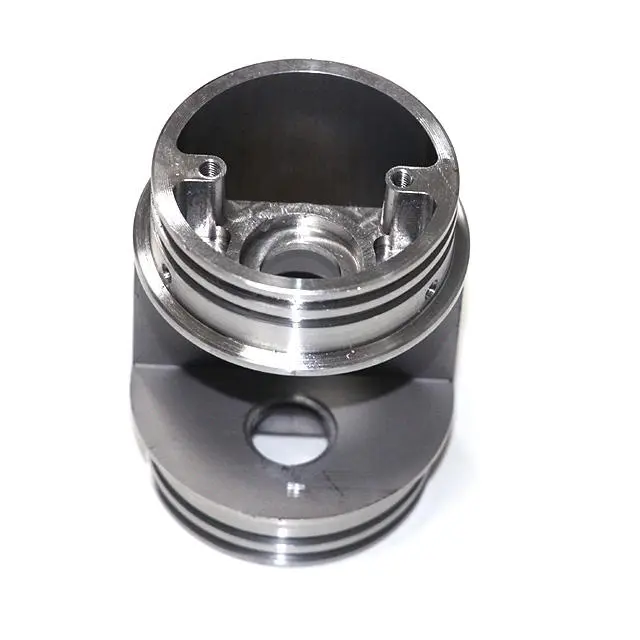
- +8615586668226
- [email protected]
- No. 30, Hongbang Industrial Park, Shenzhen
Surface finish isn’t just about making a part look good. It’s fundamental to a component’s functionality, durability, and overall performance. A properly finished surface can:
Polishing is a subtractive surface finishing process that refines the surface texture of a material, often to a mirror-like shine. It’s a critical step after CNC Machining (including CNC Milling and CNC Turning) or other fabrication processes like Sheet Metal Fabrication to remove tool marks, scratches, and other imperfections. It involves using abrasive materials to progressively smooth the surface.
The polishing process is a carefully orchestrated sequence of steps, each contributing to the final, flawless finish. Here’s a breakdown:
Surface Preparation: This initial step involves cleaning the workpiece to remove any contaminants like oil, grease, or dirt. A clean surface is essential for effective polishing. This might involve degreasing, ultrasonic cleaning, or other specialized methods.
Roughing (Coarse Polishing): This stage tackles significant surface flaws like deep scratches, pits, or burrs. Coarse abrasives (e.g., 60-80 grit) are used to remove these imperfections and create a more uniform surface.
Intermediate Polishing: With the major flaws addressed, we move to finer abrasives (e.g., 120-240 grit). This step further smooths the surface, removing the marks left by the roughing stage.
Fine Polishing: This is where the surface truly begins to shine. Very fine abrasives (e.g., 320-400 grit and higher) are used to eliminate the remaining minor imperfections, often resulting in a near-mirror finish.
Buffing: Buffing uses a soft cloth wheel (often made of cotton or felt) and a fine abrasive compound to enhance the luster and reflectivity of the surface. There are two key types of buffing:
Brightening (Optional): This step is often incorporated into the color buffing stage. It involves specialized techniques and compounds to maximize the reflectivity and brilliance of the surface.
Protection: During polishing, lubricants (like wax or kerosene) are often used. These serve a dual purpose:
Final Inspection: The polished workpiece undergoes a thorough inspection to ensure it meets the required specifications. This may involve visual inspection, surface roughness measurement, and other quality control checks.
Different materials and desired finishes require different polishing techniques. Here’s a look at some of the most common methods:
Polishing Technique | Description | Advantages | Disadvantages | Typical Applications |
---|---|---|---|---|
Mechanical Polishing | Uses abrasives (sandpaper, polishing wheels) to remove surface imperfections. Can be manual or machine-assisted. | High control over surface texture, effective for removing significant imperfections, suitable for achieving a mirror finish. | Labor-intensive, can generate heat (leading to distortion), requires skill to avoid over-polishing. | Automotive parts, tools, dies, metal components requiring a high-gloss finish. |
Chemical Polishing | Immerses the workpiece in a chemical solution that selectively dissolves surface material, smoothing out peaks and valleys. | Provides a uniform finish with minimal mechanical intervention, can polish complex geometries, improves corrosion resistance. | Requires careful handling of chemicals, less control over the process than mechanical polishing, potential environmental concerns. | Electronic components, parts with intricate shapes, applications requiring high corrosion resistance. |
Electropolishing | Uses an electrochemical process to remove material from a metal workpiece, resulting in a very smooth, bright, and corrosion-resistant surface. | Produces a very smooth and reflective surface, improves corrosion resistance significantly, can process complex shapes and internal surfaces. | Requires specialized equipment, handling of hazardous chemicals, not suitable for all metals. | Medical Devices, Aerospace components, food processing equipment, applications requiring extreme cleanliness and corrosion resistance. |
Vibratory Polishing | Parts are placed in a vibrating container with abrasive media, water, and sometimes chemical additives. The vibration causes the media to polish the parts. | Efficient for polishing large volumes of small parts, achieves consistent finishes, can be automated. | Limited to small or medium-sized parts, may require multiple cycles, not as precise as other methods for achieving specific textures. | Small Consumer Products, hardware, jewelry, deburring small parts. |
Buffing | Uses a soft cloth wheel and abrasive compounds to enhance the shine and smoothness of a surface, typically after mechanical polishing. | Produces a high-gloss, reflective finish, effective for removing minor imperfections, suitable for a wide range of materials. | Labor-intensive, may require multiple steps, not effective for removing deep scratches. | Automotive trim, jewelry, decorative items, achieving a final high-gloss finish. |
