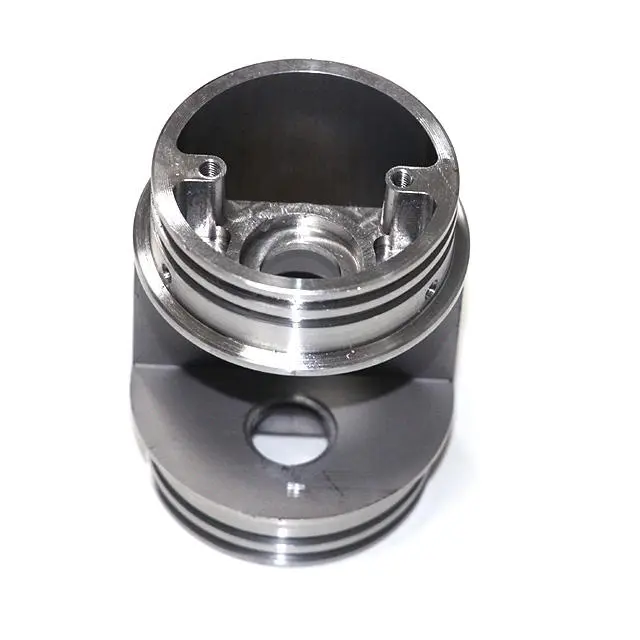
- +8615586668226
- [email protected]
- No. 30, Hongbang Industrial Park, Shenzhen
Comminution is the process of reducing solid materials to smaller pieces. In the mining industry, comminution is essential for breaking down ore into smaller particles to liberate the valuable mineral from the gangue. This process is the most energy-intensive step in mineral processing, often accounting for a significant portion of the operating costs of a mining operation. The primary goal is to achieve the desired particle size distribution, which is crucial for downstream processes like flotation and leaching.
Efficient comminution is vital because it directly impacts the recovery rate of the valuable mineral. By optimizing the comminution process, companies can reduce energy consumption and enhance the overall efficiency of their operations. In my experience as a cnc fabrication service manufacturing plant, I’ve seen firsthand how advancements in comminution technologies, like using high-quality CNC Machining, can significantly enhance precision and efficiency in creating comminution machinery. This precision ensures that the manufactured parts contribute to the overall effectiveness of the comminution process.
Crushers and mills are the primary pieces of equipment used in the comminution process. Crushers reduce the particle size of the ore through crushing, typically the first step in size reduction. Mills further reduce the particle size through grinding, often in a wet grinding environment. Crushers are classified into various types, including jaw crushers, cone crushers, and roll crushers, each suited to different stages of crushing.
Mills, on the other hand, can be ball mills, rod mills, or SAG mills, each employing different mechanisms to achieve the desired particle size. The choice of crusher and mill depends on the characteristics of the ore, the desired product size, and the overall design of the comminution circuit. We often discuss with our clients how we help them with Sheet Metal Fabrication, and the comminution equipment they use. They are always interested in hearing about our process and how it can help them improve their operations.
In mining, various types of crushers are employed depending on the stage of comminution and the ore characteristics. The primary crushing stage typically involves jaw crushers or gyratory crushers, which can handle large feed sizes and provide coarse reduction. Secondary crushing and tertiary crushing often utilize cone crushers or impact crushers, which offer finer control over the product size.
Roll crushers are also used, particularly in applications requiring a narrow size distribution. Each type of crusher has its unique design features and operating conditions, which determine its suitability for specific tasks. As a cnc fabrication service manufacturing plant, we specialize in producing components for a variety of crushers, ensuring they are built to withstand the rigorous demands of the mining environment. Our use of Precision Machining techniques ensures the durability and reliability of these components.
Crusher Type | Feed Size (mm) | Product Size (mm) | Reduction Ratio | Application |
Jaw Crusher | 100 – 1500 | 10 – 300 | 6:1 – 8:1 | Primary Crushing |
Gyratory Crusher | 150 – 2500 | 25 – 300 | 6:1 – 10:1 | Primary Crushing |
Cone Crusher | 50 – 300 | 5 – 50 | 4:1 – 6:1 | Secondary/Tertiary |
Impact Crusher | 50 – 800 | 5 – 100 | 10:1 – 25:1 | Secondary/Tertiary |
Roll Crusher | 10 – 100 | 1 – 20 | 3:1 – 4:1 | Fine Crushing/Narrow PSD |
Mills play a crucial role in the comminution process by further reducing the particle size after the crushing stages. Ball mills use steel balls as grinding media to grind the ore into a fine powder. Rod mills use steel rods, while SAG mills combine the functions of both crushing and grinding in a single piece of equipment. The choice of mill depends on the desired product size and the characteristics of the ore.
In wet grinding, water is added to the mill to facilitate the grinding process and improve the efficiency of downstream processes like flotation. SAG mills are particularly effective in handling large throughput and can significantly reduce the amount of energy required for comminution. Many of our clients are interested in improving their comminution process. We often provide them with custom solutions, such as fabricating components using 5 Axis CNC Machining to optimize their mills for maximum efficiency and performance.
A comminution circuit is a system of crushers, mills, conveyors, and other equipment designed to optimize the comminution process. Circuits can be open or closed, with closed circuits typically offering better control over the product size distribution. The design of a comminution circuit involves careful selection and arrangement of comminution equipment to achieve the desired throughput and product size while minimizing energy consumption.
Optimizing a comminution circuit involves balancing the load between different pieces of equipment, controlling the feed size and feed rate, and monitoring the operating conditions to ensure maximum efficiency. At our manufacturing plant, we work closely with mining companies to design and fabricate custom components for their comminution circuits. This ensures that each piece of equipment is optimized for its specific role in the circuit. For instance, we utilize advanced techniques like Laser Cutting to create precise parts that enhance the efficiency of the comminution process.
