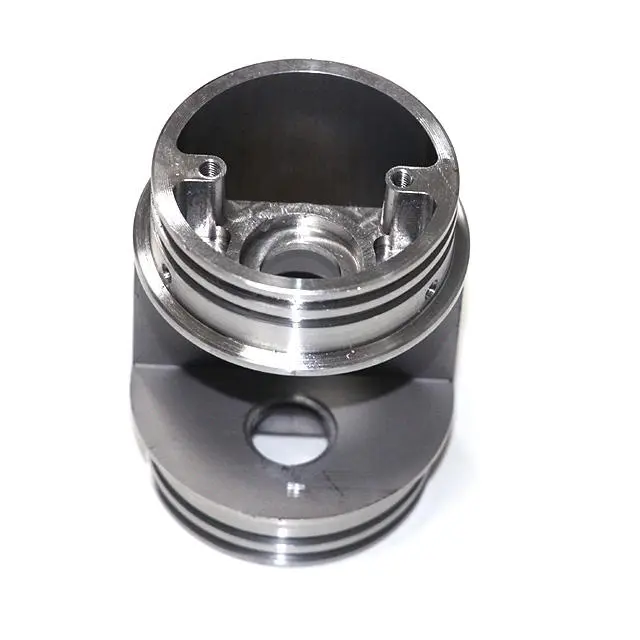
- +8615586668226
- [email protected]
- No. 30, Hongbang Industrial Park, Shenzhen
Stainless steel stamping is a specialized metal forming process that involves using stamping presses and dies to shape stainless steel sheets into various forms. This method is crucial in manufacturing because it allows for the mass production of identical, high-precision components. My personal experience in the industry has shown that the use of stainless steel in stamping offers numerous advantages, including enhanced corrosion resistance, durability, and aesthetic appeal.
Stamping on stainless steel is particularly significant in sectors like aerospace, automotive, medical devices, and consumer goods. The process’s ability to create intricate designs and maintain tight tolerances makes it an ideal choice for producing everything from small, delicate electronic connectors to large automotive parts. A case study I recall involved a client in the medical device industry who needed a specific type of surgical instrument. The stainless steel stamping process delivered the precision and hygiene standards required, far surpassing what other methods could offer.
The stainless steel stamping process begins with a blank piece of steel sheet. This blank is placed into a stamping press, where a tool, often called a punch, applies force to shape the metal. The process can be simple, involving a single punch and die set, or complex, requiring multiple stages and tools for operations like bending, coining, and deep drawing.
There are various type of stamping processes:
Progressive Die Stamping: This method uses a series of stamping stations. Each station performs a different operation on the metal sheet as it moves through the press, progressively shaping the part.
Transfer Die Stamping: Similar to progressive die stamping, but the part is transferred from one station to the next by a mechanical transport system.
Four-Slide Stamping: Also known as multi-slide stamping, this technique uses four tools to shape the workpiece. It’s particularly effective for creating complex parts with multiple bends.
Fine Blanking: This specialized process produces parts with very tight tolerances and smooth edges, often eliminating the need for secondary operations like deburring.
During my early years in the field, I witnessed firsthand the precision that stainless steel stamping could achieve. One memorable project involved creating small, intricate components for a communication device. The stamping process not only met the tight dimensional tolerances but also ensured the part’s structural integrity.
Several types of stainless steel are employed in the stamping process, each offering unique properties suited to different applications.
Type | Characteristics | Common Applications |
Austenitic | High corrosion resistance, excellent formability and weldability, non-magnetic | Kitchenware, food processing equipment, medical devices |
Ferritic | Good corrosion resistance, magnetic, lower cost than austenitic | Automotive exhaust systems, household appliances |
Martensitic | High strength and hardness, magnetic, moderate corrosion resistance | Knives, surgical instruments, tool and dies |
Duplex | High strength, excellent corrosion resistance, good weldability | Chemical processing, oil and gas, marine applications |
Precipitation Hardening | High strength and corrosion resistance, can be heat treated for additional hardness | Aerospace components, high-performance applications |
Grade 304 is a popular austenitic stainless steel known for its excellent formability and corrosion resistance. It’s commonly used in kitchenware and food processing equipment. Grade 316, another austenitic type, contains molybdenum, which enhances its resistance to pitting and crevice corrosion in chloride environments, making it suitable for marine applications.
