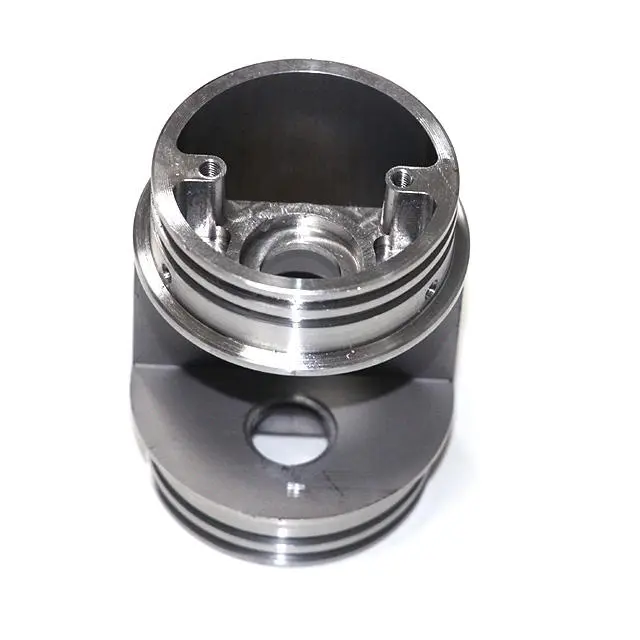
- +8615586668226
- [email protected]
- No. 30, Hongbang Industrial Park, Shenzhen
Metals are fundamental elements characterized by their unique properties, including electrical and thermal conductivity, malleability, ductility, and luster. They form the basis of countless materials used in every aspect of our lives. Their importance stems from their strength, durability, and versatility, making them indispensable for construction, manufacturing, and technological advancements.
Metals are essential for numerous industries, including Aerospace applications frequently utilize lightweight metals like titanium and magnesium for optimal performance., Automotive, Medical Devices, and Electronics. For example, in aerospace, lightweight yet strong metals like titanium and aluminum are crucial for aircraft construction. In the automotive sector, steel and aluminum alloys provide the necessary strength and fuel efficiency. The demand for specialized metals continues to grow, driving innovation in metal processing and CNC machining services.
Metals can be broadly categorized into ferrous and non-ferrous metals. Ferrous metals, like iron and steel, contain iron and are known for their strength and magnetic properties. Non-ferrous metals, such as aluminum, copper, and brass, do not contain iron and offer diverse properties like corrosion resistance and excellent conductivity. Understanding the distinction between these different types of metal is crucial for selecting the appropriate material for specific applications.
Within these two categories, a vast array of metals exists, each with unique characteristics. Copper, known for its excellent electrical conductivity, is widely used in wiring and electronics. Aluminum, a lightweight and corrosion-resistant metal, is commonly used in packaging, construction, and transportation. Understanding the specific properties of each metal type is essential for optimizing performance and longevity in CNC fabrication.
Metals are classified based on several key properties: physical, chemical, and mechanical. Physical properties include melting point, density, and thermal conductivity. Chemical properties describe how a metal reacts with other substances, including its corrosion resistance. Mechanical properties, such as tensile strength, hardness, and ductility, determine a metal’s ability to withstand stress and deformation.
For instance, titanium, with its high strength-to-weight ratio and excellent corrosion resistance, is highly valued in aerospace and medical applications. Stainless steel, an alloy of iron, chromium, and other elements, offers exceptional corrosion resistance and is used extensively in kitchen appliances and construction. These diverse properties enable the use of specific metals, such as ductile and malleable varieties, in highly specialized applications, driving the need for CNC Solutions.
Steel: A transition metal known for its strength and versatility. A versatile alloy of iron and carbon, used extensively in construction, automotive, and machinery. Different types of steel, like high carbon steel and stainless steel, offer varying levels of strength and corrosion resistance, making them suitable for different applications.
Aluminum: A lightweight metal that is ductile and resistant to corrosion, making it ideal for various applications. A lightweight and corrosion-resistant metal used in packaging, transportation, and construction.
Copper: A highly conductive metal, essential for electrical wiring and electronics.
Titanium: A strong, lightweight, and corrosion-resistant metal, such as magnesium, is used in aerospace, medical implants, and high-performance applications.
Zinc: Often used as a protective coating for steel (galvanization) and in alloys like brass.
Alloys are mixtures of two or more metals, or a metal and another element. Combining metals creates materials with enhanced properties, such as increased strength, improved corrosion resistance, or better machinability. For instance, brass, an alloy of copper and zinc, exhibits greater strength and corrosion resistance than pure copper. Bronze, an alloy of copper and tin, offers superior hardness and durability.
