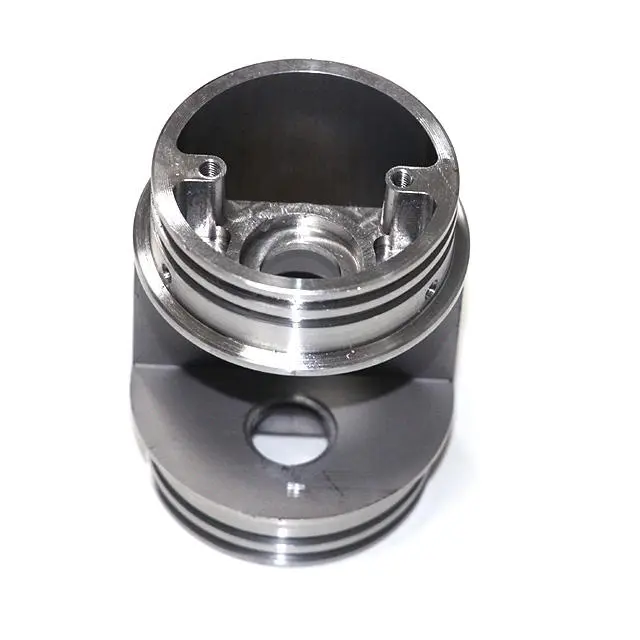
- +8615586668226
- [email protected]
- No. 30, Hongbang Industrial Park, Shenzhen
A lathe is a versatile machine tool that rotates a workpiece to perform various operations, primarily turning. Imagine a potter’s wheel, but instead of clay, it’s metal, plastic, or wood. The workpiece is secured and spun, while a cutting tool is advanced to remove material, shaping the piece into the desired form. This is an essential process in manufacturing, used across various sectors, including aerospace, automotive, and even in making intricate parts for medical devices. Lathe operations are fundamental in creating cylindrical shapes, threading, and other complex geometries, and are vital to modern manufacturing processes.
From simple bushings to intricate engine components, the lathe forms the base of a huge amount of parts for industrial equipment, consumer products, and much more. The precision that these lathe machines can offer is unparalleled, making it essential for creating components that require a high level of accuracy. Through precise control of the cutting tool, a lathe can transform raw materials into highly precise and useful components, ready for assembly and use in final products.
Without cutting tools, a lathe is just a spinning machine. It’s the cutting tool that shapes the material, removing unwanted parts to create the intended product. These tools are used to cut, groove, and form materials with incredible accuracy, ensuring the final product meets strict design specifications. The effectiveness of a turning operation largely depends on the quality and type of cutting tool being used, which is why choosing the right cutting tool is paramount. The cutting tools used in lathes are designed with specific materials and geometries, each tailored for different types of cuts and materials.
The cutting tool’s job isn’t easy; it must endure intense forces, high temperatures, and constant abrasion. A worn or inappropriate tool can lead to poor finish, incorrect dimensions, or even tool breakage, causing costly downtime. Therefore, careful selection and maintenance of lathe cutting tools are crucial for efficient and accurate manufacturing. Also remember cutting tool has to withstand cutting forces and high temperatures. It’s not just about removing material; it’s about doing it effectively and with precision.
There isn’t just one type of lathe; various types are designed for specific tasks. A bench lathe is smaller and suitable for lighter tasks and is perfect for smaller workshops, while an engine lathe is larger and more versatile, suitable for a wider range of machining operations. Then, you have CNC lathe machines, which are automated, enabling highly accurate and complex parts to be produced, and are perfect for repetitive tasks in high-volume production. Each of these types of lathe offers unique benefits depending on the size of the project, complexity and volume needed.
Understanding the different types of lathe is key to choosing the right equipment for your needs. Each type is designed for different levels of precision, size and automation. For example, a CNC lathe, which is a type of lathe, uses computer numerical control to automate the turning process, ensuring higher repeatability and precision, which is crucial in manufacturing products for medical devices, aerospace or any application that needs high reliability. We can help you with CNC turning needs.