Lapping | A slow, controlled abrasive process using a lapping plate and abrasive slurry to achieve extremely flat and smooth surfaces with tight tolerances. | Achieves extremely flat and smooth surfaces, high precision, suitable for materials requiring tight dimensional tolerances. | Slow process, requires specialized equipment and skilled operators, not suitable for large-scale production. | Semiconductor wafers, precision mechanical components, optical lenses. |
Barrel Polishing | Parts are placed in a rotating barrel with abrasive media. The tumbling action polishes the parts. Also known as tumbling. | Efficient for processing large quantities of small parts, reduces labor costs, versatile (can handle various materials). | Not suitable for large or delicate parts, lower precision compared to other methods, can be time-consuming. | Small hardware, fasteners, deburring and smoothing small parts. |
Abrasive Flow Polishing | Uses a pressurized abrasive media (often a viscoelastic polymer) that is forced through internal passages or across the surface of a workpiece. | Highly effective for polishing complex internal geometries, produces a uniform finish, can reach inaccessible areas. | Expensive equipment, not suitable for all materials, may require multiple passes. | Industrial Equipment, aerospace components, medical devices, parts with intricate internal channels. |
Ultrasonic Polishing | Uses a tool vibrating at ultrasonic frequencies with an abrasive paste to remove microscopic amounts of material. | Excellent for intricate and delicate work, high degree of control, minimizes risk of damage, achieves extremely smooth finishes. | Slow process, requires specialized equipment, not ideal for removing large amounts of material. | Mold and die polishing, precision components, fine details. |
Flame Polishing | Uses a high-temperature flame to melt the surface layer of a thermoplastic, smoothing out imperfections. | Quick and efficient for polishing plastics (especially acrylic), produces a clear, high-gloss finish, no need for abrasives. | High risk of overheating (causing warping), limited to thermoplastics, requires skilled operation. | Acrylic sheets, plastic edges, applications requiring a clear, glossy finish on plastics. |
Polishing can be applied to a vast array of materials, each with its own unique considerations:
Frequency of Polishing:
The frequency of polishing depends on the material, its use, and the environment it’s exposed to.
Polishing plays a vital role in numerous industries:
Selecting the right partner for your CNC manufacturing and polishing needs is crucial. Look for a company with:
Even experienced professionals can make mistakes. Here are some common pitfalls and how to prevent them:
How much does polishing cost?
The cost varies depending on the material, complexity, and desired finish. Basic polishing can range from $20 to $100 per hour, but specialized techniques like electropolishing can be more expensive.
What are the safety precautions for polishing?
Always wear protective gear (safety glasses, gloves, dust mask), ensure proper ventilation, secure the workpiece, handle chemicals carefully, and maintain tools regularly.
How does compound quality affect polishing?
High-quality compounds ensure consistent results, minimize imperfections, and enhance corrosion resistance. Low-quality compounds can introduce new imperfections.
What are the alternative to metal polishing?
There are many types of metal polishing such as electropolishing, bead blasting, powder coating, anodizing, and buffing.
What is the difference between lapping and polishing?
Lapping produces ultra-flat surfaces with high precision using loose abrasives, while polishing focuses on smoothness and shine using bonded or coated abrasives.
What’s the difference between polishing and buffing?
Polishing is a more aggressive process that removes surface imperfections, while buffing is a finer process that enhances shine and smoothness after polishing.
Polishing is a critical aspect of CNC manufacturing, transforming raw materials into high-performance, aesthetically pleasing components. By understanding the various techniques, materials, and applications, you can ensure your products meet the highest standards of quality and durability. Partnering with a skilled CNC manufacturing service provider like us ensures you receive expert polishing and exceptional results.
Key Takeaways:
Get the latest trends and facts about CNC fabrication from our blog.
Shenzhen Runkey Precision Technology Co. Ltd, a subsidiary of the Tensun Group, is your trusted one-stop solution for custom manufacturing from prototyping to production.Transforming your idea into reality with digital manufacturing resources,streamlined processes, expert guidance,accelerated timelines, and uncompromising quality.
©2024. CNC Fabrication All Rights Reserved.