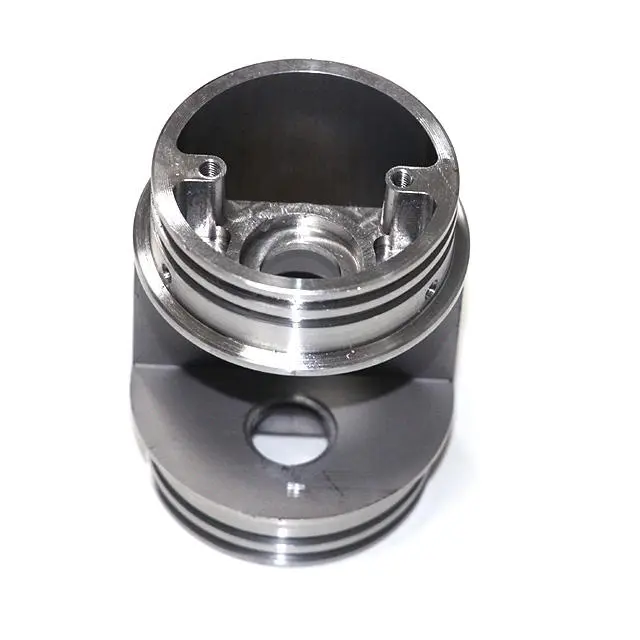
- +8615586668226
- [email protected]
- No. 30, Hongbang Industrial Park, Shenzhen
A CNC machine is a sophisticated piece of equipment that uses computer numerical control to automate the process of creating parts. Unlike manually operated machines, which rely on human input for every action, a CNC machine follows a pre-written computer program to execute precise movements. This programme, often written in G-code, dictates every aspect of the machining process, including the movement of the cutting tool, the speed of rotation, and the feed rate. A CNC machine is capable of high level of accuracy.
The operation of a CNC machine begins with the creation of a digital design, usually through computer-aided design (CAD) software. This design is then translated into a set of instructions (G-code) that the machine can understand. The machine then uses these instructions to guide the cutting tool, such as a mill or lathe, to remove material from a workpiece, shaping it into the desired form. As a leading provider of CNC machining services, we understand the intricacies of this process and leverage it to produce high-quality components for various industries.
One of the primary advantages of CNC machining is its ability to deliver high precision and accuracy. CNC machines can consistently produce parts that meet tight tolerance specifications, which is crucial in industries like aerospace and medical devices. Precision machining ensures that each component functions flawlessly within a larger system. Another key advantage is the speed and efficiency of CNC machinery. CNC machines can operate continuously, 24/7, without the need for breaks, significantly increasing production output.
CNC machining also offers unparalleled repeatability. Once a programme is created and tested, the machine can produce identical parts repeatedly, with minimal variation. This is particularly beneficial for large production runs. Additionally, CNC machines can work with a wide range of materials, from metals and plastics to composites and wood. This versatility makes use CNC machining a preferred choice across various sectors. Furthermore, the process is automated, reducing the risk of human error and improving overall efficiency.
Despite the numerous benefits, there are also some disadvantages of CNC machines. One of the most significant cons of CNC machining is the high initial investment cost. CNC machines are more expensive than manually operated equipment, which can be a barrier for smaller machine shops or startups. Additionally, the complexity of CNC machinery requires skilled operators and programmers, and the cost of training or hiring such personnel can be substantial.
Another potential drawback is the issue of skills loss. As the demand for manual machine operators decreases, the pool of skilled machinists who can operate conventional machines may shrink. This could eventually lead to a shortage of expertise in traditional machining techniques. Moreover, while CNC machines are excellent for mass production, they may not be the most cost-effective option for small-batch or one-off projects. In such cases, 3D printing or other manufacturing technologies might be more suitable. Also, remember that the size of the part can impact on the cost. The machine is not always suitable for producing large parts.
