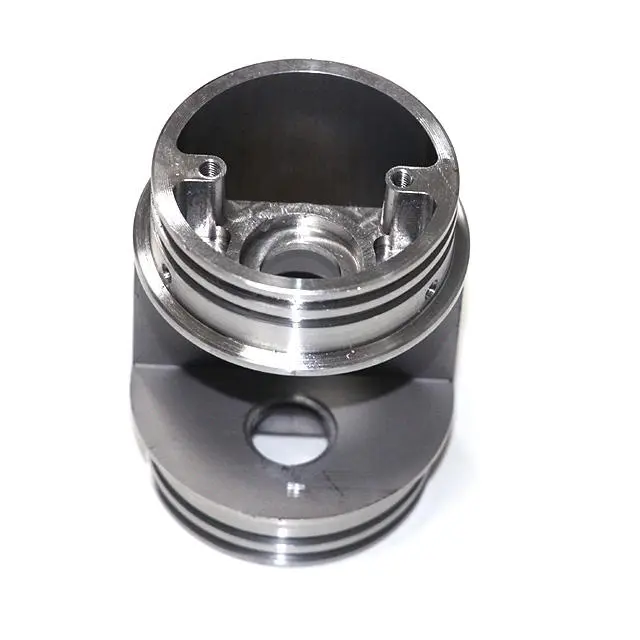
- +8615586668226
- [email protected]
- No. 30, Hongbang Industrial Park, Shenzhen
Flatness is a geometric tolerance that specifies how close a real surface must be to a perfect plane. It’s about the variation or deviation across an entire surface of a part. In simpler terms, flatness defines how “wobbly” or “uneven” a flat surface is allowed to be. Imagine a perfectly flat table; that’s the ideal. In the real world, however, no surface is perfectly flat, and that’s where flatness tolerance comes into play. It sets limits on how much deviation is acceptable.
Why is flatness so important? In numerous applications, like in aerospace, electronics, and medical devices, a part’s function depends on the flatness of the surface. For instance, if a sealing surface isn’t flat enough, it won’t seal properly, causing leaks. In high-speed electronics, where every micron counts, a non-flat surface could impair signal transmission. Flatness is a measure of quality, directly impacting the performance and reliability of the final product.
Flatness tolerance is a critical element in manufacturing, specifying the permissible deviation of a surface from a perfectly flat plane. Flatness is a tolerance that is used to define this acceptable amount of variation. This tolerance is not about size; instead, it’s about the shape or form of the surface. When we use flatness tolerance, we are specifying how much a real surface is permitted to vary within two parallel planes. It is a fundamental part of geometric dimensioning and tolerancing (GD&T), which is a standardized way of communicating engineering requirements.
The flatness tolerance value defines the separation between these two virtual planes within which the surface must lie. A larger value means that more variation is allowed, while a smaller value implies a more stringent requirement. When using gd&t, the flatness tolerance is clearly indicated on the engineering drawing, usually in a feature control frame. This feature control frame contains the flatness symbol and the tolerance value. Understanding flatness tolerance ensures that the metal part will perform as intended, avoiding issues like improper sealing, uneven contact, or performance degradation due to misaligned components. CNC Fabrication carefully considers flatness tolerance when machining parts, using precise methods to make sure every piece fits its functional requirement.
The flatness tolerance zone is the three-dimensional space defined by two parallel planes within which the entire surface of a part must reside. Imagine these two planes as parallel sheets of glass, with the actual part surface lying somewhere in between. The distance between these two planes is the flatness tolerance value shown in the flatness callout. This space represents the acceptable variation of the surface of the part from being perfectly flat.
For example, if the flatness tolerance is 0.005 inches, then the flatness tolerance zone would be a space 0.005 inches thick between those two virtual planes. Every single point on the actual surface of the part must lie within this zone to meet the drawing requirements. This tolerance zone isn’t centered on anything specific, but it describes how far out the actual part surface is allowed to deviate from being perfectly flat. The flatness tolerance zone is essential for quality control, providing a clear and measurable standard for verifying the flatness of the metal part. This also helps inspect the parts accurately.
