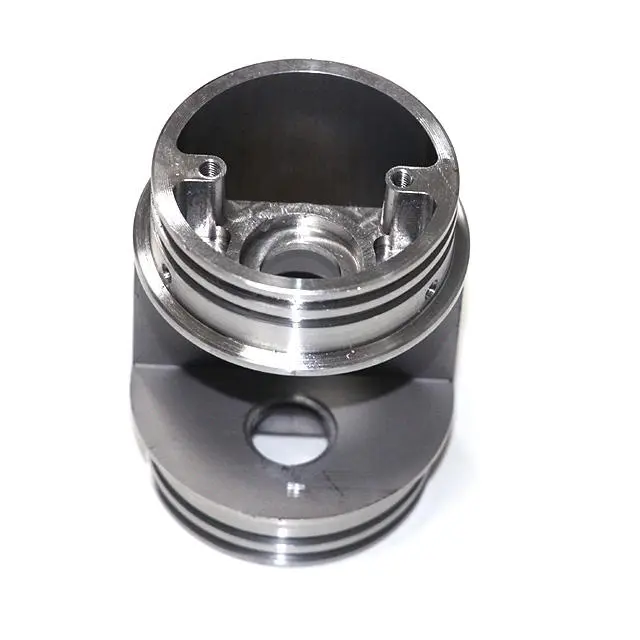
- +8615586668226
- [email protected]
- No. 30, Hongbang Industrial Park, Shenzhen
Welding aluminum isn’t as straightforward as welding steel, mainly due to the unique properties of the metal. One primary reason is the formation of aluminum oxide. This thin but tough layer forms almost instantly when aluminum is exposed to air. Aluminum oxide has a much higher melting point (around 3700°F or 2037°C) than aluminum itself (around 1220°F or 660°C). This means you can’t just melt the base metal; you also need to penetrate and break through this resistant oxide layer to achieve a good weld fusion. If not done correctly it can be a difficult to weld aluminum.
Another challenge is aluminum’s high thermal conductivity. It dissipates heat very rapidly, meaning that your weld puddle can cool down fast, which can lead to poor weld quality and weld penetration. This rapid heat transfer also makes it difficult to maintain a consistent weld puddle, and your welder may find it hard to achieve the desired weld penetration and weld bead profile. Unlike welding steel, the welding process for aluminum is more sensitive to changes in heat input and speed. Also, the rapid change in properties of the aluminum as it welds, makes it difficult to know if the weld is good.
Several welding processes can be used for aluminum, each with its advantages and disadvantages. The most common options include TIG welding (Gas Tungsten Arc Welding), MIG welding (Gas Metal Arc Welding), and stick welding (Shielded Metal Arc Welding), and even friction stir welding, but stick welding is often avoided for aluminum due to its limitations.
TIG welding, also known as tungsten inert gas welding, is favored for aluminum when high precision and clean welds are needed. It offers excellent control over the welding process, making it ideal for intricate designs and thin aluminum pieces. TIG welding uses a non-consumable tungsten electrode to produce the weld, which is why it’s so precise. MIG welding, on the other hand, uses a consumable electrode (the filler metal wire), which makes it faster and more suited for larger projects where speed is needed. It’s often referred to as the gas metal arc welding technique and can also be effectively used for welding aluminum. However, it might be hard to achieve as clean welds on aluminum compared to TIG welding. The choice depends on factors like the type of aluminum you are working with, the desired weld quality, and how fast you need to complete the job. TIG welding uses a tungsten and inert gas, normally argon or a mix of argon and helium to prevent oxidation.
TIG welding, or gas tungsten arc welding, is a very precise welding technique where a non-consumable tungsten electrode is used to generate the arc, and a separate filler rod is fed into the weld area, if required. The process uses a shielding gas, typically argon or helium, or a mix of the two, to protect the weld from contamination. Because the tungsten isn’t consumed, it provides a very stable arc, which in turn gives the welder great control over the weld puddle, heat input and weld penetration, making it a go-to process for high-quality aluminum welding.
TIG welding excels in scenarios where clean, aesthetically pleasing, and high-strength welds are paramount, as is the case in many manufacturing plants. This makes it perfect for applications like aerospace components, intricate automotive parts, and medical device fabrication where precision is crucial. The process is very effective on thin aluminum where heat control is essential, and the ability to fine-tune parameters such as amperage, travel speed, and filler addition allows the welder to manage the weld puddle and minimize distortion, which is a must when welding aluminum. Though it can be slower than other welding processes it is the best way to ensure quality welds on aluminum.
