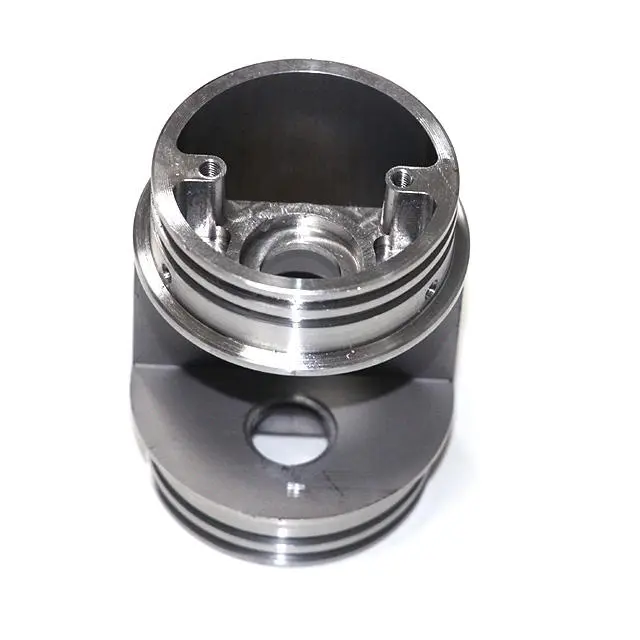
- +8615586668226
- [email protected]
- No. 30, Hongbang Industrial Park, Shenzhen
Tapping is a crucial machining process that creates internal threads within a pre-drilled hole, allowing for the secure fastening of screws, bolts, or other threaded components. Think of it like creating the internal grooves in a nut that allow a bolt to screw in tightly. This method is essential for connecting parts reliably and is widely used in numerous manufacturing applications. It is vital for creating strong connections between different components.
Tapping dates back to the Industrial Revolution, around 1775, when British instrument maker Jesse Ramsden invented the first practical tap. This invention was pivotal, laying the groundwork for how we create threads in materials today. Over time, tapping methods have advanced significantly, from manual hand tools to the highly precise CNC Machining processes used in modern manufacturing.
The tapping process involves a tool, known as a tap, which cuts threads into a material as it is twisted into a pre-drilled hole. The cutting edges of the tap remove material, creating the threads designed to match the screw or bolt intended for use.
Tapping can be performed manually with hand taps or automatically with a CNC machine, depending on precision and repeatability requirements. Here’s a simplified breakdown:
Drilling and tapping are two distinct processes in manufacturing. Drilling creates a round hole in a workpiece using a drill bit. Tapping, however, involves creating internal threads inside that hole, using a tool called a tap. Drilling is the preparation step; tapping is what makes the hole functional for fasteners.
Tapping focuses solely on creating internal threads. Milling, in contrast, is a more versatile process that removes material to shape a workpiece, creating features like slots or grooves. While CNC Milling can perform a wide range of operations, tapping is specifically for making threaded holes.
Various tapping processes exist, each tailored to specific needs and levels of precision. Here are some options:
Hand tapping is a manual method using hand taps and a tap wrench. It’s suitable for low-volume work and field repairs, typically in softer materials like aluminum and plastics.
CNC Tapping is an automated process offering high precision and consistency. It’s ideal for industries like aerospace and automotive, where precision is crucial.
This method creates threads in holes that go entirely through the material, often used when a bolt or screw needs to pass through the entire thickness.
Blind hole tapping creates threads in holes that do not go all the way through. Precision is critical to avoid damaging the bottom of the hole.
Rigid tapping synchronizes the tap with the machine’s spindle speed, ensuring perfect alignment. This method is often used in CNC machines for high-precision threading.
Floating tapping allows the tap some “float,” compensating for minor misalignments. This flexibility reduces the risk of tap breakage.
This highly precise process synchronizes the tap with the machine’s spindle for forward and reverse rotation, ideal for high-volume production.
Peck tapping involves advancing the tap in small increments, allowing for chip evacuation, especially useful in deep holes or difficult materials.
Form Tapping creates threads by displacing material rather than cutting it. This method is ideal for softer materials like aluminum.
This method pushes chips forward, out of the hole, ideal for through holes and materials that generate a lot of chips.
Spiral flute taps lift chips out of the hole, making them perfect for blind holes.
This process leaves intermittent thread sections, reducing contact area and improving chip evacuation in tough-to-cut materials.
Roll tapping, also known as thread forming, creates threads by displacing the material, eliminating chips.