To measure flatness, you need to determine the maximum variation across a surface. There are two methods to do this. One common method is to use a height gauge on a flat reference surface like a precision surface plate. By placing the part and then moving a height gauge across the surface of the part, you can observe the differences in height. Another method involves using cmms (coordinate measuring machines). CMMs are sophisticated devices that can perform detailed 3d measurement of the surface. These machines use probes to touch and record several points on the surface, then calculate the deviation from perfect flatness.
When using a height gauge, you measure the highest and lowest points of the surface must, and the difference is the flatness deviation. With a cmm, specialized software analyzes the data and generates a report displaying the surface flatness values. Choosing which method to use depends on required accuracy, with cmms providing more accuracy and detail than the traditional height gauge method. Regardless of the method, it’s important to ensure the flatness measurement is accurate and repeatable. This measurement is a critical part of the quality control process to verify the flatness requirement.
Although both straightness and flatness are both related to the form of a surface, they aren’t the same thing. Straightness refers to how well a line on a surface conforms to a perfect straight line, regardless of the surface’s overall orientation. In essence, straightness is a 2D concept, evaluated along a line, while flatness is a 3D concept, evaluated over an entire area. Think about a ruler. A perfectly straight ruler has high straightness. However, if that ruler is bent, it still has high straightness but reduced flatness, especially when used as a surface to lay something on.
When we talk about flatness, we’re not concerned about how straight any individual line is; we’re concerned about how well the entire surface conforms to a plane. A flat surface can have straight lines that are oriented differently, as long as the whole surface is within the tolerance zone. Therefore, a surface can have acceptable straightness without being flat, and vice versa. Understanding this difference is critical when selecting the appropriate geometric tolerance for your parts and when creating an engineering drawing.
Parallelism is a geometric tolerance that controls how parallel two flat surfaces or lines are to each other. It specifies how close to parallel the actual surfaces are to each other. While parallelism is different from flatness, they are often used in conjunction, especially when dealing with multiple flat surfaces. For instance, if you have a base plate where you need a surface to be both flat and parallel to the bottom of the plate, you would control both flatness and parallelism.
Think of two pieces of paper. If they are both flat and placed on top of each other, then you need to think about the flatness of each paper. To consider parallelism, you need to assess if one of the paper is tilted with respect to the other one. If two flat surfaces aren’t parallel, then you need to use parallelism to control the angle between them, and not the flatness. The relationship between flatness and parallelism is important when designing complex parts, since flatness deals with the quality of a single surface, while parallelism deals with the relationship between two surfaces. Measuring parallelism involves measuring the perpendicular distance between the two specified surfaces at different points along their length and width. If you were measuring the flatness of a surface after the part is mounted on another surface then you would be measuring parallelism and not flatness.
A datum is a reference surface, axis, or point from which measurements are taken when checking a component, it is the base against which other features are related. In the context of flatness control, a datum is often used as a reference for checking how flat another surface is. Think of it as the “zero point” in a measurement system. When a datum is used with a flatness callout, it is not defining the flatness itself, but the orientation of the part in relation to another surface. When a datum is used in a flatness control, there is a need to use a feature control frame.
For instance, if we have a part with a bottom surface defined as datum A, the flatness of a top flat surface may be specified in relation to datum A. This means the flatness isn’t just measured with respect to itself but with respect to the datum. The position of the measuring device will be related to the datum, and not only the part itself. This datum is critical for aligning and correctly inspecting the part to meet specified tolerances, providing a consistent and repeatable measurement. Datums ensure consistency in measurement across different production runs and different machines.
A flatness callout on an engineering drawing is a specific way to communicate the flatness tolerance requirement to the manufacturer. The flatness callout is contained within a feature control frame, which is a box containing all information needed to define the requirement. The feature control frame contains a flatness symbol, a diagonal line under a horizontal one, followed by the flatness tolerance value. Sometimes, especially if the flatness is referenced to a datum, then this reference to the datum will be added to the feature control frame.
