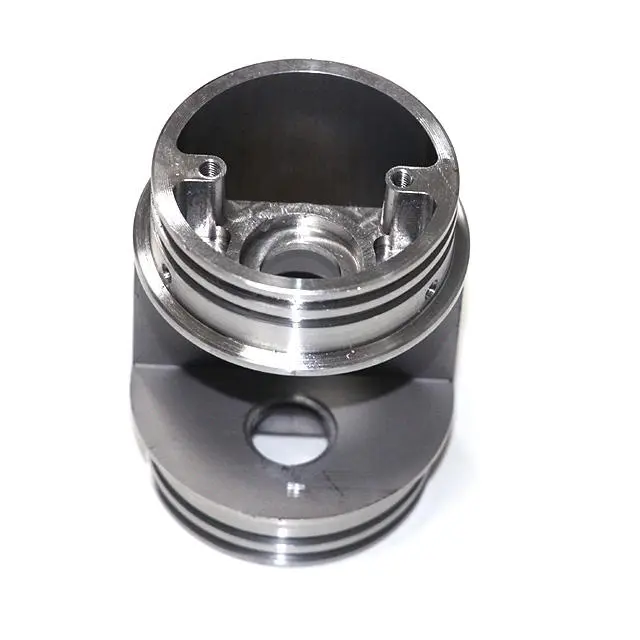
- +8615586668226
- [email protected]
- No. 30, Hongbang Industrial Park, Shenzhen
In manufacturing, a datum isn’t just a piece of data; it’s a precise reference point, surface, or axis. Imagine trying to assemble a complex puzzle without knowing where to start – that’s what manufacturing would be like without datums. A datum is the fundamental basis from which all measurements and tolerances are derived. It’s the foundation for creating accurate and repeatable parts. It is a theoretical exact plane, axis or point location that GD&T uses to accurately specify the geometric control for a part. Think of it as the starting line in a race – everything else is measured in relation to it. When we talk about a datum, we’re talking about a fundamental reference for the manufacturing process.
Without a well-defined datum, it would be incredibly difficult to ensure that parts fit together correctly and that they meet the design specifications. The datum serves as a reference to position and orient the part for machining and inspection. This precise starting point enables manufacturers to consistently produce components that adhere to the required tolerances. Datums are used to define the relationships between different features on a part. Datums are important because they provide a shared understanding between designers, manufacturers, and inspectors. In essence, the datum is the cornerstone of precision manufacturing.
The datum symbol is an important element in engineering drawings, and it’s critical for clear communication between designers and manufacturers. It’s a triangle with a letter inside or a filled triangle if the datum references a datum feature of size such as a diameter or width. This symbol identifies a specific datum and is placed on the drawing to clearly indicate which feature is being used as the reference. The triangle symbol can be placed on the surface of a feature, on an extension line from a feature, or on the axis of a geometric feature. It is always accompanied by a letter which indicates the specific datum, such as datum A, datum B, or datum C. When we see a datum symbol, it tells us that this particular feature is not just any part of the design – it’s a critical reference point.
The datum symbol is a vital component of GD&T, and it helps to minimize ambiguity in part design. The letter inside the triangle is critical, as each letter refers to a different datum. We might use datum A as the primary datum, which means it is our most important reference point. Then, datum B might be our secondary datum which controls some additional degrees of freedom. The datum symbol indicates that the datum is to be used as the basis for measuring and controlling the location and orientation of other features. Understanding the datum symbol and its associated letter is the first step in comprehending how to properly dimension a part using GD&T. Without clear datum symbols, precision manufacturing would be greatly hampered. It indicates that the datum provides the reference for other features.
A datum reference frame is a three-dimensional coordinate system, essential for accurately defining the location and orientation of a part. A datum reference frame consists of three mutually perpendicular datum planes. This system is used to precisely define how a part sits in space. Think of it like giving the location of a point in space – you need a coordinate system to reference it against. The datum reference frame establishes the fundamental basis for all geometric measurements on a part, much like the grid lines on a map help you pinpoint the location of a city. This system allows all features to be precisely measured with respect to the origin of the datum reference frame.
The datum reference frame is typically created from three datums, known as the primary datum, secondary datum, and tertiary datum, establishing the orientation of the part in 3D space. The primary datum establishes the first reference plane, the secondary datum establishes a datum plane that is perpendicular to the primary datum, and the tertiary datum establishes another datum plane that is perpendicular to the primary datum and secondary datum. This system ensures that the part is accurately positioned and measured, removing ambiguity and ensuring consistent manufacturing results. This complete datum reference frame locks the part in all six degrees of freedom, providing a robust and repeatable reference system for all manufacturing and inspection activities. The ability to establish a datum this way is fundamental for achieving precise measurements. It’s the foundation upon which the entire geometric structure of a part is based.
