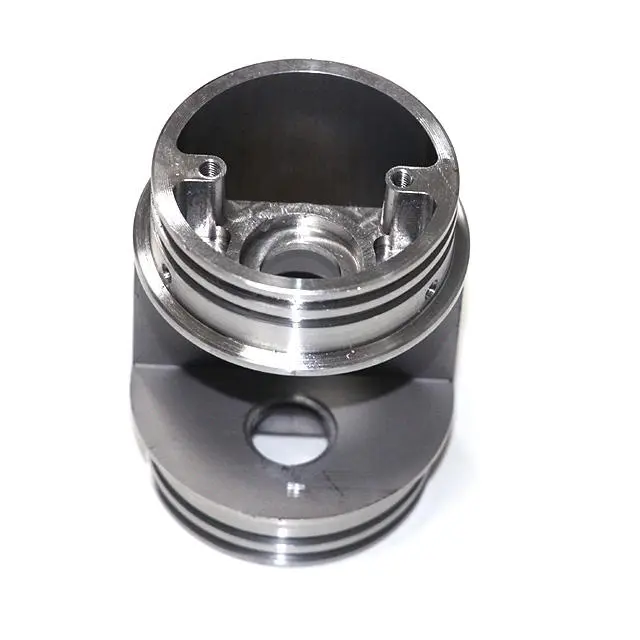
- +8615586668226
- [email protected]
- No. 30, Hongbang Industrial Park, Shenzhen
1018 steel is a low carbon steel known for its excellent machinability, weldability, and ductility. As a mild steel, it contains approximately 0.18% carbon content, which is indicated by the last two digits of its name. This steel grade is often used in applications that require good formability and ease of fabrication, such as CNC machining, forging, and cold forming.
One of the primary advantages of 1018 steel is its excellent machinability. It can be easily cut, shaped, and drilled, making it a favorite among machinists. Additionally, 1018 steel offers good weldability, allowing for strong and reliable joints. However, due to its low carbon content, 1018 steel has limited hardness and wear resistance compared to higher carbon steels. When you use 1018 steel for certain projects it can be carbonitrided or carburized 1018 steel.
4140 steel is a chromium-molybdenum alloy steel known for its high strength and hardness, excellent toughness, and good wear resistance. It contains approximately 0.40% carbon content, along with chromium and molybdenum, which enhance its hardenability and strength. The addition of chromium in 4140 steel contributes to its corrosion resistance as well. 4140 steel is often used in applications that require high strength and durability, such as gears, shafts, and structural components.
4140 steel offers superior mechanical properties compared to 1018 steel. It can be heat-treated to achieve higher levels of hardness and strength, making it suitable for demanding applications. 4140 steel also exhibits good toughness and fatigue resistance, ensuring reliable performance under stress. However, 4140 steel requires careful machining due to its hardness and may require specialized tooling.
When comparing 1018 vs 4140 steel, several key differences emerge. 1018 steel, being a low carbon steel, offers excellent machinability and weldability but has lower hardness and wear resistance. In contrast, 4140 steel is an alloy steel with higher carbon content and added alloying elements like chromium and molybdenum, which provide superior strength and hardness, toughness, and wear resistance.
Another significant difference is the response to heat treatment. 1018 steel can be case-hardened to improve its surface hardness, but it does not respond well to through-hardening processes. 4140 steel, on the other hand, can be heat-treated to achieve high levels of hardness throughout the material, making it suitable for applications that require high strength and durability. The differences between 1018 and 4140 are important to understand.
The carbon content in steel significantly influences its properties. In 1018 steel, the low carbon content (around 0.18%) results in a softer, more ductile metal that is easy to machine and weld. This makes 1018 steel ideal for applications that require forming and shaping. For example, if you were looking into different types of sheet metal fabrication.
Conversely, 4140 steel has a higher carbon content (around 0.40%), which contributes to its greater hardness and strength. The higher carbon level allows 4140 steel to be heat-treated to achieve higher hardness levels, making it suitable for applications that require wear resistance and durability. However, the increased carbon content also makes 4140 steel more challenging to machine compared to 1018 steel. Understanding the role of carbon content helps in selecting the appropriate steel alloy for specific applications.
Heat treatment is a critical process for modifying the properties of steel. For 1018 steel, heat treatment is typically limited to case hardening or carburizing, which increases the surface hardness while maintaining the core’s ductility. This process enhances the wear resistance of 1018 steel components without making them brittle.
