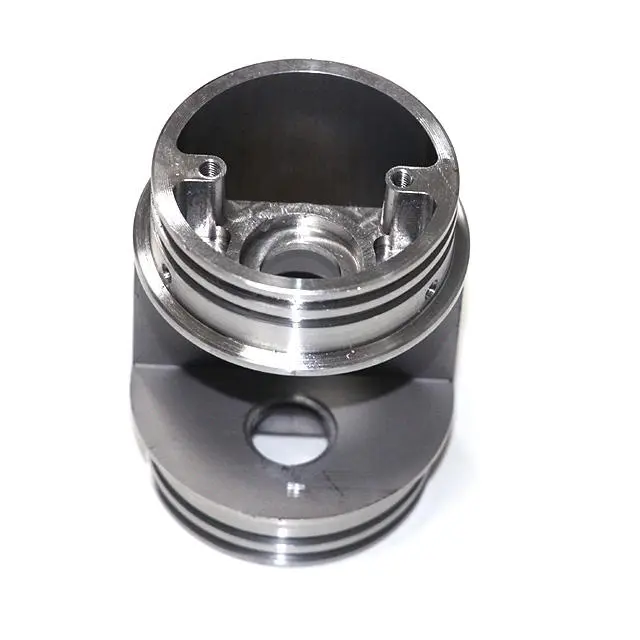
- +8615586668226
- [email protected]
- No. 30, Hongbang Industrial Park, Shenzhen
Tolerance in engineering is the permissible limit or limits of variation in a physical dimension. It’s a critical aspect of manufacturing that defines the allowable deviation from a nominal value. Tolerance ensures that parts fit together, operate correctly, and meet the functional requirements of the design. In precision engineering, where every micron counts, understanding and applying the correct tolerance is paramount.
Tolerances are not just numbers on a drawing; they represent a balance between precision, cost, and functionality. Specifying tight tolerances can increase manufacturing costs, while overly loose tolerances may compromise the product’s performance. As a leading provider of CNC fabrication services, we understand the delicate balance required to achieve optimal tolerance for each project. We have a deep understanding of many industries, and we specialize in solutions tailored to the unique needs of industries such as Aerospace, Automotive, and Medical Devices.
Unilateral tolerance is a type of tolerance where the variation from the nominal dimension is permitted in only one direction, either positive or negative. For example, if a shaft’s nominal diameter is 25mm with a unilateral tolerance of +0.05mm, the allowable diameter can range from 25mm to 25.05mm. If the tolerance were -0.02mm, the shaft could range from 24.98mm to 25mm.
This type of tolerance is often used when a dimension can only deviate in one way without causing functional issues. Consider a hole that must be at least a certain size to ensure clearance for a fastener. In such cases, specifying a unilateral tolerance ensures the hole is never too small. Our expertise in CNC machining allows us to achieve precise unilateral tolerances, ensuring components meet strict requirements.
Bilateral tolerance allows variations in both directions from the nominal value. For instance, a dimension of 25mm ±0.03mm means the allowable size can range from 24.97mm to 25.03mm. The deviation can be equal or unequal, such as +0.04mm/-0.02mm, which is known as an unequal bilateral tolerance or unequally disposed tolerance.
Bilateral tolerances are common when a dimension can fluctuate around a central value without affecting the part’s function. A classic example is the length of a non-critical component where slight variations in either direction are acceptable. Our state-of-the-art CNC facilities are equipped to handle complex bilateral tolerancing requirements with unmatched accuracy.
The primary difference between unilateral and bilateral tolerances lies in the direction of the allowable variation. Unilateral tolerance restricts variation to one direction, while bilateral tolerance allows variations in both the positive and negative directions. Understanding these differences is crucial for selecting the appropriate tolerance type for a specific application.
Choosing between unilateral or bilateral depends on the functional needs of the part. For example, if two mating parts must fit with a specific clearance, unilateral tolerances might be used to ensure they always assemble correctly. Bilateral tolerances, on the other hand, are suitable when some play is acceptable or even desirable.
The tolerance zone defines the upper and lower limits within which a feature’s actual size or location must fall. For unilateral tolerance, the tolerance zone extends from the nominal value in one direction. For bilateral tolerance, it extends in both directions.
Visualizing the tolerance zone is essential for understanding how tolerances affect a part’s geometry. Imagine a target; the bullseye represents the nominal value, and the rings around it represent the tolerance zone. A larger tolerance zone means a bigger target, making the part easier and less expensive to manufacture. We leverage advanced CNC machining techniques to ensure all features stay within tolerance, no matter how complex the part.
Geometric dimensioning and tolerancing (GD&T) is a system for defining and communicating engineering tolerances. It uses a symbolic language on engineering drawings and computer-generated three-dimensional solid models that explicitly describe nominal geometry and its allowable variation.
GD&T goes beyond basic dimensioning and tolerancing by defining the function of a part and how its features relate to each other. It includes controls for form, orientation, location, and profile, ensuring a comprehensive definition of the part’s geometric requirements. Our team is proficient in GD&T basics, ensuring clear communication and precise execution of your designs, for more info check our CNC solutions.
Selecting the appropriate tolerance type involves a deep understanding of the part’s function, manufacturing process, and cost considerations. Ask yourself: Does the feature need to fit with another part? Is there a minimum or maximum size requirement? What level of variation is acceptable?