While a datum is a theoretical concept, a datum feature is a physical feature of the part itself that is used to establish a datum. In simple terms, the datum feature is the real-world object that we use as our starting point when we machine and measure parts. A datum feature could be a flat surface, a hole, a cylinder, or any other identifiable aspect of the part. It’s the tangible item we interact with to set up our machine tools and measuring instruments. The datum feature is a crucial link between the theoretical world of design and the practical world of manufacturing. A datum feature is always a geometric feature.
The main distinction is that the datum itself is an ideal datum plane, an axis, or a point that is theoretically perfect, while the datum feature is a physical imperfection. We use the datum feature to simulate the theoretical datum. So, we’re not directly using the datum but rather the datum feature, which might have some imperfections. To ensure a reliable datum, we need to select datum features that are stable, easily accessible, and that can be accurately measured. The goal is to use the datum feature to simulate the ideal datum as closely as possible. The datum feature would often be the surface on which a part rests, or the hole into which a pin is inserted, serving as the starting point to use for further measurements.
Tolerance is the allowable variation in a dimension or feature of a part, and it’s absolutely critical when working with datums. No manufacturing process is perfect, so there will always be variations in the actual dimensions of a part. Tolerance specifies the permissible range within which these variations can occur without causing problems. When you’re dimensioning a part using datums, it’s not enough to say “this surface is flat.” You have to specify a tolerance to indicate just how flat that surface needs to be. Tolerance dictates how precise our measurements need to be, how precise we need to machine features, and how close features need to be relative to each other and the specified datums.
Tolerance is necessary because it ensures that parts will fit together and function correctly even with minor deviations from the perfect design specifications. Without tolerance, parts wouldn’t be interchangeable. Tolerance helps to specify the allowed variability between the datum feature and other features. The tolerance zone is a key aspect of GD&T. Tolerance is also tightly linked to the datum reference frame. The tolerance zones for a part are specified relative to the datum reference frame. The position of features is defined in relation to a specific datum, and the tolerance is used to show how far those features can deviate and still be acceptable. This guarantees that all manufactured parts will have consistent functionality and interoperability.
Datum targets are specific points, lines, or areas on a part that are used to establish a datum when a full surface isn’t suitable. Imagine a part with an uneven surface – it wouldn’t be practical to use the entire surface as a datum. In such cases, datum targets provide a way to pinpoint specific areas that can be used as a more reliable reference. Datum targets are indicated on a drawing with a target symbol. A datum target could be used when the surface is too small or too flexible to be used as a reliable datum. We’re not using a full feature; instead, we are using a few specific points, lines or small areas.
When a large part has a complex or irregular shape, datum targets are the perfect solution for establishing a datum because they allow the use of specific areas as references. Datum targets are essential when the overall surface might be uneven. These points or areas, rather than the whole feature, become the reference point. We can establish a stable and accurate datum plane by using multiple datum targets. By using datum targets, we can control the part in a repeatable way. Datum targets are often used in conjunction with the datum symbol and a datum letter to indicate which datum they are associated with. It is essential to understand that the datum target itself is a feature location for locating the datum on a feature, the actual datum is the contact plane using that location.
There are different types of datums, each suited to different types of features and situations. The most common types of datum are datum planes, datum axes, and datum center plane. A datum plane is a flat, theoretical surface and is often used as the primary reference. Datum axes are used for cylindrical features, using the center of the cylinder as a datum. A datum center plane is used when the datum is the mid plane of the feature. Types of datum vary based on how the part is structured and the geometric controls needed.
The primary datum is usually a flat surface that the part rests on or that it is located against. The secondary datum and tertiary datum are often used to control rotation and orientation. A single part can have multiple datums, each serving a specific purpose. When using cylindrical parts as datums we typically use the axis as a datum. Understanding the different types of datums enables us to choose the most appropriate reference points for our designs. The type of datum selected will be dependent on the geometric features of the part and the function of that part. Each datum plays a crucial role in ensuring that the part is manufactured to the intended design.
The feature control frame is a rectangular box that contains all the information about the geometric requirements of a feature. It is a cornerstone of GD&T, and it defines the tolerance and datum requirements for a particular feature. The feature control frame is typically made up of different sections, including a geometric characteristic symbol, a tolerance value, and references to datums. The feature control frame specifies the allowed deviation of a feature. This deviation is always measured relative to one or more datums. The feature control frame ensures that the geometric requirements of a part are clearly and unambiguously defined.
The feature control frame includes the datum references. After the tolerance value, you will usually see references to one, two, or three datums, often denoted as datum A, datum B, and datum C. The order in which the datums are listed in the feature control frame is significant: the first datum is the primary datum, the second is the secondary datum, and the third is the tertiary datum. The feature control frame connects the design intent of the part to the actual manufacturing requirements. When we see a feature control frame we can understand the tolerance of the feature, and how it is tied to the datum reference frame of the part.