Aluminum’s high thermal conductivity presents a significant challenge to welders. Aluminum dissipates heat much faster than other metals, like steel. This means that your weld zone can cool down quickly which can make maintaining a proper weld puddle tricky. It’s similar to a kitchen pan that heats up very fast but also cools down quickly, making it more difficult to cook something evenly. You have to be very precise to get the proper weld fusion.
Because of this high thermal transfer, you have to use a higher initial amperage when you weld aluminum to get the weld puddle established faster. As a welder, you must adjust the heat input continuously to prevent underheating or overheating. The rapid heat transfer can cause a weld to freeze before the weld pool has spread enough to create the bond with the base material, so it’s crucial to keep a steady arc and heat input to ensure good weld penetration. Preheat the aluminum is often done to reduce the thermal conductivity and ensure a more even distribution of heat during the welding process.
Choosing the right filler metal is very important for successful aluminum welding. The filler needs to match the properties of the base material in terms of strength and composition, so the welds on aluminum are strong, resistant to cracking and are durable. Using the wrong filler can lead to weak or brittle welds prone to cracking and failure. When selecting a filler, pay attention to the aluminum alloys you’re joining.
For aluminum, most filler metals are also aluminum based and they may have additives that help with weld quality. For instance, filler metal containing silicon or magnesium is often used to improve weld flow, minimize hot cracking and increase strength. Additionally, remember that the filler metal also has to be suitable for the specific welding process you’re using – there are filler rods for TIG welding and aluminum wire for MIG welding. The selection of the right filler, directly affects the weld quality, and the mechanical properties of the final weld, so it is important to ensure you get the correct one for your aluminum welding projects. Proper feeding of the filler is important, whether you are using wire feeding on a MIG or manually feeding a filler rod on TIG.
Prior to welding, preparing aluminum properly is essential for a successful weld. The main aim is to remove the aluminum oxide layer, and any other contamination that can hinder proper weld fusion and weld penetration. Firstly, cleaning the aluminum surface using a wire brush, and solvent based degreaser is a must to remove any oil, dirt or other contaminants, especially near the weld zone.
Once the surface is clean, removing the oxide layer requires further attention. While brushing can remove some of the oxide, it can be beneficial to use a stainless steel brush just before welding, as aluminum can also reform it’s oxide layer very quickly. In some cases, chemical cleaning methods may also be used. Immediately after the cleaning process, proceed with your welding to avoid the formation of a new aluminum oxide layer. Preheating the aluminum can also improve weld penetration by reducing the aluminum’s high thermal conductivity and reducing the chance of any defects on the final weld.
Preventing weld defects is very important for ensuring the strength and integrity of the welds on aluminum. Contamination is one of the most frequent causes of weld issues, often originating from the base metal itself. When welding, aluminum reacts readily with oxygen, moisture and other elements forming aluminum oxide, which can lead to poor weld penetration, porosity, or cracking.
One essential step is using shielding gas that completely protects the weld pool from contaminants. Argon is often used, though mixing with helium can sometimes offer better weld penetration. The welder must also pay attention to the cleanliness of the filler metal, and the welding area, and making sure to remove all traces of dirt, grease, or other unwanted substances. Ensure you use clean welding equipment like nozzles, and that everything is stored properly. The welder also needs to keep the welding area properly ventilated to allow any fumes to move away. These best practices help achieve quality welds on aluminum and avoid weld contamination.
Various welding techniques are used when welding aluminum, with specific methods that work best for aluminum because of it’s properties. For TIG welding, techniques like a slightly tilted electrode and feeding the filler smoothly is a method used, and for MIG welding some welders may use a push-pull wire feeding system or a spool gun, which reduces the chance of tangling when feeding aluminum. Regardless of the method, it’s important to avoid weaving the welding gun too much when making a weld, as this may create uneven heat input and lead to poor weld penetration, which can create weak spots. It’s best to move in smooth, linear lines across the piece of aluminum when welding.
When you weld aluminum, you must monitor the weld puddle carefully. The weld puddle needs to be kept consistent and you must maintain the right travel speed. If the travel speed is too fast, you might not get good weld penetration, or the weld might become too thin and will have issues holding together. If the travel speed is too slow, the aluminum can overheat and cause distortion or even burn through, so it’s important to have the correct travel speed to ensure a successful weld.