4140 steel responds exceptionally well to various heat treatment processes, such as quenching and tempering. These processes significantly increase the hardness, strength, and toughness of 4140 steel. Heat treatment allows 4140 steel to achieve a Brinell hardness rating of up to 600, making it suitable for heavy-duty applications. Proper heat treatment of 4140 steel is crucial to unlock its full potential in terms of mechanical properties.
Hardness is a critical factor when choosing the right steel for a project. It determines the material’s resistance to deformation, scratching, and wear. 1018 steel has a relatively low hardness, making it easy to machine and form but less resistant to wear and abrasion. It might seem that 1018 and 4140 would not be a good fit for certain projects.
On the other hand, 4140 steel can achieve high hardness levels through heat treatment, making it ideal for applications that require wear resistance and durability. For instance, components like gears, shafts, and tools that experience high stress and friction benefit from the strength and hardness of 4140 steel. When selecting between 1018 vs 4140 steel, consider the hardness requirements of your application to ensure optimal performance.
The mechanical properties of steel, including strength, ductility, and toughness, are vital considerations for any project. 1018 steel offers good ductility and formability, making it suitable for applications that involve bending, forming, and welding. It has moderate strength but lower wear resistance compared to 4140 steel.
Property | 1018 Steel | 4140 Steel |
Carbon Content (%) | 0.14-0.20 | 0.38-0.43 |
Manganese (%) | 0.60-0.90 | 0.75-1.00 |
Phosphorus (%, max) | 0.040 | 0.035 |
Sulfur (%, max) | 0.050 | 0.040 |
Chromium (%) | – | 0.80-1.10 |
Molybdenum (%) | – | 0.15-0.25 |
Density (lb / cu. in) | 0.284 | 0.284 |
Tensile Strength, Ultimate (psi) | 63,800 | 95,000 – 245,000 (varies with heat treatment) |
Tensile Strength, Yield (psi) | 53,700 | 60,200 – 225,000 (varies with heat treatment) |
Elongation at Break (%) | 15.0 | 10.0 – 25.0 (varies with heat treatment) |
Reduction of Area (%) | 40.0 | 40.0 – 65.0 (varies with heat treatment) |
Hardness, Brinell | 126 | 197 – 600 (varies with heat treatment) |
Machinability | Good machinability due to low carbon content. Suitable for cold working. | Moderate machinability; pre-hardened and tempered conditions are easier to machine than annealed. |
Weldability | Excellent weldability; can be welded using most common methods without preheating or post-weld heat treatment. | Good weldability; requires preheating and post-weld heat treatment to prevent cracking and maintain mechanical properties. |
Heat Treatment | Typically not heat treated for hardening, but can be case hardened. | Responds well to heat treatment; can be hardened and tempered to achieve a wide range of mechanical properties. |
Common Uses | Commonly used for parts that require cold forming, bending, and welding, such as brackets, non-critical structural components. | Used in applications requiring high strength and wear resistance, such as gears, shafts, bolts, and tools. |
4140 steel provides superior mechanical properties, including higher tensile and yield strength, enhanced toughness, and better fatigue resistance. Its ability to be heat-treated allows for tailoring its properties to meet specific application requirements. The combination of strength and hardness in 4140 steel makes it suitable for high-stress applications in industries such as automotive, aerospace, and tooling. When deciding on the best steel grade you must understand these properties.
Wear resistance is the ability of a material to withstand surface damage caused by friction, abrasion, or erosion. It is a critical factor in applications where components are subjected to constant wear and tear. 1018 steel, with its lower hardness, has limited wear resistance and may not be suitable for applications involving high friction or abrasive conditions.
In contrast, 4140 steel exhibits excellent wear resistance, especially when heat-treated. The higher hardness and presence of alloying elements like chromium enhance its ability to resist wear. This makes 4140 steel ideal for components like gears, shafts, and tools that experience significant wear during operation. Choosing a steel with adequate wear resistance ensures the longevity and reliability of your components, reducing the need for frequent replacements and maintenance.
Machinability refers to the ease with which a material can be cut, shaped, and finished using machining processes. 1018 steel is known for its excellent machinability due to its low carbon content and softness. It can be easily machined using standard tools and techniques, resulting in smooth finishes and precise dimensions. This makes 1018 steel a preferred choice for applications that require extensive machining, such as CNC milling.
4140 steel, with its higher hardness and toughness, presents more challenges in machining. It requires specialized tooling and techniques to achieve desired results. However, with proper machining practices, 4140 steel can be effectively machined to produce high-quality components. The machinability of 4140 steel is often improved by heat-treating it to a lower hardness before machining, followed by a final heat treatment to achieve the desired properties.
