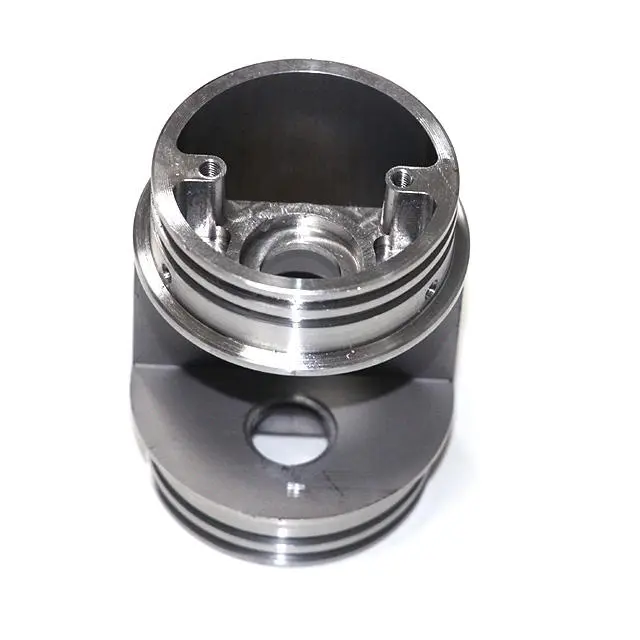
- +8615586668226
- [email protected]
- No. 30, Hongbang Industrial Park, Shenzhen
We are a full-service CNC manufacturing facility, equipped to handle projects of any size and complexity. Our commitment to quality, precision, and customer satisfaction sets us apart. We don’t just manufacture parts; we provide solutions. We utilize cutting-edge technology and a team of experienced engineers and machinists to deliver components that meet the strictest tolerances and the most demanding specifications. Whether you need a single prototype or a large-scale production run, we’re your one-stop shop. CNC Solutions
Our expertise spans a wide array of industries. We understand that each sector has unique demands, and we tailor our services accordingly. Here’s a snapshot of some of the key industries we support:
We offer a comprehensive suite of Machining Services to meet diverse manufacturing needs. These include:
Casting, a foundational manufacturing method, involves pouring molten material into a mold and allowing it to solidify. This process is especially effective for producing intricate shapes that would be challenging or costly to make using other methods.
Casting dates back to around 3200 BCE with the discovery of copper artifacts in Mesopotamia. Advances in metallurgy and materials science significantly influenced the evolution of casting techniques.
By the 18th century, improvements in cast iron production greatly expanded its applications, contributing to the Industrial Revolution.
The 20th century saw revolutionary developments like die casting and investment casting, which enabled high-volume manufacturing of precise and reliable parts. Today, casting is still a cornerstone of manufacturing, continually enhanced by automation and materials engineering.
Casting involves shaping molten material into a solid form by pouring it into a mold. The material cools and hardens, taking the shape of the mold cavity.
The casting process involves six key steps, each crucial for achieving the desired outcome:
Various casting processes exist, each suited to different project needs and material characteristics.
These methods use temporary, non-reusable molds.
Sand Casting: A versatile method using sand molds, suitable for both ferrous and non-ferrous materials.
Benefit | Description |
---|---|
Flexibility | Can cast a wide range of materials. |
Scalability | Suitable for small batches to large-scale productions. |
Cost-Effectiveness | Lower production costs due to reusable materials and inexpensive molds. |
Investment Casting (Lost Wax Casting): Creates highly accurate parts with intricate details using a wax model encased in ceramic.
Shell Molding: Uses a resin-covered sand to create a mold, offering excellent dimensional accuracy.
Lost Foam Casting: Utilizes a polystyrene foam pattern that vaporizes when molten metal is poured in.
Plaster Casting: Employs plaster of Paris molds, ideal for detailed items and art pieces.
Ceramic Mold Casting: Uses ceramic molds for high-temperature metals, ensuring precision.
