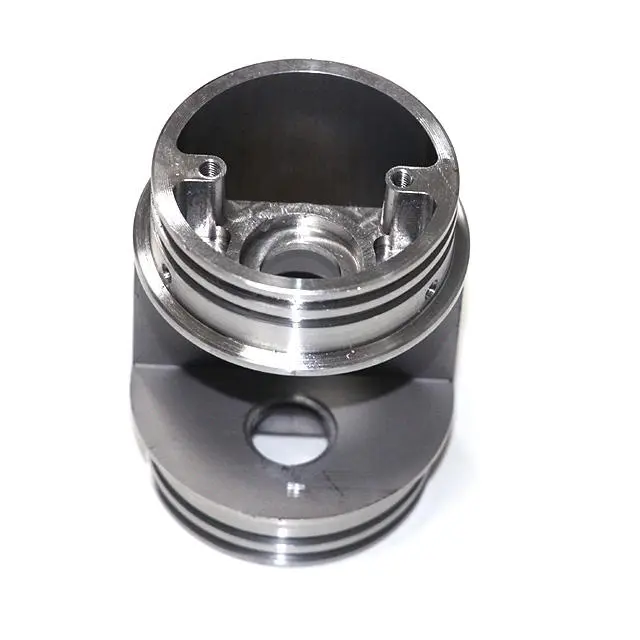
- +8615586668226
- [email protected]
- No. 30, Hongbang Industrial Park, Shenzhen
Steel, a fundamental material in countless industries, is essentially an alloy of iron and carbon, often with other elements added to achieve specific properties. We use steel for everything from structural beams to intricate electronic components. Its high strength and relatively low cost make it invaluable in manufacturing. However, steel has a vulnerability – it’s prone to rust and corrosion. This happens when iron in the steel reacts with oxygen and moisture, leading to a breakdown of the material. Without proper protection, steel structures and parts can degrade quickly. Therefore, preventing steel from rusting is paramount in many applications, driving the need for effective coating techniques like galvanizing and galvannealing.
The inherent susceptibility of steel to corrosion stems from its iron content, which is reactive in the presence of water and air. This reaction forms iron oxide, commonly known as rust, which weakens the steel and compromises its structural integrity. The issue is particularly concerning in outdoor applications or in environments with high humidity or exposure to corrosive elements. Fortunately, several methods have been developed to provide a protective barrier against corrosion, with galvanizing and galvannealing being among the most effective. Understanding the limitations of bare steel and the benefits of these protective measures is essential for any manufacturing project.
To galvanize steel, at its simplest, means to coat it with zinc. This process is crucial for preventing corrosion because zinc acts as a sacrificial anode. If the coating is scratched or damaged, the zinc will corrode first, protecting the underlying steel. Essentially, it’s a way to give steel a shield against rust. The process involves dipping the steel into molten zinc, creating a strong, bonded coating. This coating provides not only excellent corrosion resistance but also durability, extending the lifespan of the steel components. The specific way the steel is dipped can affect the final look of the galvanized product.
Galvanizing is an essential method for enhancing the durability of steel in various environments. By creating a protective zinc coating on the steel’s surface, it significantly reduces the risk of rust and deterioration. This protection is especially important when steel is exposed to harsh weather conditions, moisture, or corrosive chemicals. This process ensures that steel can maintain its structural integrity and performance over time. Galvanizing is a vital step in manufacturing processes that demand a high level of corrosion resistance.
Galvanized steel is the result of the galvanizing process we just discussed. In essence, galvanized steel is steel that has been coated in zinc to prevent corrosion. The typical method used to achieve this is called hot-dip galvanizing. Steel is dipped into a bath of molten zinc, which then bonds to the surface of the steel creating a protective zinc coating. This coating acts as a barrier, preventing moisture and oxygen from reaching the steel, thus stopping rust from forming. The appearance of galvanized steel often features a unique spangled pattern, a direct result of the zinc solidifying on the steel.
The manufacturing of galvanized steel involves a careful process to ensure a high-quality coating. Firstly, the steel is thoroughly cleaned to remove any oils, dirt, or other impurities that could interfere with the bonding of the zinc. This step is crucial for optimal adhesion. Next, the cleaned steel is dipped into the molten zinc bath, where the zinc coats the steel and creates a strong, metallurgically bonded layer. Finally, the steel is removed from the bath and allowed to cool. This hot-dip method ensures a robust and consistent zinc coating that provides long-lasting corrosion resistance to the steel. You will find this type of steel in many places from buildings to cars. We use galvanized steel a lot for sheet metal fabrication.
