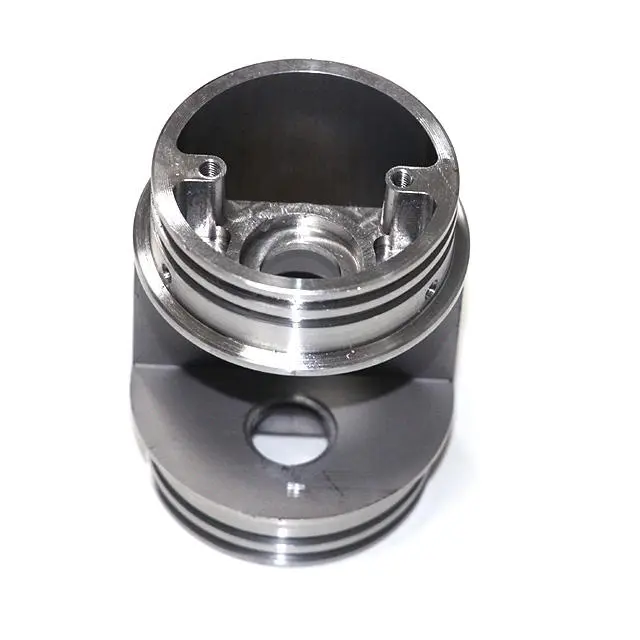
- +8615586668226
- [email protected]
- No. 30, Hongbang Industrial Park, Shenzhen
Grain direction and size directly affect the durability, flexibility, and manufacturing efficiency of sheet metal parts. By understanding these factors, engineers can design components that withstand stress, reduce waste, and align with industry standards.
Sheet metal fabrication transforms flat metal sheets into functional parts through cutting, bending, and assembly. Common applications include brackets, enclosures, and industrial equipment. Key processes include:
Alt: Visualizing grain direction in sheet metal fabrication processes
Metals consist of polycrystalline structures—tiny crystals (grains) bound together. During rolling, these grains elongate, creating a grain direction that impacts material behavior:
Grain Orientation | Strength | Common Applications |
---|---|---|
Longitudinal | High | Aerospace components |
Transverse | Moderate | Consumer electronics |
Bending sheet metal against the grain requires more force but reduces cracking risks. Key considerations:
Pro Tip: For projects like robotic arms or medical device housings, align bends perpendicular to the grain for optimal durability.
Smaller grains mean more grain boundaries, which block cracks and enhance strength. Factors affecting grain size:
Case Study: A defense contractor reduced part failures by 30% after optimizing grain size through precision annealing.
When cutting multiple parts from a single sheet, align all components to the same grain direction. This ensures:
Explore our sheet metal fabrication services for tailored nesting solutions.
Post-rolling treatments like annealing or normalizing adjust grain size:
Ideal for custom prototypes requiring precise tolerances.
A major automotive brand faced repeated bracket failures due to improper grain alignment. By redesigning parts to bend against the grain, they achieved:
At CNC Manufacturing Service, we combine advanced laser cutting and precision machining to optimize grain structure. Our process includes:
Request a free quote for projects requiring 5-axis machining or on-demand manufacturing.
Grain alignment impacts stress distribution. Parts bent with the grain may crack under cyclic loads, common in industrial equipment.
Yes! Processes like annealing refine grain structure post-production.
Uniform grain direction ensures predictable behavior during mass production, vital for consumer goods.
Indirectly. Smaller grains slow crack propagation, enhancing durability in harsh environments like energy sector applications.
Ready to optimize your next project? Explore our CNC solutions or contact us for a consultation!
Get the latest trends and facts about CNC fabrication from our blog.
Shenzhen Runkey Precision Technology Co. Ltd, a subsidiary of the Tensun Group, is your trusted one-stop solution for custom manufacturing from prototyping to production.Transforming your idea into reality with digital manufacturing resources,streamlined processes, expert guidance,accelerated timelines, and uncompromising quality.
©2024. CNC Fabrication All Rights Reserved.