Particle size is a critical factor in determining the efficiency of comminution. The goal is to achieve a particle size distribution that maximizes the liberation of the valuable mineral while minimizing over-grinding, which wastes energy. The feed size to each stage of comminution must be carefully controlled to ensure optimal performance of the crushers and mills.
In general, finer grinding requires more energy, so it’s essential to strike a balance between liberation and energy consumption. Monitoring the particle size distribution throughout the comminution circuit allows operators to adjust the operating conditions and optimize the process for maximum efficiency. I always emphasize to my clients the importance of using precise manufacturing techniques, such as those we employ at our plant, to maintain tight tolerances on components, ensuring optimal particle size control and overall efficiency. We often employ Aluminum Extrusion techniques for creating specialized parts that are crucial to the comminution process, further enhancing its performance.
Energy consumption is one of the biggest challenges in comminution. The comminution process is inherently energy intensive, and reducing energy consumption is a major focus for the mining industry. The amount of energy required depends on factors such as the hardness of the ore, the desired product size, and the efficiency of the comminution equipment.
High energy consumption not only increases operating costs but also contributes to greenhouse gas emissions. Finding ways to reduce energy consumption in comminution is therefore crucial for both economic and environmental reasons. As a cnc fabrication service manufacturing plant, we are committed to developing innovative solutions that help our clients achieve energy savings in their comminution processes.
Improving energy efficiency in crushing and grinding involves a combination of equipment selection, process optimization, and technological innovation. Selecting energy-efficient equipment, such as high-pressure grinding rolls (HPGR) or advanced cone crushers, can significantly reduce energy consumption. Optimizing the comminution circuit to minimize energy use while maintaining throughput and product size is also crucial.
Technological innovations, such as advanced control systems and new comminution mechanisms, offer further opportunities for energy savings. By continuously monitoring and adjusting the operating conditions, operators can achieve significant reductions in energy consumption. At our manufacturing plant, we leverage the latest technologies to produce components that enhance the energy efficiency of comminution equipment, helping our clients reduce their operating costs and environmental impact.
The future of comminution is focused on developing new technologies and processes that are more energy efficient and sustainable. Innovations such as high-pressure grinding rolls (HPGR) and advanced ball mills are already making a significant impact on energy consumption in the mining industry. Emerging trends include the use of artificial intelligence and machine learning to optimize comminution circuits, as well as the development of new comminution mechanisms that require less energy.
Another trend is the increasing focus on dry comminution, which can significantly reduce water consumption in mineral processing. As a forward-thinking cnc fabrication service manufacturing plant, we are actively involved in researching and developing these new technologies, ensuring that we can offer our clients the most advanced and sustainable solutions for their comminution needs.
Several real-world case studies demonstrate the benefits of implementing energy-efficient comminution practices. For example, a major copper mine in Chile successfully reduced its energy consumption by 15% by replacing its conventional ball mills with HPGR technology. This not only lowered operating costs but also increased throughput and improved the overall efficiency of the comminution circuit.
Another case study involves a gold mine in Australia that optimized its comminution circuit using advanced process control systems. By continuously monitoring and adjusting the operating conditions, the mine achieved a 10% reduction in energy consumption while maintaining the desired product size distribution. These examples highlight the significant impact that energy-efficient comminution can have on the mining industry.
What is the main goal of comminution in mineral processing?
The main goal of comminution is to reduce the particle size of ore to liberate the valuable mineral from the gangue, making it easier to extract in downstream processes like flotation.
What are the most energy-intensive steps in mineral processing?
Crushing and grinding, collectively known as comminution, are the most energy-intensive steps, often accounting for a significant portion of the total energy consumption in a mineral processing plant.
How do high-pressure grinding rolls (HPGR) improve energy efficiency?
HPGR technology improves energy efficiency by using high pressure to crush the ore between two counter-rotating rolls, which requires less energy compared to traditional ball mills and can achieve finer grinding.
What role does particle size distribution play in comminution efficiency?
Particle size distribution is crucial for optimizing comminution efficiency. Achieving the right distribution ensures effective liberation of minerals while minimizing over-grinding, which saves energy and improves downstream processing.
How can mining operations reduce energy consumption in comminution?
Mining operations can reduce energy consumption by using energy-efficient equipment like HPGR, optimizing comminution circuits, implementing advanced process controls, and adopting new comminution technologies and mechanisms.
What are the benefits of dry comminution?
Dry comminution reduces water consumption, which is particularly beneficial in water-scarce regions. It can also lower energy consumption and improve the efficiency of downstream processes.
Comminution is a critical process in mining and mineral processing, aimed at reducing ore to smaller particles for efficient mineral extraction.
Crushers and mills are the primary equipment used, with various types suited to different stages of comminution.
Energy consumption is a major challenge in comminution, and improving energy efficiency is vital for economic and environmental reasons.
Optimizing comminution circuits involves selecting the right equipment, controlling feed size and feed rate, and monitoring operating conditions.
Technological innovations like HPGR and advanced control systems offer significant opportunities for reducing energy consumption and improving throughput.
Real-world case studies demonstrate that implementing energy-efficient practices can lead to substantial cost savings and increased operational efficiency.
Get the latest trends and facts about CNC fabrication from our blog.
Shenzhen Runkey Precision Technology Co. Ltd, a subsidiary of the Tensun Group, is your trusted one-stop solution for custom manufacturing from prototyping to production.Transforming your idea into reality with digital manufacturing resources,streamlined processes, expert guidance,accelerated timelines, and uncompromising quality.
©2024. CNC Fabrication All Rights Reserved.