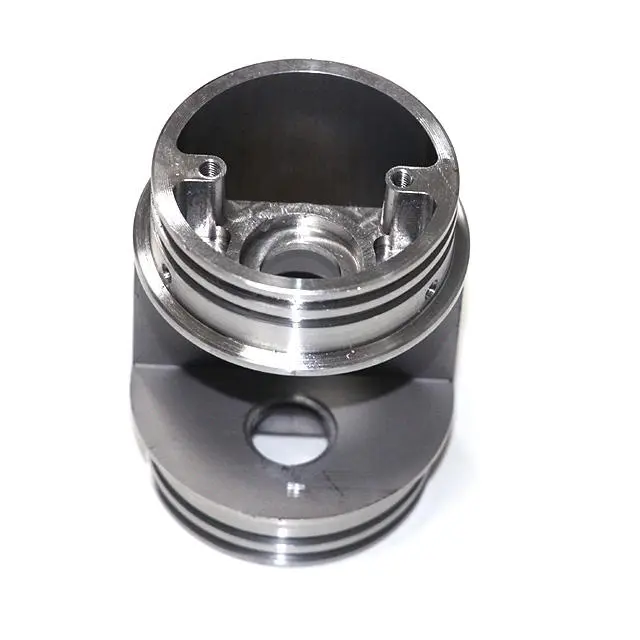
- +8615586668226
- [email protected]
- No. 30, Hongbang Industrial Park, Shenzhen
Steel, known for its remarkable strength and hardness, stands out as a primary material for CNC machining. Its robustness ensures durability in the final product, making it perfect for industries like aerospace and automotive, where component reliability is paramount. The versatility of steel allows it to be shaped into a variety of forms, from simple to highly intricate designs, meeting the diverse needs of our clients.
Moreover, the adaptability of steel in various grades, such as stainless steel and carbon steel, provides options to suit specific project requirements. For instance, stainless steel offers excellent corrosion resistance, ideal for medical devices, while carbon steel’s strength is a boon for heavy equipment parts. This flexibility in material selection underscores steel’s suitability for a wide array of CNC machining applications, ensuring that we can always find the right fit for your project.
The machinability of steel directly influences the efficiency and outcome of CNC machining projects. Machinability refers to how easily a material can be cut and shaped without causing excessive wear on the cutting tools. Steel with good machinability allows for faster processing times, reduced tool wear, and a smoother surface finish, ultimately leading to lower production costs and higher quality parts.
For example, 1018 steel, a low carbon steel, is known for its excellent machinability. It’s easier to machine, making it a cost-effective option for many applications. Conversely, steel with lower machinability, like certain grades of stainless steel, may require slower machining speeds and more durable cutting tools, potentially increasing the overall project cost. Understanding the machinability of different steel types is crucial for optimizing the CNC machining process and achieving the desired results efficiently.
4140 steel, a type of alloy steel, is highly regarded in the CNC machining world for its exceptional balance of strength, toughness, and wear resistance. This steel alloy contains chromium and molybdenum, which enhance its hardness and make it resistant to high temperatures. These characteristics make 4140 steel particularly well-suited for components that undergo significant stress and wear, such as gears, shafts, and spindle parts used in heavy machinery.
The robustness of 4140 steel also makes it a preferred choice for industries like aerospace and tooling and dies, where precision and durability are non-negotiable. Its ability to maintain integrity under extreme conditions ensures that parts machined from 4140 will have a longer service life, providing value and reliability. If you require parts that are strong, long-lasting, and of high precision, 4140 steel is one of the best steel options.
1045 steel is a medium carbon steel known for its good balance of strength and toughness. It is commonly used in the CNC machining of parts that require moderate hardness and wear resistance. While 1045 offers improved mechanical properties compared to low carbon steels like 1018, it is not as hard as 4140. This makes it suitable for applications where high strength is required, but extreme hardness is not necessary.
