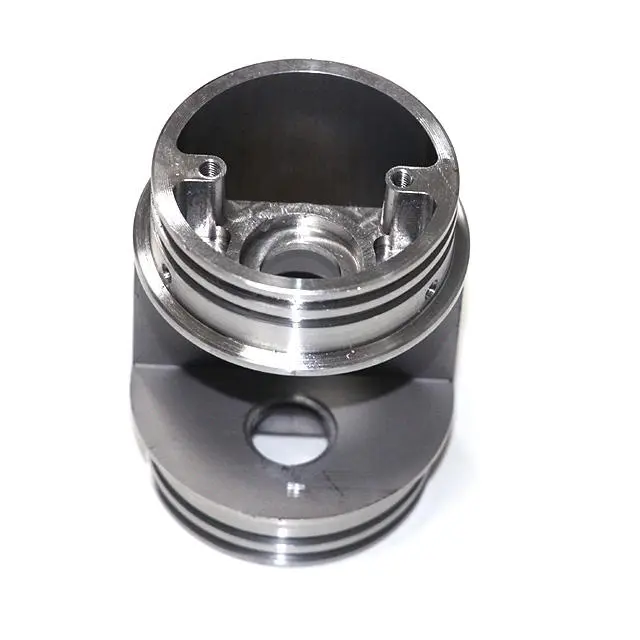
- +8615586668226
- [email protected]
- No. 30, Hongbang Industrial Park, Shenzhen
Anodizing is an electrochemical process that converts the metal surface of aluminum parts into a decorative, durable, corrosion-resistant, and wear-resistant finish. It’s like giving aluminum a tough, protective skin that also looks great! In simple terms, anodizing is an electrochemical process that converts the exterior of aluminum into aluminum oxide. This aluminum oxide layer is much harder than the original aluminum surface, making the aluminum parts more durable. It is not just a coating; instead, it is a part of the surface of the aluminum, and this fact provides better adhesion and protection. It’s often used to enhance the qualities of metal parts.
Think of it like this: When you leave aluminum out in the air, it forms a very thin layer of aluminum oxide. This thin layer is what protects it, but it’s also very easy to scratch. Anodizing just does the same thing but makes that aluminum oxide layer much, much thicker, harder, and better at protecting the aluminum component. If you’re not familiar with anodizing, it can seem complicated, but it’s really an elegant way to improve the durability and appearance of aluminum. This is why you see anodized aluminum is often used in many applications ranging from aerospace to consumer goods.
There are several key reasons why we anodize aluminum parts. The main reason is to make aluminum that is more durable. Untreated aluminum is relatively soft and prone to scratches, corrosion, and wear. By anodizing it, we create a much harder surface of the aluminum part. This layer of aluminum oxide is incredibly tough and can withstand a lot of abuse. It’s not just about toughness, though; it also makes the surface of aluminum parts more resistant to corrosion. This is particularly important in harsh environments where moisture and chemicals can rapidly degrade untreated aluminum.
Additionally, anodizing allows for a wide range of decorative finishes. It’s not just about creating a protective barrier; it’s also about making things look good. We can introduce a dye during the anodizing process, resulting in various colors and finishes. This means you can have aluminum parts in the exact color and texture you need. Many applications benefit from both the functional and aesthetic enhancements anodizing offers. Whether it’s a sleek black finish or a vibrant red, anodizing process can also help your project shine. Finally, it can enhance the insulating properties of the aluminum parts, making it useful in electronic components where electrical conductivity can be controlled.
The anodizing process is an amazing electrochemical process that converts the surface of the aluminum into a protective layer. First, the aluminum parts are cleaned thoroughly to remove any oils or contaminants. This is crucial because any impurities can affect the outcome of the anodizing process. After cleaning, the aluminum part is submerged in an anodizing tank filled with an anodizing solution. Then, electricity is passed through this solution, with the aluminum component acting as the anode (positive electrode).
As the electrical current flows, it causes the oxidation of aluminum. This oxidation of aluminum forms a layer of aluminum oxide on the surface of the aluminum. The porous nature of this process allows for the dye to be easily absorbed into the newly formed oxide layer. Once dyed, the anodized part is sealed, and this closes the pores and makes sure the color doesn’t fade or wash away. It is a very controlled process can also be used to ensure the correct anodizing thickness and durability of the finish. Understanding the steps and principles of the anodizing process is key to achieving desired results.