Ferritic stainless steels, like grade 430, are another option. They offer good corrosion resistance and are less expensive than austenitic grades but have lower formability.
Choosing the right type depends on the application’s requirements. For instance, a project I managed for an automotive client required stamping components for exhaust systems. We opted for a ferritic grade due to its heat resistance and cost-effectiveness. To learn more about fabrication services click here: Fabrication Services
The benefits of stainless steel in stamping are numerous. Stainless steel’s inherent properties, such as high strength, corrosion resistance, and aesthetic appeal, make it an ideal choice for many applications. One of the primary advantages is its resistance to rust and staining, which is crucial for products exposed to harsh environments or requiring high hygiene standards.
Durability and Longevity: Stainless steel is known for its durability and long lifespan. Products made of stainless steel can withstand harsh conditions and maintain their integrity over time.
Corrosion Resistance: One of the most significant benefits of stainless steel is its exceptional corrosion resistance. The presence of chromium in stainless steel forms a passive protective layer that prevents rust and corrosion.
Aesthetic Appeal: Stainless steel has a sleek, modern appearance that is highly desirable in many applications, from kitchen appliances to architectural elements.
Hygiene and Cleanability: Stainless steel’s non-porous surface makes it easy to clean and resistant to bacterial growth. This property is crucial in industries like food processing, healthcare, and pharmaceuticals.
Recyclability: Stainless steel is 100% recyclable, making it an environmentally friendly choice. The ability to recycle stainless steel without any loss of quality supports sustainable manufacturing practices.
High Strength and Formability: Despite its strength, stainless steel can be easily formed and shaped through stamping. This combination of strength and formability allows for the creation of complex and durable metal parts.
Temperature Resistance: Stainless steel can withstand extreme temperatures, both high and low, without losing its properties. This makes it suitable for applications in harsh environments.
Moreover, stainless steel is recyclable, aligning with the growing emphasis on sustainability in manufacturing. A case I’m particularly proud of involved developing stamped parts for a new line of eco-friendly kitchen appliances. The use of stainless steel not only enhanced the products’ durability and appearance but also their environmental credentials. Explore our Precision Machining services for your precision needs.
Selecting the appropriate grade of stainless steel for stamping involves considering several factors:
Application Requirements: What are the specific needs of the application? Will the part be exposed to corrosive environments, high temperatures, or require high strength?
Formability: How complex is the part’s design? Some stainless steel grades offer better formability than others.
Cost: Different stainless steel grades vary in price. Balancing performance requirements with cost considerations is crucial.
Availability: Some grades may be more readily available than others, impacting lead times and project timelines.
For example, if you need to stamp a part that will be exposed to saltwater, grade 316 or 316L with their superior corrosion resistance would be a suitable choice. Conversely, for a decorative component where corrosion resistance is less critical, a more cost-effective grade like 430 might suffice.
In one of my projects, we needed to stamp components for medical devices. After careful evaluation, we chose grade 316L due to its excellent corrosion resistance and biocompatibility. Our Medical Devices division often deals with similar requirements.
Stamped stainless steel parts are ubiquitous, finding use across various industries. Here are some common applications:
Automotive: Body panels, exhaust components, brackets. Our automotive division relies heavily on stainless steel stamping for durable and corrosion-resistant parts. More details can be found here: Automotive.
Aerospace: Structural components, engine parts. The strength and lightweight nature of certain stainless steel alloys make them ideal for aerospace applications.
Medical Devices: Surgical instruments, implants. The biocompatibility and sterilizability of stainless steel are crucial in this sector.
Consumer Products: Appliances, utensils, sinks. The aesthetic appeal and durability of stainless steel make it popular in household items.
