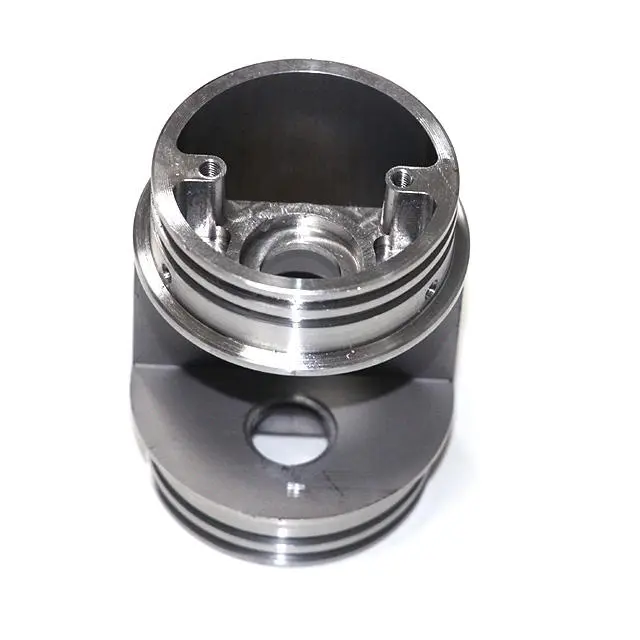
- +8615586668226
- [email protected]
- No. 30, Hongbang Industrial Park, Shenzhen
Brackets are unsung heroes in engineering, providing structural support and connectivity in applications like robotics, medical devices, and heavy equipment. They transform static structures into dynamic systems by:
Fun fact: Over 70% of industrial equipment failures originate from poorly designed support components like brackets.
Material choice impacts durability, weight, and cost. Below is a comparison of popular options:
Material | Strength | Weight | Corrosion Resistance | Cost | Best For |
---|---|---|---|---|---|
Stainless Steel | High | Heavy | Excellent | $$$ | Medical, Food Packaging |
Aluminum | Medium | Light | Good | $$ | Aerospace, Automotive |
Brass | Medium | Medium | Moderate | $$$$ | Decorative Applications |
Pro Tip: For high-stress environments like defense systems, consider combining materials. Learn more about material selection strategies.
Visual: Common bracket profiles and their load distribution patterns.
Case Study: A robotics firm reduced bracket failure rates by 40% using our 5-axis CNC machining for complex geometries.
“Over-engineering is the enemy of cost-efficiency. Simplicity often outperforms complexity in bracket design.” – Lead Engineer, CNC Fabrication
What’s the best material for outdoor brackets?
304 stainless steel offers optimal weather resistance for construction and energy applications.
Can you make custom-shaped brackets for unique prototypes?
Yes! Our rapid prototyping team specializes in one-off designs.
How thin can sheet metal brackets be?
We reliably work with materials as thin as 0.5 mm using precision machining.
Do you handle full assembly services?
Absolutely – explore our end-to-end assembly solutions.
Ready to transform your bracket designs? Contact our team for a free design review and quote today!
Get the latest trends and facts about CNC fabrication from our blog.
Shenzhen Runkey Precision Technology Co. Ltd, a subsidiary of the Tensun Group, is your trusted one-stop solution for custom manufacturing from prototyping to production.Transforming your idea into reality with digital manufacturing resources,streamlined processes, expert guidance,accelerated timelines, and uncompromising quality.
©2024. CNC Fabrication All Rights Reserved.