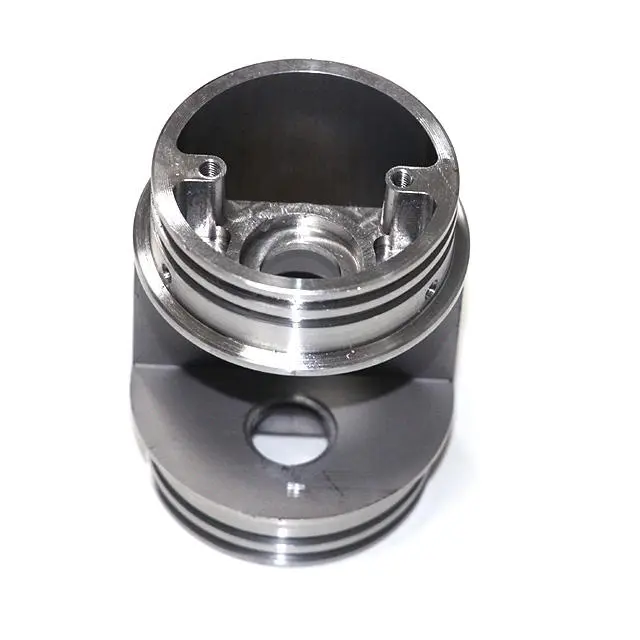
- +8615586668226
- [email protected]
- No. 30, Hongbang Industrial Park, Shenzhen
A reamer is a rotary cutting tool used in metalworking to enlarge and finish a previously drilled hole to a precise diameter and smooth surface finish. Unlike drill bits, which create initial holes, reamers refine existing holes, ensuring accuracy and consistency. As a representative of a CNC fabrication service manufacturing plant, I can attest that reamers are indispensable in our operations, particularly when producing components for industries like aerospace, automotive, and medical devices, where precision is paramount.
Reamers come in various types, including chucking reamers, hand reamers, and specialized designs for specific applications. The choice of reamer depends on factors such as the material being machined, the desired hole size, and the required surface finish. Our plant utilizes CNC machining centers equipped with advanced tool holders to ensure the precise control needed for reaming operations. We often rely on carbide reamers for their superior hardness and wear resistance, especially when working with tough materials like hardened steel.
Selecting the right tool is crucial for successful reaming. Reamer type selection hinges on the specific requirements of your project. Chucking reamers are designed for use in machines like lathes and milling machines, providing stability and accuracy. They are ideal for high-volume production and offer consistent performance. In contrast, hand reamers are used manually and are suitable for low-volume work or when a machine tool is unavailable.
Another critical consideration is the reamer material. High-speed steel reamers are a cost-effective option for softer materials, while solid carbide reamers are preferred for harder materials due to their durability. For demanding applications, such as those encountered in the medical devices industry, we often use carbide reamers to ensure longevity and precision. A good rule of thumb is to match the reamer material’s hardness to the workpiece material for best results.
Chucking reamers and hand reamers are both designed for reaming, but they differ significantly in their application and operation. Chucking reamers are machine-operated, often used in conjunction with a spot drill and center drill to ensure precise alignment. They are secured in a toolholder and rotated by the machine’s spindle, providing precise control over the reaming process. We frequently use chucking reamers in our CNC machines to achieve tight tolerances and excellent surface finishes in our products.
Hand reamers, on the other hand, are manually operated using a tap wrench. They are typically used for enlarging holes by a small amount or for finishing a hole to a very precise size. Hand reaming is often preferred for delicate or one-off tasks. While hand reamers offer flexibility, they require skill and experience to achieve consistent results. In our plant, we primarily rely on machine reaming for its efficiency and precision, but hand reamers are still valuable for specific applications.
Choosing the correct drill size is crucial for a successful reaming operation. The drill should be slightly smaller than the desired final hole size to allow the reamer to remove the correct amount of material. A general guideline is to leave between 0.005″ and 0.015″ of stock for the reamer to remove, depending on the reamer diameter and the material being machined.
Drill Size (in) | Reamer Size (in) | Material to be Removed (in) |
---|---|---|
0.492 | 0.500 | 0.008 |
0.738 | 0.750 | 0.012 |
0.984 | 1.000 | 0.016 |
Using an undersized drill can result in an oversized hole or reamer breakage, while using an oversized drill may not leave enough material for the reamer to cut effectively, leading to a poor surface finish. Our machinists meticulously calculate the appropriate drill size based on the specific reamer and workpiece material to ensure optimal results. A common practice in our plant is to use drill bits that are slightly smaller than the nominal size of the reamer and then gradually work up to the final size.
Proper speed and feed are essential for achieving the desired hole size and finish while maximizing tool life. The optimal cutting speed for reaming depends on the material being machined and the reamer material. Generally, reaming speeds are lower than drilling speeds. For example, when working with steel, a cutting speed of 30-50 SFM (surface feet per minute) is often recommended for high-speed steel reamers, while carbide reamers can handle higher speeds.
The feed rate in reaming is typically expressed in inches per revolution (IPR). A good starting point for the feed rate is around 0.001″ to 0.003″ IPR per flute. However, the optimal feed for your application may vary. It’s crucial to consult the reamer manufacturer’s recommendations and adjust the speed and feed based on the specific conditions of your machining operation.