A lathe cutting tool may seem simple, but it’s a complex structure designed to perform specific cutting actions. There is a shank which is the part of the tool held in place by the machine. The tool face is the top surface where chips slide away as the tool cuts into the material. The main cutting edge is the part of the tool that directly engages with the material, removing the waste. The nose radius is the tip, which defines the shape of the cut. The rake angle helps the tool slide more easily through the material, affecting the quality and speed of the cut, while the relief angle provides clearance to prevent friction.
Understanding these components of a lathe cutting helps you choose the correct lathe tool for the task. Each component affects the performance and quality of the cut. The cutting edge is particularly crucial; its shape and sharpness directly impact the cutting operation. A properly designed tool optimizes material removal, reduces heat buildup, and creates a smoother finish. For example, carbide tools often have different rake angles compared to high-speed steel tools, each being better suited to different types of cutting.
The world of lathe tools is vast, each with a specific purpose. Facing tools, for instance, are designed to create flat surfaces perpendicular to the lathe’s axis. Turning tools reduce the diameter of a material. Parting tools, also know as cut-off tools, are used to separate a finished part from the rest of the material. Grooving tools create grooves or channels, and are often used for creating recesses or reliefs in a component. Thread cutting tools are used for creating threads on materials and are essential for making screws and bolts. Knurling tools create a patterned, textured surface for better grip. Forming tools are used to cut specific shapes.
Each of these lathe tool types allows different lathe operations and each tool type has its own geometries and applications. The choice of tool depends on the desired outcome. For example, if you’re aiming to create a perfect thread, you need thread cutting tools. If you are simply making something with a circular profile, you may only require turning tools. The right cutting tool can make all the difference between a mediocre result and a perfect one. Tools are also suitable for different materials, and some are designed to remove large amounts of material, while others focus on precision finishing.
Choosing the right cutting tool is critical for project success. Consider the material you’re machining; different materials require different tools. High-speed steel tools are versatile and cost-effective, suitable for most common metals, while carbide tools, are harder and better for machining tougher materials, and are often used for high cutting speeds and feed. Also, take into account the desired surface finish. For a rough cut to remove large amounts of material, use roughing tools, while for a smooth, precise finish use finishing tools. Also, don’t forget the type of operation being performed; facing, turning, threading, each will require different types of cutting tools.
Also, the cutting speed, feed rate, and depth of cut greatly influence the tool choice. Higher speeds and deeper cuts may require more robust tools like carbide tools. The cutting tool should be able to withstand the forces generated during machining without breaking or deforming. The cutting edge quality is also key, as a dull cutting edge can cause poor surface finish and increased cutting force. When making your choice the right tool, remember to choose a material that is suitable to the material you will cut and operation you will perform. When you choose the right tool, you not only ensure better output, but you can save time and money by avoiding machine downtime and damaged parts.
When performing lathe operations, you will most often need to perform two types of turning: roughing and finishing. Rough turning tools are designed to quickly remove large amounts of material from the workpiece. They are generally more robust and have a greater depth of cut capability. The goal is not precision, but speed. These tools have a more aggressive cutting edge that helps remove material quickly without much regard for surface finish. On the other hand, finish turning tools are designed for the final pass, focusing on achieving a high degree of precision and a smooth surface finish. They generally have a smaller depth of cut and create less material waste.
While rough turning tools focus on speed and volume, finish turning tools emphasize precision and surface quality. Finish turning tools use a sharper cutting edge, are designed for less aggressive cuts, and create a much smoother surface finish. These tools are used for the final cut, ensuring a high-quality product. Knowing which tool to use and when can improve both your efficiency and final product, and this is often a key difference in results. If you start with a poor surface finish because you are using a rough turning tool for a finishing task, you will see the quality suffer.
CNC lathes, or Computer Numerical Control lathes, introduce a new level of precision and automation. These machines rely on computer programs to control the cutting operation. CNC turning often requires cutting tools designed for higher precision and repeatability. These tools are designed to perform consistently over long production runs without requiring constant adjustments, this is a big benefit when it comes to efficiency. For CNC lathes, consistency is key, therefore tools that maintain their edge longer are needed. Also, tool holders and mounting systems need to be very precise.