Machine Tapping involves using a tap to remove material and create threads, suitable for harder materials where forming isn’t feasible.
Pipe tapping creates threads in pipes for secure connections, commonly used in plumbing and hydraulic systems.
Bottoming tapping creates full threads at the bottom of a blind hole, ensuring maximum thread engagement.
Plug tapping, or intermediate tapping, creates threads deeper into a hole, guided by the tap’s tip.
Taper tapping uses a tap with a gradual taper, ideal for starting threads in a hole.
Power tapping uses a CNC machine or power tool to drive the tap, ideal for high-speed, precision environments.
Gun nose tapping, similar to spiral point tapping, pushes chips forward, perfect for through holes.
Multi-spindle tapping uses multiple spindles to tap several holes simultaneously, boosting productivity in high-volume settings.
Choosing the right tapping method is key for optimal results. Factors to consider include:
Numerous tap types are available, each suited to specific tasks:
Tap Type | Description |
---|---|
Hand Taps | Used for manual or light machine work. |
Machine Taps | Optimized for high-speed operations in CNC machines. |
Gas Taps | Designed for gas fittings, ensuring tight seals. |
Machine Screw Taps | Create threads for machine screws. |
Extension Taps | Feature a long shank for reaching deeper into blind holes. |
Bend Shank Taps | Ideal for hard-to-reach areas in complex workpieces. |
Stay Bolt Taps | Used in high-pressure applications like steam boilers. |
Detailed look at Hand Taps
Hand taps are among the most common taps used for general tapping applications. They can be operated by hand or with a machine and are versatile in terms of material and application. Below is a detailed look at different hand taps:
Choosing the right tap involves considering:
Successful tapping requires a set of tools:
Understanding tapping parameters is crucial for quality and efficiency:
Choosing the right material is crucial for successful tapping. Suitable materials include:
Material selection directly impacts tool life, thread quality, and overall efficiency. Softer metals allow faster speeds, while harder metals require cutting fluids and slower speeds.
High-speed steel (HSS) is a common choice for taps due to its toughness and heat resistance. Cobalt steel offers greater wear resistance for harder materials.
Tapping is essential in various industries:
Mistake | Cause | Solution |
---|---|---|
Wrong Tap Size | Using an incorrect tap size for the hole. | Verify the tap size using a tap drill chart. |
Incorrect Speed | Spindle speed too high or too low. | Adjust speed based on material and tap design. |
Inadequate Lubrication | Insufficient or no cutting fluid. | Apply proper lubrication to reduce heat and wear. |
Improper Alignment | Misaligned tap. | Use a tap guide or fixture. |
Not Clearing Chips | Accumulated chips clog the hole. | Use spiral point/flute taps for chip evacuation. |
Overuse of Taps | Using worn taps. | Regularly inspect and replace taps. |
Tapping costs vary, typically ranging from $0.10 to $2 per hole. Factors influencing cost include:
Tapping is a critical process in manufacturing, offering precision, efficiency, and reliability. Understanding the various methods, tools, and parameters involved is crucial for achieving high-quality threaded holes. Whether you’re working in aerospace, automotive, or creating custom prototypes, mastering the art of tapping is essential for success.
Is tapping the same as threading?
Tapping is a type of threading. Tapping creates internal threads, while threading encompasses both internal and external thread creation.
Can you tap with a milling machine?
Yes, milling machines can perform tapping using appropriate tools and settings.
Can you tap on a CNC machine?
Yes, CNC machines are ideal for tapping, offering automated precision and control.
What is the best tap for hardened steel?
For hardened steel, cobalt or carbide taps are generally recommended due to their increased hardness and wear resistance compared to standard high-speed steel (HSS) taps.
Why use cutting fluid for tapping?
Cutting fluid serves multiple important purposes in the tapping process: It lubricates the tap and workpiece, reducing friction and heat generation, which helps prevent tap breakage and extends tool life.
Is tapping a machining process?
Yes. Machining is a broad term encompassing various processes that remove material from a workpiece to achieve a desired shape or feature. Tapping falls under this category because it involves removing material to create internal threads within a pre-drilled hole.
Get the latest trends and facts about CNC fabrication from our blog.
Shenzhen Runkey Precision Technology Co. Ltd, a subsidiary of the Tensun Group, is your trusted one-stop solution for custom manufacturing from prototyping to production.Transforming your idea into reality with digital manufacturing resources,streamlined processes, expert guidance,accelerated timelines, and uncompromising quality.
©2024. CNC Fabrication All Rights Reserved.