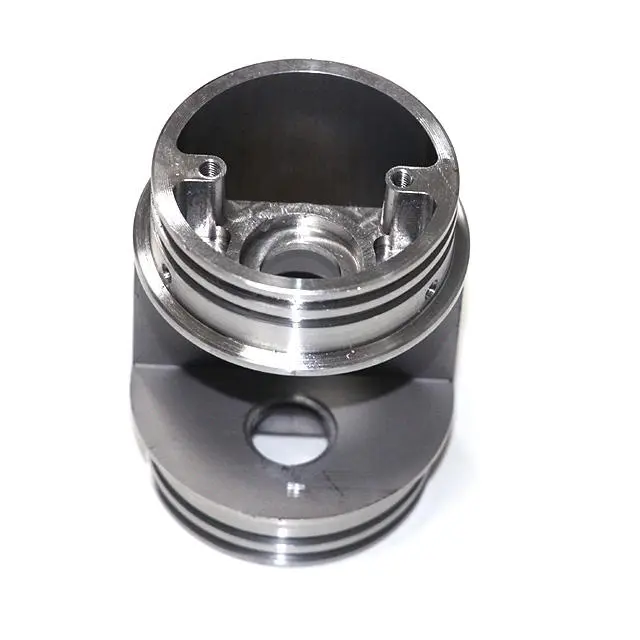
- +8615586668226
- [email protected]
- No. 30, Hongbang Industrial Park, Shenzhen
An end mill is a type of cutting tool used in milling processes. It is designed with cutting teeth on the end and sides, allowing it to cut both axially and laterally, making it incredibly versatile. Unlike drill bits that primarily cut downward, end mills can cut sideways, making them ideal for creating complex shapes, profiles, and slots. They are fundamental to CNC milling operations. Think of an end mill as a sculptor’s chisel for metal; it is this tool’s job to shape and refine materials into precise components.
As a cnc fabrication serive we use end mills every day. They are the heart of our manufacturing process, allowing us to craft everything from intricate medical device components to robust parts for heavy equipment. The precision and versatility of the end mill make it indispensable in modern manufacturing, especially for creating parts with complex geometries. The cutting edge of each end mill is designed with unique geometric properties for material removal. The choice of end mill will impact the machining process used.
Selecting the right end mill for a project is a critical decision that directly impacts the quality and efficiency of the machining process. Factors like the material you’re working with, the depth of cut required, the type of milling operation, and desired surface finish all play a crucial role. For example, softer materials like aluminum might work best with single-flute end mills or two-flute cutters which help with chip evacuation, while harder materials like steel require more robust carbide end mills with multiple flutes. You need to consider the material, application, and required finish before making a choice of end mill.
In our experience as a manufacturing plant, we have learned that starting with an understanding of your project’s specific requirements is key. Do you need to make a deep cut? You might consider a roughing end mill. Do you need to make a smooth, shiny finish? You should look into a finishing end mill. We also must consider the diameter of the end mill, as this effects the speed and feed rates. The correct end mill will have a significant impact on the efficiency of your machining process and quality of the finished product.
The world of end mills is vast, encompassing many designs each tailored for specific tasks. Here’s a rundown of some common types of end mills:
As a facility specializing in cnc milling, we use these different types of end mills to meet all of our clients’ needs. Whether you need smooth contours, precise pockets, or robust removal of material, the correct type of end mill is critical for a successful operation.
The number of flutes on an end mill plays a significant role in determining its performance in different milling scenarios. Flute end mills have cutting edges; more flutes allow for a faster material removal rate while fewer flutes can be used for softer materials where chip removal is a concern. Single-flute end mills are great for soft materials like aluminum. They excel at chip evacuation because they have a lot of space for chips to flow away from the cutting edge.
For instance, in our work as a production facility, we frequently use carbide end mills with four or more flutes for cnc milling steel components, achieving a fine surface finish with high precision. Understanding the number of flutes will help you to improve your milling operations and make the right end mill selection. The right choice of end mill is important for efficient material removal.
Milling is a versatile machining process used to shape metal and other materials. It involves using a rotating mill cutter to remove material from a workpiece, typically mounted on a milling machine. Here are some of the common milling processes:
At our facility, we use these milling processes for various milling applications. From aerospace components to automotive parts, end mills are essential to shaping the raw material into highly precise and functional parts. Each milling operation will use one of these processes. The end milling process is critical for creating detailed parts.
