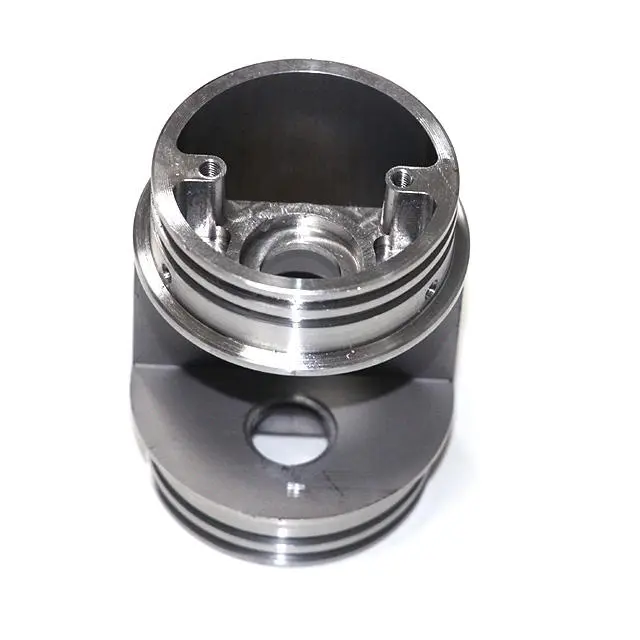
- +8615586668226
- [email protected]
- No. 30, Hongbang Industrial Park, Shenzhen
Sheet metal fabrication is a crucial manufacturing process that involves cutting, bending, and assembling metal sheets to create a desired shape or structure. I can confidently say that this process is the backbone of many industries, providing essential components for everything from aircraft to household appliances. We leverage our expertise as a leading sheet metal fabrication service provider to transform raw metal into high-quality parts, meeting the exact specifications of our clients.
There are numerous reasons why this process is paramount in modern manufacturing. Firstly, it allows for the creation of complex and intricate designs with high precision. Secondly, it offers durability and strength, making sheet metal parts ideal for demanding applications. Finally, our custom sheet metal fabrication services provide cost-effective solutions for both low and high volume production runs, making it a versatile choice for various projects.
CNC machining, or Computer Numerical Control machining, is a game-changer in the world of metal fabrication. This advanced technology uses pre-programmed computer software to dictate the movement of factory tools and machinery. In my experience, CNC machining significantly enhances both precision and efficiency. For example, CNC milling and CNC turning can produce parts with incredibly tight tolerances, ensuring perfect fit and function.
The use of CNC machines automates many steps that were once done manually, minimizing human error and increasing production speed. This not only leads to higher quality metal products but also reduces lead times, allowing us to deliver projects faster. Our machine shop is equipped with state-of-the-art CNC machines, enabling us to provide precision machining services that meet the highest industry standards.
The sheet metal fabrication process encompasses a range of techniques, each designed to shape and manipulate metal sheets into the desired form. As a seasoned metal fabricator, I can attest to the importance of mastering these processes. Key methods include laser cutting, CNC punching, metal bending using press brakes, and welding. Each of these techniques plays a vital role in transforming a flat metal sheet into a functional component.
Laser cutting uses a high-powered laser beam to make precise cuts, while CNC punching creates holes and shapes using a turret punch. Metal bending involves using a press brake to form angles and curves, and welding joins multiple metal parts together. Our expertise in these sheet metal fabrication processes ensures we can handle even the most complex projects, delivering exceptional results every time. We also offer sheet metal fabrication and machining in tandem to create the highest-quality finished products.
The choice of material is critical in sheet metal fabrication, as it directly impacts the final product’s strength, durability, and functionality. From my extensive experience, I can confidently state that stainless steel and aluminum are among the most popular choices due to their excellent properties. Stainless steel offers exceptional corrosion resistance and strength, making it ideal for harsh environments.
Aluminum, on the other hand, is lightweight yet strong, making it perfect for applications where weight is a concern. Other commonly used materials include mild steel, copper, and brass. Each material has its unique characteristics, and our team helps clients choose the best option for their specific needs. Whether it’s a robust part for an industrial machine or a lightweight component for an aircraft, we ensure the right material is used to achieve optimal performance. We utilize lean manufacturing principles to ensure that our use of raw materials is as efficient as possible.
