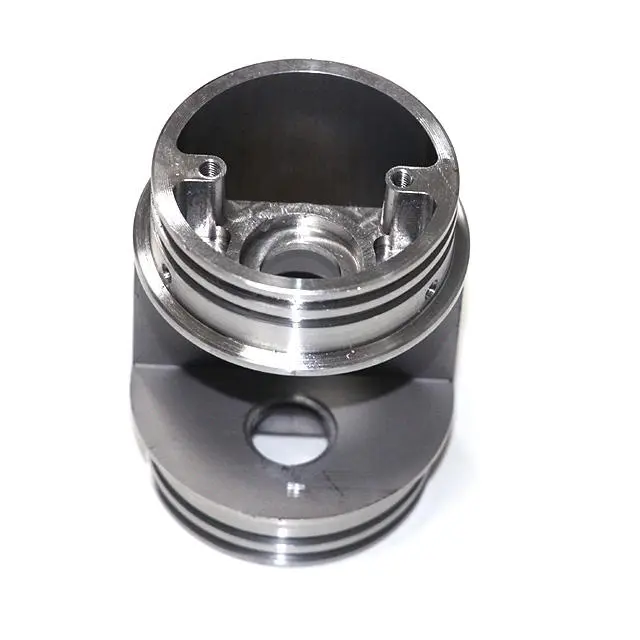
- +8615586668226
- [email protected]
- No. 30, Hongbang Industrial Park, Shenzhen
The accuracy of any machined part, especially in fields like aerospace or medical devices, hinges on the correct selection of drill bits. Using the wrong drill size can lead to a range of problems, from imprecise holes to tool breakage. For CNC machining, where precision is paramount, a thorough understanding of drill bit sizes is not just beneficial—it’s essential. The right size directly impacts the quality of the hole and the overall integrity of the part. Whether you’re working on aluminum, steel, or a composite material, knowing the correct drill bit sizes is the cornerstone of efficient and accurate manufacturing. It’s about avoiding errors, saving time, and ensuring the final product meets exacting specifications. At CNC, we emphasize the importance of precision and expertise in every project, which includes a deep understanding of drill specifications and standards.
When we talk about machining services, the ability to consistently produce precise holes is essential for quality control. Imagine the impact of using a wrong size drill bits – it can lead to ruined parts and costly delays. Therefore, understanding the different drill bit sizes, their applications, and how to choose the correct one for a specific material and hole size is crucial for success in CNC machining. It’s a skill every CNC operator needs to master. Moreover, the correct drill size ensures that taps can create precise threads when needed, further enhancing the functionality and usability of the part.
There’s a broad spectrum of drill bits, each designed for specific applications. Among the most commonly used are twist drills, which are versatile and suitable for general-purpose drilling in various materials. Then we have spade drill and step drill bits, known for their efficiency in making large holes. Each type has its particular strengths and weaknesses. Understanding these differences is vital to selecting the correct tool. At CNC Fabrication, we specialize in optimizing processes for precise outcomes, recommending the most effective cutting tools based on the application.
The standard drill set often includes a range of sizes, usually from the smallest to larger diameters, available in both fractional inch and metric sizes. For specialized applications, we use letter gauge or wire gauge drill bits. This diversity of sizes ensures the ability to tackle any project, regardless of the complexity or specific material requirement. The choice of the correct drill bit is vital to minimize the risk of breakage and maximize tool life, and is a cornerstone of successful CNC machining. For example, when drilling stainless steel, we’d use specialized cutting tools optimized for the material.
The most fundamental distinction in drill bit sizes lies between fractional inch (imperial) and metric systems. Fractional sizes are commonly used in the United States, where sizes are measured in inches, usually expressed as fractions, such as 1/4″ or 3/8″. Metric drill sizes, on the other hand, use millimeters, like 6mm or 10mm. Understanding this difference is vital when working with global standards or when importing or exporting CNC parts. The transition between imperial and metric sizes can be confusing, highlighting the importance of using accurate conversion charts or tables, which are critical in preventing errors during machining. At CNC, we understand this and regularly use accurate conversion tables to prevent mistakes.
Fractional sizes are measured in inches, often expressed as fractions or in decimal form. Metric sizes are measured in millimeters, and the sizes are listed as whole numbers. It’s important to have a grasp of both systems since different industries may favor one over the other. Having access to reliable conversion tables is also critical when you are working on projects that involve both metric and fractional systems. This ensures that the correct hole size can be achieved, no matter the specified system of measurement.