For example, a flatness callout might appear as a rectangle containing the flatness symbol followed by a number like 0.005, which means the flatness tolerance value is 0.005 inches. This indicates that the actual part surface must lie within two parallel planes that are 0.005 inches apart. When a flatness callout appears on a drawing, it’s a clear instruction to the manufacturer that flatness is a tight tolerance that must be achieved within that tolerance. Understanding how to read and interpret the flatness callout is essential for producing parts that meet design requirements correctly. This flatness callout will help the manufacturer produce parts to the specified flatness.
Flatness plays an important role in quality control during the manufacturing process. It ensures that the surface must conform to specified tolerances, thus preventing issues in assembly, and operation of the products. During quality control, the flatness of a manufactured part is inspected using methods like height gauges or cmms. If the flatness does not meet the requirements, then it might need to be re-machined to the specified flatness, or rejected. This step ensures that the finished product will perform as intended, preventing unexpected failures due to dimensional inconsistencies.
The flatness control measures how much a surface must conform to a perfectly flat plane, which means it also impacts functionality of a part and reduces the chance of rejection. For example, in a gasket, the flatness ensures a tight seal, and in electronics, the flatness ensures a good contact between components. In the quality control process, understanding and applying the flatness specifications helps reduce costs associated with rework and prevents poor-quality products from reaching consumers. Flatness is a measure of quality that directly impacts the performance and reliability of products.
A tight tolerance in flatness control means that the allowable variation in the flatness of a surface is very small. This level of precision is often needed in high-performance applications, such as aerospace, medical, and electronics, where even the slightest deviation can lead to significant functional problems. For example, in semiconductor manufacturing, a nearly perfectly flat surface is required to allow accurate fabrication of microchips. Tighter tolerance requirements generally lead to more precise manufacturing techniques and higher quality output.
When a design calls for a tight tolerance, it signals that achieving the specified flatness is essential to the part’s function. For example, a surface for a precision bearing would need a very tight tolerance to ensure smooth operation. While a tighter tolerance usually results in higher production costs due to the need for more precise machines and more stringent inspection, the improved performance and reliability of the final products justify the increased expenditure. In other words, having the flatness correctly will ensure that the product operates correctly for a longer time.
Why Choose CNC Fabrication?
At CNC Fabrication, we understand the importance of flatness in precision engineering. We utilize state-of-the-art machines and metrology equipment to achieve even the most stringent flatness tolerance requirements. Our expert team ensures that every component we produce adheres to the highest standards of accuracy and quality, and is in accordance with asme standards. Whether your application demands a tight tolerance for aerospace components or consistent flatness for medical devices, you can count on us. We provide customized CNC solutions for on-demand manufacturing and rapid prototyping, helping you bring your ideas to life with accuracy and efficiency. From CNC Machining to Sheet Metal Fabrication we have the expertise to produce high quality parts. We’re more than a manufacturing plant; we’re your partner in ensuring your products achieve optimal performance. Our services extend from precision machining to surface finishing to get your product exactly right. Contact us today to discuss your project, and experience the CNC Fabrication difference.
FAQs
What is the flatness tolerance zone and why is it important?
How do I select the correct flatness tolerance for my part?
* The selection of the flatness tolerance depends on the requirements of the final product. Start with the functional requirements of the product, and how flat it needs to be to properly operate. Use the asme standard as the guide to properly call out the requirements.
What is the difference between flatness and parallelism?
What kind of equipment does CNC Fabrication use to measure flatness?
What is the significance of datums when controlling flatness?
Why does CNC Fabrication focus on tight tolerances?
Summary of Key Points
Ready to experience the precision of CNC Fabrication? Explore our services for CNC Machining, Fabrication Services, and CNC Solutions today! We also offer Rapid Prototyping and On Demand Manufacturing, and work with industries ranging from Aerospace to Automotive, so contact us today!
Get the latest trends and facts about CNC fabrication from our blog.
Shenzhen Runkey Precision Technology Co. Ltd, a subsidiary of the Tensun Group, is your trusted one-stop solution for custom manufacturing from prototyping to production.Transforming your idea into reality with digital manufacturing resources,streamlined processes, expert guidance,accelerated timelines, and uncompromising quality.
©2024. CNC Fabrication All Rights Reserved.