fabrication processes to minimize downtime and maintain the highest quality standards for our clients across various industries, including industrial equipment and robotics.
Here are some tips for maintaining your drill and drill bits:
The best type of drill for stainless steel is one that can handle the heat generated during the drilling process and is compatible with cobalt or carbide-tipped drill bits. A drill press is often preferred for its stability and control, but a high-quality handheld drill can also be used with the right technique.
While you might be able to make some progress with a regular high-speed steel (HSS) drill bit, it’s not recommended. Stainless steel will quickly dull the bit, and you’ll likely end up with a damaged workpiece and a broken bit. Cobalt or carbide-tipped drill bits are the best choice.
To prevent overheating, use a cutting fluid or lubricant, apply steady but not excessive pressure, and use a pecking motion (drill a short distance, then retract the bit to clear chips and allow it to cool). Choosing the correct drill bit (cobalt or carbide) is also crucial.
The size of the pilot hole depends on the size of the drill bit you’ll be using for the final hole. A general rule of thumb is to use a pilot hole that’s slightly smaller than the web thickness of the final drill bit.
How often you need to sharpen your drill bits depends on how frequently you use them and the types of materials you’re drilling. When you notice that it takes more effort to drill a hole or the drill bit is producing excessive heat, it’s time to sharpen it. For optimal performance, especially when working with stainless steel, it’s a good idea to inspect and sharpen your bits regularly.
No, a hammer drill is designed for masonry and concrete, not metal. The hammering action is not only unnecessary but also detrimental when drilling stainless steel. It can damage the bit, the workpiece, and even the drill itself.
Here are the most important things to remember when drilling stainless steel:
Internal Links:
Are you ready to experience the precision and efficiency of our CNC fabrication services?
We’ve shared our expertise on selecting and using the best drill bits for stainless steel, a critical aspect of many manufacturing processes. As a leading CNC fabrication service provider, we’re committed to delivering high-quality components to our clients across a wide range of industries. Our expertise in CNC machining, 5-axis CNC machining, and precision machining, combined with our advanced fabrication services, such as laser cutting and sheet metal fabrication, allows us to handle even the most complex projects.
Whether you’re in aerospace, automotive, medical devices, or any other industry that demands precision and reliability, we have the capabilities and experience to meet your needs. Our rapid prototyping and on-demand manufacturing services ensure that you get your parts quickly and efficiently, while our commitment to quality ensures that they meet the highest standards.
Don’t leave the success of your project to chance. Contact us today to discuss your specific requirements and discover how our CNC fabrication services can help you achieve your goals. We’re confident that our expertise and dedication to customer satisfaction will make us your preferred partner for all your manufacturing needs.
Get the latest trends and facts about CNC fabrication from our blog.
Shenzhen Runkey Precision Technology Co. Ltd, a subsidiary of the Tensun Group, is your trusted one-stop solution for custom manufacturing from prototyping to production.Transforming your idea into reality with digital manufacturing resources,streamlined processes, expert guidance,accelerated timelines, and uncompromising quality.
©2024. CNC Fabrication All Rights Reserved.