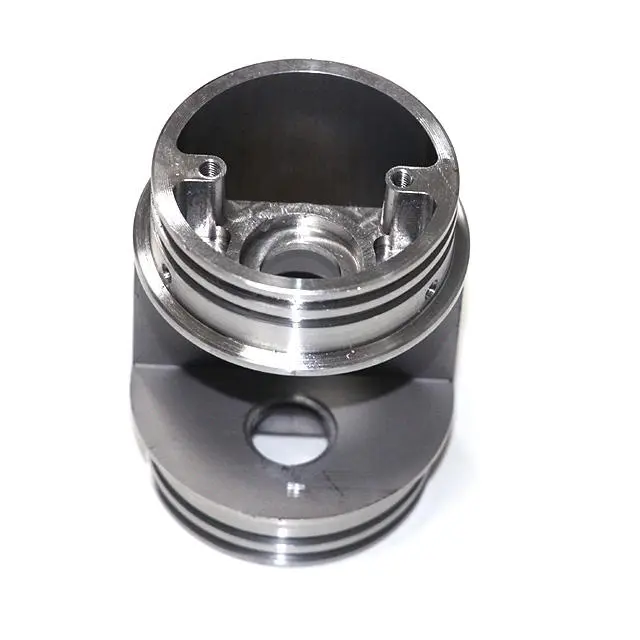
- +8615586668226
- [email protected]
- No. 30, Hongbang Industrial Park, Shenzhen
Welding is a metal joining process that uses heat to melt the metal at the joint, creating a permanent bond. It often involves a filler material to enhance the strength and integrity of the weld. Welding requires specialized equipment and trained personnel, and offers high strength and a seamless finish. Think of it like melting two pieces of ice cream together – they become one solid piece. This makes welding suitable for applications demanding structural integrity, such as in the creation of Aerospace components.
Welding creates a continuous, homogenous join between two pieces of metal. This is achieved through various processes like arc welding, TIG welding, and MIG welding, each using different methods to generate the required heat. Welding requires careful control of temperature and other parameters to ensure a strong and reliable weld. The welding process results in a permanent bond that is often stronger than the base metal.
Riveting is a metal joining method that involves inserting a rivet through holes drilled in two or more metal parts. The rivet is then deformed on the opposite side, creating a permanent mechanical connection. Riveting is a cold-working process, meaning it doesn’t involve melting the metal. Imagine fastening two pieces of paper together with a brad – the brad acts like a rivet, clamping the papers together. Riveting is often used for joining Sheet Metal Fabrication and in applications where access to only one side of the joint is possible. A rivet is used to mechanically join two pieces together. The riveting process is simpler than welding and doesn’t require the same level of specialized equipment.
Riveting can be a faster and more cost-effective method than welding in certain applications. Riveting allows for the joining of dissimilar metals, which can be challenging with some welding processes. However, riveting creates a visible joint and may not offer the same level of strength as welding in high-stress applications. Riveting is also known for its fatigue resistance, making it suitable for dynamic structures like aircraft.
The difference between welding and riveting lies primarily in how they join metal together. Welding fuses the metal, while riveting uses a mechanical fastener. This fundamental difference leads to variations in strength, appearance, and application. Understanding these differences between welding and riveting is crucial for selecting the appropriate method for a specific project.
Feature | Welding | Riveting |
Joining Process | Fusion | Mechanical |
Strength | High | Moderate |
Appearance | Seamless | Visible Fasteners |
Heat Required | Yes | No |
Equipment | Specialized | Less Specialized |
Speed | Varies | Generally Faster |
Cost | Can be higher | Generally lower |
There are various types of welding, each suited to specific materials and applications. Common types include:
MIG welding (Metal Inert Gas): Uses a continuously fed wire electrode and a shielding gas to protect the weld from contamination.
TIG welding (Tungsten Inert Gas): Employs a non-consumable tungsten electrode and a shielding gas, providing precise control over the welding process.
Arc welding: Uses an electric arc to melt the metal at the joint.
Laser welding: Utilizes a high-powered laser to create a precise and focused heat source for welding.
Flux-cored arc welding: A semi-automatic or automatic arc welding process that uses a continuously-fed consumable electrode containing a flux and a shielding gas.
Welding offers high strength, a seamless finish, and can be used to join a wide range of metals. However, it can also be a more complex and expensive process, requiring skilled labor and specialized equipment. Welding may also introduce residual stresses and distortions in the metal. Advantages and disadvantages of welding must be carefully considered for each application.
Riveting is often preferred for its simplicity, speed, and lower cost compared to welding. It also allows for the joining of dissimilar metals. However, riveting leaves visible fasteners and may not be as strong as welding in high-stress applications. Advantage of riveting is its suitability for applications where access to both sides of the joint is not possible.
Welding is the better choice when high strength, a seamless finish, and a permanent bond are required. It’s often the preferred method for structural applications in industries like Automotive, aerospace, and construction. For creating strong and reliable joints in critical components, welding is better suited than riveting.
Riveting is a method of joining metal that is often preferred when speed, cost-effectiveness, and accessibility are paramount. It’s frequently used in Electronics, Consumer Products assembly, and sheet metal fabrication, particularly when joining thin sheet metal or dissimilar metals. Riveting is much faster than welding, and is often preferred for joining pieces of sheet metal where cosmetic appearance is not a primary concern.
Cheaper than riveting? Not always. While generally, riveting is considered less expensive due to lower equipment costs and faster processing times, the actual cost depends on various factors like material thickness, joint complexity, and labor costs. For simple joints in thin materials, riveting is often the more economical choice. However, for complex assemblies or thick materials, welding can be more cost-effective in the long run due to its superior strength and durability.
Both welding and riveting find extensive use in various industries. Welding is widely used in Industrial Equipment manufacturing, automotive chassis construction, and pipeline fabrication. Riveting is commonly used in aircraft assembly, Robotics construction, and fastening components in electronic devices.
The choice between welding and riveting depends on several factors, including the application requirements, material properties, budget constraints, and desired aesthetic finish. Consulting with experienced CNC Solutions providers can provide valuable insights and help you make the right choice for your specific project.
Is welding stronger than riveting? Generally, welding creates a stronger joint than riveting.
Can dissimilar metals be riveted? Yes, riveting is often used to join dissimilar metals.
Which method is faster, welding or riveting? Riveting is typically faster than welding.
What are the safety precautions for welding and riveting? Both processes require appropriate safety gear, including eye protection, gloves, and potentially respirators.
What type of welding is best for thin sheet metal? MIG or TIG welding are often preferred for thin sheet metal.
Can riveted joints be disassembled? Yes, riveted joints can be disassembled by drilling out the rivets.
Welding fuses metal together, while riveting uses a mechanical fastener.
Welding generally offers higher strength but can be more complex and costly.
Riveting is typically faster and less expensive, but may not be as strong.
The best choice depends on the specific application, materials, and budget.
Consulting with experts can help you determine the optimal joining method.
Get the latest trends and facts about CNC fabrication from our blog.
Shenzhen Runkey Precision Technology Co. Ltd, a subsidiary of the Tensun Group, is your trusted one-stop solution for custom manufacturing from prototyping to production.Transforming your idea into reality with digital manufacturing resources,streamlined processes, expert guidance,accelerated timelines, and uncompromising quality.
©2024. CNC Fabrication All Rights Reserved.