Laser cutting has revolutionized the metal fabrication industry by offering unparalleled precision and versatility. This cutting-edge technology uses a focused laser beam to melt, burn, or vaporize material, resulting in clean, precise cuts. In my professional opinion, laser cutting is a superior method for creating intricate designs and achieving tight tolerances.
One of the key advantages of laser cutting is its ability to cut through various materials, including stainless steel, aluminum, and even non-metals. This versatility makes it an invaluable tool in our machine shop. Moreover, laser cutting produces minimal heat-affected zones, reducing the risk of material warping. This ensures that the metal parts maintain their structural integrity and meet the required specifications. We utilize our laser cutting expertise to provide clients with superior precision cutting solutions for a wide range of applications.
Sheet metal fabrication services are essential to a multitude of industries, each with its unique requirements and standards. As a provider of precision sheet metal fabrication, I’ve had the privilege of serving clients across various sectors. Here’s a table outlining some of the industries we serve and their specific needs:
Industry | Specific Needs |
Aerospace and Aviation | Lightweight, high-strength components, precise tolerances, compliance with strict regulations |
Automotive | Durable parts, high-volume production, cost-effective solutions |
Medical Devices | Biocompatible materials, precision, sterilization-resistant components |
Electronics | Intricate housings, heat dissipation solutions, EMI shielding |
Defense and Military | Rugged components, reliability under extreme conditions, high security standards |
Industrial Equipment | Robust parts, resistance to wear and tear, long service life |
Consumer Products | Aesthetically pleasing designs, cost-effective manufacturing, mass production |
Energy and Renewable Energy | Durable components for harsh environments, efficiency, sustainability |
Robotics | Lightweight yet strong parts, precision for intricate movements |
Construction & Architecture | Structural components, aesthetic finishes, durability |
Tooling and Dies | High precision, wear resistance, complex shapes |
Food and Packaging | Food-grade materials, hygienic designs, resistance to corrosion |
Pharmaceuticals | Cleanroom-compatible materials, high purity, precise tolerances |
Heavy Equipment | High-strength components, durability, resistance to extreme conditions |
Custom Projects/Prototyping | Unique designs, flexibility, quick turnaround |
Art and Design | Creative freedom, intricate details, unique finishes |
Telecommunications | Precision components for communication devices, durability, reliability |
Packaging | Custom packaging solutions, durability, precision |
Our expertise allows us to cater to the specific needs of each industry, delivering custom metal products that meet the highest standards of quality and performance. Whether it’s aerospace components requiring stringent tolerances or automotive parts needing high-volume production, we have the capabilities to deliver. We are an ISO 9001 certified company.
CNC punching and milling are two indispensable processes in our machine shop, each offering unique advantages. CNC punching is particularly efficient for creating holes and shapes in metal sheets with high speed and accuracy. This process uses a turret punch, which can hold various tools to create different shapes and sizes.
CNC milling, on the other hand, is ideal for creating complex 3D shapes and contours. It involves using rotating cutting tools to remove material from a workpiece, allowing for intricate designs and precise detailing. Both CNC punching and milling enhance productivity, reduce material waste, and ensure consistent quality across production runs. Our skilled machinists leverage these technologies to produce high-quality metal parts that meet the exact specifications of our clients.
Welding and assembly are the final steps in the fabrication process, bringing together individual metal parts to create a finished product. Welding involves joining metal pieces using heat, pressure, or both, creating a strong and durable bond. Common welding techniques include MIG, TIG, and spot welding, each suited for different applications and materials. Our certified welders possess the expertise to perform precise and reliable welds, ensuring the structural integrity of the final product.
Assembly services involve putting together various components to create a complete assembly. This can range from simple tasks like inserting fasteners to complex operations requiring specialized tools and fixtures. Our assembly team meticulously follows detailed instructions to ensure each component is correctly positioned and secured, resulting in a high-quality finished product.
Choosing the right sheet metal fabrication supplier is crucial for the success of your project. From my extensive experience in the industry, I can offer some key factors to consider. First and foremost, look for a supplier with a proven track record of delivering high-quality metal products. Check their certifications, such as ISO 9001, which demonstrate their commitment to quality management systems.
Expertise and experience are also vital. A reputable fabricator should have a deep understanding of various sheet metal fabrication processes and materials. They should be able to offer valuable insights and recommendations to optimize your design for manufacturability (DFM). Additionally, consider their capabilities and equipment. A well-equipped machine shop with advanced CNC machines, laser cutting capabilities, and other essential tools ensures they can handle your project efficiently. We also offer a wide range of additional services, including powder coating and other surface finishes.
