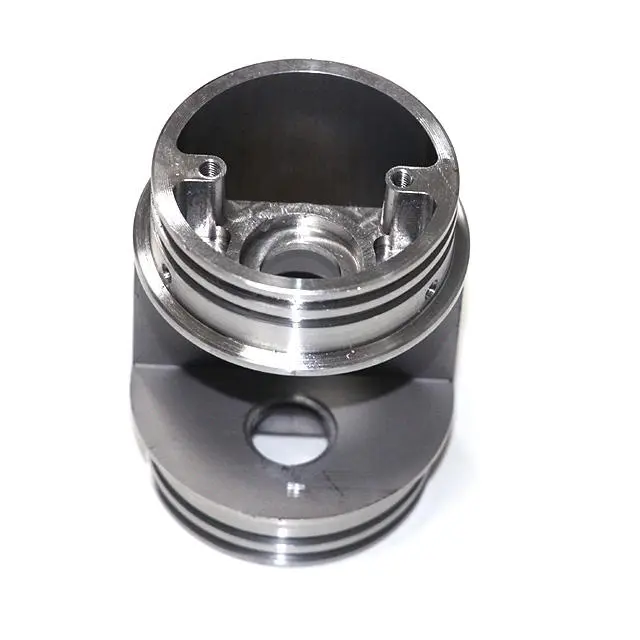
- +8615586668226
- [email protected]
- No. 30, Hongbang Industrial Park, Shenzhen
CNC metal spinning is a highly efficient metal fabrication process used to shape metal parts with precision and consistency. This manufacturing process uses a CNC machine to control the spinning process, ensuring each piece meets exact specifications. I’ve seen firsthand how CNC spinning transforms a flat metal disc into complex shapes, making it invaluable for industries like aerospace and automotive.
The process involves rotating a flat metal disc or tube at high speed on a spinning lathe while a spinning tool applies pressure to shape the metal. It’s fascinating to watch how the grain structure of the metal adapts, maintaining strength and integrity. CNC metal spinning allows for the creation of seamless, hollow parts, which is why it’s often preferred over processes like metal stamping. I find that the ability to shape metal without seams significantly improves the quality and durability of the final product.
CNC spinning and hand spinning are two distinct methods in the world of metal fabrication. Hand spinning, also known as manual metal spinning, relies on the skill of an operator to manually guide the spinning tool and shape metal. While this traditional method allows for a high degree of customization, it is labor-intensive and less precise than CNC methods.
On the other hand, CNC spinning utilizes computer numerical control to automate the spinning process. This ensures greater accuracy, repeatability, and efficiency. When I first introduced CNC spinning machines into our manufacturing process, the improvement in production speed and quality was remarkable. The precision offered by CNC control also minimizes material waste, which is a significant benefit for cost-effective manufacturing.
Metal spinning offers numerous advantages that make it a preferred choice in various industries. One of the key advantages of metal spinning is its ability to produce seamless, hollow parts with high structural integrity. I often emphasize to clients that the seamless nature of spun parts enhances their durability and performance, particularly in high-stress applications.
Another significant advantage is the cost-effectiveness of metal spinning for low to medium-volume production runs. Unlike processes that require expensive tooling, metal spinning uses relatively simple and inexpensive tools. This makes it ideal for prototyping and custom projects. Additionally, the metal spinning process maintains the grain structure of the metal, resulting in stronger parts compared to those made through casting or forging.
Table: Advantages of Metal Spinning
Advantage | Description |
Seamless Parts | Produces parts without seams, enhancing durability and performance. |
Cost-Effective | Ideal for low to medium-volume production due to low tooling costs. |
Material Integrity | Maintains the grain structure of the metal, resulting in stronger parts. |
Versatility | Can be used with a variety of metals, including aluminum, steel, and copper. |
Precision | CNC spinning offers high precision and repeatability, ensuring consistent quality. |
Reduced Material Waste | Precise control minimizes material waste, making the process more efficient and sustainable. |
Quick Turnaround | Faster production times compared to other metal forming processes, especially for complex shapes. |
Customizable | Allows for the creation of custom shapes and sizes, making it suitable for unique and specialized applications. |
Structural Integrity | Spun parts have high structural integrity, making them suitable for high-stress applications. |
Enhanced Aesthetics | The spinning process can impart a smooth, polished finish to the metal, improving the aesthetic appeal of the final product. |
The CNC metal spinning process is a fascinating blend of traditional techniques and modern technology. It begins with selecting the appropriate metal sheet or metal disc. From my experience, the choice of material greatly influences the outcome, so we carefully consider factors like thickness and alloy composition.