However, the suitability of 1045 steel depends on the specific requirements of the project. For components subjected to high stress or requiring superior wear resistance, 4140 might be a more appropriate choice. On the other hand, 1045 steel is a great option for parts like bolts, studs, and less demanding gears, offering a cost-effective solution without compromising on quality. 1045 is easier to machine than 4140 and can give you a good surface finish.
1018 steel, a low carbon steel, is celebrated for its excellent machinability and weldability. It’s one of the most commonly used steels in CNC machining due to its ease of processing, which results in a good surface finish and reduced machine wear. 1018 is particularly suited for parts that require intricate shaping and detail, as its softness allows for precise cuts without compromising the structural integrity of the machine tools.
Moreover, 1018 steel is an economical choice for projects where high-strength and hardness are not primary concerns. Its applications range from simple brackets and spacers to more complex components that do not endure extreme stress. By choosing 1018, manufacturers can benefit from reduced production times and costs, making it an attractive option for a wide range of CNC machining projects. 1018 steel is a general purpose steel that is highly machinable and perfect for parts that do not need a lot of strength.
The surface finish of CNC machined steel parts is not just about aesthetics; it significantly impacts the functionality, durability, and performance of the components. A smoother surface finish can reduce friction between moving parts, improve corrosion resistance, and enhance the overall quality of the final product. Achieving the desired surface finish requires careful consideration of the machining process, including the choice of cutting tools, speeds, and feeds.
In industries such as medical devices and aerospace, where precision and reliability are critical, a high-quality surface finish is essential. It ensures that parts fit together perfectly, operate smoothly, and meet stringent quality standards. By focusing on achieving an optimal surface finish, we enhance the value and performance of CNC machined steel parts, meeting the exacting demands of these specialized sectors. Achieving a good surface finish when machining steel is very important, especially for parts that will come into contact with other moving parts.
Steel Type | Machinability | Surface Finish Quality | Recommended Applications |
1018 Steel | Excellent | Very Good | General purpose, low-stress components, intricate designs |
1045 Steel | Good | Good | Medium-stress components, bolts, studs, gears |
4140 Steel | Fair | Fair to Good | High-stress components, gears, shafts, aerospace parts |
304 Stainless | Fair | Good to Excellent | Corrosion-resistant parts, medical devices, food and packaging |
12L14 Steel | Excellent | Excellent | High-volume production, parts requiring excellent surface finish |
Choosing the right steel alloy is pivotal for achieving optimal machining results. Alloys are mixtures of steel with other elements, designed to enhance specific properties such as hardness, corrosion resistance, or machinability. For instance, stainless steel alloys, like 304, are renowned for their excellent corrosion resistance, making them ideal for applications exposed to harsh environments or requiring high levels of hygiene.
On the other hand, free machining steel grades, such as 12L14, contain additives like lead or sulfur that significantly improve machinability. These alloys allow for faster cutting speeds, reduced tool wear, and a superior surface finish, making them a preferred choice for high-volume production runs. By selecting the appropriate steel alloy for your CNC machining project, you can enhance both the efficiency of the machining process and the quality of the finished parts. 12l14 is a free machining steel that is frequently used in cnc machines.
The hardness of steel is a critical factor in CNC machining, directly impacting the choice of cutting tools, machining parameters, and the overall efficiency of the process. Harder steels, such as 4140, offer greater wear resistance and durability but can be more challenging to machine. They require robust cutting tools, often made from carbide or other high-strength materials, and may necessitate lower cutting speeds to prevent tool damage and ensure a quality surface finish.
Conversely, softer steels, like 1018, are easier to machine and allow for faster processing times. However, they may not offer the same level of durability or wear resistance as harder steels. Understanding the hardness of the steel you’re working with is essential for selecting the right machining strategy, optimizing production efficiency, and achieving the desired quality in the finished product.
Selecting the appropriate steel for your CNC milling needs involves a thorough assessment of the project requirements, including the intended use of the part, the operating environment, and the desired mechanical properties. Factors such as strength, hardness, corrosion resistance, and machinability should all be considered. For instance, parts intended for outdoor use or exposed to moisture may benefit from stainless steel due to its excellent corrosion resistance.