The feature control specifies the geometric characteristics of a feature, such as its flatness, circularity, or perpendicularity, and is directly linked to datums. The feature control section in the drawing, often seen in a feature control frame, defines how a feature must be controlled relative to the specified datums. The feature control tells us which geometric characteristic is being controlled, what its tolerance is, and the datums it is related to. For example, we might use a flatness control that specifies how flat a surface must be relative to a certain datum.
The feature control ensures that all dimensions and tolerances are tied back to the datums on the part. The datums provide the reference system that defines how features should be measured and controlled. The feature control specifies the allowed deviation of the part relative to the datums. Without the datum, the feature control cannot function correctly, because there wouldn’t be a stable reference point. The combination of the feature control and the datums gives us clear instructions on what is acceptable and what is not. When we select the datums and apply the feature control, we create a manufacturing plan that ensures part consistency and accuracy. The feature control also ensures the part will function within the tolerance and geometric parameters that are required.
The use of geometric principles with datums is at the heart of GD&T. Geometric principles are used to control the shape, orientation, and location of features on a part. When combined with datums, these geometric controls ensure that the parts are manufactured to the highest standards. Geometric principles like flatness, straightness, circularity, perpendicularity, and parallelism are all measured relative to one or more datums. Using geometric controls relative to datums makes it possible to control the critical features of a part.
Geometric principles and datums work together to specify the precise relationships between features and their tolerance limits. For example, a perpendicularity control will always specify one or more datums to be perpendicular too. The geometric controls ensure that all features are controlled in relation to the datum reference frame. This combination allows for parts to be produced with more precision than dimensional measurements alone, and provides consistent results between batches. By combining geometric and datum information, we define not only the dimensions of a part but the shape, orientation, and location of features in a clear, understandable, and measurable way.
Establishing a datum plane is a critical step in the manufacturing process. This plane is the basis for all subsequent measurements and machining operations. To establish a datum plane, you need to first identify a suitable datum feature on the part. A datum feature should be stable, accessible, and repeatable. Once a datum feature has been selected, we can define a datum plane. The real physical surface we will use as our datum is the datum feature on the real part.
The process of establishing a datum plane often involves contacting the datum feature at several points. This might be done with a coordinate measuring machine (CMM) or another type of precision measurement device. The datum plane that is used to establish the reference is typically a theoretical ideal, however the datum feature itself is a real part that will have some amount of deviation from the theoretical surface. It is vital to ensure that the chosen datum feature and the datum plane are stable and consistent across all manufactured parts. The ability to establish a datum is a key skill for a manufacturing and quality control professional. A datum plane used to establish the reference makes all future measurements consistent and accurate.
A datum system is essential in manufacturing to provide a clear and consistent method for referencing all measurements and features on a part. Without a well-defined datum system, each person involved in the design and manufacturing process might interpret the design differently. This would make it nearly impossible to produce parts that meet the design specifications. A datum system provides a shared understanding of how a part is to be positioned and measured. The datum system forms the backbone for all geometric controls.
The primary purpose of a datum system is to provide a reliable reference system. A datum system ensures that all features and all tolerances are measured and controlled consistently, improving the quality of all parts. By utilizing a datum system, we can minimize variation and increase the interchangeability of parts. Having a datum system increases manufacturing efficiency, reduces waste, and improves the fit and function of parts. A datum system allows all designers, engineers, and machinists to work using the same set of references and guidelines.
Datums are represented on an engineering drawing using specific symbols and conventions. The datum symbol, a triangle, is the key identifier. This datum symbol is placed on or near the datum feature that is being used as a reference. Along with this datum symbol, a letter is added inside or nearby to distinguish each different datum. The datums are identified with a datum symbol, such as datum A, datum B, and datum C. This lettering is then used to reference that datum in the feature control frame.
When we see a datum symbol on an engineering drawing it is usually accompanied by a note indicating that the datum is to be used to reference other features. The engineering drawing typically illustrates the order of importance of datums, usually with the primary datum indicated first, followed by the secondary datum, and then the tertiary datum. Datums can be explicitly stated in the notes on a drawing or in the feature control frame. An engineering drawing uses these symbols and conventions to create a shared understanding of the part among all stakeholders. These symbols used to establish a datum, are standardized and understood by everyone who is in the business of producing manufactured parts.
A datum feature simulator is a physical device or representation that simulates the theoretical datum based on a real part. It’s crucial to understand that a physical part is never perfect, but a datum is theoretical. The datum feature simulator is the tool that we use to try to match the theoretical ideal to the real part. It enables us to use the datum in a way that is consistent with the GD&T standards. A datum feature simulator is not always required, but it is necessary when measuring or inspecting a part with high tolerance requirements.