The process involves mounting the metal disc on a CNC lathe and programming the machine to follow a specific path. As the disc rotates, a spinning tool applies pressure, gradually shaping the metal to the desired form. I’ve been amazed by the precision of CNC spinning, which allows for intricate designs and tight tolerances. The entire operation is controlled by a computer, ensuring each part is identical to the last. A typical metal spinning operation leverages metal spinning technology to shape metal, while relying on the expertise of the operator to achieve the desired result.
Several types of machines are used in metal spinning, each with its own set of capabilities. Spinning lathes are the most common, and they come in both manual and CNC variants. Manual spinning lathes require skilled operators to control the spinning tool, while CNC spinning machines automate the process for greater precision.
In addition to lathes, other spinning equipment includes rollers, shear forms, and trimming tools. Each piece of equipment plays a crucial role in the metal spinning process. When I upgraded our facility to include CNC spinning machines, the efficiency and quality of our output improved dramatically. The investment was well worth it, considering the long-term benefits. Employing a spinning tool is crucial in the metal spinning process, a specialized metal fabrication method that shapes metal parts with precision.
The introduction of CNC technology has revolutionized traditional metal spinning. CNC spinning machines offer unparalleled precision and repeatability, which is crucial for industries that demand high-quality components. From my perspective, the most significant benefit of CNC spinning is its ability to produce complex shapes with consistent accuracy.
CNC control also enables the automation of the spinning process, reducing the need for manual intervention and minimizing the risk of human error. This leads to higher productivity and lower labor costs. Moreover, CNC spinning allows for greater flexibility in design, as the machines can be easily reprogrammed to produce different parts. This adaptability is invaluable for our business, as we often handle custom orders with unique specifications.
Table: Enhancements of CNC Technology in Metal Spinning
Feature | Description |
Precision | CNC machines offer higher precision compared to manual spinning, ensuring accurate shaping and dimensions. |
Repeatability | CNC spinning ensures consistent quality and dimensions across multiple parts, crucial for mass production. |
Automation | Automates the spinning process, reducing the need for manual labor and increasing efficiency. |
Complex Shapes | Enables the creation of complex and intricate shapes that are difficult or impossible to achieve with manual spinning. |
Reduced Labor Costs | Automation reduces the reliance on skilled labor, leading to lower production costs. |
Design Flexibility | CNC machines can be easily reprogrammed to produce different parts, offering greater flexibility in design and production. |
Material Efficiency | Precise control minimizes material waste, making the process more cost-effective and environmentally friendly. |
Faster Production | CNC spinning speeds up the production process, allowing for quicker turnaround times. |
Enhanced Quality Control | Automated processes and precise control improve overall quality control, reducing defects and ensuring high-quality output. |
Scalability | CNC technology allows for easy scalability of production, making it suitable for both small and large-scale manufacturing operations. |
Metal spinning is a versatile process with applications across a wide range of industries. In the aerospace sector, CNC spinning is used in metal to create lightweight, high-strength components for aircraft. The automotive industry benefits from metal spinning for producing parts like wheels, reflectors, and housings. I’ve also seen metal spinning used in the medical field to manufacture precision instruments and implants.
Other industries that rely on metal spinning include lighting, HVAC, and consumer products. The ability to shape metal into complex forms makes it a valuable process for creating custom parts. Whether it’s a decorative item or a critical component, metal spinning provides a reliable solution for many manufacturing challenges. As you can see from the image below, metal spinning creates a wide variety of products.
Choosing CNC metal spinning for your manufacturing needs can provide numerous benefits. Metal spinning offers a unique combination of precision, versatility, and cost-effectiveness. I often recommend CNC spinning to clients who require high-quality parts with intricate designs. The process is particularly well-suited for low to medium-volume production runs, where traditional methods like stamping may be less economical.