A drill size chart is an invaluable tool for any machinist, serving as a quick reference for drill bit diameters across various size systems. These charts typically list drill sizes in fractional, metric, wire gauge, and letter gauge formats, providing the decimal equivalents of the diameters. To use a chart effectively, first identify the required hole size, whether from a drawing or specific project requirement. Once you’ve determined the target size, locate the matching drill size on the chart. Charts will often show multiple systems next to each other, allowing you to switch between systems seamlessly. Understanding the layout of the size chart prevents costly mistakes during machining, and also ensures the correct size drill bits are used.
Using a drill size chart is straightforward, but it requires attention to detail. Make sure to select the right system—fractional, metric, wire gauge, or letter gauge—based on the design specification. The chart will show the diameter of each drill bit in the selected system. For example, if you need to drill a hole with a 1/2 inch diameter, you would find this entry in the fractional column, which will show its decimal equivalent of 0.500 inches. Similarly, if you need to drill a 10mm hole, you’d look for the corresponding value in the metric column. These charts become the go-to resource for making informed decisions when selecting cutting tools, ensuring precision and avoiding delays or wasted materials.
Gauge drill bit sizes, especially wire gauge drill bit sizes, use a numerical system to indicate the tool diameter. This system is frequently used in the electronics industry, where the drill bit needed for small hole is very small. Wire gauge numbers work in reverse: the larger the gauge number, the smaller the diameter of the drill bit. This system is fundamentally different from fractional and metric sizes, which are based directly on physical measurements. Understanding these differences is paramount, especially when dealing with older designs or when selecting cutting tools for specialized applications in our machining services. The wire gauge system is different from the standard sizes in that, rather than being a direct measure, the wire gauge number refers to a specific tool diameter.
When comparing gauge drill bit sizes to standard drill bit sizes, it’s essential to use a conversion chart to find the equivalent diameter in metric or fractional units. The wire gauge numbers do not have any direct relationship with metric or fractional sizes and must be converted separately. You will often find a size chart that will give you the decimal equivalents of the diameters in the wire gauge system. It is vital that anyone using wire gauge bits makes sure to understand the system, to avoid mistakes. At CNC, our experience means that we can handle all systems of measurement.
Metric drill bit sizes are essential in international manufacturing settings, where the metric system is the standard. A metric drill size is measured in millimeters (mm) and is shown as a whole number or a number with a decimal place. They are used for any application where metric sizes are required by the design or the project specification. Knowing when to use metric sizes is critical for avoiding confusion and ensuring accuracy. It’s usually best to use metric when working from international drawings or when making parts for industries that use the metric system.
When working on CNC parts, the specification for the hole will dictate which system of measurement should be used. If the design specifies metric sizes, then metric drill bits are necessary. The decimal number may be rounded up to the nearest available size drill bits, or the closest standard metric size may be used if no exact size drill bits are available. The usage of metric drill bit sizes allows for greater consistency when machining parts for international customers. With metric sizes, every measurement will follow the same standard, thus avoiding any confusion and reducing the potential for human error.
Wire gauge drill bit sizes are a unique system that uses numbers to specify drill bit diameters. This contrasts sharply with fractional and metric systems, where the sizes are measured in inches or millimeters, respectively. Wire gauge sizes increase as the wire gauge number decreases. For example, a #20 wire gauge drill bit has a larger diameter than a #30 wire gauge drill bit. The relationship is not linear, and this requires the use of a size chart that will show you the diameter. This system is most frequently used in the electronics industry, where components may require very small holes.
Unlike fractional and metric systems, where the sizes are directly related to physical measurements, the wire gauge system is specific to tool diameters. The system does not follow a linear relationship, and they must be looked up separately using a drill size chart. At CNC, we have extensive experience with all these different sizing systems, and use this knowledge to maintain our high level of precision in all that we do. The knowledge of different sizing systems helps us to maintain high quality when providing our machining services.
The relationship between drill size and tap size is a critical part of making threads inside a hole. Taps are used to create the thread after the hole has been made, and the drill size must be smaller than the tap size to allow for the threads to be formed correctly. This ensures the tap has enough material to grip and cut a thread. Therefore, when designing parts for CNC machining, you must carefully consider the correct drill size to use to achieve the correct thread. A drill and tap size chart is an invaluable tool for this purpose.
