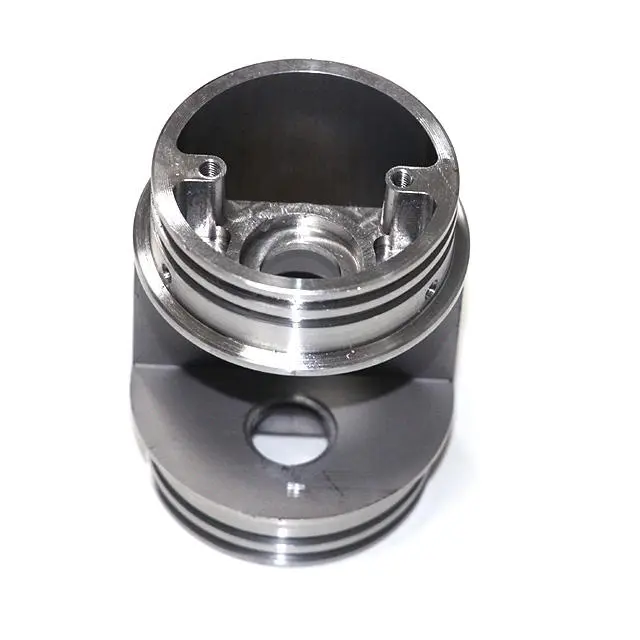
- +8615586668226
- [email protected]
- No. 30, Hongbang Industrial Park, Shenzhen
Honing is a precision machining process used to improve the surface finish, dimensional accuracy, and geometry of bores in various workpieces. Unlike other machining methods, honing focuses on fine material removal using abrasive stones that abrade the surface. The honing tool, which is a tool equipped with these stones, is rotated and reciprocated inside the bore, creating a smooth and precise internal cylindrical surface. This process used involves a controlled abrasive machining action that enhances the functional properties of the workpiece.
The honing process involves a multi-point tool where honing stones are held in a tool holder and expanded radially against the cylinder wall as it rotates. This controlled action ensures that any imperfections on the surface of the part are removed uniformly, resulting in a cylinder bore that is not only precise but also exhibits an optimal surface finish. The reciprocating motion of the tool while rotating creates a characteristic cross-hatch pattern on the internal surface, which is crucial for lubrication and oil retention, especially in applications involving pistons and cylinders. This intricate honing action is vital for creating functional surfaces.
A typical honing machine consists of several vital components that work in unison to execute the honing process efficiently. The main parts include a rotating spindle that drives the honing tool, a hydraulic system for controlling the pressure and expansion of the honing stones, a reciprocating mechanism that provides the up and down motion, and a coolant system that lubricates and cools the workpiece during the machining operation. The machine is engineered for high-precision, providing the level of control necessary for high-quality surface finishes and dimensional accuracy.
The honing machine is relatively simple, but the precision lies in its ability to maintain consistent pressure and movements. The spindle must be precisely aligned, and the hydraulic system needs to deliver consistent force to ensure uniform material removal. Many honing machines also incorporate automated systems that monitor the process and adjust parameters as needed. Furthermore, some advanced honing machines have features that allow for complex movements and sophisticated honing operations, broadening the range of surfaces that honing can achieve. These elements come together to ensure precision for every workpiece honed.
Honing tools come in various designs, each tailored for different applications and bore sizes. The core component is the honing stone, which is an abrasive element that removes material from the workpiece. These abrasive stones are made of various materials, including aluminum oxide, silicon carbide, and diamond, depending on the required finish and the workpiece material. The honing tool itself is designed to hold these honing stones securely and expand them radially against the bore surface.
Honing stones may be mounted in a variety of ways, such as on a mandrel that allows for adjustable expansion. The selection of the honing tool and abrasive stones depends on several factors, such as the size and geometry of the bore, the desired surface finish, and the tolerance required. For instance, larger bores might require larger honing tools with multiple abrasive stones, while small, intricate bores demand more compact honing tools with fine abrasive. The tool must be appropriate for the specific job, ensuring the proper surface finish. We produce a variety of honing tools at our machine shop, and we use them every day.
While both honing and grinding are abrasive machining processes used to refine workpieces, they differ significantly in their process, purpose, and the results they achieve. Grinding typically utilizes a rotating grinding wheel to abrade material from the surface of the workpiece using a high speed operation for rapid material removal of material. It often leaves behind a rougher surface finish than honing and is not suitable for the same level of dimensional accuracy. Grinding is great for shaping and smoothing outside surfaces, while honing focuses on inside surfaces.
In contrast, honing uses abrasive stones with a slower, reciprocating action to achieve a highly refined surface finish and precise bore geometry. The difference between honing and grinding lies in the process and the application. Honing is a finishing process, while grinding is more for shaping. Honing is excellent for achieving specific dimensional and form accuracy, especially in applications requiring minimal friction and optimal oil retention. The focus of honing is on refinement, whereas grinding focuses more on removal, which makes both abrasive processes very different.
The applications of honing are incredibly diverse, spanning various industries where high-precision and smooth bores are critical. In the automotive manufacturing industry, honing is essential for finishing cylinder walls in internal combustion engines, ensuring proper sealing and smooth piston movement. Aerospace relies on honing for hydraulic cylinders and valve bodies, where high accuracy and reliability are paramount. The medical device industry utilizes honing for producing smooth, precise bores in surgical instruments.
