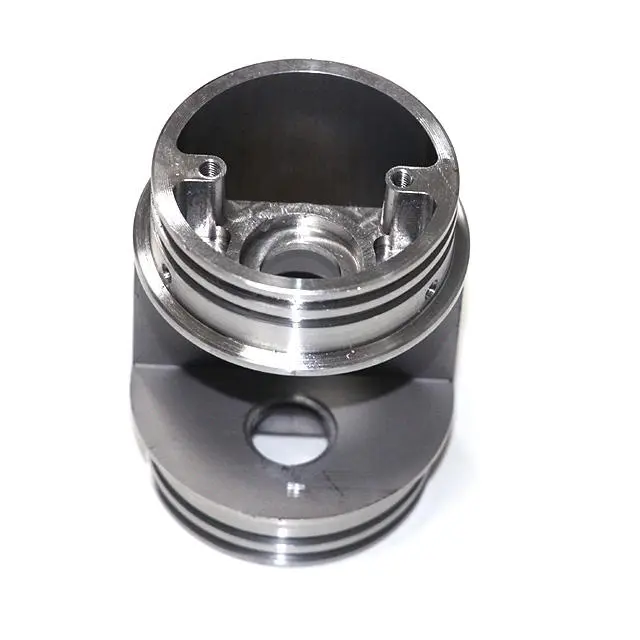
- +8615586668226
- [email protected]
- No. 30, Hongbang Industrial Park, Shenzhen
Attention: In the world of precision manufacturing, understanding the nuances of material removal processes is paramount. Abrasive wear, a critical aspect of many manufacturing operations, involves the removal of material from a surface due to the action of harder particles. This can occur in two primary ways: either a rough, hard surface slides against a softer one, or loose, hard particles slide between two surfaces. A case study on abrasive surface finishing of aluminum flat sheet, detailed in Wear 258 (2005) 13-17, provides valuable insights into this process. The research highlights that the resistance to abrasive wear is a function of a material’s hardness, as confirmed by numerous investigators.
Key Takeaway: The smaller the abrasive grain size, the larger its identifying number, and the softer the material being worked on, the more pronounced the wear.
Interest: Tribology, the science of interacting surfaces in relative motion, plays a pivotal role in our CNC machining operations. It helps us understand the friction, wear, and lubrication principles that are essential for optimizing manufacturing processes. Without a deep understanding of tribology, achieving precise and efficient material removal would be impossible. Our factory leverages these principles to enhance the quality and longevity of our products, ensuring they meet the rigorous demands of industries like aerospace and medical devices.
Interest: Our CNC machining services are designed to cater to a broad range of industries, each with its unique requirements.
Desire: Surface finish is not just about aesthetics; it’s about functionality and performance. The study on aluminum flat sheet finishing demonstrates how different abrasive media and techniques can impact the final product. We apply these learnings in our surface finishing processes to achieve the desired texture, roughness, and durability for each component.
For instance, in clad aluminum, commonly used in aerospace applications for its corrosion resistance, controlling the abrasive process is crucial. The study found that using abrasive belt media with an equivalent grit size below 320 could penetrate the clad layer, exposing the substrate aluminum alloy and compromising its protective properties.
Desire: Choosing the right material is as crucial as the machining process itself. We work with a wide range of materials, including aluminum, steel, titanium, and various alloys, each selected for its specific properties and suitability for the intended application. Our expertise in aluminum extrusion and die casting allows us to offer versatile solutions for different manufacturing needs.
Material Selection Guide
Industry | Material | Properties |
---|---|---|
Aerospace | Aluminum Alloys | Lightweight, high strength, corrosion-resistant |
Automotive | Steel, Aluminum | Durable, strong, cost-effective |
Medical Devices | Stainless Steel | Biocompatible, sterilizable, corrosion-resistant |
Electronics | Copper, Aluminum | Conductive, heat dissipative |
Industrial Equipment | Steel Alloys | High strength, wear-resistant |
Consumer Products | Plastics, Aluminum | Versatile, cost-effective, aesthetically pleasing |
Energy and Renewable Energy | Stainless Steel, Aluminum | Durable, corrosion-resistant, weather-resistant |
Robotics | Titanium, Aluminum | Lightweight, high strength, durable |
Construction and Architecture | Steel, Aluminum, Concrete | Strong, durable, weather-resistant |
Tools and Molds | Tool Steel | High hardness, wear-resistant |
Food and Packaging | Food-Grade Plastics, Stainless Steel | Safe for food contact, easy to clean |
Pharmaceuticals | Medical-Grade Plastics, Stainless Steel | Non-reactive, sterilizable |
Heavy Equipment | Steel Alloys | High strength, impact-resistant |
Custom Projects/Prototypes | Various | Dependent on project requirements |
Art and Design | Metals, Plastics, Wood | Aesthetically pleasing, workable |
Telecommunications | Copper, Aluminum, Plastics | Conductive, lightweight, durable |
Packaging | Plastics, Paper, Aluminum | Protective, lightweight, cost-effective |
Action: A major aerospace client approached us with a challenge: they needed to improve the surface finish of their 2024-T3 clad aluminum components without compromising the clad layer’s integrity. Drawing on the insights from the Wear journal study and our extensive experience, we implemented a multi-stage abrasive finishing process using a new abrasive belt of grit size 320.
