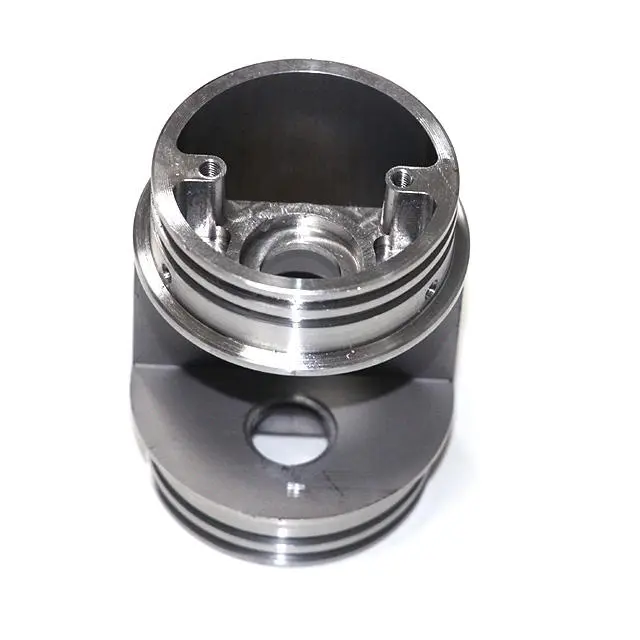
- +8615586668226
- [email protected]
- No. 30, Hongbang Industrial Park, Shenzhen
Formula:
[ \text{SFM} = \frac{\text{RPM} \times \pi \times \text{Tool Diameter (inches)}}{12} ]
Example:
Material | Recommended SFM Range |
---|---|
6061 Aluminum | 800–1000 |
Mild Steel | 80–100 |
Titanium | 50–100 |
Pro Tip: Use CNC Solutions software for real-time adjustments.
Fix It:
Tool | Use Case |
---|---|
HSMAdvisor | Optimizes SFM for complex alloys. |
G-Wizard | Tailors feeds/speeds for Robotics. |
Machinist Calculator | Handles quick conversions. |
Case Study: A Defense contractor reduced tool costs by 30% by adjusting SFM for titanium components.
How does SFM affect tool life?
Optimal SFM reduces heat, preventing premature wear.
Can I use the same SFM for all materials?
No—titanium demands lower SFM than aluminum.
What’s the ideal SFM for prototyping?
Use Rapid Prototyping guidelines to balance speed and precision.
Why does spindle RPM fluctuate with tool size?
Larger tools require lower RPM to maintain SFM.
Ready to Optimize Your Machining? Contact Us for tailored SFM solutions across Automotive, Electronics, and more!
Get the latest trends and facts about CNC fabrication from our blog.
Shenzhen Runkey Precision Technology Co. Ltd, a subsidiary of the Tensun Group, is your trusted one-stop solution for custom manufacturing from prototyping to production.Transforming your idea into reality with digital manufacturing resources,streamlined processes, expert guidance,accelerated timelines, and uncompromising quality.
©2024. CNC Fabrication All Rights Reserved.