Aluminum anodizing work involves careful planning and execution to make sure the anodized part meets the required specifications. It’s not just about dunking aluminum pieces in a tank; it’s about precision and control. We first must ensure that the parts are properly cleaned. Any residue will cause problems in the anodizing process. Next, the choice of anodizing solution and electrical current settings is critical, and that depends on the desired finish, such as color and durability.
Also, the anodizing thickness depends on the intended use of aluminum parts. For example, aircraft parts require thicker anodizing layers to ensure durability and corrosion resistance. The color also needs careful attention, and this is achieved by immersing the anodized part in a dye solution after anodizing. Finally, sealing is a critical step, and it ensures that the dye is locked into the pores and the anodized layer is fully protective. All these considerations ensure the anodized parts perform as intended. It’s all about making sure that the finish you want is both beautiful and very useful.
Let’s talk about the anodizing 101, which means understanding the basics of what anodizing brings to the table. One of the main advantages is enhanced durability. Anodizing makes aluminum parts much harder, reducing the chances of scratches and wear. The abrasion resistance of anodized aluminum is a significant upgrade compared to bare aluminum. This means your anodized parts do not chip easily and last much longer.
Furthermore, anodizing improves corrosion resistance. The aluminum oxide layer acts as a protective barrier against moisture and chemicals, which prevents rust and degradation. The finish provides a highly durable and long-lasting coating. In addition, anodizing can improve the aesthetic appeal. The anodizing process allows for a variety of colors and finishes. You’re not just limited to the original silver-gray color of aluminum. Anodizing also helps with electrical insulation. This is great for electronics or for any application where electrical conductivity needs to be managed. The functional benefits of anodized aluminum make it a popular choice for various applications. Also, another important factor to consider is that anodizing does not add weight to the aluminum materials , as the new aluminum oxide is very light. Finally, anodized aluminum is often used because of its unique features and its good for parts.
Effectively anodize aluminum parts involves careful preparation and a controlled anodizing process. First, make sure that the parts to be anodized are completely clean. Remove any dirt, grease, or other contaminants before beginning the process. This can be done using cleaning agents that are suited for the aluminum materials you are using. Pre-treatment of the surface of the aluminum is key to a successful anodizing result, so we make sure that the parts are ready for the anodizing solution.
Next, you need to choose the correct anodizing solution. The choice will depend on the desired finish and applications of aluminum parts. The most common solution involves sulfuric acid, but chromic acid is also used in certain situations, so understanding the different types of anodizing processes will help you make the best choice. After selecting the anodizing solution, the aluminum parts are submerged in it, and an electrical current is passed through it. The electrical current settings must be precisely controlled to create the correct anodizing thickness and aluminum oxide layer. If you are going to use a dye, then after the anodizing process the aluminum pieces will be soaked in dye, and finally a sealing solution is used to lock in the color and enhance the durability and protection. Proper monitoring throughout each step is necessary to check the anodization of aluminum and ensure a good result. Also, the type of alloy that the aluminum wire and aluminum materials are made of affects how the anodizing works.
Choosing the type of anodizing is best for an application depends on what the part needs to withstand. There are several types of anodizing processes, each with unique characteristics. Type II anodizing is a common and versatile option. It uses sulfuric acid and creates a good layer thickness. Type II has moderate wear and corrosion resistance, making it suitable for many general-purpose applications where the parts may experience moderate wear.
However, type II is not good enough for all applications, because it won’t last in harsh environments. For those requiring higher durability, type III is best. Type III creates a layer that’s much thicker and harder than type II. This hard anodizing process is also the best type for maximum corrosion resistance, and it is ideal for demanding environments such as aircraft and military applications, because type iii is best for parts. Although the hard anodizing process is also a popular option it can be more costly. There is also type 1 which is less common and is used in less critical applications. Chromic acid anodizing produces the thinnest and is best when there is a low tolerance requirement. So the choice of suitable type of anodizing really depends on the demands and requirements of the aluminum component. When comparing different types of anodizing this will help you to choose the best anodizing for the parts. Always consider your application requirements.