End mills offer numerous advantages over other cutting tools when used in a milling machine. They are designed for both lateral and axial cutting, unlike drill bits or boring tools, which only cut in one direction. Here are a few key benefits:
As a cnc fabrication serive we have seen how efficient end mills are. They are our go to cutting tool. The use of end mills in milling machines is essential for producing high-quality parts across various industries from medical device to the automotive. The right mill will determine the quality of cut.
The end milling process is a method of machining that involves using a rotating end mill to remove material from a workpiece. In the end milling process, the end mill is mounted in the milling machine and rotated at high speeds. The workpiece is fed into the rotating end mill, which then cuts away the material. The depth, direction, and speed at which this operation occurs depends on the material being cut and the desired shape. Here are some ways that end milling is utilized:
End mills are used in a variety of milling applications. For example, when working in automotive, we use end milling to create precise engine components. In aerospace, we make specialized molds and dies for composite materials with our cnc milling equipment using end mills. The process is versatile and necessary for many of the products we use today. End milling is an essential machining process for all different kinds of industries.
A face mill is a cutting tool primarily used for creating large, flat surfaces on a workpiece. Unlike an end mill that cuts on its end and sides, a face mill primarily cuts on its face – the flat surface at the end of the tool. This makes them ideal for quickly removing material from large surface areas, resulting in a smooth, flat finish. However, face mills are not as versatile as end mills.
Here’s a brief comparison:
While both face mills and end mills are used in milling processes, their applications differ. A face mill is great for bulk material removal while an end mill is better suited for more detailed and intricate machining operations. Depending on the job the right mill should be used.
Selecting the correct end mill for your project requires a careful evaluation of both the material to be machined and the specific application. For example, when working with aluminum you should use high helix flutes that promote easy chip removal. Here are some guidelines:
As a cnc fabrication serive we always consider the material and the end-use of the project when deciding which end mill to use. Whether it is a complex component for a medical device or a simple bracket for industrial equipment, choosing the right end mill will lead to better parts, a more efficient machining process and a quality finish. This is the right end mill for your job!
Yes, absolutely! There are many specialized end mills designed for unique or complex machining tasks. These tools are engineered to address the specific challenges in different milling applications. Here are some examples of specialized end mills:
Our manufacturing processes often require specialized end mills to complete a complex operation with precision. These specialized end mills are essential to achieve complex designs with high accuracy and efficiency, and this helps improve the end product for all industries. A variety of end mills exist to meet the many unique requirements of today’s manufacturing.
What is the difference between an end mill and a drill bit?
An end mill is designed for cutting both axially and laterally, making it ideal for creating complex shapes and slots. A drill bit is primarily used for creating holes by cutting only axially.
What is the best material for end mills?
Carbide end mills are the most popular option due to their strength and wear resistance. Other materials include high-speed steel (HSS) and cobalt. Carbide end mills provide long life and excellent performance.
How can I prolong the life of my end mills?
Use proper feeds and speeds, avoid excessive heat, keep them sharp by resharpening as needed, and always properly store them when not in use to avoid damage. Proper machine maintenance can extend the life of your end mills.
What is the difference between roughing and finishing end mills?
Roughing end mills are designed for quickly removing material with a high material removal rate, while finishing end mills are for achieving smooth and precise surface finishes.
What is profile milling?
Profile milling is the process of using an end mill to cut the outer shape of a part along a predetermined path.
How does coolant affect the milling process?
Coolant helps reduce heat, lubricate the cutting edge, and flush away chips. It improves the life of the cutter and enhances the surface finish of the part.
To find out how we can assist you with your cnc milling needs, visit our pages on Machining Services, CNC Machining, CNC Milling and Fabrication Services. We also offer Rapid Prototyping services and work with a wide variety of Materials. Contact us today to discuss your next project!
Get the latest trends and facts about CNC fabrication from our blog.
Shenzhen Runkey Precision Technology Co. Ltd, a subsidiary of the Tensun Group, is your trusted one-stop solution for custom manufacturing from prototyping to production.Transforming your idea into reality with digital manufacturing resources,streamlined processes, expert guidance,accelerated timelines, and uncompromising quality.
©2024. CNC Fabrication All Rights Reserved.