Beyond these, honing is also vital in the manufacturing of hydraulic components, bearings, gears, and various other high-precision parts. The process is even used in the production of tooling and dies. The ability of honing to achieve tight tolerances and superb surface finish makes it indispensable in many different fields. It’s also useful in automation where precision parts are needed. In these areas, honing allows us to achieve the results that we need.
The honing process offers several key advantages that make it ideal for precision machining applications. First and foremost, honing delivers exceptional dimensional accuracy and form accuracy, ensuring that bores meet the tight tolerances specified in engineering designs. The process provides a superior surface finish, which is critical for reducing friction, enhancing wear resistance, and promoting optimal lubrication. This helps in the removal of material for a smooth finish.
Additionally, honing is a very controlled machine process, which allows it to remove small amount of material precisely. The cross-hatch pattern created by honing on the surface of the workpiece is essential for effective oil retention, which is especially important in cylindrical components that operate under high loads. This process increases the longevity and performance of parts. Overall, honing offers unparalleled precision and efficiency when it comes to bore finishing, and when you need this done, it can be a lifesaver.
Several honing operations and techniques are available, each tailored for specific needs. Conventional honing involves using a honing tool with abrasive stones to achieve the desired surface finish. Stroke honing involves controlling the stroke length and speed of the honing tool to customize the cross-hatch pattern and surface finish. This method is great for long bores. Form honing shapes the bore geometry to achieve a specific profile that a standard honing procedure would not achieve.
Single-pass honing is another technique that utilizes single-pass honing machines with specialized honing stones that perform the finishing process in one pass. This method is ideal for high-volume production where consistency and speed are essential. Depending on the application, different honing techniques can be employed to achieve the desired results, and a variety of honing machines come with a range of options for different parts. The machine you use depends on the process at hand.
The selection of abrasive material for honing stones is crucial for achieving the desired results. Common materials include aluminum oxide, silicon carbide, and diamond. Aluminum oxide is a versatile abrasive used for various workpiece materials, providing a good balance of cutting efficiency and surface quality. Silicon carbide is often used for cast iron and other harder materials, thanks to its sharper and more aggressive cutting action. It is also cost-effective.
Diamond is the hardest abrasive available and is used for very demanding applications where maximum material removal and very precise surface finishes are required. The grit of the abrasive stones also plays a significant role. Finer grit stones are used for achieving a smoother surface finish, while coarser grit stones are used for faster material removal. The correct abrasive material is essential for a successful and efficient honing operation.
Honing significantly impacts both the surface finish and the tolerance of a workpiece. The controlled abrasive action ensures that honing creates an exceptionally smooth surface finish, often with a surface finish of only a few microinches. The precise movements and controlled pressure of the honing machine allow for the creation of consistent and accurate bores that meet the required dimensional accuracy. The precision and accuracy of our honing machines makes this achievable.
Honing is capable of achieving tight tolerances which are often critical in high-performance components. The process also minimizes the chance of any surface irregularities and maintains the integrity of the workpiece. Honing enables manufacturers to produce parts with outstanding fit and finish, which enhances the product’s overall durability and performance. The precision machining of the honing process makes it a great way to improve tolerance.
Understanding how honing works is fundamental for achieving high-quality production in various industries. Knowing the nuances of the honing process enables manufacturers to optimize their machining operations, enhance product performance, and reduce manufacturing costs. The proper use of honing leads to tighter tolerances, superior surface finishes, and improved material properties. Using honing properly reduces waste and ensures that parts are functional and long-lasting.
By mastering honing, machine shops can ensure that their products meet the rigorous requirements of modern applications. Honing is an abrasive machining process and can be tailored to specific workpieces, providing the unique benefits that other machining techniques cannot provide. Honing is essential for providing better and more durable parts. Contact us today to learn how our expertise in honing can meet all your precision machining needs.
What is the primary purpose of honing?
Honing is primarily used to achieve a highly refined surface finish and precise dimensional accuracy in bores and other cylindrical surfaces.
Can honing correct errors in bore shape created by earlier machining processes?
Yes, honing can correct minor errors in bore geometry, improving roundness and straightness.
What is the typical material removal rate for honing?
Honing is a finishing process and is designed for very small rates of material removal, focusing on achieving a smooth finish and dimensional accuracy, unlike the large amount of material removed by grinding.
How does honing improve oil retention?
The cross-hatch pattern produced during honing creates tiny grooves that trap lubricant, which is especially helpful in applications like engine cylinders where proper oil retention is crucial.
Is honing an expensive process?
While the cost of honing may depend on the specific needs, the process is generally cost-effective, particularly when considering the improved performance and life of the components.
Can honing be automated?
Yes, many modern honing machines incorporate automated controls and systems, enhancing efficiency and consistency, and also improving the quality and results.
Contact us today to explore how our expert CNC Machining services can elevate your manufacturing processes. Visit our site to learn more about CNC Solutions and how our Fabrication Services can assist you. For more information, also see our details on Precision Machining and CNC Milling. Discover our high-quality CNC Turning capabilities, and how 5 Axis CNC Machining can improve your project.
CNC Machining
Fabrication Services
On Demand Manufacturing
Surface Finishing
Aerospace
Medical Devices
Get the latest trends and facts about CNC fabrication from our blog.
Shenzhen Runkey Precision Technology Co. Ltd, a subsidiary of the Tensun Group, is your trusted one-stop solution for custom manufacturing from prototyping to production.Transforming your idea into reality with digital manufacturing resources,streamlined processes, expert guidance,accelerated timelines, and uncompromising quality.
©2024. CNC Fabrication All Rights Reserved.