When comparing CNC machining to manual machining, several key differences emerge. Manual machine operations rely heavily on the skill and experience of the machinist. While this can lead to high-quality results, it also introduces the possibility of human error. CNC machines, on the other hand, are computer-controlled, minimizing the risk of mistakes and ensuring consistent quality. Accuracy and precision are also big pluses when we talk about CNC.
Manually operated machines require constant supervision and are limited by the physical endurance of the operator. CNC machines can operate continuously, leading to higher productivity. However, manual machining can be more cost-effective for small production runs or unique, custom parts. In contrast, CNC machining excels in producing large quantities of identical parts quickly and efficiently. CNC is perfect when you need CNC to produce many elements.
While CNC machining is versatile, it does have certain limitations of CNC regarding materials and part size. Some materials, such as extremely hard or brittle substances, may be challenging to machine using standard CNC methods. Additionally, the size of the part that can be produced is limited by the dimensions of the CNC machine itself. Large parts may require specialized equipment or multiple setups, increasing the complexity and cost of the machining process.
Furthermore, certain materials may require specific cutting tool materials or coatings to prevent excessive wear or damage. This can add to the overall cost of machining. When choosing a manufacturing method, it’s essential to consider the properties of the material and the capabilities of the CNC machinery available. Our team of experienced engineers can help you determine the best approach for your specific project, ensuring optimal results.
Tolerance and repeatability are critical factors in many manufacturing processes, particularly in industries where precision is paramount. CNC machining excels in both areas. CNC machines can achieve incredibly tight tolerances, often measured in thousandths of an inch. This level of accuracy is essential for creating parts through a machine shop that fit together perfectly and function as intended.
Repeatability refers to the ability of a machine to produce identical parts consistently. CNC machines are renowned for their repeatability, thanks to their computerized controls. Once a programme is optimized, the machine can create machined parts with minimal variation from one piece to the next. This consistency is vital for maintaining quality and ensuring interchangeability of components. This is particularly important in industries such as aerospace, automotive, and medical devices.
Automation is at the heart of CNC machining. The entire machining process, from loading the workpiece to executing the cuts, can be fully automated. This process is automated nature of CNC machining offers several significant benefits. First, it reduces the need for manual labor, cutting overall expenses and minimizing the risk of human error. Second, automation allows for continuous use of the machinery, maximizing productivity.
Moreover, automation enables CNC machines to perform complex machining operations that would be difficult or impossible to achieve with manually operated equipment. This capability opens up new possibilities for design and innovation, allowing manufacturers to create intricate and high-precision components. Automation also improves safety in the workplace by reducing the need for operators to interact directly with the machinery during operation.
Precision machining is essential in numerous industries where the performance and reliability of components are critical. In sectors like aerospace, medical devices, and automation, even the slightest deviation from specifications can have significant consequences. CNC machining excels in precision machining due to its computer-controlled nature and ability to achieve extremely tight tolerances. CNC machines can create parts with a high level of accuracy, ensuring that they meet the exact requirements of the application.
The precision of CNC machining also contributes to the longevity and efficiency of the final product. Well-machined parts fit together seamlessly, reducing wear and tear and improving overall performance. This is particularly important in high-stress environments, such as those found in aircraft engines or medical implants. By delivering exceptional accuracy and precision, CNC machining plays a vital role in ensuring the safety, reliability, and effectiveness of critical components.
Choosing the right CNC machining services is crucial for the success of your project. When evaluating potential partners, consider their experience, capabilities, and quality control processes. Look for a manufacturing company that has a proven track record in your industry and can demonstrate expertise in working with the materials you require. It’s also essential to assess the range of machining operations they offer and ensure they have the necessary equipment to handle the size of the part and complexity of your project.
Another critical factor is communication. A good CNC machining provider will work closely with you to understand your specific needs and provide regular updates throughout the manufacturing process. They should also be responsive to your questions and concerns and offer expert advice on optimizing your design for manufacturability. At our facility, we pride ourselves on our commitment to customer satisfaction and our ability to deliver high-quality components that meet the most demanding specifications. Contact us today to learn more about how we can help you with your next project.