The development and application of alloys have revolutionized various industries. High-strength steel alloys enable the construction of lighter and more fuel-efficient vehicles. Nickel-based superalloys, capable of withstanding extreme temperatures and pressures, are crucial for jet engines and gas turbines. Understanding the specific properties of alloys is essential for optimizing design and performance in demanding applications.
The melting point, a crucial physical property, dictates the temperature at which a solid metal transforms into a liquid. This characteristic plays a vital role in metal processing techniques like casting, welding, and 5 Axis CNC Machining. Metals with lower melting points, like aluminum and zinc, are easier to cast and mold, while those with higher melting points, like steel and titanium, require more specialized equipment and techniques.
Tensile strength, a critical mechanical property, measures a metal’s resistance to being pulled apart. Hardness indicates a metal’s resistance to indentation or scratching. Durability encompasses a metal’s ability to withstand wear, tear, and corrosion over time. These properties are essential considerations in structural applications, ensuring the safety and longevity of buildings, bridges, and other critical infrastructure.
Different testing methods, such as tensile testing and hardness testing, determine these mechanical properties. Understanding these properties is crucial for selecting the appropriate metal for specific applications. For example, in the construction of high-rise buildings, high-strength steel is essential for supporting the immense weight and resisting wind loads.
Metals find diverse applications across various industries:
Aerospace: Aluminum and titanium are crucial for aircraft construction due to their lightweight and high strength.
Automotive: Steel and aluminum alloys provide the necessary strength and fuel efficiency in vehicle manufacturing.
Medical Devices: Titanium and stainless steel are commonly used in medical implants due to their biocompatibility and corrosion resistance.
Electronics: Copper is essential for electrical wiring and circuitry due to its excellent conductivity.
Construction: Steel, aluminum, and other metals are used in building structures, bridges, and infrastructure.
The demand for specific metals continues to evolve with technological advancements and changing industry needs. This necessitates continuous innovation in metal processing and manufacturing techniques like sheet metal fabrication often employs malleable metals to achieve intricate designs. and laser cutting.
Precious metals, such as gold, silver, and platinum, are highly valued for their rarity, aesthetic appeal, and resistance to corrosion. Gold, known for its lustrous appearance and inertness, is widely used in jewelry and as a store of value. Silver, with its excellent electrical conductivity, finds applications in electronics and silverware. Platinum, a dense and corrosion-resistant metal, is used in catalytic converters and high-end jewelry.
The value of precious metals fluctuates based on market demand and supply. They often serve as investment vehicles and are used in various industrial applications due to their unique properties.
A comprehensive list of metals and their properties can be found on the periodic table, a fundamental tool in chemistry. The periodic table organizes elements based on their atomic number and electron configuration, providing a systematic way to understand the properties of different metals. Online resources and scientific databases also offer detailed information about specific metals and their characteristics.
What is the difference between ferrous and non-ferrous metals? Ferrous metals, like wrought iron, contain iron, while non-ferrous metals do not.
Ferrous metals contain iron, while non-ferrous metals do not. This key distinction influences their properties and applications.
What is an alloy?
An alloy is a mixture of two or more metals, or a metal and another element. Alloys are created to enhance the properties of pure metals.
Why is stainless steel so corrosion-resistant?
Stainless steel contains chromium, which forms a protective oxide layer on the surface, preventing rust and corrosion.
What is the melting point of aluminum?
The melting point of aluminum is 660.32 degrees Celsius (1220.58 degrees Fahrenheit).
Metals are essential materials with diverse properties and applications.
Understanding the different types of metals, their classifications, and properties is crucial for selecting the right material for specific tasks.
Alloys, such as bronze and brass, play a vital role in enhancing metal properties and expanding their range of applications, including those that require good conductivity of electricity and heat.
The melting point of a metal significantly influences its processing and manufacturing methods.
Precious metals are valued for their rarity, aesthetic appeal, and resistance to corrosion.
The periodic table serves as a valuable resource for information about metals and their properties.
Remember, choosing the right metal, including options like cast iron or wrought iron, for your project can greatly impact its success. Consult with experts in CNC machining and fabrication, including the use of malleable and ductile metals, to ensure you select the ideal metal for your specific needs. Consider factors like strength, corrosion resistance, machinability, and cost to optimize performance and achieve your desired outcome. Whether you’re working on a complex aerospace project or a simple consumer product, understanding the world of metals is essential for innovation and efficiency.
Get the latest trends and facts about CNC fabrication from our blog.
Shenzhen Runkey Precision Technology Co. Ltd, a subsidiary of the Tensun Group, is your trusted one-stop solution for custom manufacturing from prototyping to production.Transforming your idea into reality with digital manufacturing resources,streamlined processes, expert guidance,accelerated timelines, and uncompromising quality.
©2024. CNC Fabrication All Rights Reserved.