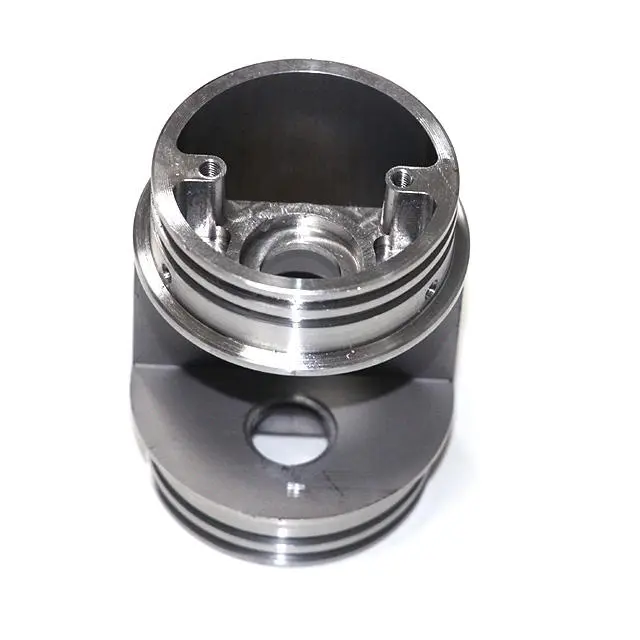
- +8615586668226
- [email protected]
- No. 30, Hongbang Industrial Park, Shenzhen
MIG welding, short for Metal Inert Gas welding, is a process that uses a continuous wire electrode fed through a mig welder. An electric arc forms between the electrode and the metal workpiece, welding the materials together.
MIG welding’s ease of use and speed make it a favorite choice for many industries, including automotive and construction.
TIG welding, or Tungsten Inert Gas welding, involves a non-consumable tungsten electrode to produce the weld. The tig welder uses a separate filler material that is manually fed into the weld pool.
TIG welding is known for its precision and the high quality of the welds it produces, making it a preferred choice in demanding welding applications.
Choosing between MIG and TIG welding requires understanding their fundamental differences:
Aspect | MIG Welding | TIG Welding |
---|---|---|
Speed | Faster for larger projects | Slower, more detailed |
Skill Level | Easier to learn and master | Requires more skill and practice |
Materials Thickness | Better for thicker materials | Ideal for thinner, more delicate materials |
Weld Quality | Functional, but may have more spatter | Superior finish, cleaner welds |
Understanding mig vs tig welding helps in selecting the most suitable method for your welding job.
MIG welding is often the preferred welding technique for projects requiring speed and efficiency, particularly those with thicker materials.
MIG welding is easier to learn than TIG, making it suitable for beginners and rapid production environments.
TIG welding is the go-to choice when precision and weld quality are paramount, despite being a slower process.
TIG welding is better for projects that require refined craftsmanship and precision work.
Both MIG and TIG welding have diverse applications across numerous sectors:
The breadth of applications of mig and tig welding highlights their essential roles in modern manufacturing.
MIG welding offers several advantages that make it an attractive choice for many applications:
These advantages make MIG welding a key player in high-volume production environments.
TIG welding also provides distinct benefits, particularly for projects where detail and quality are crucial:
The superior quality of TIG welding excels in industries where exacting standards are mandatory.
Whether you’re using a mig or tig welder, here are some advanced tips to enhance your skills:
For MIG Welders
For TIG Welders
Mastering the subtleties of mig and tig welding can elevate your proficiency and lead to better results.
What is the main difference between MIG and TIG welding?
MIG welding is faster and more suitable for thicker materials, while TIG welding provides a cleaner, more precise weld.
What type of projects are best for TIG welding?
TIG welding is best for projects requiring high-quality, aesthetically pleasing welds, such as in art and design or medical devices.
How does MIG welding compare to stick weld?
MIG welding is generally faster and produces cleaner welds than stick welding, making it better for larger scale projects.
When should I choose MIG welding over TIG welding?
Choose MIG welding when speed is a priority, especially for thicker materials like automotive frames or construction beams.
Can I use TIG welding on all materials?
TIG welding is versatile but best suited for thinner materials and applications where cosmetic appeal is essential.
At our CNC Fabrication Manufacturing Plant, we are committed to delivering exceptional welding solutions tailored to your industry needs. Discover more about our services:
Ready to choose the right welding technique for your project? Contact us today to learn how we can help.
Get the latest trends and facts about CNC fabrication from our blog.
Shenzhen Runkey Precision Technology Co. Ltd, a subsidiary of the Tensun Group, is your trusted one-stop solution for custom manufacturing from prototyping to production.Transforming your idea into reality with digital manufacturing resources,streamlined processes, expert guidance,accelerated timelines, and uncompromising quality.
©2024. CNC Fabrication All Rights Reserved.