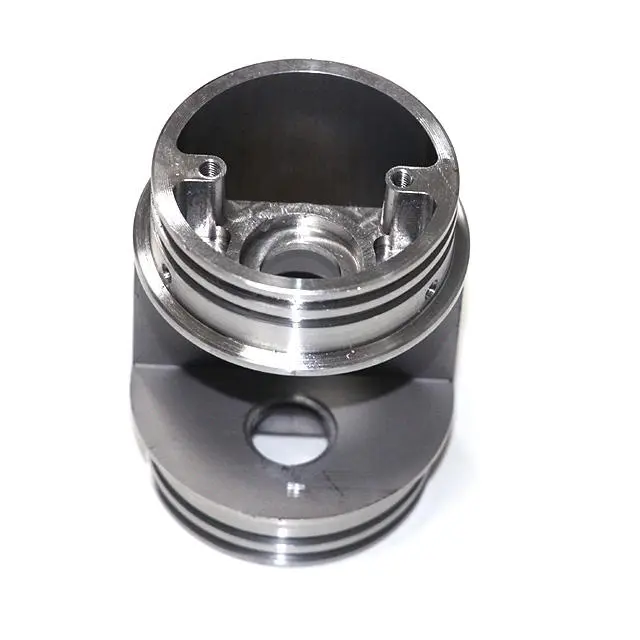
- +8615586668226
- [email protected]
- No. 30, Hongbang Industrial Park, Shenzhen
Understanding the factors influencing sheet metal fabrication costs is crucial for effective cost management. Material choice, design complexity, and manufacturing processes all play a significant role. For instance, stainless steel typically costs more than standard steel. Intricate designs with numerous bends, welds, and tight tolerances require specialized tooling and increase labor costs, driving up the overall cost.
Beyond material and design, other factors like surface finishing (e.g., powder coating) and post-processing steps add to the final expense. Shipping costs, especially for large or heavy sheet metal products, can also significantly impact the budget. Finally, the metal fabrication company’s hourly cost and cost per service also play a role.
The cost of raw materials makes up a significant portion of your total sheet metal fabrication project cost. Common sheet metals like aluminum and steel have different price points, and specialized alloys can be considerably more expensive. Carefully consider the required properties of your sheet metal part and choose the most cost-effective sheet metal materials that meet your needs. For example, if high strength isn’t critical, opting for a less expensive raw material can result in significant cost savings.
Furthermore, the metal market is dynamic, with fluctuating prices. Partnering with a knowledgeable metal fabricator who understands these fluctuations can help you negotiate material costs effectively and minimize expenses. They can advise on suitable alternatives and sourcing strategies. Our Materials page provides more information about various material options and their characteristics.
Absolutely! Simplifying your sheet metal design is one of the most effective ways to reduce sheet metal fabrication costs. Minimize bends, welds, and complex features whenever possible. Each bend adds time and labor to the fabrication process, increasing the overall product cost. Prioritize functionality and strive for clean, streamlined designs.
Even small changes to your sheet metal design can add up to big savings. For instance, reducing the number of angle bends or simplifying complex curves can streamline the metal fabrication process and lower labor costs. Consider consulting with experienced designers for design tips on optimizing your design for manufacturability. CNC Solutions can offer various design optimization services.
Bends are essential in sheet metal fabrication, but they directly influence the cost of sheet metal parts. The more bends a part requires, the higher the production cost. This is due to the added time and specialized tooling necessary for each bend. Bend radii also matter – radius equal to or greater than the thickness of the sheet is generally easier and cheaper to achieve. Small bends on large, thick sheet metal are difficult and add significantly to costs.
When designing sheet metal parts, aim to minimize the number of bends and optimize their placement. Consider using features like tabs and slots instead of complex bends whenever possible. Employing techniques like CNC machining and strategically selecting appropriate fabrication methods may also help you reduce the number of bends needed.
Tight tolerances demand specialized equipment and meticulous attention during the sheet metal fabrication process. This translates directly to increased manufacturing cost. While precise metal fabrication is sometimes essential, carefully evaluate whether such tight tolerances are truly necessary for your sheet metal products. Loosening tolerances where possible can lead to significant cost savings without sacrificing functionality.
If your design requires tight tolerances, consider using more precise fabrication techniques like CNC Machining or Precision Machining. While these may seem more costly upfront, they can eliminate errors and reduce rework in the long run.
Using standard sheet gauges and sizes in your sheet metal design is a smart way to cut costs. Non-standard sizes often result in material waste and require additional processing, driving up expenses. Sticking to standard sheet sizes ensures efficient material usage and minimizes scrap, directly impacting your material cost. Before finalizing your design, refer to commonly available standard sheet dimensions to optimize your material usage.