Choosing between 1018 steel vs 4140 steel depends on the specific requirements of your project. 1018 steel is an excellent choice when machinability, weldability, and formability are priorities. It is suitable for applications that do not require high strength or wear resistance, such as brackets, non-critical structural components, and parts that undergo cold forming.
On the other hand, 4140 steel should be chosen when high strength, hardness, and wear resistance are essential. It is ideal for applications involving heavy loads, high stress, and abrasive conditions, such as gears, shafts, and tools. Consider factors like the operating environment, load conditions, and required durability when making your decision. Consulting with a materials expert can also provide valuable insights to help you select the right steel for your specific needs.
4140 vs 1018 is a common issue for many people. If you are looking for the best steel alloy for your project, you must think about these points. Choosing between 1018 and 4140 may not always be easy. That is why we are here to help. 1018 steel might be a good choice for some projects. It is important to understand the applications of 1018 before making your decision.
What are the main differences between 1018 and 4140 steel?
The main differences between 1018 and 4140 steel lie in their carbon content, mechanical properties, and response to heat treatment. 1018 steel is a low carbon steel with excellent machinability and weldability but lower hardness and wear resistance. 4140 steel is an alloy steel with higher carbon content, providing superior strength, hardness, and wear resistance, especially when heat-treated.
When should I opt for 4140 steel over 1018 steel?
Opt for 4140 steel when your application requires high strength, hardness, and wear resistance. 4140 steel is ideal for components that experience heavy loads, high stress, and abrasive conditions, such as gears, shafts, and tools. If machinability and weldability are more critical than strength, 1018 steel may be a better choice.
Can 1018 steel be hardened?
1018 steel can be case-hardened or carburized to improve its surface hardness and wear resistance. However, it does not respond well to through-hardening processes like 4140 steel. Case hardening creates a hard surface layer while maintaining the core’s ductility, making it suitable for applications that require a combination of toughness and surface wear resistance.
Is 4140 steel difficult to machine?
4140 steel presents more challenges in machining compared to 1018 steel due to its higher hardness and toughness. It requires specialized tooling and techniques to achieve desired results. However, with proper machining practices, such as using carbide tools and appropriate cutting speeds, 4140 steel can be effectively machined.
What industries commonly use 1018 and 4140 steel?
1018 steel is commonly used in industries that require good machinability and formability, such as construction, automotive, and general fabrication. 4140 steel is widely used in industries that demand high strength and durability, including aerospace, automotive, tooling, and heavy machinery.
How does the cost of 1018 steel compare to 4140 steel?
1018 steel is generally less expensive than 4140 steel due to its lower carbon content and simpler composition. The additional alloying elements and heat treatment requirements of 4140 steel contribute to its higher cost. However, the superior mechanical properties and performance of 4140 steel often justify its higher price in demanding applications.
1018 steel is a low carbon steel known for excellent machinability, weldability, and ductility.
4140 steel is a chromium-molybdenum alloy steel offering high strength, hardness, and wear resistance.
Carbon content significantly influences the properties of steel, with higher carbon leading to increased hardness and strength.
Heat treatment enhances the mechanical properties of steel, particularly in 4140 steel, which can achieve high hardness through quenching and tempering.
Hardness is crucial for determining a material’s resistance to deformation and wear, with 4140 steel providing superior wear resistance compared to 1018 steel.
1018 steel is ideal for applications requiring good machinability and formability, while 4140 steel is best for high-strength, high-wear applications.
Choosing the right steel involves considering factors such as carbon content, mechanical properties, heat treatment response, hardness, machinability, and cost.
Understanding the differences between 1018 vs 4140 steel is essential for selecting the appropriate steel for your project. Whether you need the machinability of 1018 steel or the strength and durability of 4140 steel, making an informed decision ensures optimal performance and longevity of your components. If you are in an industry like aerospace, automotive, or any other sector that relies on CNC fabrication, leveraging the right materials is crucial for success. We encourage you to contact us for expert guidance and top-notch fabrication services. Let us help you bring your projects to life with the perfect materials and precision engineering.
Get the latest trends and facts about CNC fabrication from our blog.
Shenzhen Runkey Precision Technology Co. Ltd, a subsidiary of the Tensun Group, is your trusted one-stop solution for custom manufacturing from prototyping to production.Transforming your idea into reality with digital manufacturing resources,streamlined processes, expert guidance,accelerated timelines, and uncompromising quality.
©2024. CNC Fabrication All Rights Reserved.