Consider the manufacturing implications as well. Tight tolerances often require more precise, and therefore more expensive, manufacturing methods. Unilateral tolerances might be necessary for features that must fit together with a specific clearance or interference. Bilateral tolerances can offer more flexibility and potentially lower production costs when slight variations are permissible. Our fabrication services cover a wide range of capabilities.
Feature | Tolerance Type | Reasoning |
Shaft Diameter | Unilateral (+0.02mm) | Ensures minimum clearance with a mating hole |
Hole Diameter | Unilateral (-0.03mm) | Guarantees a maximum interference fit with a shaft |
Slot Width | Bilateral (±0.05mm) | Allows for slight variations in width without affecting the insertion of a mating part |
Plate Thickness | Bilateral (+0.1mm/-0.05mm) | Permits more variation on the positive side while maintaining a minimum thickness |
CNC (Computer Numerical Control) machining plays a vital role in achieving and managing precise tolerances. CNC machines, guided by computer programs, can produce parts with high accuracy and repeatability, making them ideal for tight tolerance applications.
CNC machining offers several advantages in tolerance management:
Precision: CNC machines can achieve tolerances as tight as ±0.001 inches (0.025 mm) or even better, depending on the machine and the material.
Consistency: Once a CNC program is optimized, it can produce identical parts with minimal variation, ensuring consistent tolerance control.
Flexibility: CNC machining can handle a wide range of materials and complex geometries, making it suitable for various tolerance requirements.
Efficiency: CNC machines can operate 24/7, reducing lead times and improving overall production efficiency.
Quality control is the backbone of tolerance management. It involves a series of inspections and measurements to ensure that manufactured parts meet the specified tolerances. Effective quality control processes are essential for maintaining consistency and preventing costly errors.
Quality control in tolerance management includes:
Dimensional Inspection: Using precise measuring tools like micrometers, calipers, and coordinate measuring machines (CMMs) to verify that part dimensions are within tolerance.
Process Monitoring: Continuously tracking the manufacturing process to identify potential deviations early on.
Statistical Process Control (SPC): Applying statistical methods to monitor and control the manufacturing process, ensuring it remains stable and capable of meeting tolerance requirements.
We offer precision machining service for all customers.
Applying tolerances in engineering design requires a systematic approach. Start by identifying the critical features and their functional requirements. Then, determine the appropriate tolerance values based on factors like fit, function, and manufacturing capabilities.
Here’s a step-by-step guide to applying tolerances:
Define Nominal Dimensions: Establish the ideal size of each feature.
Identify Functional Requirements: Determine how each feature interacts with other parts.
Select Tolerance Type: Choose between unilateral and bilateral based on functional needs.
Determine Tolerance Values: Assign specific values based on industry standards, material properties, and manufacturing capabilities.
Document Tolerances: Clearly indicate tolerances on engineering drawings using proper notation.
Remember, tolerance specification is not just about assigning numbers; it’s about understanding the implications of those numbers on the final product. Our machining services are designed to ensure that all designs are executed with the utmost attention to detail.
What is the main difference between unilateral and bilateral tolerances?
The main difference is that unilateral tolerance allows variation in only one direction from the nominal value, while bilateral tolerance permits variations in both positive and negative directions.
Why are tolerances important in engineering?
Tolerances are crucial because they define the allowable limits of variation in a dimension, ensuring that parts fit together correctly, function as intended, and meet the design requirements.
How does CNC machining help in achieving tight tolerances?
CNC machining uses computer-controlled machines to produce parts with high precision and repeatability, making it ideal for achieving tight tolerances that might be difficult or impossible to reach with manual methods.
What is a tolerance zone?
A tolerance zone is the range between the upper and lower limits of a dimension, within which the actual size or location of a feature must fall to be considered acceptable.
What is the purpose of geometric dimensioning and tolerancing (GD&T)?
GD&T provides a standardized way to define and communicate engineering tolerances, specifying not only the size and location of features but also their form, orientation, and relationship to other features.
How do I determine the appropriate tolerance value for a specific feature?
Determining the right tolerance value involves considering the feature’s function, how it interacts with other parts, the manufacturing process being used, material properties, and industry standards.
Tolerance is a fundamental concept in engineering and manufacturing, defining the allowable variation in a physical dimension.
Unilateral tolerance permits variation in only one direction, while bilateral tolerance allows variations in both positive and negative directions.
Understanding the differences between unilateral and bilateral tolerances is crucial for selecting the right tolerance type for a specific application.
The tolerance zone defines the range within which a feature’s actual size or location must fall.
Geometric dimensioning and tolerancing (GD&T) provides a comprehensive system for defining and communicating engineering tolerances.
CNC machining plays a vital role in achieving and managing precise tolerances, offering precision, consistency, flexibility, and efficiency.
Quality control is essential for ensuring that manufactured parts meet the specified tolerances.
Applying tolerances in engineering design requires a systematic approach, considering functional requirements, manufacturing capabilities, and cost implications.
Get the latest trends and facts about CNC fabrication from our blog.
Shenzhen Runkey Precision Technology Co. Ltd, a subsidiary of the Tensun Group, is your trusted one-stop solution for custom manufacturing from prototyping to production.Transforming your idea into reality with digital manufacturing resources,streamlined processes, expert guidance,accelerated timelines, and uncompromising quality.
©2024. CNC Fabrication All Rights Reserved.