Achieving high weld quality and good weld penetration when welding aluminum requires meticulous control over all aspects of the welding process. We must ensure that we have cleaned the base metal correctly, that we have correctly chosen the right filler metal, and selected the right welding technique. The right welding equipment is also important as well. With TIG welding, having a good quality tig welding power unit, with the correct size tungsten electrode and the right shielding gas are also important factors. With MIG welding, the welder must have the correct settings on the wire feeding unit. The type of aluminum, its thickness and its use will determine which method is best.
The welder has to maintain the right heat input to get the ideal weld puddle. It is important to monitor and adjust heat, travel speed, and filler addition continuously. A consistent weld puddle is needed and good heat control is important for achieving the desired weld penetration. When welding aluminum, it can also be beneficial to preheat the base material to help achieve proper weld penetration. It’s important to look at the weld, and you must observe the weld closely as the weld puddle forms, this way you can make sure that the weld is good and strong.
As a CNC fabrication service, we provide a full service for clients who need to weld aluminum, and also offer services in cutting, bending and other services. Our experience and advanced manufacturing facilities allow us to create precision components that may need to be joined together by welding. The fact that we provide these services means we can offer a turnkey solution for our clients which helps reduce lead times and reduce overall cost.
Our team can help with design and pre-fabrication tasks. We can take care of all preparatory processes, like laser cutting, CNC machining, bending, etc. We can machine parts using aluminum alloys, then carefully weld them to give you a final high quality and finished part. Our team of expert welders use TIG and MIG to produce high quality welds, and our advanced welding equipment helps us to create good looking welds. For aluminum fabrication, we are experts in producing the highest standards of products and we are able to advise you on best practices to deliver the best product for your needs. We’re skilled in producing products for aerospace, automotive, medical device and many other types of industries.
What is the most difficult part of welding aluminum?
The most difficult aspect of welding aluminum is its high thermal conductivity and the presence of the aluminum oxide layer. These properties require skilled techniques and careful control to achieve strong and clean welds.
Can you weld aluminum with a standard stick welding machine?
While it’s possible to use stick welding (shielded metal arc welding) on aluminum, it’s not recommended for most applications. The process is hard to control on aluminum, which makes it unsuitable for any precision work. For aluminum, TIG welding or MIG welding are the better choices.
Do I need special welding equipment to weld aluminum?
Yes, you need specific welding equipment to weld aluminum effectively. For TIG welding, you need a TIG welder with alternating current (AC) capability, a tungsten electrode, and argon or helium shielding gas. For MIG welding, you’ll need a MIG machine with wire feeding system, aluminum wire, and the right shielding gas.
How do I know I have a good weld on aluminum?
A good weld on aluminum will have a consistent and smooth weld bead with good weld penetration and no signs of porosity or cracking. The weld should also be free from any weld contamination. Experienced welders can often identify the quality of a weld by looking at the appearance and hearing how the weld is being made.
Is TIG welding always better than MIG welding for aluminum?
Not always, it depends on the specific job. TIG welding is best for precision and clean welds, especially on thinner aluminum or when working on a intricate piece of aluminum. MIG welding is more efficient for thicker materials and where welding needs to be performed faster. Each method has it’s advantages, so you must choose the method that works best for your specific application.
How can I get help with my aluminum welding project?
Our CNC fabrication service can help, we have expert welders and we can also machine and fabricate the parts, giving you a full turn key solution. You can contact us to discuss your requirements, and we can offer you the best advice to help you achieve your desired goals.
Summary of Key Points
If you are looking for a company that can do weld aluminum projects, we can help. Contact us today to see how we can help with your project. We can help you with all your aluminum fabrication needs.
Our Machining Services could be the answer for all your CNC machining needs. Our Fabrication Services are designed to meet even the most challenging projects. We can provide you with CNC Solutions to help with your manufacturing needs. Our expertise in Precision Machining sets us apart in the industry. If you are looking for expertise in Sheet Metal Fabrication, look no further. We offer a full service from start to finish, and are experts in On Demand Manufacturing.
Get the latest trends and facts about CNC fabrication from our blog.
Shenzhen Runkey Precision Technology Co. Ltd, a subsidiary of the Tensun Group, is your trusted one-stop solution for custom manufacturing from prototyping to production.Transforming your idea into reality with digital manufacturing resources,streamlined processes, expert guidance,accelerated timelines, and uncompromising quality.
©2024. CNC Fabrication All Rights Reserved.