Additionally, the complexity of the part’s design can influence material selection. Intricate designs may require a more machinable steel, such as 1018, to achieve precise details without excessive tool wear. By carefully evaluating these factors and consulting with our team of experts, you can make an informed decision that ensures the success of your CNC milling project. Stainless steel may be a good choice for many projects due to its excellent corrosion resistance.
Welding CNC machined steel parts can be an effective way to join components, create complex assemblies, or repair damaged parts. The success of welding depends on the type of steel used, as well as the welding process and technique employed. Low carbon steels, such as 1018, are generally easier to weld and offer good weldability, making them suitable for a wide range of welding applications.
However, medium and high carbon steels, like 1045 and 4140, may require preheating or post-weld heat treatment to prevent cracking and ensure a strong, durable weld. Additionally, stainless steels require specific welding techniques and filler materials to maintain their corrosion resistance properties. Consulting with our welding experts can help you determine the best approach for welding your CNC machined steel parts, ensuring a successful and reliable outcome.
What is the best type of steel for CNC machining?
The best type of steel for CNC machining depends on the specific requirements of your project. 1018 steel is highly machinable and suitable for general-purpose applications, while 4140 steel offers greater strength and wear resistance for more demanding applications.
How does carbon content affect the machinability of steel?
Carbon content significantly affects the machinability of steel. Low carbon steels (e.g., 1018) are softer and easier to machine, while medium and high carbon steels (e.g., 1045, 4140) are harder and more challenging to machine but offer greater strength and wear resistance.
Can stainless steel be used in CNC machining?
Yes, stainless steel can be used in CNC machining, but it’s generally less machinable than carbon steel. Stainless steel is known for its excellent corrosion resistance and is often chosen for applications requiring this property, such as in medical devices and food processing equipment.
What is the difference between 1018 and 4140 steel?
1018 steel is a low carbon steel known for its excellent machinability and weldability, making it ideal for general-purpose applications. 4140 steel is a medium carbon alloy steel that offers higher strength, hardness, and wear resistance, suitable for more demanding applications like gears and shafts.
How do I choose the right surface finish for my steel parts?
The right surface finish for your steel parts depends on their intended use and operating environment. A smoother finish can reduce friction, improve corrosion resistance, and enhance the aesthetic appeal. Consider the functional requirements and consult with our experts to determine the optimal surface finish for your project.
Is it possible to improve the machinability of steel?
Yes, the machinability of steel can be improved by selecting free machining steel grades, such as 12L14, which contain additives like lead or sulfur. These additives help break up chips during the machining process, reducing tool wear and improving the surface finish.
Steel is a versatile and robust material, ideal for a wide range of CNC machining applications.
Understanding the machinability, hardness, and other properties of different steel types is crucial for optimizing the machining process and achieving high-quality results.
4140, 1045, and 1018 steels each offer unique benefits for CNC machining, catering to various project needs.
Surface finish significantly impacts the functionality and durability of steel parts, particularly in precision-demanding industries.
Choosing the right steel alloy and consulting with experts can enhance the efficiency of the machining process and the quality of the finished product.
As experts in CNC fabrication services, we’re here to guide you through every step of your project, from material selection to final assembly. Our extensive experience with diverse industries, including aerospace, automotive, medical devices, and more, enables us to provide tailored solutions that meet your specific needs. We encourage you to reach out to us to discuss your project and discover how our expertise in machining services, fabrication services, and CNC solutions can bring your vision to life. Let’s collaborate to create something exceptional together.
Get the latest trends and facts about CNC fabrication from our blog.
Shenzhen Runkey Precision Technology Co. Ltd, a subsidiary of the Tensun Group, is your trusted one-stop solution for custom manufacturing from prototyping to production.Transforming your idea into reality with digital manufacturing resources,streamlined processes, expert guidance,accelerated timelines, and uncompromising quality.
©2024. CNC Fabrication All Rights Reserved.