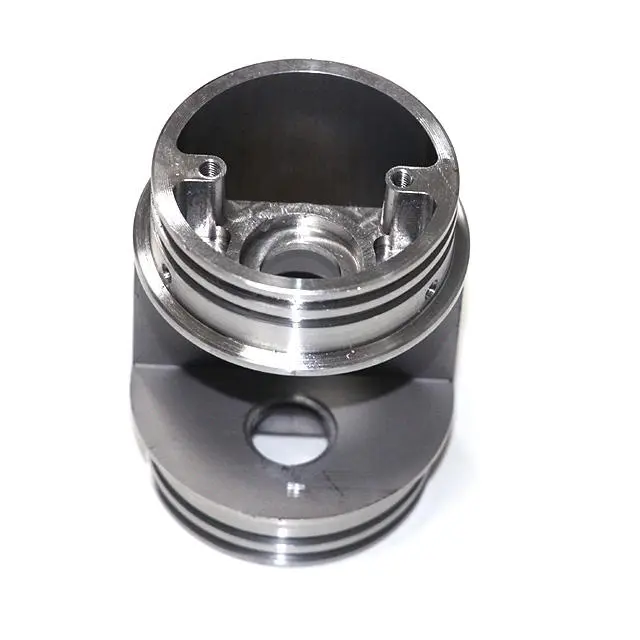
- +8615586668226
- [email protected]
- No. 30, Hongbang Industrial Park, Shenzhen
Precision grinding is a machining process that utilizes an abrasive grinding wheel to remove material from a workpiece. Unlike turning and milling, which use cutting tools, grinding uses a wheel consisting of abrasive particles to achieve extremely tight tolerances and superior surface finishes. This method is crucial when standard machining methods cannot provide the required precision. It’s not just about removing material; it’s about achieving a level of accuracy that can significantly impact the performance and reliability of the finished parts. The process allows for the creation of precise shapes and surfaces, and is essential for manufacturing precision parts, and parts with tight tolerance, where achieving specific surface finish, flatness, and dimensional accuracy is critical, often at the micron-level. For our customers, that means consistent and reliable components every single time.
The importance of precision grinding extends across diverse industries. From aerospace components requiring high precision to medical devices demanding the utmost accuracy, our precision grinding services ensure the quality and reliability of critical components. The need for tight tolerance in precision machining means that precision grinding is essential to meet those requirements, and create high-quality products. We take pride in offering state-of-the-art precision grinding capabilities, utilizing advanced machines and highly experienced staff to ensure the best results for every single project.
We offer a range of precision grinding services, each designed to meet the specific needs of our customers. Our offerings include surface grinding, cylindrical grinding, and centerless grinding, as well as specialized precision grinding processes. Surface grinding involves using a grinder to create flat surfaces, ensuring that every part has a perfect surface quality, and achieving tolerance accuracy. Cylindrical grinding, also known as center-type grinding, shapes and refines cylindrical workpieces, often utilizing a cylindrical grinder to achieve the specific geometry you need, with the workpiece rotate. This is a common technique for producing od (outer diameter) work on various cylindrical components. Finally, centerless grinding provides high productivity for producing cylindrical workpieces without needing to hold them between centers. This technique is particularly well-suited for small parts, or for components where the workpiece held can be done more efficiently without traditional methods.
Our ability to manage a wide range of precision grinding processes means we can handle complex and simple projects effectively. Our advanced grinding machine and abrasive technology allows us to deliver components with the highest quality, meeting the exact specifications of our customers. We also offer specialized grinding such as rotary grinding, which can be used to create precise circular forms. We’re committed to using the latest technology and techniques to ensure we are at the forefront of precision grinding inc, helping you to deliver superior products.
The benefits of precision grinding are numerous, making it an invaluable process in manufacturing. One of the primary advantages is its ability to achieve extremely tight tolerances and superior surface finishes that other machining methods simply cannot match. This results in precision parts that perform reliably in critical applications. Grinding allows for a high degree of precision and repeatable results, making it an important part of manufacturing high-quality components. This allows for consistently superior parts production, and reduced wastage due to inaccuracies.
