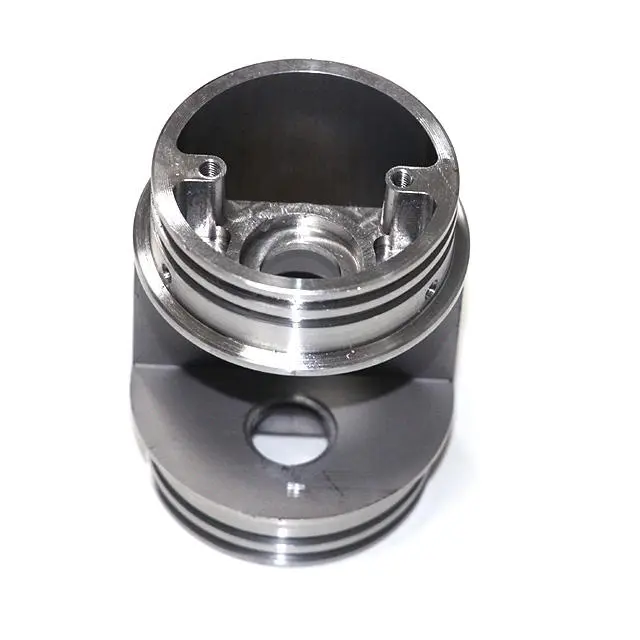
- +8615586668226
- [email protected]
- No. 30, Hongbang Industrial Park, Shenzhen
Electroplating, also known as electrodeposition, is an electrochemical process used to coat a conductive substrate (metal) with a thin layer of another metal. This process involves using an electric current to deposit metal ions from an electrolyte solution onto the substrate, forming a uniform metal coating. The substrate acts as the cathode (negatively charged electrode), while the metal to be plated acts as the anode (positively charged electrode).
The electroplating process relies on a chemical reaction where the positively charged metal ions in the electrolyte are attracted to the negatively charged cathode (the object being plated). These ions gain electrons at the cathode and are reduced, forming a solid metallic layer on the substrate’s surface. This layer can be extremely thin, offering precise control over the coating thickness.
Electroplating offers a myriad of benefits, making it an essential process in various industries. It enhances corrosion resistance, improves electrical conductivity, increases wear resistance, enhances aesthetic appeal (e.g., gold plating), and can even improve the surface hardness of the substrate. For instance, nickel plating offers exceptional corrosion resistance, while copper plating is known for its excellent electrical conductivity.
Consider the automotive industry: electroplating is crucial for protecting parts from wear and tear, extending their lifespan. Similarly, in electronics, gold and silver plating are frequently employed to ensure reliable electrical connections. The versatility of electroplating allows manufacturers to tailor the properties of a metal surface to meet specific requirements.
Several types of electroplating exist, each designed for specific applications. Some common types include:
Nickel Plating: Provides excellent corrosion resistance and wear resistance.
Copper Plating: Enhances electrical conductivity and acts as a base for other plating processes.
Gold Plating: Offers superior corrosion resistance and is often used in electronics.
Silver Plating: Provides high electrical conductivity and reflectivity.
Chromium Plating: Creates a hard, wear-resistant, and decorative surface.
The electroplating process involves several key components:
Anode: The positively charged electrode, typically made of the metal to be plated. It supplies the metal ions to the electrolyte solution.
Cathode: The negatively charged electrode, which is the object being plated. Metal ions from the electrolyte are deposited onto the cathode.
Electrolyte: A conductive solution containing dissolved metal salts. It acts as a medium for the transfer of metal ions between the anode and cathode. For instance, in copper electroplating, the electrolyte might be copper sulfate.
Direct Current (DC) Power Supply: Provides the electric current required for the electroplating process.
Electroplating is widely used in a diverse range of industries, including:
Aerospace: Protecting components from harsh environments.
Automotive: Enhancing corrosion resistance and appearance of parts.
Electronics: Ensuring reliable electrical contacts and conductivity.
Medical Devices: Improving biocompatibility and corrosion resistance.
Consumer Products: Enhancing aesthetics and durability.
Electroplating prevents corrosion by creating a protective barrier between the substrate and the corrosive environment. For example, plating a steel part with nickel creates a layer of nickel that prevents oxygen and moisture from reaching the steel, thus inhibiting rust formation. The choice of plating material depends on the specific application and the type of corrosion that needs to be prevented.
Selecting the appropriate electroplating method requires careful consideration of factors such as the substrate material, desired properties of the coating (e.g., corrosion resistance, hardness, conductivity), cost, and environmental impact. Two common methods are:
Rack Plating: Individual parts are hung on racks and immersed in the plating solution.
Barrel Plating: Smaller parts are tumbled in a barrel containing the plating solution.
Successful electroplating requires attention to several crucial factors, including:
Surface Preparation: Proper cleaning and pre-treatment of the substrate are essential for achieving a strong and uniform coating.
Electrolyte Concentration and Temperature: Maintaining the correct electrolyte parameters ensures optimal plating performance.
Current Density: The amount of current applied per unit area affects the plating rate and quality.
Plating Time: The duration of the plating process determines the thickness of the coating.
The electroplating industry is constantly evolving, with ongoing research and development focused on improving efficiency, reducing environmental impact, and exploring new applications. Emerging trends include pulse plating, composite plating, and the use of nanomaterials.
CNC fabrication manufacturing plants offer precision machining and fabrication services that can seamlessly integrate with electroplating processes. Precisely machined parts ensure optimal surface preparation for electroplating, leading to higher quality coatings. Moreover, partnering with a CNC fabrication facility can streamline the entire manufacturing process, from design to finishing, offering a comprehensive solution for your project needs. Consider CNC solutions for your next electroplating project.
What is the difference between electroplating and plating? Electroplating specifically uses an electric current to deposit the metal, while plating can refer to other coating methods as well.
Is electroplating expensive? The cost of electroplating varies depending on several factors, including the type of metal being plated, the size and complexity of the part, and the required thickness of the coating.
Can any metal be electroplated? Most metals can be electroplated, although some require specialized techniques.
How long does an electroplated coating last? The lifespan of an electroplated coating depends on factors such as the type of plating, the environment it is exposed to, and the level of wear and tear it experiences.
What are the environmental concerns associated with electroplating? Some electroplating processes use hazardous chemicals. However, there is a growing emphasis on developing more environmentally friendly plating solutions.
How is electroplating used in rapid prototyping? Electroplating can be used to add a functional or decorative finish to prototypes.
Electroplating enhances the properties of metal surfaces, including corrosion resistance, conductivity, and appearance.
Different types of electroplating exist, each suited for specific applications.
The electroplating process involves the anode, cathode, electrolyte, and a direct current source.
Proper surface preparation and process control are crucial for successful electroplating.
CNC fabrication manufacturing plants can complement electroplating processes, providing precision machined parts and streamlined manufacturing solutions.
The electroplating industry is continuously evolving, with ongoing advancements in techniques and materials. Remember to choose the right electroplating method, material, and partner to achieve your desired results. Contact us today to discuss your next project and explore how our expertise in CNC fabrication and machining services can help you achieve your goals.
Get the latest trends and facts about CNC fabrication from our blog.
Shenzhen Runkey Precision Technology Co. Ltd, a subsidiary of the Tensun Group, is your trusted one-stop solution for custom manufacturing from prototyping to production.Transforming your idea into reality with digital manufacturing resources,streamlined processes, expert guidance,accelerated timelines, and uncompromising quality.
©2024. CNC Fabrication All Rights Reserved.