Choosing standard sheet sizes minimizes waste and often leads to lower shipping costs. Custom sizes can necessitate specialized packaging and handling, increasing overall expenses. Additionally, working with standard sizes simplifies procurement, as suppliers readily stock these common dimensions.
Partnering with the right metal fabrication company is crucial for controlling costs. Look for a company with experience in custom sheet metal fabrication and a reputation for delivering high-quality work at competitive prices. Ask about their cost structure, experience with similar projects, and capabilities. A strong fabrication partner can provide valuable design tips and suggest cost-effective fabrication methods for your custom sheet metal fabrication project.
Seek out a fabrication partner like us, offering a range of services from Fabrication Services to Machining Services, who can provide a comprehensive solution under one roof. This can help streamline the entire process and reduce costs associated with multiple vendors.
(Image Here: image_url random image with alt attribute filling in the title.)
Design to reduce complexity by minimizing features like bends and welds. Using a cost-saving plan, optimize for standard sheet sizes to minimize waste. Explore alternative materials to find cost-effective options without compromising functionality. Remember, efficient design is key to reducing the cost of your sheet metal part.
By carefully considering factors such as bend radii, material thickness, and tolerance requirements, you can significantly reduce your sheet metal fabrication costs. Collaboration with an experienced metal fabricator can also help identify opportunities for cost savings during the designing sheet metal phase.
Develop a cost-saving plan by outlining specific design considerations aimed at reducing material usage, minimizing complex features, and optimizing for efficient manufacturing processes. This plan should encompass material selection, design simplification, tolerance optimization, and collaboration with your chosen fabrication partner.
Regularly review and update your plan based on market trends, material price fluctuations, and evolving project requirements. This proactive approach will help you maintain cost control throughout the entire sheet metal fabrication process. Remember to factor in potential shipping costs and explore options like local sourcing to minimize transportation expenses.
The future of sheet metal fabrication will likely see increased automation and the integration of advanced technologies like 3D printing and artificial intelligence. These advancements can lead to faster production times, reduced labor costs, and increased precision, ultimately lowering the cost of sheet metal fabrication services.
Keeping abreast of these trends will allow you to make informed decisions and leverage these new technologies to further reduce cost in your future sheet metal fabrication projects. Exploiting trends effectively and proactively will be pivotal for future cost and lead time optimization.
How can I estimate the cost of my sheet metal fabrication project?
Estimating costs involves considering the complexity of the design, material choice, quantity, and chosen fabrication processes. Contacting a fabrication company for a quote is recommended for accurate estimations.
What tolerances are achievable in sheet metal fabrication?
Achievable tolerances vary depending on the fabrication method and material. CNC machining generally offers tighter tolerances compared to traditional methods.
What are the lead times for sheet metal fabrication projects?
Lead times depend on project complexity, order volume, and the fabricator’s capacity. Discuss your timeline with the fabrication company to ensure they can meet your deadlines.
What are some common finishes for sheet metal parts?
Common finishes include powder coating, anodizing, plating, and painting. The choice depends on the desired aesthetic and functional requirements.
What are some cost-effective sheet metal materials?
Steel and aluminum are generally more cost-effective than specialized alloys. Choosing the right material depends on the application’s specific needs.
How can I improve the manufacturability of my sheet metal design?
Design for manufacturability (DFM) principles can significantly improve the efficiency and reduce costs. Consult with experienced fabricators for DFM guidance.
Simplify your design: Fewer bends, welds, and complex features mean lower costs.
Choose cost-effective materials: Opt for standard materials like steel or aluminum when possible.
Utilize standard sheet sizes: Minimize waste and reduce material costs.
Loosen tolerances where applicable: Tight tolerances increase costs.
Partner with an experienced fabricator: Their expertise can help optimize your design and fabrication process.
Develop a cost-saving plan: Proactively manage costs throughout your project.
By applying these tips, you can significantly reduce your sheet metal fabrication costs without compromising the quality or functionality of your product. Remember, a well-designed and efficiently manufactured part is not only cost-effective but also contributes to a successful project overall.
Get the latest trends and facts about CNC fabrication from our blog.
Shenzhen Runkey Precision Technology Co. Ltd, a subsidiary of the Tensun Group, is your trusted one-stop solution for custom manufacturing from prototyping to production.Transforming your idea into reality with digital manufacturing resources,streamlined processes, expert guidance,accelerated timelines, and uncompromising quality.
©2024. CNC Fabrication All Rights Reserved.