Another key benefit is the ability to work with very difficult to machine materials like hardened steel or alloys. Precision grinding allows manufacturers use to achieve the specific shapes and sizes required even with difficult workable materials. It can also be used for sharpen tools, such as drill bits and cutters. The fine finishes achieved through precision grinding also improve part functionality, reducing friction and increasing wear resistance. These factors lead to increased productivity and a cost-effective approach to achieving high-precision components, and parts that meet critical performance demands.
A grinding machine is a complex piece of equipment, but the basic principle is quite straightforward. The grinding machine uses motors rotate to turn a grinding wheel and the workpiece against each other. The grinding wheel, consisting of abrasive particles held together, removes material from the surface of the workpiece. Grinding is a machining process, where the rate of material removal is determined by the type of abrasive, the speed of the grinding wheel, and the pressure applied. The grinder moves the wheel relative to the workpiece, controlling the exact amount of material removed. Advanced cnc grinding machines can perform these movements with a high degree of accuracy, ensuring consistent results with every part. The specific type of grinding operations determines how these movements are coordinated to remove material in a specific way, like cylindrical or flat.
Modern grinding machines are capable of very fine control, which allows for achieving micron-level accuracy. The grinding process is typically done using a coolant that washes away the swarf and keeps the workpiece and grinding wheels cool. This minimizes heat buildup that could compromise tolerance. In addition to the grinding wheel, many grinders will use a magnetic chuck to hold the workpiece, particularly when surface grinding is being performed. The movements of the grinder can be in radial directions, or the workpiece may be programmed to move and/or workpiece rotate along different axis in cnc machining, using the latest cnc control technology.
The versatility of precision grinding allows it to be used with a wide range of materials include including ferrous and non-ferrous metals, alloys, ceramics, composites, and even plastics. This makes it a vital process for many different industries. Whether the material is difficult to machine or requires a high degree of precision, grinding offers a solution. For metals, a variety of grinding wheels and techniques can be utilized to achieve the desired results.
For non-metal parts, it’s often possible to grind ceramics and composite materials to the necessary sizes and shapes with abrasive grinding, using the right tools and approaches. Even specialized materials include plastic components can be precision ground to meet the requirements for your specific product needs. We adapt our processes and wheel selection to each unique material, ensuring optimal results, and that the surface of the workpiece reaches the specified quality. No matter what materials include are being used, the key is to select the right abrasive grinding wheels and processing conditions to ensure optimal outcomes, and superior quality components.
Choosing us for your precision grinding services means partnering with a team that has a commitment to quality and effective machining. We have invested heavily in the latest grinding machines and technology, including advanced cnc capabilities. This ensures we can consistently meet the tightest tolerance requirements. Our experienced staff is highly skilled and understands the intricacies of various precision grinding processes, which can meet even the most complex projects. We ensure every single workpiece meets the required specifications.
We also understand that the cost-effectiveness is important, and our optimized processes allow us to deliver high-quality parts at a reasonable cost. Our precision grinding offers increased productivity and the ability to handle high volumes of parts. We are ISO certified and follow a strict quality control process, which means we can assure you of our superior quality, and that you will receive consistently reliable parts. Let us be your partner in precision machining and see how our precision grinding services will help your production meet all the goals you have set.
While surface grinding is a form of precision grinding, it specifically focuses on creating flat surfaces with the grinder. Surface grinding is an essential part of the wider set of precision grinding processes, and involves removing material from a flat surface to achieve a high degree of smoothness and accuracy. This is often used when parts require a perfectly flat surface, with exact parallel or perpendicular faces. All surface grinding is precision grinding, however, not all precision grinding is surface grinding.
Other forms of precision grinding include cylindrical grinding, centerless grinding, and other specialized grinding operations. Each is designed for different applications, while they all require abrasive removal of material from the workpiece and the grinding wheel. Precision grinding encompasses all these techniques, and it is often used in conjunction with other manufacturing techniques, to create the best possible final products. Our wide range of precision grinding allows us to help you with a variety of manufacturing needs.