When selecting an anodize finish, several key factors influence the decision. First, think about the intended environment for your aluminum component. If it will be exposed to harsh weather or chemicals, corrosion resistance will be a top priority. Type III is often selected for such cases. The anodizing process chosen can have a big impact on how well the finish protects the underlying aluminum substrate. Also, the desired aesthetic is a major consideration. Do you need a specific color? Different anodizing methods and dye choices can lead to various outcomes. Some finishes are more suitable for decorative purposes than for practical applications.
The thickness of the aluminum anodic coatings is also something you must think about. Thicker finishes provide more protection and durability but may require more precise manufacturing of the aluminum parts. Another key consideration is cost. Some types of anodizing processes can be more expensive than others. If you require high precision for the parts, then ensure you chose the appropriate method. You may find that a more cost effective process might be better for your project. To choose the most suitable type, you need to think about the needs and demands of your aluminum parts. So, think about what you want the anodized parts to do before choosing a finish. This will make sure that you get the best results for the project. Also, consider if you need to find small aluminum parts to be anodized.
Yes, let’s delve into a more detailed explanation of the different types of anodizing processes. As we discussed previously, Type II anodizing uses sulfuric acid and results in a coating with good corrosion and moderate wear resistance. This is suitable for general applications, but can’t always withstand chemical damage and stress. Type ii has moderate wear and can be used for all kinds of general purposes, but isn’t the best in every single situation. On the other hand, Type III anodizing, also known as hard coat anodizing, uses a higher voltage and stronger chemicals to create a thicker, harder, and more abrasion-resistant coating. Type iii is best for parts that can withstand chemical damage, high abrasion, and hard conditions.
Other types include type 1 is good because it uses chromic acid, and is the oldest type of anodizing. It’s commonly used in aerospace applications where corrosion resistance is essential, but it doesn’t offer the same level of hardness as type iii. Chromic acid anodizing produces the thinnest coating, and it’s used when you need dimensional precision. Each type of anodizing provides unique features to the aluminum parts. The acid anodizing produces the thinnest coating, which is very good for some niche applications. So, comparing different types of anodizing helps you select the suitable type of anodizing for your aluminum parts. Make sure you understand the strengths and weaknesses of each process, and if you are not sure how to choose the anodizing process, there are plenty of resources you can consult.
Anodized aluminum is found everywhere! In aerospace, anodized aluminum is essential for aircraft parts, where durability and resistance to corrosion are critical. It’s also used in automotive components, enhancing the appearance and longevity of car parts. In medical devices, anodized aluminum is favored for its biocompatibility and durability, ensuring that tools and implants remain safe for patients. You will find it in consumer products for their sleek finish and tough exterior.
What is the main difference between type II and type III anodizing?
Type II anodizing creates a thinner coating that is good for general use, while type III creates a thicker, harder coating for more demanding applications.
Can any aluminum alloy be anodized?
Most aluminum alloys can be anodized, but some perform better than others. The specific alloy can influence the final finish and durability.
Does anodizing change the dimensions of aluminum parts?
Yes, anodizing adds a layer to the surface, and this is something to bear in mind during the manufacturing process. The added layer is extremely small but it needs to be considered if tolerances are important.
How long does the anodizing process usually take?
The anodizing process time varies depending on the type and thickness of the coating needed, but it can range from a few minutes to several hours.
Are there color limitations for anodized aluminum parts?
While many colors are possible, the color range may be slightly limited by the nature of the dyes and the porous nature of the oxide layer. Some colors may be more vibrant and long lasting than others.
Is anodized aluminum more expensive?
Anodizing adds cost to the production of aluminum parts. It depends on the application, volume and type of anodizing, so check with your manufacturing partner.
Ready to make your aluminum projects the best they can be? If you need durable and beautiful aluminum parts, consider the benefits of anodizing. For precision engineering and dependable CNC Machining services, that include Sheet Metal Fabrication, and Precision Machining, contact us today! We can also help you with advanced techniques, such as 5 Axis CNC Machining, that can turn your design dreams into reality. You can also explore Rapid Prototyping and On Demand Manufacturing to get your ideas going quickly. Also, you can learn more about the Materials we work with.
Get the latest trends and facts about CNC fabrication from our blog.
Shenzhen Runkey Precision Technology Co. Ltd, a subsidiary of the Tensun Group, is your trusted one-stop solution for custom manufacturing from prototyping to production.Transforming your idea into reality with digital manufacturing resources,streamlined processes, expert guidance,accelerated timelines, and uncompromising quality.
©2024. CNC Fabrication All Rights Reserved.