The future of CNC machining looks bright, with ongoing advancements in technology driving further improvements in efficiency, precision, and versatility. We can expect to see even greater automation, with CNC machines becoming increasingly integrated into smart factories and connected through the Internet of Things (IoT). This will enable real-time monitoring, predictive maintenance, and even greater optimization of the manufacturing process.
Another trend is the growing use of artificial intelligence (AI) in CNC machining. AI algorithms can analyze vast amounts of data to identify patterns and optimize machining parameters, leading to further improvements in quality and productivity. Additionally, we are likely to see increased use of hybrid manufacturing methods, combining CNC machining with other techniques like 3D printing to create even more complex and customized parts. As a forward-thinking manufacturing company, we are committed to staying at the forefront of these developments and leveraging the latest technologies to deliver exceptional value to our customers.
What are some common applications of CNC machining?
CNC machining is used across a wide range of industries, including aerospace, automotive, medical devices, electronics, and consumer products. It is particularly well-suited for creating complex parts that require high precision and repeatability.
How long does it take to create a CNC program?
The time required to create a CNC programme depends on the complexity of the part and the experience of the programmer. Simple parts may only take a matter of hours, while more intricate designs could take several days or even weeks.
Can CNC machines be used for prototyping?
Yes, CNC machines are an excellent choice for creating prototype parts. They offer the ability to quickly produce accurate and functional prototypes, allowing designers to test and refine their ideas before moving to full-scale production.
What is the difference between 3-axis and 5-axis CNC machining?
A 3-axis CNC machine can move the cutting tool in three directions (X, Y, and Z), while a 5-axis CNC machine can move in five directions (X, Y, Z, and two rotational axes). This added flexibility allows 5-axis machines to create more complex shapes and features.
How do I maintain a CNC machine?
Regular maintenance is essential for keeping a CNC machine in optimal condition. This includes cleaning the machine, lubricating moving parts, checking for wear and tear, and ensuring that the computerized controls are functioning correctly.
What materials are suitable for CNC machining?
CNC machining can be used with a wide variety of materials, including metals (aluminum, steel, brass, etc.), plastics (ABS, polycarbonate, etc.), wood, composites, and more. The choice of material depends on the specific application and the desired properties of the finished part.
CNC machining offers numerous advantages, including high precision, repeatability, and automation, making it ideal for a wide range of industries.
While there are some disadvantages of CNC, such as the initial investment cost and the need for skilled operators, the benefits often far outweigh the drawbacks.
CNC machining excels in precision machining, delivering parts that meet tight tolerances and perform reliably in demanding applications.
Choosing the right CNC machining services provider is crucial for the success of your project, considering factors like experience, capabilities, and communication.
The future of CNC machining is bright, with ongoing advancements in automation, AI, and hybrid manufacturing methods driving further improvements in efficiency and versatility.
As a leading provider of CNC machining services, we are committed to leveraging the latest technologies and our extensive expertise to deliver exceptional value and high-quality components to our customers across various industries.
Visit our website to explore our comprehensive fabrication services and discover how we can help you bring your designs to life. We specialize in a wide range of processes, including sheet metal fabrication, die casting, and metal bending. Our state-of-the-art facility is equipped with the latest CNC machinery, and our team of experienced engineers is dedicated to delivering high-precision parts that meet your exact specifications. Whether you need rapid prototyping or high-volume production, we have the capabilities and expertise to handle your project with efficiency and precision. Learn more about our CNC solutions and how we can help you optimize your manufacturing process. Additionally, we offer a variety of surface finishing options to enhance the appearance and durability of your parts.
Get the latest trends and facts about CNC fabrication from our blog.
Shenzhen Runkey Precision Technology Co. Ltd, a subsidiary of the Tensun Group, is your trusted one-stop solution for custom manufacturing from prototyping to production.Transforming your idea into reality with digital manufacturing resources,streamlined processes, expert guidance,accelerated timelines, and uncompromising quality.
©2024. CNC Fabrication All Rights Reserved.