The automation of CNC lathes allows for more complex cuts and shapes, which requires cutting tools of higher accuracy. The use of CNC lathes also allows you to use multiple cutting edges at a time, and many of the latest lathe machine designs use tooling that allows multiple cutting tool to machine the same workpiece, for both speed and precision. Carbide tools, with their wear resistance and capability for high cutting speeds, are often the go-to choice for CNC lathe operations. The precision and repeatability of a CNC lathe mean the difference between success and failure.
Carbide tools are popular for their hardness and durability, but it’s essential to choose the right one for your lathe work. Carbide tools are usually composed of a carbide material with some other type of hard metal that is designed to withstand high heat and friction. They are also great for high cutting speeds and feeds. The quality of carbide tools can vary, and you should select a tool that matches the material being worked with. For example, tools designed for steel may not be as effective for aluminium or other materials. Consider the coating of the tool as this can reduce friction and extend the life of the cutting edge.
Also, consider the geometry of the cutting edge for your carbide tools, and if it is designed for roughing or finishing. The rake angle, chip breaker design, and cutting edge shape affect the efficiency and quality of the cut. Carbide tools may be more expensive than high-speed steel tools, but their long life and higher cutting speeds can make them more economical in the long run, and the higher quality often ensures less downtime. They are extremely useful for high cutting speeds and feed rates, and are often the choice of many manufacturers needing highly precise components. Choosing the right one is the key to success.
When it comes to lathe operations, there are many common tools that you can expect to find in most workshops. Turning tools, perhaps the most fundamental, are used for reducing the diameter of a workpiece. Facing tools help in creating flat surfaces on the end of the piece. Parting tools or cut-off tools separate a finished piece from the stock. Grooving tools are crucial for creating channels, or grooves, which are useful for creating recesses or reliefs. These common lathe cutting tools are the basis for most operations performed on a lathe.
Also, thread cutting tools, both single-point and multi-point, are very important for creating threads on materials. If you need to put a grip on a component, the knurling tool is the way to go. Boring tools enlarge existing holes, and are vital in any lathe operations. Having a selection of these tools used can handle a wide range of lathe operations and are essential for both simple and more complex projects. These tools must be chosen based on material, cutting speed and intended cut type.
What is the best type of cutting tool for aluminum?
Carbide tools with a high positive rake angle are often recommended because they provide a clean cut without adhering to the aluminum, which is vital for high cutting speeds.
How do I know when my cutting tool is dull?
A dull cutting tool will typically produce a poor surface finish, require more force to cut, and generate excessive heat. Check for a change in surface finish, and the formation of burs.
Can carbide tools be sharpened?
Yes, but it’s often more cost-effective to replace them, especially if they are inserts. If you do resharpen, only use a professional sharpening service.
What’s the difference between single-point and multi-point thread cutting tools?
Single-point tools cut one thread at a time, while multi-point tools cut multiple threads simultaneously for faster threading, and are often used for cnc turning and cnc lathe operations.
How does the cutting speed affect the life of the cutting tool?
Excessive cutting speeds can lead to increased heat, friction, and accelerated wear, reducing the tool life. Use the right cutting speeds for the material you are working with.
What is the role of cutting fluids in lathe operations?
Cutting fluids provide lubrication, reduce heat, and help clear chips. They extend tool life and improve surface finish.
We at cnc fabrication service offer high quality manufacturing, and with our experience you can be assured of the quality of every single product. We use a wide range of equipment such as CNC turning, CNC milling, and more. We offer a wide range of services, including sheet metal fabrication, laser cutting and more. Contact us today to discover how we can turn your ideas into reality. For a better understanding of different applications, explore our services in aerospace, automotive, medical devices, and electronics, each requiring precision and the right cutting tool.
Get the latest trends and facts about CNC fabrication from our blog.
Shenzhen Runkey Precision Technology Co. Ltd, a subsidiary of the Tensun Group, is your trusted one-stop solution for custom manufacturing from prototyping to production.Transforming your idea into reality with digital manufacturing resources,streamlined processes, expert guidance,accelerated timelines, and uncompromising quality.
©2024. CNC Fabrication All Rights Reserved.