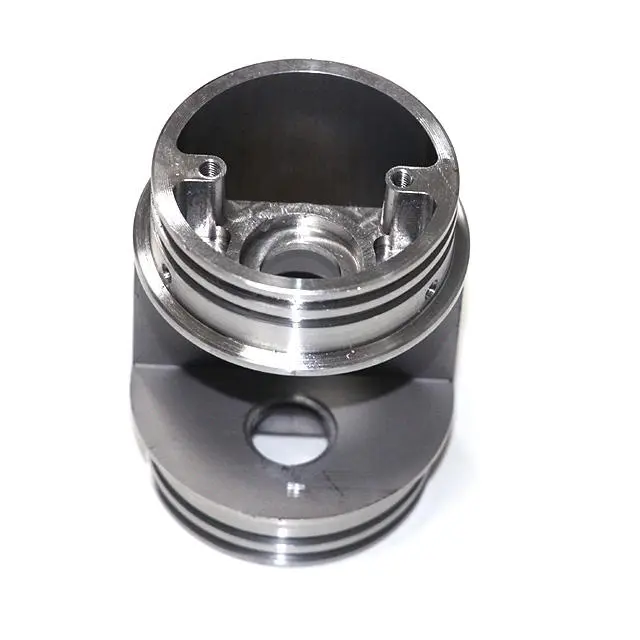
- +8615586668226
- [email protected]
- No. 30, Hongbang Industrial Park, Shenzhen
By eliminating the need for exposed fasteners, these joints enhance the aesthetics of products while also reducing production time and costs. This makes them ideal for a range of industries from consumer electronics to automotive and medical devices. In this article, we will explore the different types of snap fit joints, discuss their applications, and highlight the best practices for designing them to ensure optimal performance.
A snap fit joint is a mechanical fastener used to assemble components by interlocking parts. The mechanism typically consists of a protrusion, such as a hook or stud, on one part that snaps into a corresponding recess on another part. During assembly, the protruded feature deflects, allowing it to engage with the mating part. Depending on the design, the joint can be permanent or removable, offering flexibility in both assembly and disassembly.
Snap fit joints are commonly used in plastic components due to the material’s flexibility, allowing for large deflections without damage. However, stress concentration at the joints can cause plastics to creep over time, leading to potential loss of tension. To prevent this, stiff locator elements, such as catches and lugs, are often used to ensure a secure assembly.
Cantilever snap joints are the most common type of snap fit fasteners, typically featuring a simple beam structure with a hook at the tip. The cantilever bends as it engages with the receiving part, allowing the hook to snap back into place. This joint can be either permanent or removable, depending on the design angle between the hook and the recess.
Some cantilever designs incorporate U-shaped or L-shaped beams, which extend the length of the cantilever while minimizing the required space. These configurations reduce deflection forces and are often used in plastic parts for ease of assembly in injection molding.
U-shaped snap joints consist of a U-shaped cantilever beam that fits into a groove on the mating component. This design is commonly used in applications that require a strong grip, such as electronic housings and automotive interior trims. U-shaped joints can be made from various materials, including metal and plastic, offering versatility across different industries.
Torsion snap joints operate by twisting a bar to create a separable connection. A rocker arm mechanism provides deflection force, allowing for easy opening and closing of the joint. These joints are highly durable and are often used for applications that require frequent disassembly.
Annular snap joints are used for circular or elliptical parts, such as pen caps or container lids. A ridge on one part locks into a groove on the other, creating a secure connection. The design of these joints can be adjusted to allow for either easy removal or permanent assembly, depending on the application.
To achieve optimal performance in snap fit joints, it’s essential to follow specific design guidelines:
Fillet the Base of the Cantilever: Adding a fillet at the base of the cantilever beam reduces stress concentration and strengthens the joint. The recommended fillet radius is at least 0.5 times the cantilever base thickness.
Taper the Design: Tapering the cantilever beam’s cross-section distributes stress evenly, reducing material use and improving overall performance.
Increase Clip Width: Wider clips provide more strength to the joint. A minimum width of 5mm is recommended for stability.
Add Lugs: Lugs improve alignment and shear force transfer, reducing the risk of part misalignment during assembly.
Consider Build Direction: Avoid designing snap fits that are built vertically, as this weakens the joint. Deflection should occur only during assembly.
The process of manufacturing snap fasteners involves several key steps:
Design: Start by creating a detailed design using software. Prototypes can be made through 3D printing or CNC machining to validate the design.
Material Selection: Depending on the application, snap fasteners can be made from metal (e.g., brass or stainless steel) or plastic (e.g., polycarbonate or nylon).
Stamping or Molding: Metal fasteners are typically produced using a stamping technique, while plastic fasteners are injection molded.
Plating: A corrosion-resistant coating can be applied to enhance the fastener’s durability and strength.
Quality Testing: Inspection tests are conducted to ensure that the fasteners fit properly and function as intended.
Pros:
Cons:
Snap fit joints provide a versatile and cost-effective solution for assembling a wide variety of components, particularly in plastic and metal parts. When designed and implemented correctly, they improve assembly efficiency, reduce production costs, and offer flexibility in product design. By following best design practices and considering material selection, manufacturers can ensure durable and high-performing snap fit joints. Whether you’re working on prototypes or large-scale production, snap fit joints offer a practical, aesthetic, and efficient fastening solution for modern products.
Get the latest trends and facts about CNC fabrication from our blog.
Shenzhen Runkey Precision Technology Co. Ltd, a subsidiary of the Tensun Group, is your trusted one-stop solution for custom manufacturing from prototyping to production.Transforming your idea into reality with digital manufacturing resources,streamlined processes, expert guidance,accelerated timelines, and uncompromising quality.
©2024. CNC Fabrication All Rights Reserved.