Moreover, CNC spinning allows for greater control over the manufacturing process, ensuring that each part meets stringent quality standards. The ability to automate the process also speeds up production times, allowing for faster delivery of finished products. In my experience, the efficiency and reliability of CNC spinning make it an excellent choice for businesses looking to optimize their manufacturing operations.
Selecting the appropriate CNC metal spinning equipment is crucial for achieving optimal results. Several factors should be considered, including the type of material, the complexity of the parts, and the production volume. From my experience, it’s essential to choose machines that offer the right balance of precision and flexibility.
Investing in CNC spinning machines with advanced features, such as multi-axis control and automatic tool changers, can significantly enhance your capabilities. It’s also important to consider the reputation of the equipment manufacturer and the availability of technical support. I always advise clients to thoroughly research their options and choose equipment that aligns with their specific needs and budget.
The future of CNC metal spinning looks promising, with ongoing advancements in technology driving further innovation. I believe that the integration of artificial intelligence and machine learning will play a significant role in optimizing the spinning process. These technologies can help predict tool wear, improve process control, and enhance overall efficiency.
Additionally, the development of new materials and alloys will expand the applications of CNC spinning. As industries continue to demand lighter, stronger, and more durable components, the versatility of metal spinning will become even more valuable. I’m excited about the future of this technology and its potential to transform manufacturing processes across various sectors. A skilled operator utilizing a spinning tool to expertly shape metal into the desired form—this hands-on approach is a hallmark of manual metal fabrication.
How does CNC metal spinning differ from traditional metal spinning?
CNC metal spinning uses computer numerical control to automate the spinning process, offering greater precision and repeatability compared to traditional, manual methods.
What are the main advantages of using CNC metal spinning?
The main advantages include high precision, cost-effectiveness for low to medium-volume runs, the ability to produce seamless parts, and the maintenance of material integrity.
Which industries benefit the most from CNC metal spinning?
Industries such as aerospace, automotive, medical devices, and consumer products benefit significantly from the precision and versatility of CNC metal spinning.
What should I consider when choosing CNC metal spinning equipment?
Consider factors like material type, part complexity, production volume, machine features, and the reputation of the manufacturer.
What materials can be used in CNC metal spinning?
CNC metal spinning can be used with a variety of metals, including aluminum, steel, copper, brass, and stainless steel.
Is CNC metal spinning suitable for prototyping?
Yes, CNC metal spinning is ideal for prototyping due to its low tooling costs and ability to produce custom shapes quickly and accurately.
CNC metal spinning is a highly efficient and precise method for shaping metal parts.
The process offers numerous advantages, including cost-effectiveness, material integrity, and the ability to create seamless, complex shapes.
CNC technology enhances traditional metal spinning by automating the process and improving accuracy.
Metal spinning has wide-ranging applications across industries such as aerospace, automotive, and medical devices.
Selecting the right CNC metal spinning equipment is crucial for achieving optimal results.
The future of CNC metal spinning looks promising, with ongoing technological advancements driving further innovation.
As an expert in CNC fabrication services, I can confidently say that our manufacturing plants are equipped to handle the most demanding projects. Whether you need precision machining for aerospace components or intricate assembly for medical devices, our state-of-the-art CNC machines and experienced team ensure top-quality results. We also specialize in sheet metal fabrication, offering custom solutions tailored to your specific needs. Our expertise extends to CNC machining, ensuring that every part meets your exact specifications. For those in need of rapid prototyping, our advanced CNC metal spinning capabilities provide quick and accurate prototypes to accelerate your product development cycle.
Get the latest trends and facts about CNC fabrication from our blog.
Shenzhen Runkey Precision Technology Co. Ltd, a subsidiary of the Tensun Group, is your trusted one-stop solution for custom manufacturing from prototyping to production.Transforming your idea into reality with digital manufacturing resources,streamlined processes, expert guidance,accelerated timelines, and uncompromising quality.
©2024. CNC Fabrication All Rights Reserved.