The datum feature simulator provides a reliable and repeatable way of establishing a datum. The datum simulator can be an accurate machine table or a gauge with a precision surface. We may use a gauge block as a datum simulator to ensure that the datum is the same every time we measure the part. A datum feature simulator is sometimes used to define a planar datum. A datum feature simulator helps to ensure that all measurements are consistent and accurate. It’s the bridge between theory and the physical world and essential for accurate manufacturing.
The point of contact is critical when establishing a datum. The point of contact refers to the exact location where the part touches the datum feature simulator or the measurement device. Using multiple points of contact to establish a datum ensures the part is stable and positioned correctly. When establishing a planar datum, at least three datums are required to completely fix the part in three dimensional space. We call this three datums method of fixing the part in space as the 3-2-1 method. The first point of contact establishes a single plane. The next two points of contact then fix the second axis. The last three points then establish the datum around the third axis.
The point of contact is essential because even small variations in the point of contact can have a large impact on measurements. When measuring and inspecting parts, the point of contact should be exactly the same every time. Consistency in the point of contact is crucial for maintaining accuracy in manufacturing. When using a datum, the point of contact will affect the reliability of your measurements. Careful consideration of the point of contact is one of the most important elements in achieving good manufacturing results. The point of contact ensures that the part is precisely oriented relative to the specified datum.
To use the datum effectively, we must first understand the design intent. The datum is never to be used as a dimension, instead, the datum is to use datums to help specify the tolerance of other features. First select the datums, and then use these datums to control the geometric properties of the parts. Datums should be selected on the basis of how they relate to the other features of the part. The datums are planes and axes that control geometric tolerances of the part and should be selected accordingly.
We must place the datum on the part in a way that makes sense for the part’s function. Datums provide the reference for other features and allow us to measure the part accurately. When using a datum, think about what the primary datum should be and which features are most important for the function of the part. Then, select the secondary and tertiary datums to help define the part with more precision. Proper use of the datum involves understanding not just where the datum is but also how it is used to control the overall quality of a part. To use the datum correctly requires a thorough understanding of GD&T principles. Datums are used as a reference to datum, and they should not be used as dimensions.
Datums are defined in the feature control using the feature control frame. The feature control frame specifies which datums control the geometric properties of the feature. The datum letter inside a triangle symbol specifies a particular datum, and this letter is used in the feature control frame. The feature control frame shows which datums are used to establish a location for the feature. The order in which the datums are listed in the feature control frame is significant. The primary datum is the first datum listed in the feature control frame.
In the feature control, a datum is identified by a letter, and the datum is usually the geometric feature that is used as the reference. The feature control specifies how that feature must be controlled relative to the datums specified. Typically, the feature control frame will specify the tolerance for the feature, and then will show a reference to datum A, or datums A and B, or datums A, B, and C. The location of each of these datums is shown on the drawing with the datum triangle and a letter. The datums specified in the feature control frame allow us to control how features relate to the part as a whole. Datums in the feature control are essential for a part to be precisely manufactured.
A datum is a theoretical concept, like a perfect plane, axis, or point, whereas a datum feature is the physical feature of a part that is used to represent that theoretical datum.
Multiple datums are needed to fully constrain a part, controlling all six degrees of freedom and providing a stable and repeatable reference system. We need a primary datum, a secondary datum, and a tertiary datum.
Select the primary datum based on the functional requirements of the part. The primary datum is typically a surface that is stable and can be easily located. Datums should be selected on the basis of how they are related to the other features on the part.
The datum symbol, which is a triangle, is used to identify a specific datum on an engineering drawing and to reference that datum in the feature control frame. It is usually accompanied by a datum letter.
Yes, a cylinder can be used as a datum. In this case, the datum is typically the datum axis of the cylinder, and it is the reference used to measure and control other features of the part.
The feature control frame is used to specify the geometric requirements for a feature, including its tolerance, and how it relates to one or more datums. It clearly communicates the design requirements to the manufacturer.
Understanding and applying datums effectively is essential for precision manufacturing. This comprehensive guide should provide you with a strong foundation for working with datums and GD&T. By mastering these concepts, you can achieve higher levels of accuracy and quality in your manufacturing processes.
We at CNC Fabrication are here to help you in your precision manufacturing needs. Contact us today for a quote!
Here are some other pages on our site that may be of interest: CNC Machining, Fabrication Services, Rapid Prototyping, Aerospace, Automotive and Medical Devices
Get the latest trends and facts about CNC fabrication from our blog.
Shenzhen Runkey Precision Technology Co. Ltd, a subsidiary of the Tensun Group, is your trusted one-stop solution for custom manufacturing from prototyping to production.Transforming your idea into reality with digital manufacturing resources,streamlined processes, expert guidance,accelerated timelines, and uncompromising quality.
©2024. CNC Fabrication All Rights Reserved.