Precision grinding differs significantly from other common machining methods like turning and milling. Turning uses a lathe to remove material from a rotating workpiece, while milling uses a rotating cutting tool to remove material from a stationary workpiece. While both methods are very effective for creating parts, they often struggle to achieve the tight tolerance and surface finishes that precision grinding offers. In many cases, turning and milling can be combined with precision grinding to achieve the final precision parts.
When considering which process is most suitable, it is important to note that grinding is a machining process, that uses an abrasive grinding wheel, instead of a cutting tool. Where tolerance is critical, and fine finishes are required, precision grinding is usually required after turning and milling, to achieve the highest accuracy and finishing. Precision grinding is a final process for finishing in many industries, especially for parts with tight tolerance, and where superior accuracy and reliability are critical. Also, other processes, such as hone and lap are used in specific applications after the grinding process is completed.
You’d choose precision grinding over other methods when parts require very tight tolerances, superior surface finishes, or when working with very hard materials. If you require parts with micron-level accuracy, or have parts with very specific geometry, it’s likely that precision grinding would be the most suitable option. This is particularly true when standard machining processes can’t achieve the required results. The cost of grinding is usually higher than other methods, however for the desired results, precision grinding is one of the most effective methods, and a cost-effective choice.
Grinding is used as a finishing process after other machining methods, such as cnc turning, where the specific geometric tolerances or smooth surface finishes need to be achieved. Consider using precision grinding when working with hardened metals, alloys, or other materials that are difficult to machine. The ability to achieve the required precision for these materials and requirements, makes precision grinding essential in many situations. When the need for tolerance requirements is high, you will need to look at the precision grinding process.
If you’re ready to elevate your parts manufacturing, contact us to discuss your project and precision grinding services needs. We’re here to answer your questions and provide solutions. Our team is dedicated to understanding your requirements and we’re here to deliver the best quality and most precise results for all your machining needs. We offer a no-obligation consultation, to go through your specific requirements, and how we can meet your needs. Don’t hesitate to get in touch to see how our grinding services can make a difference for you. We are ready to listen to your needs and show you how our precision machining and experienced staff, will give you the edge.
Our ability to deliver exceptional quality and accuracy, makes us the ideal partner for all your precision manufacturing needs. We are excited to work with you, and show you how our commitment to quality can help you be successful. So reach out to us today, and find out how we can provide you with a total solution. You can find our contact information on our website, and one of our experienced team members is ready to assist you. Contact us now, to start on your next project.
What is the primary difference between precision grinding and other machining processes?
The key difference is the use of an abrasive grinding wheel to achieve tight tolerances and superior surface finishes, while other methods use cutting tools.
What kinds of tolerances can be achieved with precision grinding?
Precision grinding can achieve micron-level tolerances, often measured in thousandths of an inch.
Is precision grinding suitable for small parts?
Yes, precision grinding is often used for small parts, especially when extremely tight tolerances are needed.
What industries benefit most from precision grinding services?
Industries such as aerospace, medical devices, electronics, and automotive, among many others, heavily rely on precision grinding for critical components.
Can precision grinding be used on hardened materials?
Yes, it’s often used for hardened materials, as it can achieve very fine results and specific geometry.
What does ISO certification mean for precision grinding services?
ISO certification means that the provider follows strict quality control processes, ensuring the parts meet international quality standards, and high-quality products.
Ready to experience the difference that precision grinding can make? Contact us today and discover how we can help with your manufacturing needs! Check out our CNC Machining services, and our capabilities in CNC Turning and CNC Milling. We also offer Fabrication Services and Rapid Prototyping for a complete solution. You can find details about Materials that we work with on our website.
Get the latest trends and facts about CNC fabrication from our blog.
Shenzhen Runkey Precision Technology Co. Ltd, a subsidiary of the Tensun Group, is your trusted one-stop solution for custom manufacturing from prototyping to production.Transforming your idea into reality with digital manufacturing resources,streamlined processes, expert guidance,accelerated timelines, and uncompromising quality.
©2024. CNC Fabrication All Rights Reserved.