Industrial Equipment: Processing equipment, tanks, pipes. Stainless steel’s resistance to harsh chemicals and high temperatures is essential here.
One fascinating project I was involved in was developing stamped stainless steel components for a new line of high-end kitchen appliances. The combination of aesthetics, durability, and hygiene made stainless steel the perfect material choice.
Stamping stainless steel presents unique challenges compared to stamping softer metals:
Hardness: Stainless steel is harder than many other metals, requiring more force to stamp and potentially leading to increased tool wear.
Work Hardening: Stainless steel can work harden during the stamping process, meaning it becomes harder and less ductile as it’s deformed. This can necessitate annealing between stamping stages.
Springback: Stainless steel exhibits more springback than softer metals, meaning it tends to return to its original shape after being stamped. This requires careful tool design and process control to achieve the desired final shape.
Lubrication: Proper lubrication is crucial in stainless steel stamping to reduce friction, prevent galling, and extend tool life.
In my experience, addressing these challenges requires a combination of using appropriate stamping tools made of high-strength materials like tool steel, optimizing the stamping process parameters, and employing suitable lubricants.
Optimizing the stainless steel stamping process involves several key considerations:
Tool Design: Using high-quality stamping tools designed specifically for stainless steel is crucial. Features like proper clearances, radii, and surface finishes can significantly impact tool life and part quality.
Material Selection: Choosing the right grade of stainless steel based on the application’s requirements and the part’s design is essential.
Process Parameters: Optimizing parameters like stamping speed, pressure, and lubrication can improve efficiency and part quality.
Lubrication: Using appropriate lubricants formulated for stainless steel can reduce friction, prevent galling, and extend tool life.
A case study that highlights process optimization involved a project where we were experiencing excessive tool wear when stamping a complex stainless steel part. By switching to a different tool material, adjusting the punch speed, and using a specialized lubricant, we significantly increased tool life and improved part quality.
The field of stainless steel stamping is continually evolving, with ongoing innovations aimed at improving efficiency, quality, and capabilities:
Advanced Tool Materials: New tool materials, such as powdered metals and advanced coatings, are being developed to withstand the rigors of stamping stainless steel, offering increased wear resistance and longer tool life.
Finite Element Analysis (FEA): FEA is increasingly used in tool design and process simulation to predict material flow, identify potential problems, and optimize the stamping process before physical prototyping.
Servo Press Technology: Servo presses offer greater control over ram speed, position, and dwell time compared to traditional mechanical presses, enabling more precise stamping and the ability to handle complex shapes.
In-Die Sensing and Monitoring: Sensors integrated into stamping dies can monitor process parameters in real-time, allowing for immediate adjustments and improved process control.
These innovations are driving improvements in stainless steel stamping, enabling the production of more complex parts with tighter tolerances and higher quality while also increasing efficiency and reducing costs.
As a leading provider of stainless steel stamping services, we offer a unique combination of expertise, technology, and commitment to quality that sets us apart. Here’s why you should choose us for your next project:
Experience: With decades of experience in the metal stamping industry, we have the knowledge and skills to tackle even the most challenging projects. Our team of engineers and technicians is well-versed in the intricacies of stamping stainless steel and can provide expert guidance throughout the entire process, from design to production.
State-of-the-Art Equipment: We invest in the latest stamping technology, including advanced servo presses and high-precision tooling, to ensure that we can deliver superior results. Our state-of-the-art facility is equipped to handle a wide range of stainless steel stamping projects, from small, intricate parts to large, complex components.
Quality Commitment: We are committed to delivering the highest quality stamped stainless steel parts to our customers. Our rigorous quality control processes, including in-process inspections and final part verification, ensure optimal that every part we produce meets the most exacting standards.
Customization: We understand that every project is unique, and we work closely with our customers to develop customized solutions that meet their specific needs. Whether you need a standard stainless steel grade or a specialized alloy, we can help you select the right material and optimize the stamping process for your application.
Customer Service: We pride ourselves on providing exceptional customer service and support. From initial consultation to final delivery, we are dedicated to ensuring that our customers are satisfied with every aspect of our service.