Full Mold Casting: Combines characteristics of sand and lost foam casting.
Electroslag Casting: Used for high-performance metal parts with excellent integrity.
These methods use reusable molds made from metal.
Several machines and tools are crucial for the casting process:
Understanding material properties is vital for optimizing the casting process. Here are some popular materials:
Material | Properties | Applications |
---|---|---|
Aluminum | Lightweight, corrosion-resistant | Automotive, aerospace |
Cast Iron | Durable, wear-resistant | Machine tools, automotive parts |
Steel | High strength, versatile | Construction, heavy machinery |
Copper | Highly conductive | Electrical components |
Bronze | Corrosion-resistant, fatigue-resistant | Sculptures, marine hardware |
Zinc | Low melting point, easy to cast | Die casting intricate components |
Magnesium | Lightweight, high strength-to-weight ratio | Automotive, aerospace |
Nickel | High melting point, corrosion-resistant | Specialty steels |
Tin | Coats other metals to prevent corrosion | Alloys like bronze, coatings |
Lead | Heavy, malleable | Radiation shielding, batteries |
Titanium | Strong, lightweight, corrosion-resistant | Aerospace, medical applications |
Other materils | Silicon Bronze, Brass, Gold, Bismuth, Pewter, Cobalt, Ceramics, Graphite, Polyurethane | Various uses |
Understanding these parameters is vital for achieving high-quality castings:
Casting is used across various industries:
Don’t leave your project to chance. Partner with a trusted CNC manufacturing service provider that delivers exceptional results. Contact us today to discuss your project requirements and receive a personalized quote. We’re here to help you bring your vision to life. We are ready for your call, e-mail or other form of a request.
What materials can you work with?
We work with a wide range of materials, including aluminum, steel, stainless steel, titanium, brass, copper, plastics, and more. We can help you select the optimal material for your application.
What is your typical lead time?
Lead times vary depending on the complexity of the project, the material, and the quantity required. However, we strive to provide the fastest possible turnaround times without compromising quality. We’ll provide a detailed timeline with your quote.
What tolerances can you achieve?
We can achieve extremely tight tolerances, often down to +/- 0.001 inches (0.025 mm) or better, depending on the specific requirements of the part and the material.
Do you offer design assistance?
Yes, our experienced engineers can provide design assistance and optimization to ensure your parts are manufacturable and meet your performance requirements.
What quality control measures do you have in place?
We have a rigorous quality control system in place, including in-process inspections, dimensional verification, and material testing. We are committed to delivering parts that meet or exceed your expectations.
Can I order a prototype before committing to a large production run?
Yes, we specialize in creating quick prototypes.
Common defects include:
Minimizing defects involves using simulation software, controlling material quality, regular equipment maintenance, training personnel, and implementing quality checks.
Common tests include:
Casting costs depend on material, mold complexity, production volume, machining requirements, finishing processes, energy, and labor costs. It is most economical for large quantities and complex geometries.
The casting timeline varies from days to weeks, influenced by mold design, material preparation, casting method, cooling time, post-processing, and inspection.
Safety protocols include using personal protective equipment (PPE), ventilation systems, training, and equipment maintenance. Environmental considerations involve recycling initiatives, energy efficiency, emission control, and water management.
Casting involves pouring molten metal, while forging deforms metal under pressure. Casting offers versatility, while forging provides superior strength.
Casting shapes molten metal, while machining removes material for precision. Casting is suitable for mass production, while machining provides refined finishes. CNC Machining
Future trends include 3D printing molds, new materials, digital simulation, and sustainable practices.
Get the latest trends and facts about CNC fabrication from our blog.
Shenzhen Runkey Precision Technology Co. Ltd, a subsidiary of the Tensun Group, is your trusted one-stop solution for custom manufacturing from prototyping to production.Transforming your idea into reality with digital manufacturing resources,streamlined processes, expert guidance,accelerated timelines, and uncompromising quality.
©2024. CNC Fabrication All Rights Reserved.