Taper is a crucial factor in reamer design and performance. Many reamers have a slight taper at the cutting end to aid in starting the reaming process and to help center the reamer in the hole. Morse taper reamers, for example, are commonly used for creating tapered holes in machine spindles and tool holders. These reamers are ideal for applications that require secure and precise alignment.
When selecting a taper reamer, it’s essential to match the taper angle with the required taper of the hole. Using the right tool for the job ensures that the reamer seats correctly in the hole and produces the desired taper. In our operations, we often use specialized taper reamers for creating precision tapered holes in components for industries like industrial equipment and tooling.
Flutes are the grooves that run along the length of the reamer. They serve two primary functions: allowing chips to escape from the cutting area and providing a pathway for coolant to reach the cutting edges. The number and design of the flutes can significantly impact reaming efficiency.
Straight flute reamers are a common choice for general-purpose reaming. They are effective in a wide range of materials and are relatively easy to grind and maintain. Spiral flute reamers, on the other hand, have flutes that twist around the body of the reamer. This design helps to pull chips out of the hole, making them particularly useful for reaming deep or blind holes.
Coolant plays a vital role in the reaming process, serving several critical functions. First, it helps to reduce heat generated during cutting, preventing thermal damage to the workpiece and the reamer. Second, coolant lubricates the cutting edges, reducing friction and wear, which in turn extends tool life. Finally, coolant helps to flush away chips, preventing them from clogging the flutes and ensuring a smooth surface finish.
In our plant, we use a variety of coolants, including cutting oil and water-soluble fluids, depending on the material being machined and the specific requirements of the reaming operation. For example, when reaming aluminum, we often use a light cutting oil to prevent chip welding and ensure a high-quality finish. When reaming steel, we may use a water-based coolant with high lubricity to minimize heat and wear. Using the right type of coolant or cutting oil can significantly improve the reaming process, leading to better hole size and finish and longer tool life.
Maximizing tool life is crucial for maintaining efficiency and reducing costs in any machining operation. Several factors can affect the tool life of a reamer, including the material being machined, the reamer material, the cutting speed and feed, and the use of coolant.
One key to extending tool life is to select the right tool for the job. Using a reamer made from a material that is appropriate for the workpiece material can significantly reduce wear. For example, carbide reamers are an excellent choice for machining hard materials like stainless steel or titanium, as they offer superior hardness and wear resistance compared to high-speed steel reamers.
Another important factor is maintaining proper cutting speed and feed. Operating the reamer within the recommended parameters helps to minimize stress on the cutting edges, reducing the risk of tool breakage or premature wear. Additionally, using the correct coolant and ensuring it reaches the cutting zone effectively can significantly extend tool life.
While reaming is a relatively straightforward machining operation, several challenges can arise, especially when working with difficult materials or demanding tolerances. One common issue is oversized holes, which can result from using an incorrect drill size, excessive feed rate, or a worn reamer. To avoid this, it’s crucial to carefully select the drill size and reamer size, maintain proper speed and feed, and regularly inspect the reamer for wear.
Another challenge is poor surface finish, which can be caused by various factors, including incorrect speed and feed, inadequate coolant, or chip buildup in the flutes. Adjusting the cutting parameters, ensuring proper coolant flow, and using a reamer with the appropriate flute design can help to improve surface finish. For example, using spiral flute reamers can help prevent chip buildup, especially when reaming deep or blind holes. In our experience, using spiral flute reamers in conjunction with through-tool coolant delivery can significantly improve chip evacuation and surface finish.
What is the primary purpose of a reamer?
The primary purpose of a reamer is to enlarge and finish a previously drilled hole to a precise diameter and achieve a smooth surface finish.
How do I choose between a chucking reamer and a hand reamer?
Choose a chucking reamer for machine operations where precision and consistency are crucial. Opt for a hand reamer for manual operations, low-volume work, or when a machine tool is unavailable.
What is the recommended stock allowance for reaming?
A general guideline is to leave between 0.005″ and 0.015″ of material for the reamer to remove, depending on the reamer diameter and the material being machined.
Why is coolant important in reaming?
Coolant reduces heat, lubricates the cutting edges, extends tool life, and helps flush away chips, ensuring a smooth surface finish.
How can I extend the tool life of a reamer?
Extend tool life by selecting the right tool for the material, maintaining proper cutting speed and feed, using the correct coolant, and regularly inspecting the reamer for wear.
What are the common causes of poor surface finish in reaming?
Poor surface finish can result from incorrect speed and feed, inadequate coolant, chip buildup in the flutes, or using a worn reamer.
Here are the most important takeaways from this comprehensive guide:
By mastering the art of reaming and partnering with an experienced CNC fabrication service provider like us, you can achieve exceptional results in your manufacturing projects, ensuring precision, quality, and efficiency every step of the way. Contact us today to learn more about how we can help you with your next project.
Get the latest trends and facts about CNC fabrication from our blog.
Shenzhen Runkey Precision Technology Co. Ltd, a subsidiary of the Tensun Group, is your trusted one-stop solution for custom manufacturing from prototyping to production.Transforming your idea into reality with digital manufacturing resources,streamlined processes, expert guidance,accelerated timelines, and uncompromising quality.
©2024. CNC Fabrication All Rights Reserved.