Communication and customer service are equally important. A reliable sheet metal fabrication supplier should be responsive to your inquiries, provide regular updates on your project, and offer excellent support throughout the process. Finally, evaluate their pricing and lead times. While cost is a significant factor, it shouldn’t be the sole determinant. Focus on value for money, considering the quality, expertise, and service you’ll receive.
Here is a list of our services:
What is the difference between sheet metal fabrication and machining?
Sheet metal fabrication primarily involves cutting, bending, and assembling metal sheets to create parts and structures. Machining, on the other hand, involves removing material from a workpiece using cutting tools to achieve a desired shape. While both processes can create metal parts, sheet metal fabrication is typically used for thinner materials and larger structures, whereas machining is ideal for creating complex shapes and precise dimensions in thicker materials.
How do I choose the right material for my sheet metal fabrication project?
Choosing the right material depends on several factors, including the intended application, environmental conditions, and desired properties such as strength, weight, and corrosion resistance. Stainless steel is an excellent choice for applications requiring durability and corrosion resistance, while aluminum is ideal for lightweight components. Consult with our experts to determine the best material for your specific needs.
What are the benefits of using a contract manufacturer for sheet metal fabrication?
Using a contract manufacturer like us offers numerous advantages, including access to specialized expertise, advanced equipment, and scalable production capabilities. We can handle your entire project from prototype to production, ensuring consistent quality and timely delivery. Additionally, partnering with a contract manufacturer allows you to focus on your core business while we take care of your fabrication needs.
What is the typical lead time for a sheet metal fabrication project?
Lead times can vary depending on the complexity of the project, the materials used, and the production volume. Simple projects may take a few days, while more complex ones could take several weeks. We work closely with our clients to establish realistic timelines and provide regular updates throughout the process to ensure timely delivery.
What is water jet cutting and how does it compare to laser cutting?
Water jet cutting is a process that uses a high-pressure stream of water mixed with an abrasive substance to cut through materials. Unlike laser cutting, which uses heat, water jet cutting is a cold cutting process, making it suitable for materials that are sensitive to heat. Both methods offer precision cutting, but water jet cutting can handle thicker materials and does not produce a heat-affected zone.
How does your company ensure quality in sheet metal fabrication?
Quality is at the core of our operations. We are an ISO 9001 certified company, adhering to stringent quality management systems. Our experienced team conducts thorough inspections at every stage of the fabrication process, from material selection to final assembly. We use advanced measuring equipment to verify tolerances and ensure that every part meets the required specifications. Our commitment to quality ensures that you receive reliable and high-performance metal products.
Here are the most important things to remember from this comprehensive guide to sheet metal fabrication and CNC machining:
Sheet metal fabrication is a versatile process used across numerous industries to create durable and precise metal parts.
CNC machining enhances precision and efficiency, making it ideal for complex designs and tight tolerances.
Key sheet metal fabrication processes include laser cutting, CNC punching, metal bending, and welding.
Choosing the right material, such as stainless steel or aluminum, is crucial for achieving the desired properties in the final product.
Laser cutting offers unparalleled precision and versatility, revolutionizing metal fabrication.
Industries such as aerospace, automotive, and medical devices rely heavily on sheet metal fabrication services.
CNC punching and milling provide efficient solutions for creating holes, shapes, and complex contours.
Welding and assembly services are essential for completing the fabrication process and ensuring structural integrity.
Selecting a reputable sheet metal fabrication supplier involves considering their expertise, capabilities, communication, and pricing.
Quality assurance, through certifications like ISO 9001 and rigorous inspections, is vital for delivering high-quality metal products.
By understanding these key aspects, you can make informed decisions for your next project and partner with a sheet metal fabrication supplier who meets your needs and exceeds your expectations. Our team is ready to assist you with your fabrication needs, leveraging our expertise and advanced technology to deliver exceptional results. Contact us today to discuss your project and discover how we can help you achieve your goals.
Get the latest trends and facts about CNC fabrication from our blog.
Shenzhen Runkey Precision Technology Co. Ltd, a subsidiary of the Tensun Group, is your trusted one-stop solution for custom manufacturing from prototyping to production.Transforming your idea into reality with digital manufacturing resources,streamlined processes, expert guidance,accelerated timelines, and uncompromising quality.
©2024. CNC Fabrication All Rights Reserved.