Our extensive experience with diverse applications, including those in aerospace, automotive, and medical devices, gives us a unique perspective on the challenges and opportunities in stainless steel stamping. We leverage this knowledge to provide innovative solutions that meet our customers’ evolving needs.
What is the difference between stamping and deep drawing?
Stamping is a broad term that encompasses various metal forming processes, including deep drawing. Deep drawing is a specific type of stamping used to create parts with a depth greater than their diameter. It involves drawing a blank into a die cavity using a punch, resulting in a seamless, hollow shape.
Can stainless steel be stamped with decorative patterns?
Yes, stainless steel can be stamped with decorative patterns using design stamps or custom tooling. This is common in applications like jewelry, flatware, and architectural elements.
What is the typical lead time for a stainless steel stamping project?
Lead times can vary depending on the complexity of the part, the grade of stainless steel used, tooling requirements, and order volume. Simple parts with readily available materials and existing tooling may have shorter lead times, while complex parts requiring custom tooling or specialized materials may take longer.
How does the cost of stainless steel stamping compare to other metal forming processes?
The cost of stainless steel stamping depends on factors such as material cost, tooling complexity, part volume, and secondary operations required. While tooling costs for stamping can be higher than some other methods, it often becomes more cost-effective for high-volume production due to its repeatability and efficiency.
How thick of stainless steel can be stamped?
The thickness of stainless steel that can be stamped depends on the specific grade, the stamping equipment, and the part design. Generally, stainless steel sheets ranging from 0.01 inches (0.25 mm) to 0.25 inches (6.35 mm) can be stamped. However, specialized equipment and techniques may be required for thicker materials or complex shapes.
What is spring back in stainless steel stamping?
Springback refers to the tendency of stainless steel to partially return to its original shape after being stamped. This phenomenon is more pronounced in stainless steel compared to softer metals due to its higher yield strength. Proper tool design, stamping process parameters, and material selection can help mitigate the effects of springback.
In summary, stainless steel stamping is a versatile and essential manufacturing process with a wide range of applications across various industries. Here are the key takeaways:
Stainless steel stamping offers numerous benefits, including corrosion resistance, durability, aesthetic appeal, and recyclability.
Different types of stainless steel, such as austenitic, ferritic, and martensitic grades, are used in stamping, each with unique properties suited to different applications.
Choosing the right grade of stainless steel involves considering factors like application requirements, formability, cost, and availability.
Common applications of stamped stainless steel parts include automotive components, aerospace parts, medical devices, consumer products, and industrial equipment.
Challenges in stamping stainless steel include its hardness, work hardening, springback, and lubrication requirements.
Optimizing the stamping process involves tool design, material selection, process parameters, and lubrication.
Innovations in tool materials, FEA, servo press technology, and in-die sensing are advancing the field of stainless steel stamping.
Partnering with an experienced and reputable stainless steel stamping provider like us ensures access to expertise, state-of-the-art technology, and a commitment to quality.
By understanding the intricacies of stainless steel stamping and working with a trusted partner, manufacturers can leverage the many advantages of this process to produce high-quality, durable, and cost-effective parts for a wide range of applications.
As experts in the field, we’re committed to pushing the boundaries of what’s possible with stainless steel stamping. Our ongoing investment in research and development, combined with our passion for innovation, allows us to offer cutting-edge solutions that meet the evolving needs of our customers across diverse industries.
Whether you’re in the aerospace, automotive, medical device, or any other industry requiring precision metal components, we’re here to help you harness the power of stainless steel stamping.
Let’s collaborate to bring your vision to life.
Get the latest trends and facts about CNC fabrication from our blog.
Shenzhen Runkey Precision Technology Co. Ltd, a subsidiary of the Tensun Group, is your trusted one-stop solution for custom manufacturing from prototyping to production.Transforming your idea into reality with digital manufacturing resources,streamlined processes, expert guidance,accelerated timelines, and uncompromising quality.
©2024. CNC Fabrication All Rights Reserved.