While both are steel with a protective coating, galvannealed steel is created through a different process. Like galvanized steel, steel is dipped in molten zinc. But, galvannealed steel goes through an extra step – it’s immediately heated to a higher temperature after being dipped in zinc. This additional annealing process causes the zinc to react with iron from the steel, forming a zinc-iron alloy coating. This zinc-iron alloy results in a matte, dull grey finish that’s quite different from the shiny surface of galvanized steel. This extra step significantly impacts the properties of the steel, making galvannealed steel uniquely suited for certain applications.
The creation of galvannealed steel is a carefully controlled process. After the steel is dipped in the molten zinc, it’s passed through an annealing furnace. This heating process causes the zinc and iron to fuse, creating the distinctive zinc-iron alloy coating. The presence of iron in the coating is a key difference. This coating is also harder, and better suited for painting and powder coating, when compared to standard galvanized steel. The galvannealed coating is also more consistent across the surface of the steel, which is useful for applications where a consistent surface finish is required. This process elevates the performance of the steel, making it ideal for applications that require superior paint adhesion and corrosion resistance.
While they have different production methods and different looks, both galvanized and galvannealed steel are designed to provide excellent protection against corrosion. Both types start with the same base material, steel, and undergo a hot-dip process involving zinc. Both types of steel offer a significant improvement in corrosion resistance compared to bare steel, extending the lifespan of structures and components. They also share the core principle of using zinc to protect the steel. Both galvanized and galvannealed steel are vital materials in various manufacturing industries, providing a dependable solution to corrosion issues.
The primary similarity lies in their shared purpose: preventing the steel beneath the coating from rusting and corroding. Both use a zinc coating to form a barrier against moisture and oxygen, two crucial factors in the rusting process. The application of zinc in both galvanized and galvannealed steel ensures that even if the coating is breached, the zinc corrodes preferentially, protecting the underlying steel. This mechanism provides a robust defense against rust and corrosion, making both types of steel highly desirable in many demanding environments. It also helps to use galvanized or galvannealed metal for projects requiring extra durability.
The coating on both galvanized steel and galvannealed steel is essential for their corrosion resistance. In galvanized steel, the coating is primarily composed of pure zinc, creating a layer that effectively shields the underlying steel. This zinc coating is typically thick, which allows it to provide long-lasting corrosion protection. In galvannealed steel, the coating is a zinc-iron alloy, a compound formed when zinc and iron react during the annealing process. The zinc-iron alloy coating is thinner but provides better paint adhesion and a more consistent surface of the steel.
The specific composition of the coating impacts the performance of each type of steel. A zinc coating on galvanized steel provides a sacrificial barrier, meaning that the zinc will corrode first, safeguarding the steel. The zinc-iron alloy coating on galvannealed steel has the same sacrificial benefit but offers a harder and more uniform surface. This harder surface is a primary reason why many manufacturers choose galvannealed steel for projects that require painting or powder coating. Because of the iron in the coating, galvannealed steel is often more suited for steel parts that require a specific surface finish.
While both prevent corrosion, there are key differences between galvanized and galvannealed steel. The most noticeable difference is the appearance: galvanized steel has a shiny, spangled finish due to the solidification of pure zinc, whereas galvannealed steel has a dull, matte gray appearance, a result of the zinc-iron alloy coating. Another critical distinction is the coating’s composition; galvanized steel features a pure zinc coating, while galvannealed steel boasts a zinc-iron alloy coating. This difference in coating leads to variations in their weldability, paintability, and overall surface quality, with galvannealed steel being generally better suited for painting applications and requiring less preparation.
Another key difference lies in the corrosion performance of galvannealed. Although both galvanized and galvannealed offer excellent corrosion resistance, the zinc-iron alloy in galvannealed steel results in a harder, more uniform, and more abrasion-resistant coating. Galvannealed steel is also typically easier to weld because the zinc-iron alloy has a lower melting point compared to the pure zinc in galvanized steel. The slightly lower thickness of the galvannealed coating can also affect weld quality. However, welding galvanized is still a common practice in the industry. These factors often influence which type of steel is selected for specific manufacturing projects.
The question of whether galvanized or galvannealed steel is “better” doesn’t have a single answer. The ideal choice depends on the application’s specific requirements. Galvanized steel is generally more cost-effective and has a thicker zinc coating, which provides excellent corrosion resistance, especially in highly corrosive environments. It’s a good choice for projects where the visual appearance isn’t a primary concern, but corrosion protection is. However, galvanized steel may not be the best for painting due to its slick surface.
On the other hand, galvannealed steel is superior for applications that require painting or powder coating. The zinc-iron alloy coating provides a better surface for paint adhesion, and it is often chosen for steel parts where surface finish and paintability are critical. Galvannealed steel is also favored in applications where a consistent, matte surface finish is needed. The slight price increase of galvannealed steel over galvanized steel is often justified by its superior paint adhesion and weldability when working with steel products. Ultimately, the “better” material depends on the specific needs of the project at hand.