The correct drill size before tapping is known as the “tap drill size,” and the size chart specifies the exact drill size to be used for a specific tap size and thread. If the hole is too big, the threads will be too shallow and will not hold the screw correctly. If it is too small, the tap may break, and the thread will be difficult to create. The use of a drill and tap size chart ensures accuracy in this process, and when used correctly, will prevent the wastage of tools and material. At CNC, we know how important this process is, and we use standard sizes to ensure all parts are made to specifications.
When designing parts for efficient CNC machining, it’s crucial to consider the standard drill bit sizes available. Avoid specifying hole sizes that are not commonly available, as this can lead to higher costs and longer production times. Instead, choose sizes that correspond to standard sizes or to the commonly available metric sizes. It’s also important to clearly specify the hole size, the required tolerance, and any surface finish required. Understanding what is a standard drill size for your project will make the machining process much easier.
When working on the design, it’s important to specify the correct hole sizes required for each project. This includes the diameter, depth, and any tolerances that need to be met. The design should take into account the smallest possible size drill bits that can be used, and should be carefully planned to avoid small hole sizes, as this can lead to tool breakage. If you have any questions, always check with your manufacturer to make sure that you are adhering to standard sizes. This attention to detail will allow the manufacturer to produce cnc parts at the quality and precision that you require.
Finding a reliable conversion chart for drill bit sizes is important for anyone doing machining. There are many resources available online and in print. Look for charts that are comprehensive, accurate, and easy to use. The best charts will include fractional, metric, wire gauge, and letter gauge systems, showing the decimal equivalents. Conversion tables are essential for designers and engineers, who need to convert between different systems of measurement. At CNC, we always use the latest resources to ensure all conversions are correct.
Many resources are available. There are websites, which contain conversion tables that allow the user to switch between english and metric units and between standard metric and other gauge systems. You can also find printed charts that are designed to last a long time, and can be a useful addition to any workshop. The best resources are regularly updated to ensure that they are accurate and easy to use, and will show diameters are shown in all systems. At CNC, we find the conversion tables to be an invaluable tool. We use conversion tables to ensure all cnc parts are produced to our highest standards, and we regularly check that our tools are up to date.
What is a standard drill bit?
A standard drill bit is a cutting tool with a cylindrical shank that comes in a range of sizes. These are commonly used for general-purpose drilling.
What are standard drill bit sizes?
Standard drill bit sizes include fractional inch, metric, letter gauge, and wire gauge systems, each with specified diameters for different purposes. A size chart can help you select the appropriate tool.
How does wire gauge numbering work?
In the wire gauge system, the tool diameters that increase as the wire gauge number decreases. It’s often used for very small holes and requires a conversion chart to determine the diameter.
What does ‘letter gauge’ mean when talking about drill bits?
Letter gauge systems refer to tool diameters that are identified by a letter. The system continues from a to z, with A being the smallest size and z being the largest.
What is a drill and tap size chart?
A drill and tap size chart specifies the correct drill size required for a specific tap size to form the threads properly. It’s critical for making threads correctly and avoiding tool breakage.
Where can I find a reliable drill bit size chart online?
Many reliable resources are available online including manufacturing websites and machining services suppliers that provide both fractional and metric charts, as well as other gauge system conversion tables. Always verify the source of the chart for accuracy.
Ready to take your CNC machining to the next level? At CNC Fabrication, we combine our technical expertise and dedication to quality to produce precision parts. Explore our machining services, including CNC milling, CNC turning, and 5 axis CNC machining and see how we can help with your next project. We also specialize in sheet metal fabrication and laser cutting. Consider our rapid prototyping services for your new product development or on demand manufacturing to accelerate your production. Let’s discuss your next project! Contact us today.
Machining Services
Fabrication Services
CNC Solutions
Rapid Prototyping
Surface Finishing
Aluminum Extrusion
Get the latest trends and facts about CNC fabrication from our blog.
Shenzhen Runkey Precision Technology Co. Ltd, a subsidiary of the Tensun Group, is your trusted one-stop solution for custom manufacturing from prototyping to production.Transforming your idea into reality with digital manufacturing resources,streamlined processes, expert guidance,accelerated timelines, and uncompromising quality.
©2024. CNC Fabrication All Rights Reserved.