Results:
Action: Proper surface preparation, including deburring, is crucial for ensuring the quality and functionality of manufactured parts. Burrs, those tiny projections left behind after cutting or forming, can interfere with assembly, cause damage, and compromise safety. Our factory employs a variety of deburring techniques, tailored to the specific material and application, to ensure a smooth, clean finish. In the context of metal bending and wire EDM, precise deburring is essential for achieving tight tolerances and seamless integration.
Desire: Selecting the right abrasive media is crucial for achieving the desired surface finish and maintaining material integrity. The research detailed in the PDF emphasizes the relationship between abrasive grit size and penetration depth, particularly in clad materials.
Abrasive Media Selection Chart
Grit Size | Material | Application |
---|---|---|
180 | Aluminum | Aggressive material removal, roughing |
240 | Steel | General-purpose finishing, moderate material removal |
320 | Clad Aluminum | Fine finishing, preserving clad layer integrity |
>320 | Various | Polishing, achieving very smooth surfaces |
Our factory stocks a wide range of abrasive media, from coarse grits for aggressive material removal to fine grits for polishing. We carefully select the appropriate media based on the specific material and application requirements. Our capabilities in rapid prototyping and on demand manufacturing allow us to quickly adapt to different project needs.
Interest: Ensuring the quality and precision of our products requires advanced measurement techniques. While surface profilometers are useful for general roughness measurements, they may not be sufficient for applications where the depth of surface features is critical. In such cases, we use optical microscopes to analyze the depth and distribution of grooves, ensuring that they meet the required specifications. This is particularly important in industries like medical devices and aerospace, where even minute deviations can have significant consequences.
Desire: CNC solutions are at the heart of modern manufacturing, enabling automation, precision, and efficiency. Our factory utilizes state-of-the-art CNC machines, including multi-axis milling centers, lathes, and EDM machines, to produce complex parts with tight tolerances. These technologies allow us to offer a wide range of services, from one-off prototypes to high-volume production runs.
What is clad aluminum, and why is it important in aerospace applications?
Clad aluminum consists of a layer of pure aluminum metallurgically bonded to a substrate, typically an aluminum alloy. It’s widely used in aerospace for its superior corrosion resistance and attractive finish.
How does abrasive grit size affect the surface finish of aluminum?
The smaller the grit size (higher grit number), the finer the abrasive particles, resulting in a smoother surface finish. Larger grit sizes remove more material but leave a rougher surface.
What is the significance of tribology in CNC machining?
Tribology, the study of friction, wear, and lubrication, is crucial for understanding and optimizing machining processes. It helps us select the right cutting tools, lubricants, and operating parameters to minimize wear and maximize efficiency.
What advanced measurement techniques do you use to ensure product quality?
Besides standard surface profilometers, we employ optical microscopes for detailed analysis of surface features, including groove depth and distribution.
Can you handle custom projects and prototypes?
Absolutely! Our rapid prototyping and on demand manufacturing services are designed to bring your unique ideas to life, whether it’s a one-off prototype or a small batch of custom parts.
How do you ensure the integrity of the clad layer during abrasive finishing of clad aluminum?
We carefully select the abrasive media, using a grit size of 320 or higher, and control the process parameters to prevent penetration of the clad layer, as highlighted in the research.
As a leading CNC manufacturing service provider and product manufacturing factory, we are committed to delivering innovative solutions that meet the evolving needs of our diverse clientele. Our expertise in areas like machining services, fabrication services, and cutting-edge technologies like 5-axis CNC machining positions us at the forefront of the industry. We understand the science behind manufacturing processes, as illustrated by the insights from the Wear journal study on abrasive finishing.
Ready to experience the difference that precision and expertise can make? Contact us today to discuss your project and discover how our tailored CNC solutions can bring your vision to life. Whether you’re in aerospace, automotive, medical devices, or any other industry, we have the knowledge, technology, and commitment to deliver exceptional results. Let’s collaborate to create the future of manufacturing.
Get the latest trends and facts about CNC fabrication from our blog.
Shenzhen Runkey Precision Technology Co. Ltd, a subsidiary of the Tensun Group, is your trusted one-stop solution for custom manufacturing from prototyping to production.Transforming your idea into reality with digital manufacturing resources,streamlined processes, expert guidance,accelerated timelines, and uncompromising quality.
©2024. CNC Fabrication All Rights Reserved.