Galvanized steel is frequently used in construction, such as roofing and structural beams, due to its robust corrosion resistance. Its ability to withstand harsh weather conditions makes it a popular choice in outdoor applications. You’ll also find galvanized steel in highway guardrails, fencing, and other infrastructure projects, where protecting against rust and corrosion is crucial. Galvanized steel is also a common choice for larger scale sheet metal parts when a long lifespan and good protection against the elements is paramount.
Galvannealed steel, however, is often found in automotive manufacturing, particularly in car bodies and interior panels, due to its excellent paint adhesion and weldability. Its smoother, more uniform surface of galvannealed steel makes it ideal for applications that require a high-quality finish. Additionally, galvannealed steel is often used in appliances, HVAC systems, and other consumer goods where both durability and aesthetics are important. The ability to paint galvannealed steel efficiently makes it preferable in these applications, helping to achieve a perfect surface. Both galvanized and galvannealed steel are also extremely useful for sheet metal fabrication.
At CNC Fabrication, we possess the expertise and technology to handle all your sheet metal needs, whether you require galvanized or galvannealed steel. Our skilled team understands the nuances of working with these materials, ensuring precision and quality in every project. With our advanced CNC machinery, we can accurately fabricate metal parts to meet your exact specifications. We can assist you in choosing the right type of steel for your project to maximize durability and performance. Our team at CNC Fabrication is ready to provide solutions that meet all your manufacturing requirements.
We also offer a variety of services, including laser cutting, bending, and welding, ensuring that we can handle even the most complex sheet metal designs. At CNC Fabrication, we understand the importance of using the right materials and coatings to ensure the longevity and performance of your products. Whether your project demands the rugged durability of galvanized steel or the superior paintability of galvannealed steel, we have the capability to deliver. Let us help you galvanize your projects with our expert sheet metal fabrication services. Our goal is to become your trusted partner in manufacturing, producing parts with excellent precision and quality. We work with steel and metal on a daily basis. If you need on demand manufacturing or even rapid prototyping we can assist!
What is the difference between a40 and a60 galvannealed steel?
A40 and A60 refer to the coating weights for galvannealed steel. A60 has a heavier zinc-iron alloy coating than A40, offering enhanced corrosion resistance. The a40 galvannealed finish is preferable when a lighter coating is sufficient, and the a60 galvannealed steel is better in more demanding environments where greater protection against corrosion is required.
Is galvannealed steel more expensive than galvanized steel?
Yes, galvannealed steel is typically more expensive than galvanized steel due to the additional heating and annealing steps involved in its production. However, the benefits of improved paint adhesion and welding performance may outweigh the cost increase in many applications. The added performance that you get from galvannealed steel usually makes it worth the investment.
Can you paint over galvanized steel?
While it is possible to paint over galvanized steel, it typically requires more preparation compared to galvannealed steel. Galvanized steel has a slick surface of the steel, and paint may not adhere well to the zinc coating unless properly treated. It is generally better to choose galvannealed steel if you require a painted steel finish.
Which is better for welding, galvanized or galvannealed steel?
Galvannealed steel is generally considered better for welding due to its thinner zinc-iron alloy coating and lower melting point of the coating, resulting in less splatter and more consistent welds. Welding galvanized requires more care and skill due to the higher amount of zinc that needs to be managed. It’s also important to consider which one will work best for your steel products.
What are the common uses of each type of steel?
Galvanized steel is commonly used in construction (roofing, beams), infrastructure (fences, guardrails), and outdoor applications where high corrosion resistance is needed. Galvannealed steel is frequently found in automotive manufacturing, appliances, and consumer goods where paint adhesion and a smooth finish are essential.
Can both types of steel be used in sheet metal fabrication?
Absolutely. Both galvanized and galvannealed steel are commonly used in sheet metal fabrication. The choice depends on the specific application requirements, such as the need for paint, weldability, and the environment in which the final product will be used. It also depends on the requirements for the steel metal needed. We utilize both for different sheet metal parts at CNC Fabrication.
At CNC Fabrication, we are dedicated to providing high-quality manufacturing solutions. Whether you need precision machining, sheet metal fabrication, or assistance with rapid prototyping, our team is ready to help. Contact us today to discuss how we can support your next project.
Contact us today to discuss your next project!
Learn more about our machining services
Explore our fabrication capabilities
Get the latest trends and facts about CNC fabrication from our blog.
Shenzhen Runkey Precision Technology Co. Ltd, a subsidiary of the Tensun Group, is your trusted one-stop solution for custom manufacturing from prototyping to production.Transforming your idea into reality with digital manufacturing resources,streamlined processes, expert guidance,accelerated timelines, and uncompromising quality.
©2024. CNC Fabrication All Rights Reserved.